While most people ignore it, there’s still pretty common knowledge that tires are the most important part you can throw at a car. And it makes sense because the rubber on your wheels is all that keeps a car on the road. But if tires are so important, then it would mean that the wheels they are mounted on play almost as important of a role in vehicle performance, right?
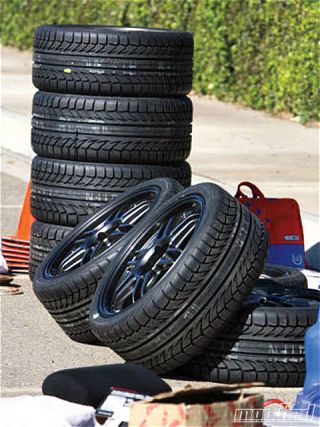
Most tuners pick wheels for looks and by reputation. Racers swear that lighter wheels will enhance performance, but no one seems to know by just how much. So we took it upon ourselves to do a performance wheel test by rounding up five different makes of wheels and running them through a gamut of our home-brewed tests. Each wheel came in the identical 18x8.5-inch size with a +30et offset (a conservative size for our EVO 9 test car) and was shod in identical brand-new 255/35/18 BFGoodrich g-Force Sport spec tires.
Our test wasn’t about which brand of wheels is necessarily best. More important was the real-world performance difference, if any, between wheels manufactured by different methods, and how much bang you get for your buck. So we picked five different types of aluminum wheels—cast and forged, single or multi-piece—to put to the test. Each wheel is JWL certified and at least passes the basic JWL strength and durability tests for safety. We intentionally picked products that span the entire market of reputable aluminum wheels. This way, we’d be able to see the extent of difference as each wheel is put through our real-world tests.
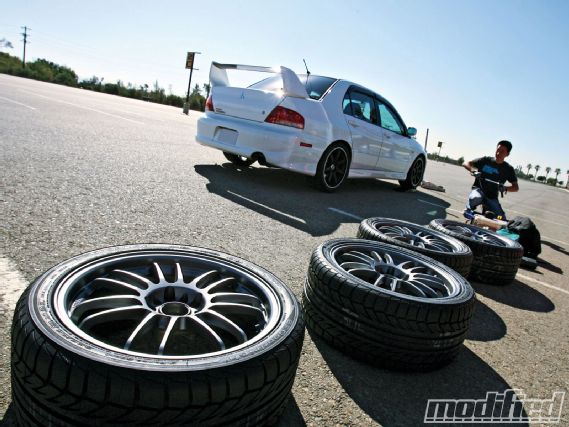
Whether in grassroots racing, drifting or professional time attack here or in Asia, 5Zigen’s FN01R-C line has proved to be one of the most popular and capable cast wheels to be found at the track. Although the wheel is gravity-cast like most entry-level street wheels, 5Zigen’s emphasis is on racing, robust construction, reasonable weight and cost, making this a great example of an affordable, high-quality, gravity-cast wheel. The engineers at 5Zigen designed and tested this wheel at the track and used computer-aided tools to optimize the strength characteristics of this traditional five-spoke design while minimizing unnecessary weight. These wheels are manufactured by pouring closely controlled molten aluminum alloys into a polished multi-piece steel mold, which minimizes the amount of machining necessary after casting.
