Automotive suspension design has traditionally had to strike a difficult balance between three conflicting needs: road holding or handling, load carrying and passenger comfort. At its most basic level, your car’s suspension must be able to support the vehicle’s weight (and its cargo) while providing adequate handling capabilities and at the same time provide reasonable ride comfort for its passengers. With passive shock and spring suspensions, you could either have a cushy grandpa-approved ride quality or a firmer setup that’s great in the corners but hard on the kidneys. But that all started to change back in 1981 when some clever chaps at Lotus (as part of its Formula 1 team) began to develop the first active suspension system capable of adapting to changing loads and driving conditions.
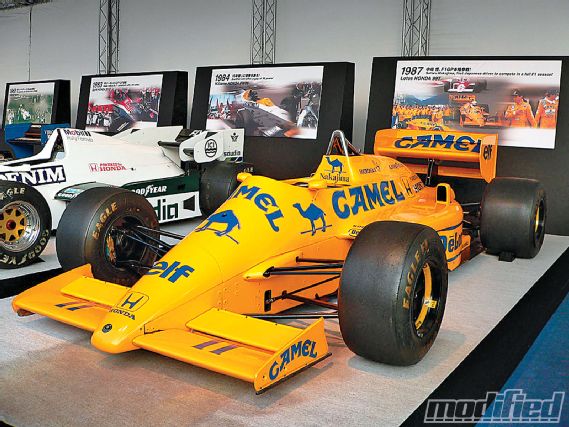
Lotus’ cutting-edge approach to true active handling meant replacing the passive shocks and springs with double-acting hydraulic actuators at each corner of the car. As the wheel and tire meet a bump, the wheel’s acceleration and vertical load is measured by load sensors, travel sensors and accelerometers and this data is transmitted to a computer that calculates the required wheel velocity and displacement to counteract the bump and triggers the servomechanism at each wheel accordingly. This high-bandwidth electro-hydraulic dance takes place hundreds of times per second, allowing each wheel to accurately follow the contour of every bump, dip and curb it encounters, protecting the body structure against unwanted forces and virtually eliminating unwanted weight transfer.
Successfully testing this system at the Brazilian F1 race in 1983, Lotus proved the concept had merit, but for a number of reasons it never quite lived up to its potential. In theory, the system could raise cornering speeds considerably (Lotus engineer Peter Wright was famously quoted as saying its active-suspension F1 car could go around “any corner at any speed”), but in practice it reduced tire-slip angle so much that it was nearly impossible to get enough heat into the tires to allow them to function properly. The hydraulic system was also a bit of a horsepower pig, robbing 4 to 4.5 hp on a smooth road and up to 9 hp on a rough road. Add to that the computational complexity of the system and the need for aerospace-quality hydraulic actuators and you can start to see why this type of fully active suspension has yet to make it onto a mass-produced road car.
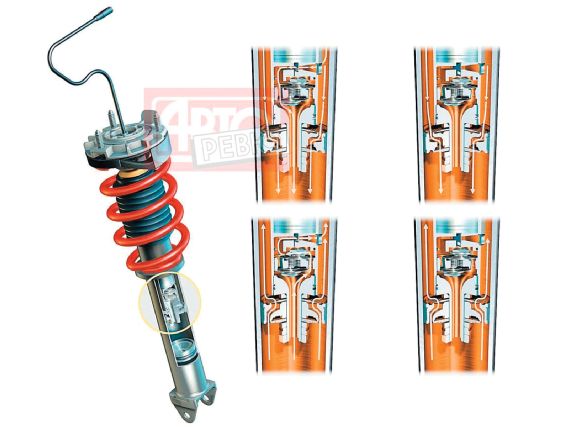
But as an engineering challenge with the potential to decouple the relationship between load carrying, road holding and ride quality, it should come as no surprise that many of the world’s major automakers have continued to look for ways to implement active suspension technologies on their vehicles. Nissan, for example, began developing a hydraulically controlled suspension system in the late ’80s that actively adjusted shock absorber damping (referred to as skyhook damper control) using a pressure control valve in combination with a small accumulator and a hydraulic cylinder to go along with onboard accelerometers, front and rear vehicle height sensors and a vehicle speed sensor (along with a computer to control the system, of course). Although not a fully active system like Lotus’ F1 invention, Nissan’s semi-active approach proved effective at smoothing out bumps and irregularities in the road via its frequency-sensitive damping while also controlling body roll when cornering by increasing hydraulic shock pressure on the outer wheels and reducing it on the inner wheels. Similarly, nose dive under braking could also be controlled by stiffening the front shocks and softening the rear shocks. The system was even sophisticated enough to make damping adjustments for crosswinds and adjust to high speeds by stiffening up slightly for improved roll control and yaw stability.
