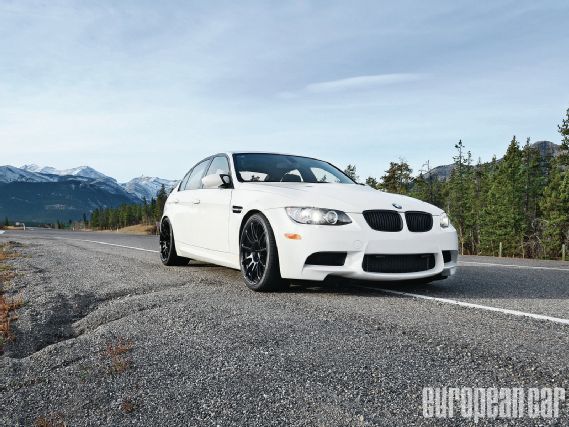
One thing’s for certain with every project build is that if you’re planning to add more power, you’d better be damn sure your chassis is ready for it.
This is especially true when you plan a huge power upgrade like we are for Project Q – remember “Q” stands for quick!
In this first working episode of Project Q, we blast out of the starting gates with a four-wheel big brake upgrade, coilover installation and set of new wheels. It’s a lot to bite off at one go, but it had to be done.
Let’s start first with the brake upgrade. The E9X M3 comes with the previous generation E46 M3’s Competition Package (CP) brake set up, which performs better than most factory brakes under track conditions. However, you can’t escape the mushy, uncommunicative pedal at the limit caused by its floating body and sliding calipers.
So we decided to go with a StopTech big brake solution for this upgrade because we’d gain strength, stiffness, less unsprung weight, track endurance and value for money. The pads are also easy to replace and there’s a wide variety of street and track choices.
The OEM rotors measure 360x30mm and 350x24mm, front and rear respectively. However, the StopTech kit provides greater mechanical leverage and heat capacity with larger 380x32mm front, and 355x32mm replacements. The narrow annulus (rotor surface swept by the pad), reduces the amount of cast iron required, thus reducing the weight.
The weight savings for the kit, including rotors, calipers, pads and associated hardware was about 6 lb front and 2 lb rear at each corner.
All StopTech Big Brake Kits include caliper mounting brackets and hardware, flexible stainless steel brake lines and their own Street Performance pads.
The installation is straightforward for anybody with some experience. Regardless, read the detailed instructions and if you don’t want to deal with it yourself, the R&R is about four hours of shop time.
Coilovers
Project Q will remain a daily driver with occasional track duty, so we had several handling goals: lower center of gravity, adjustable shocks and good ride quality. With this in mind we opted for KW Suspensions’ Variant 3 coilover kit.
From past experience, the KW V3 provides a high quality coilover system with true individual rebound and compression adjustability at a reasonable price point. It allows for a wide range of height adjustment and uses stainless steel struts.
For the M3, the V3 kit includes progressive rate springs to help the ride comfort while managing to keep things flat and firm when cornering. In addition, the rebound and compression adjustment make it possible to dial-in the right setting for either street or track.
Add another three hours of shop time if you’re a “wallet” mechanic, and don’t forget to have the alignment reset as well.
HRE
Next on our checklist was a performance wheel and tire upgrade. Most European OEM alloys can be classified as “lead weight” so we wanted something lighter yet strong. So we opted for HRE’s newest forged monoblock “R Series”. The motorsport design R40 was finished in satin black to make a bold statement on the white M3.
Weighing 21 and 22 lb for the 19x10 and 19x11" staggered sizing, these certainly met the criteria.
With the ultra-lightweight wheels, we were also able to increase our contact patch for improved traction. So we selected 265/30 R19 front and 285/30 rear Hankook V12 evo for “mostly” street use. This maximum performance summer tire is an excellent all-rounder – strong wet and dry performance, while being quiet, hard wearing and easy on the wallet.
On the Road
We’re happy to report the M3 chassis responded extremely well to all our upgrades. On the road, it feels solid but more agile. It’s eager to turn-in and is fully connected to the surface thanks to the better rubber, stiffer springs and damping.
Brake pedal feel is significantly firmer courtesy of the fixed-piston calipers taking the slack out of the system. The StopTech kit is easy to modulate and makes the braking seem effortless.
Now the chassis has been improved to our liking, it’s time to find more power. In the next installment we’ll execute our monster power upgrades with full dyno testing.
StopTech
Founded in 1999 with one mission, StopTech’s goal was to become the leading manufacturer and supplier of high performance brake components. Today, it’s a leading contender with more than 300 applications. The company is deeply involved in production car racing, specifically in the Speed World Challenge, ALMS and Grand-Am Cup series.
StopTech’s long association with top teams such as Turner Motorsport, GMG Racing, Tri-Point Motorsports, LG Motosports, Napleton Motorsports and Compass 360 Racing has validated its technology.
At their 75000sqft plant south of Los Angeles, the company designs and manufactures its rotors, calipers, DOT-compliant stainless lines, as well as complete upgrade systems for the street and racing markets. In fact, they currently hold three patents for their two-piece forged calipers with removable bridges, AeroHats and AeroRotors.
Of course, there’s an aesthetic appeal of big brake kits, and StopTech products will give your vehicle the enhancement every enthusiast will notice. Yet StopTech considers the “function” to be more important than the “form”. So its products are designed to exceed OEM performance in two important areas by firstly increasing the rotor size to gain mechanical leverage and heat capacity. Secondly, stiffer calipers and stainless lines reduce compliance. All this is achieved without upsetting the optimum brake bias. If the brake upgrade adds too much bias, it can reduce the car’s braking ability and actually increase stopping distances. Furthermore, when caliper pistons are too large, they make the brake pedal difficult to modulate, limiting your control.
So the engineering department utilizes 3D drafting and finite element analysis software during the design. Once prototypes are produced, they have two Link Engineering brake dynos to test the components. Test parameters may include repeated stops from up to 160mph, or extended driving cycles to measure wear rates for different vehicle weight. This is in addition to extensive real-world vehicle testing.