It's no secret the F22C loves boost. In fact, it's truly amazing just how much power can be had from this high-revving, high-compression 2.2-liter engine with the addition of forced induction. However, when building an engine for road racing/time attack, you must account for the extended loading and increased heat generation that's not experienced during street or strip use. Consequently, we assembled an array of the best engine internals available and had the pros at Gord Bush Performance (GBP) work their engine assembly magic to ensure our F22C would make reliable turbocharged power all day long.
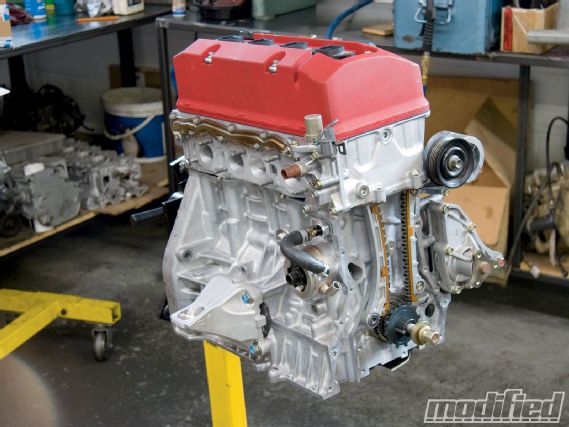
Our F22C came from an overheated AP2 that lost a rad hose, making it a perfect candidate to build. GBP wasted no time stripping the OEM long-block in preparation for the build. Everything was cleaned and prepared for assembly. Our first decision was to sleeve or not to sleeve, since the S2000's Fiber Reinforced Material (FRM) coating on the cylinder walls limit piston selection considerably. While sleeving would allow us to run the JE pistons we've had great success with in other applications, the reduced cooling capacity as a result of the sleeving process didn't meet our design requirements. Fortunately, the OEM S2000 pistons are a high-quality forged piece to start with, so they should support all the cylinder pressure we can throw at them. The guys at GBP inspected the cylinder walls and were pleasantly surprised to see that they were in excellent condition and didn't require honing. As a result of the overheat, the block/head mating surface was no longer flat and required .035 inches of material to be removed, a process that's child's play for a fully equipped engine shop.
With the bare block ready to go, the crankshaft was next up. GBP removed 5 lbs from the crank using a process called "knife edging," where the counter weights are chamfered on a lathe. While the reduced mass results in less inertial losses (think lightweight flywheel), one must be careful not to remove too much and upset the engine's balance. Following this machining process, the crank was polished and finally balanced along with the Competition Clutch twin disc clutch and flywheel setup.
With the crank looking lean and mean, it was time to assemble the bottom end. The Carrillo H-beam connecting rods were chosen for their quality and known history of being great performers. While there are cheaper alternatives available, the cost of connecting rod failure is always catastrophic and far outweighs the purchase cost of a top-quality set of rods, and that's why I chose Carrillo rods. It's the "pay a little more now and save a whole bunch later" thing.
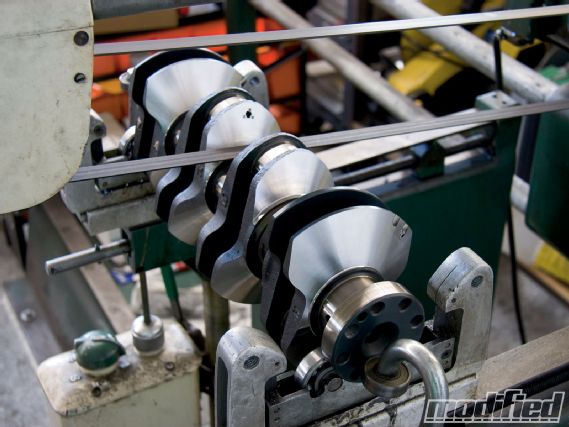
GBP honed out the Carrillo H-beam rods to accommodate the OEM Honda bearings (they're delivered at the tight end to ensure adequate material, depending on what bearing you use) and verified the big end/small end weights. All four rods were spot on. The OEM pistons were then fitted with fresh rings and the SPS-Carr rod bolts (which are reusable) were coated in the supplied heavy-duty, non-metallic anti-seize. Using the recommended stretch method (bolt length is measured at rest, then checked at incremental torque steps until the desired stretch is achieved), the target 0.005 to 0.007 inches of stretch was achieved for each fastener, ensuring perfect clamp load. Finally, a set of ARP head studs was threaded into the block to ensure the head stays put under the serious loads we plan to throw at it.
GBP wasn't done yet, though. Gord Bush himself (well known for some of the best flowing headwork) hand ported all of the intake and exhaust ports and cut a competition multi-angle valve job to accommodate the Supertech Inconel valves (1mm larger on the exhaust side). Inconel is a super alloy that maintains strength when subjected to extremely high temperatures, making it a perfect candidate to withstand the high exhaust gas temperatures typically found with a turbocharged setup.
You may be wondering at this point how well the OEM 11:1 pistons combined with a decked head and block are going to work with boost? Even with a stable fuel like the 114 octane Pro Fuels unleaded race gas we'll be running, trying to run big boost at over 11:1 compression could result in detonation. To protect against this, we ordered Inline Pro's 3mm head gasket, which measured out to a boost-friendly 9:1 compression ratio when combined with the material removed from our F22C's block and head. With sealant applied in the recommended location, the gasket and head were installed and the ARP head studs coated in the ARP Ultra Torque Lubricant before being tightened, following the OEM torque sequence to the recommended 95 ft-lbs.
Finally, with the OEM cams back in place along with a set of Supertech's new beehive valvesprings (slight increase in spring rate from stock to compensate for the positive manifold pressure acting on the intake valves) and titanium retainers, GBP clocked the cam drive gear to restore cam timing following the thicker head gasket install. As a finishing touch, a set of high-strength ARP exhaust manifold studs (2-inch length) was fitted to support the additional load from the turbocharger and manifold.
With our boost-friendly F22C long-block fully built and ready to rock, stay tuned as we fit the new twin-scroll Full-Race manifold with BorgWarner's new EFR series turbo and TiAl's water-cooled MVS wastegates. You won't want to miss it!