The lower cost and complexity of this approach allowed Nissan to put this system into production on the ’90 Infiniti Q45, making it one of the first commercially available semi-active suspensions on the market (Mitsubishi having a semi-active system in the ’87 Galant called ECS and Citroën having a hydropneumatic system in 1989 called Hydrative). Toyota equipped the Supra with a similar system that controlled shock damping electronically rather than hydraulically (called TEMS for Toyota Electronically Managed Suspension) that same year, and so it seemed the active (or at least semi-active) suspension system battle was heating up.
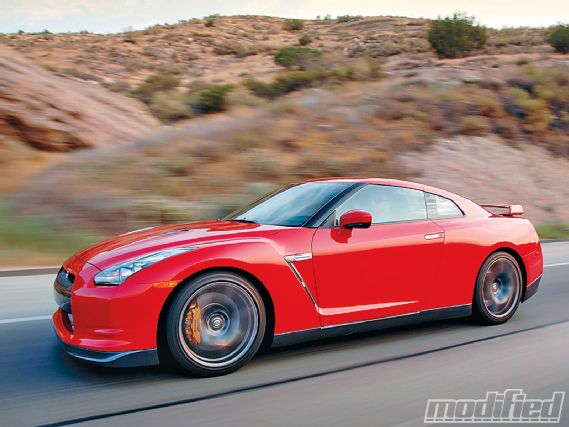
Or was it? Through the ’90s surprisingly little progress was made with active suspension technology and its implementation onto road cars, perhaps because consumers weren’t yet ready for a technology that actively alters the handling characteristics of the car they’re driving. Whatever the case may be, in recent years there’s been renewed interest in active suspension including the use of magneto-rheological dampers.
Magneto what? No, the X-Men super villain isn’t behind this masterful plan, but it does involve the power of magnetism. Initially developed by Delphi Corporation for GM (first used on the ’02 Cadillac STS), a magneto-rheological shock absorber is a damper filled with magneto-rheological fluid that has small iron particles in it. The Damping power can be adjusted by applying a magnetic field to the suspension fluid, causing the iron particles to align themselves in the direction of the magnetic flux. More specifically, a computer-controlled electromagnetic coil is integrated into the damper piston in such a way that when it’s energized the iron particles align in a way that creates flow resistance within the damper, effectively increasing its “stiffness.” The greater the electromagnetic energy applied to the damper, the greater the damping power.
With a sophisticated ECU controlling the magnetic force within each damper, this system is able to respond in real time to road and driving conditions based on input from sensors that monitor vehicle body and wheel motion. This type of damper tuning offers a very large range of damping with faster response (up to 1,000 adjustments per second) than valve-based controlled systems like Nissan’s, and it also provides the driver with several driving programs to choose from (from the all-mighty push-button on the dash or center console), allowing emphasis in damper tuning to be placed on road holding and corner carving or ride comfort. In fact, the technology has become so effective that it’s now used on some of today’s highest performance vehicles including the Audi R8 and Ferrari 599GTB.
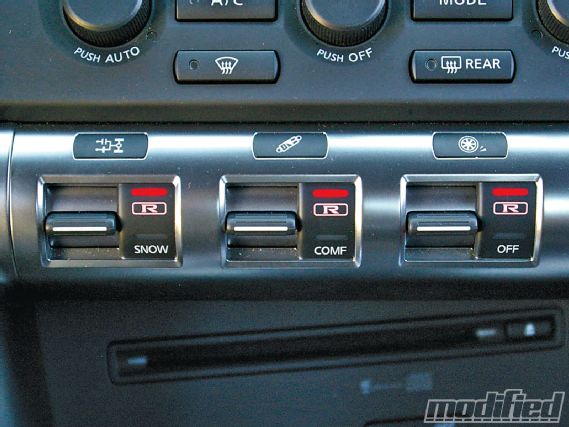
But not all of today’s supercars use magneto-rheological dampers. Nissan’s all-conquering R35 GT-R uses Bilstein’s DampTronic system, at the heart of which is an electronically controlled variable-rate shock absorber. Think of this as a very sophisticated version of TEIN’s EDFC controller and you get the idea. This system, combined with the GT-R’s many other high-tech handling and power delivery aids, gives the driver that same push-button sense of control, with Normal/Sport mode for automatic control of damping based on the ECU’s best maths, a Comfort setting for maximum ride comfort and, of course, an R mode for maximum damping rate when you really want to tear it up in the turns.
Given the incredibly high performance levels of sports cars like the GT-R, Audi R8 and Ferrari 599GTB, there’s little question that these modern forms of (semi-) active suspension provide improved cornering ability along with a wider range of ride quality characteristics from Comfort mode to R mode. Although neither the magneto-rheological or electronically controlled damper approach fully decouples the relationship between load carrying, road holding and ride quality, the process is well under way, and as performance-minded drivers who want to have their cake and eat it too, we should all be looking anxiously toward the future as these forms of active suspension technology trickle down to the sport compact machines we love and can afford.
Send your feedback to dpratte@modified.com.