Time and technology march into the future stride for stride. This unwavering advancement can be seen in computers, manufacturing techniques, medical care and the automobile. Here we will look at the turbocharger, which has advanced considerably since Swiss engineer Alfred Buchi filed a patent for the device on November 16th 1905.
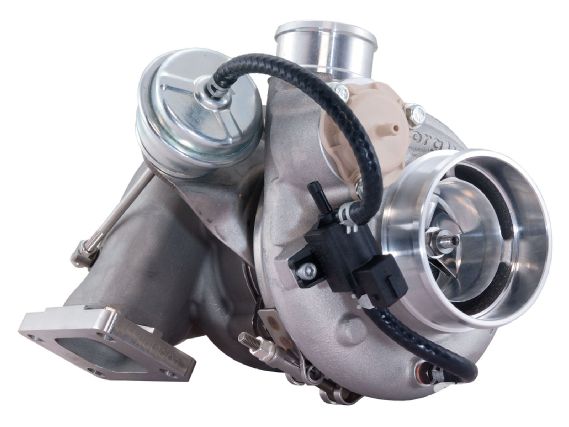
The first successful use of a turbo in motorsports was the Cummins Special, a diesel-powered racer that took the Indy 500 pole in 1952. On the production side, the first mass-produced turbo engine was General Motor's Jetfire in 1962.
The turbo's biggest evolutionary step was the introduction of electronic fuel injection in the late 1980's. In the '90s it was the introduction of dual ball bearing center cartridges and inconel turbine wheels. The 21st Century ushered billet forged compressor wheels and add-on stainless turbine housings.
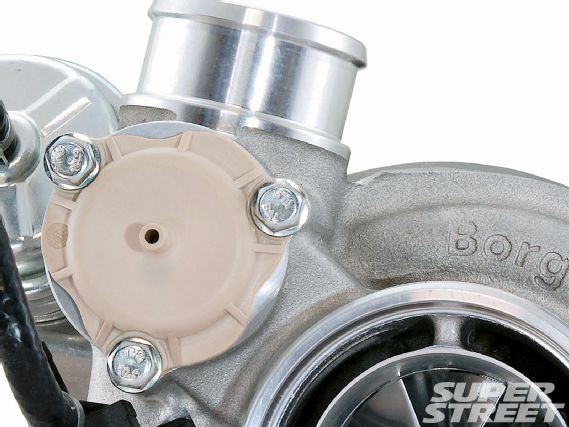
It's the second decade of the century that could well be remembered for the innovation and integration seen in Borg Warner's EFR (Engineered For Racing) line of turbochargers. These leading-edge turbos promise cat-like low-end response, crazy top-end flow, lightweight and the integration of secondary turbo system components.
Geoff Raicer is a highly skilled fabricator and owner of Full Race, makers of awe-inspiring turbo kits. Geoff worked with Borg Warner performing test fits of EFR turbos on some of his more common kits so he has a profound insight on the units.
Ti-Gamma Turbine Wheels
"Over the last 12-plus years we've seen many turbos come and go, and almost all of them used the same turbine wheels and housings," says Geoff. "The Stage 3/5 turbine wheels, P-trim turbine wheels or the GT series turbines were all good for their respective time, however we are in the year 2011 and those 'old-timers' are simply antiquated compared to what we've been seeing on the OE side. Borg Warner recognized this and put together the most advanced turbine wheel/housing configurations ever offered to the aftermarket."
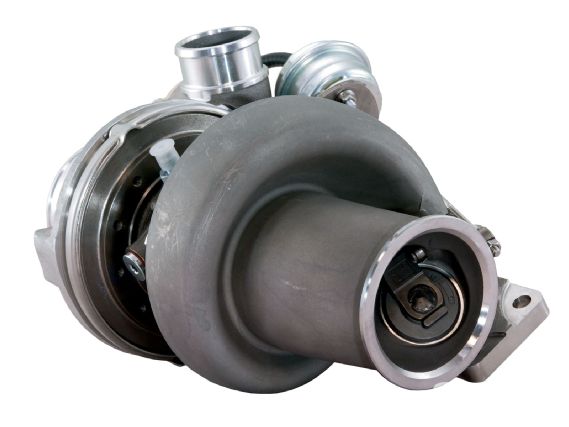
The EFR turbine wheel features a highly-advanced alloy that combines titanium and aluminum. These titanium-aluminide turbine wheels, codenamed Gamma-Ti, in reference to their cerametallic compound call-sign, are extremely difficult to cast but the big pay-off can be seen on the scales. The Gamma-Ti turbine wheels are roughly half the weight of the typical inconel wheel. This reduction of weight results in improved low-end response; higher boost levels at lower rpms and higher overall wheel speeds. This type of wheel has been seen before in the 1999 Evo VI RS but it was a very limited production and Borg Warner is the first to bring this metallurgical magic to the masses. "The material properties of the Gamma-Ti are such that the material is weakest at room temperature but as temps go up the wheel gains strength and becomes more ductile, more stable," says Geoff. "It really is the dream material for this application."
At introduction tip diameters of EFR Gamma-Ti turbine wheels will range from 55mm to 80mm.
Turbine Housing
EFR turbine housings are cast out of stainless steel, which is extremely crack-resistant compared to conventional cast-iron housing that can buckle under the thermal loads produced by turbochargers. They are also lighter, and any weight savings inherently increases performance. Borg Warner uses an investment casting process generally seen in the jewelry-making industry because of its intricate detail and fine surface finishes. A smooth surface reduces friction and Geoff compares the effect to polished cylinder heads. He says the round shape of the EFR volute compared to the D-shaped volute in tradition housings also contributes to improved performance. The new housings range in size from a T25 .65 A/R to a T4 1.05 A/R.