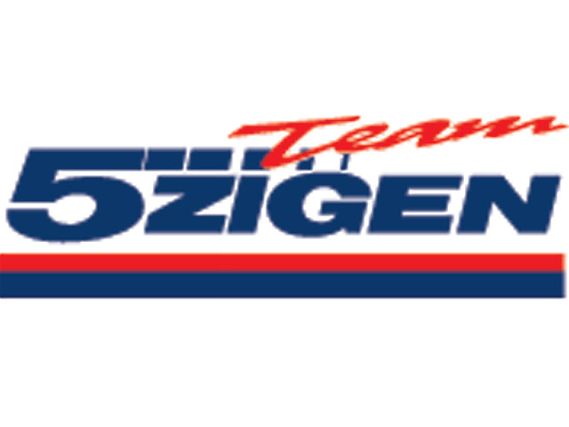
AME TM02
Manufactured by Enkei, the AME TM02 is AME’s first track-oriented wheel
sold in the U.S. The single-piece wheel uses Enkei’s patented MAT (Most
Advanced Technology) that combines conventional casting and
flow-forming forging in its construction. The wheel starts off as a
gravity die-cast wheel (using AC 4 CH aluminum material) with the hoop
structure cast narrow and with thicker material. The flow-forming
forging process takes the heat-treated cast wheel and then extrudes and
draws out the hoop to its final width and profile as the wheel is
spinning. Flow forming not only extrudes the wheel hoop to its final
shape, but also forges the wheel hoop section by compacting the
original cast-aluminum crystal structure to become more dense and
rigid, without creating breaks in the crystalline grain structure
(which causes brittleness).
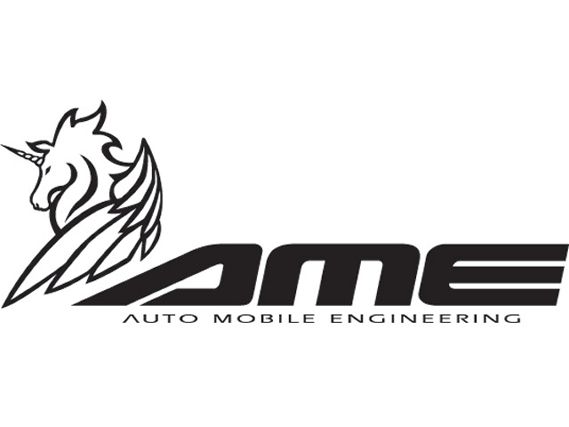
The cross-sectional profile that is drawn out is designed to optimize strength while reducing material and weight. This hybrid forging technique helps keeps this wheel’s price down. While other forged wheels also use a type of spinning extrusion process to flow forming the wheel hoop, Enkei claims that its process is differentiated by the combination of heat treatments, alloys and hoop profile. Above all else, Enkei/AME’s goal is to provide a high-quality wheel using efficient and cost-effective processes that are almost completely free from manufacturer defects with a very low defect rate.
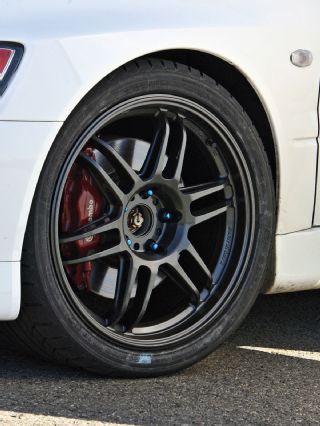
AXIS Halo
As one of the premier sport compact wheel manufacturers spawned
stateside, AXIS wheels has been around since the beginning. That means
the company also has a lot of experience in making street tuner wheels
that are stylish and long-lasting. The Halo is one of AXIS’ more recent
wheel lines that was designed with street performance in mind. This
means more spokes, less excess weight and no lip—all in a gravity-cast
package. While not track tested during development, the Halo is a good
reflection of a conventional gravity-cast wheel that most entry-level
consumers would be looking at.
