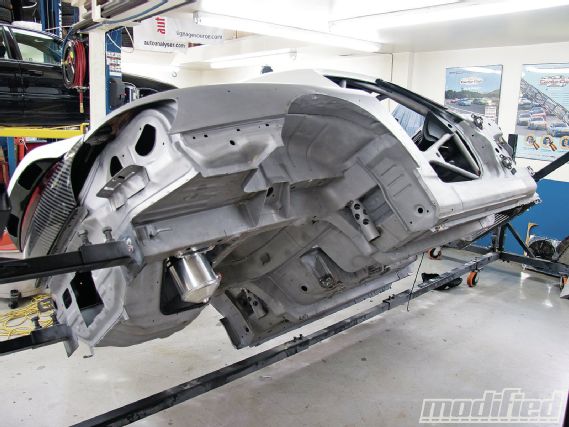
The ability to adjust the vertical position of the upper control arm pickup points in a ULCA (upper/lower control arm) suspension allows for adjustable roll-center height and anti-dive. These terms get thrown around pretty loosely, so let’s clear up what they actually mean and why we want to be able to adjust them.
Roll-center height is simply the vertical location of the point which the car rolls. The higher the roll center, the greater percentage of roll is resisted by the control arms (geometric load transfer) versus the spring and damper (elastic load transfer). If you move the roll center up to the vehicle’s center of gravity, you’ll achieve 100 percent geometric load transfer, and the suspension won’t move when cornering (though the total vehicle will still roll). More importantly, however, is the roll inertia and how this affects the vehicle’s response. Raising the roll-center height reduces roll inertia and, consequently, affords faster response during turn-in, which is great for tight circuits. Lowering the roll-center height increases roll inertia, causing a slower response at turn-in, which is better suited to high-speed tracks. One more thing that must be considered is that a high roll center will cause a vertical force component on the chassis that will raise ride height during cornering (though total load at the tires will remain the same). This can be an issue in long sweepers on cars like our S2000 that are ride-height sensitive for downforce production. A very low roll center (below ground) will cause the opposite, resulting in the ride height decreasing during cornering. I’d like to go more in depth on this, but space is limited.
Anti-dive is pretty much the sideview equivalent of roll-center height, and the same principle of transferring load through the control arms (geometric), as opposed to the spring/damper (elastic) to resist motion applies. The difference is it’s acting in pitch, instead of roll, allowing for manufacturers to limit nose-dive in braking while keeping relatively soft ride rates for comfortable travel on rough roads. This is most commonly achieved by installing the front upper control arm at an angle (approximately 5 degrees on an S2000) that also causes the wheel to regress in bump, once again reducing ride harshness. However, this non-vertical wheel path causes caster to increase in bump and will change the weight of the steering feel as the suspension compresses. Considering change in steering weight is a critical piece of information for a driver to know when the tire is at its peak lateral grip, removing this effect on a race car will certainly help improve lap times and consistency. This increase in caster will also cause a change in wheel loads to occur, reducing load on the outer front/inner rear and increasing load on the inner front/outer rear changing the balance of the car to oversteer through bumpy sections. Finally, using the control arms to resist pitch increases friction at the bushings, further hindering suspension performance.
Implementing these changes is often a challenging task, and the S2000 proved to be no exception. The first step was removing the upper control arm mounts (figure six to eight hours of spot-weld drilling). Use a hole-saw-type, spot-weld driller to leave locating dimples for reinstalling the mounts. Next, the mounts had to be pressed flat to remove the stamped angle feature for the OEM bushings to rest against. Knowing the upper arm inclination and with some basic trigonometry, it was possible to work out what needed to be machined while referencing the existing holes. We designed carrier rings to accommodate BRP adjustment pills available in 0.125-inch increments giving a total of 0.75-inch of vertical adjustment range and milled 0.75-inch slots into each upper arm mount. At this point, we reduced the anti-dive from 5 degrees to 2 degrees at the extent of the adjustment range. It’s also possible to get 0 degrees by running different front and rear pills. With some custom tooling, the rings were located and welded on to the upper arm mount and ready to be welded back on to the chassis. In addition to re-welding the drilled spot-welds, we also stitch-welded the mounts to ensure they will withstand the increased loads from slick tires and high downforce.
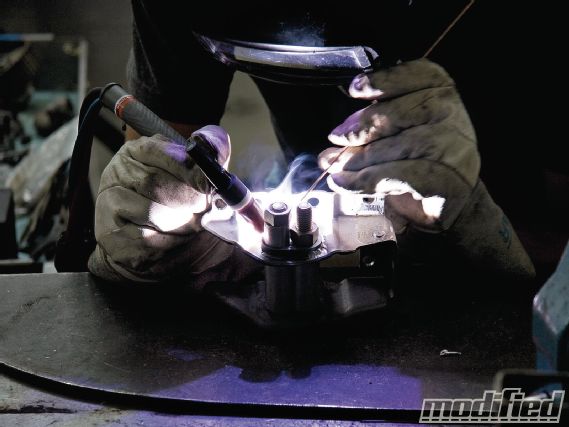
Finally, to help improve the stiffness of the mounts we fitted the elusive Spoon upper arm gussets sourced from AJ Racing. These are an OEM-quality part designed to eliminate issues regarding failed spot-welds experienced by AP1 S2000 owners on track. If you’re a track regular with an AP1 S2000, be sure to inspect your upper arm mounts for cracks. Cleaning the area and stitch-welding the mounts has proved to do the job and can’t hurt for the AP2 guys, either. You can also fit the Spoon gusset like we have to achieve worry-free track performance. Rumor has it Honda developed the upper arm gussets for testing, but never fitted them for production. Whatever the truth may be, they’re a very nice piece and greatly increase the strength and stiffness of the upper arm mount. Our sandblasted chassis made installation a breeze, and we were able to get nice welds all around.
With the custom front upper arm mounts complete, our S2000 is no longer at risk of tearing off its front control arm pickup points and has the adjustability needed to be dialed in at a wide range of circuits. With the anti-dive reduced, we can expect increased front grip and stability during cornering on rough circuits while offering more consistent feedback from the steering wheel to the driver. It’s the details like these that make a build like Project S2000 so time-consuming, but will pay dividends once completed and on track.
Source box
AJ Racing
Spoon Gussets
aj-racing.com
Bicknell Racing Products
Anodized inserts
bicknellracingproducts.com