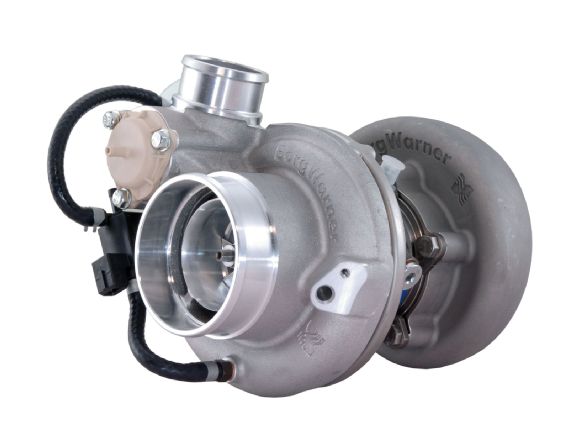
Further many of the hot side housings can be ordered with internal wastegates as an option. Also constructed via investment casting, the swivel-valve style wastegates are available in three different canister/spring combinations with 36mm or 42mm ports.
The Cold Side
The compressor side of the EFR turbo features six available billet compressor wheels ranging from 62mm to 91mm and EFR compressor housing outlets have been machined to accommodate either a standard hose connector or V-band connector and larger turbos employ a ported shroud that increases aerodynamic efficiency. Durability has been addressed with a dual ceramic bearing system and bearing housings with additional outlets for those who also want to water cool their center sections.
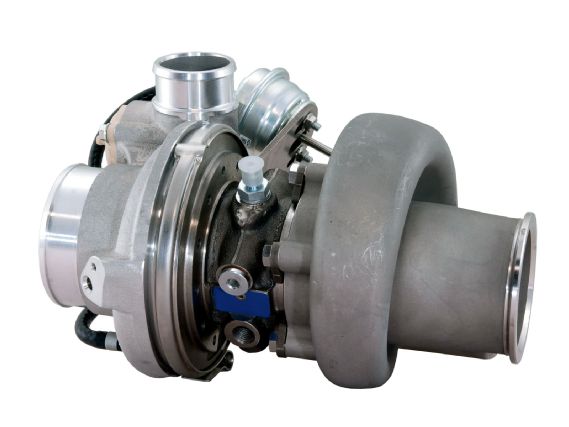
EFR Integrations
Borg Warner broke the existing turbocharger mold when it created the EFR line. One of the main goals was integrating other turbo system components into the turbocharger. This ploy can save time, money and headaches. The biggest integration is the inclusion of an integrated blow-off valve. No more bung welding on delicate intake pipes. The blow-off valve (BOV) is laid-out as a compressor recirculation device that redirects the charge air from the turbo's compressor outlet to a low-pressure point just before the compressor inlet, which really helps keep the unit spooled between shifts.
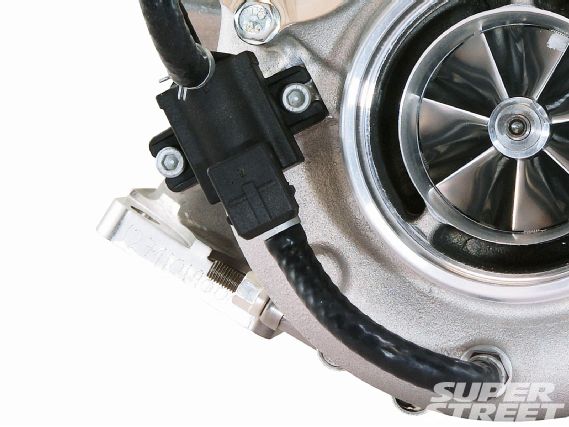
Also Borg Warner includes a boost control solenoid valve as standard issue on every EFR unit. This makes controlling boost easy whether an optional integrated wastegate or external wastegate set-up is employed.
The Bottom Line
The EFR turbo will look pricey at first glance but it represents a savings for professional turbo kit makers and hands-on enthusiasts who choose to fashion their own set-ups.
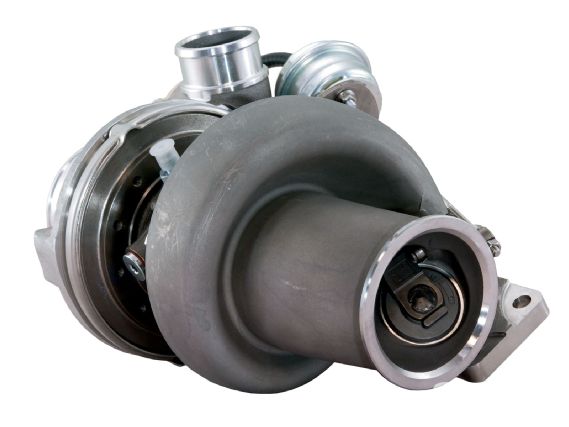
"The high-tech EFR presents huge savings to the applications that can take advantage of it. For example on our Subaru twin-scroll kit there are two wastegates at $350 each, a pair of dump-tubes is $400 for the pair, and the labor to put the wastegate ports on the manifold is about $500. Then the built-in BOV and BCSV represent at least another $300 to $400 savings."
"Unfortunately the EFR turbos are very large, and will NOT bolt up to most existing turbo kits. EFR turbos are meant for new installation/new design turbo kits."
The new EFR are a bold step and the mass production of titanium-aluminide turbine wheels represents a paradigm shift in engine boosting. Moving forward it will be interesting to see some apple-to-apple comparisons of traditional turbos and EFRs.