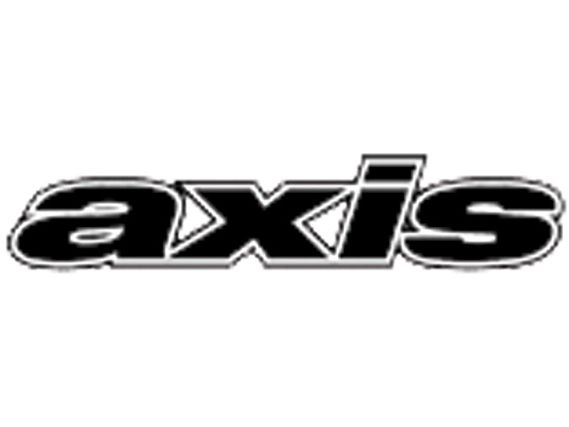
RAYS Volk Racing RE30
What’s a wheel test if we didn’t include Volk Racing Wheels. The RE30
is the newest in its line of forged monoblock wheels. Manufactured by
RAYS Japan (like all Volk wheels), the RE30 was designed as the premier
no-compromise, non-center-lock track wheel for maximum strength and
minimal weight.
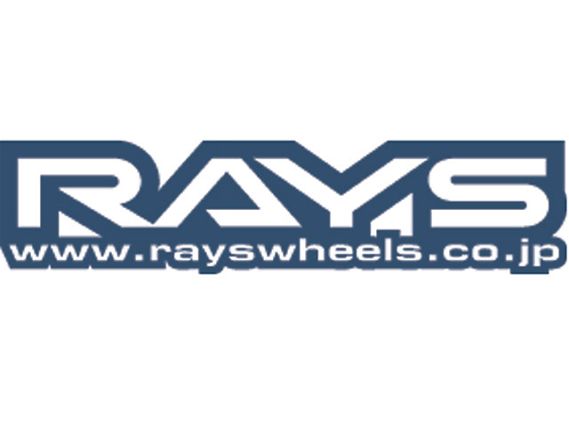
The patented RM8000 process is unique in that it uses an open die, which allows the aluminum to squish and expand naturally, thus ensuring continuous and dense metal grain flow. During RM8000 forging, the wheel face is simultaneously forged with pressure from the top and bottom, while at the same time spinning the wheel so the hoop is partially extruded out. The voids between spokes are then punched out and the inside of the hoop profile is formed. The wheel is then reheated and quenched for final strength. Machining is kept to a minimum as it increases stress risers and breaks in the metal flow. The wheel’s surface is also shot-blasted to add surface strength.
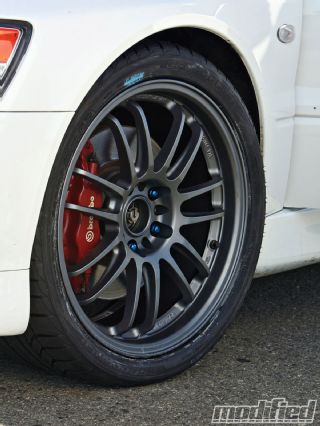
The RAYS forging process begins with its proprietary version A6061-T6 billet disk of aluminum (an alloy designed specifically for forging) that is first hot-forged into the rough shape of a wheel. This initial forging squishes the disk to create the features on the wheel face as well as the material that will be extruded into the hoop. A second proprietary low-heat forging process called RM8000 further refines the wheel shape and ensures the continuous grain and metal flow throughout the wheel.
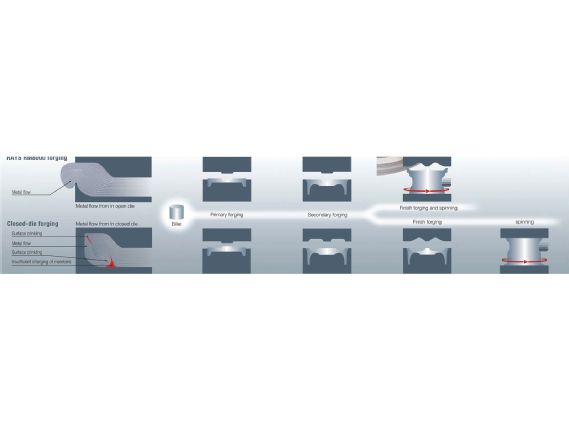
SSR Type-F
The only multi-piece wheel in our wheel test, the Type-F is SSR’s
replacement wheel for the venerable Type-C. The face of the new type is
made from SSR’s patented SSF (semi-solid forging) process. SSF starts
with an extremely pure aluminum that’s been alloyed and treated through
a process called Magneto-Hydro Dynamics (MHD) to have an ideal
crystalline structure. The alloy is then heated to a semi-solid state
and then forced into a die at high pressures and speed, causing the
metal to take the shape of the wheel face while still retaining its
original microstructure and continuous grainflow. This is much denser
and stronger than conventional casting. The wheel’s hoop is spun and
heat-treated to increase hoop strength before it is welded to the
Type-F face.
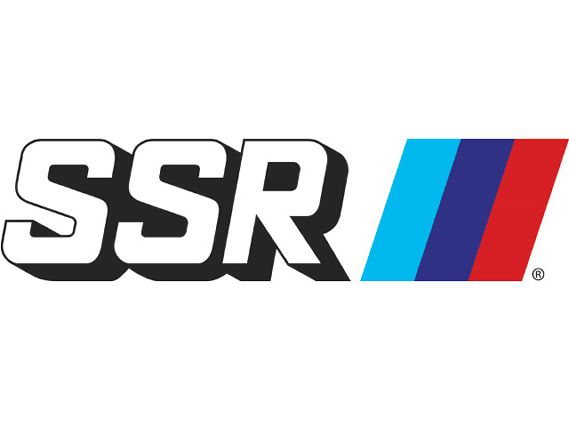
First off would be the simple tests that everyone looks for: price and weight, which we’ve listed on page 96. One thing to keep in mind is that lighter doesn’t necessarily mean better or stronger. While a light wheel will have less unsprung weight, it doesn’t necessarily mean that it has less rotational inertia. Much of that has to do with how the material is distributed throughout the wheel. Less weight can also mean less strength if the wheel wasn’t strengthened through forging.
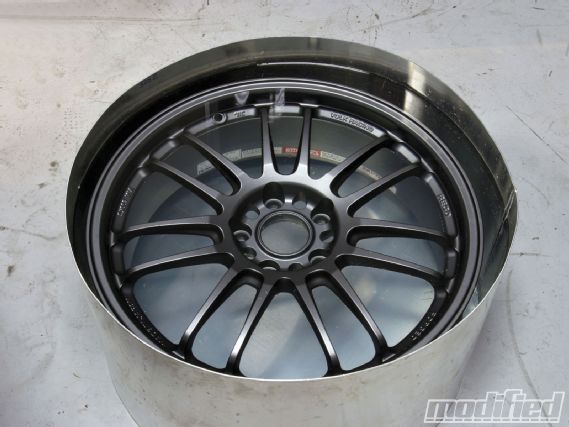
While we’re no metallurgists, the average density of each wheel can also say something about its strength. Each wheel is made of aluminum, and the more densely the metal is compacted together or forged, the stronger the wheel is. But because no one would give us exact material properties or the computer-generated solid model files of each wheel that would allow us to determine wheel volume precisely, we resorted to dunking each wheel inside a tub of water and figuring out how much water it displaces. Divide the wheel volume by its weight, and we have a ballpark density for each wheel, even though this included the paint on the wheel. Either way, the forged wheels should have a higher density than the cast wheels.
One other physical aspect of a wheel is its mass moment of inertia (more commonly referred to as rotational inertia). Rotational inertia basically indicates how hard it will be to start and stop a wheel from spinning.In theory, this will affect braking and acceleration performance. But rotational inertia is affected not only by a wheel’s weight and shape, but more importantly how the weight is distributed throughout the wheel and its overall size. Two same-weight wheels could have vastly different amounts of rotational inertia if the weight or metal in the wheel was distributed differently. A wheel with a heavy hoop will have more rotational inertia than an identically heavy wheel whose weight is mostly in the hub.
Units of rotational inertia are impossible for most to understand and even harder to relate to, so we opted for a real-world test where each wheel and tire was mounted on the same car and spun up to 30 mph on the dyno. From there, we measured the amount of time that it took for each wheel to slow down to 5 mph (since data at lower speeds becomes more and more unreliable). The idea is that the wheel with less weight and rotational inertia will come to a stop faster than a wheel with more rotation inertial. To be consistent, each tire was inflated to the same cold pressures and given the same amount of rolls on the dyno under identical conditions.
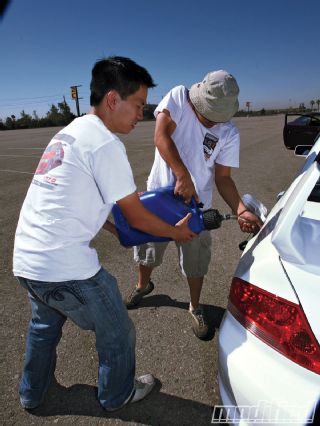
Physical properties aside, the biggest question was whether these vastly different wheels would result in noticeably different lap times on our Figure 8 test track. The Figure 8 is basically two 200-foot-diameter circles spaced 500 feet apart from center to center. This configuration allows us to test how a car accelerates, brakes and performs in average lateral grip and transitional handling.
With apples-to-apples real-world testing in mind, we took out a mildly tuned Mitsubishi EVO 9 on JIC coilovers as our test car. Each wheel was pressurized to the same cold tire pressure and the car was topped off with fuel before each run so that weight did not change. Each brand-new set of wheels and tires were sent out for two scrub-down laps before starting its 10 continuous recorded laps. Through our vehicle telemetry data and driver input, we would be able to see if one set of wheels allowed the car to consistently accelerate or brake faster and have more stable steering transitions in addition to overall lap times.
The one test we didn’t get to pursue—and possibly the most important—concerns wheel strength. We had originally designed a very precise test on a hydraulic press to squish every wheel and measure how much each wheel would bend for a known amount of force applied, but that would have pegged the nerd meter. So we opted to get a rental car and have our test driver Andy Hope crash into some curbs for our testing/entertainment. Apparently, our legal department had some issues with that, so we unfortunately came up empty on real strength testing.
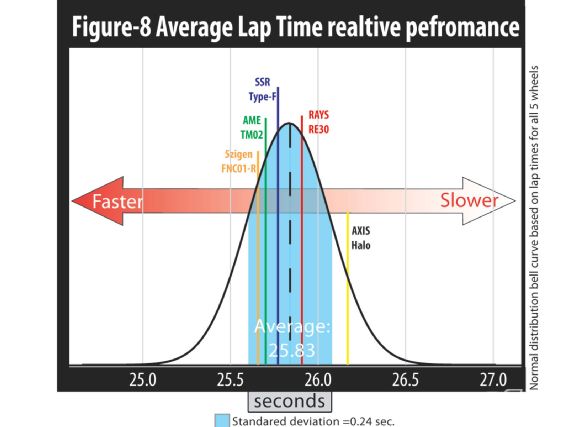
As expected, our real-world rotational inertia test did show a difference between lighter and heavier wheels. Wheels with less rotational inertia (i.e. easier to accelerate and decelerate) took less time to decelerate from 30 mph to 5 mph on the dyno. But more importantly, the time each wheel it took depended more on the tire temperature and how it changed rolling resistance. As the tires heated up after just one cold run, the change in rolling resistance was more than the difference between all the wheels.
As expected, the fully forged monoblock Volk RE30 was the lightest and densest among the wheels. At 17.4 lbs, it’s 3.5 lbs lighter than the heaviest wheel and more than 25 percent more dense than the least dense wheel while taking up the least volume. The two-piece Semi-Solid Forged SSR comes in just 1-lb heavier, even though its density is similar to that of the other conventional cast wheels. In terms of physical properties, each wheel reflects its price point almost proportionally.
This makes sense because most of the mass is in the tire. At 25.4 lbs, each tire weighs more than the wheel itself, and because it’s at the outer diameter of the rolling stock, its effect on rotational inertia will have a much larger effect than minor differences in rotational inertia within each wheel.
Performance-wise, the differences were not as significant. With the same car, same fuel load, same number of laps and identical-wear tires, the difference between average lap time for the fastest and slowest wheel was a scant half-second. Averaged over all the different wheels, our EVO’s average lap time on the Figure 8 is 25.83 seconds, which means we’re splitting hairs in terms of a noticeable handling difference between the wheels.
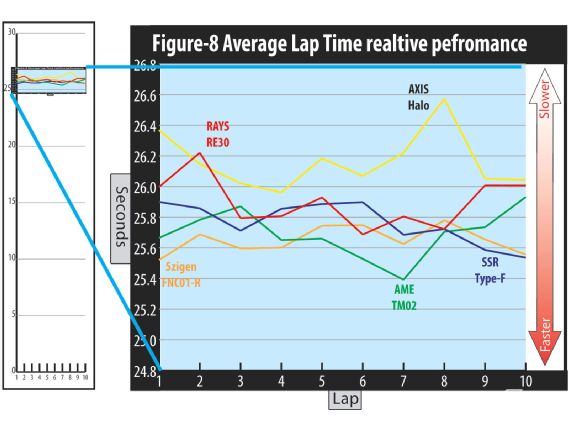
The 5Zigen wheel was consistently faster than most and on average the fastest while the AXIS wheel was the slowest. Ironically, both are gravity-cast and the cheapest of the wheels. While the results are real, if we factor in minor variations between each lap and the couple-degree change in track temps, we think claiming one wheel to be faster would be unwarranted.
Even through using some statistical tools, only the AXIS wheel was conclusively slower than the rest since its average time fell outside of one standard deviation of all the samples. The performance results did not correlate with the order or time of day (even though track temperatures remained reasonably consistent). So for this test, the generally accepted theory is that lighter and stronger didn’t actually equal faster. If we had tested on a longer actual circuit, the differences might be more significant, making all the difference if you were in a race. But more complex courses also add in more testing inconsistencies.
If you’re aching to see a Part 2 destruction test, let us know.
MANUFACTURER RAYS SSR AME 5Zigen AXIS WHEEL CE30MSRP (USD)
Weight (lbs)
Wheel Volume (cc)
Average Density (kg/m^3)
$900
17.4
1525
5134.43
$700
18.4
1965
4213.74
$620
20.3
2250
4060.00
$340
20.8
2250
4150.00
$325
20.9
2125
4425.88
Free roll time from 30-5 mph on cold tires (sec)
50.7
49.6
50.8
50.7
50.6
Average lap time
Fastest lap time (sec)
Slowest lap time
25.898
25.687
26.221
25.764
25.536
25.900
25.692
25.392
25.932
25.652
25.521
25.780
26.164
25.962
26.574
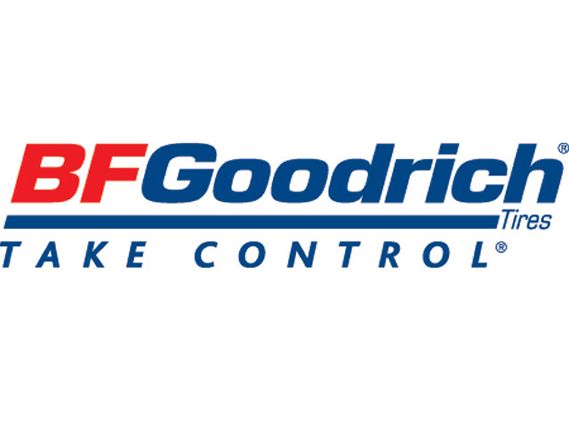
In the end, we settled on using ultra-high-performance tires with significant levels of grip for a street car, and the predictable handling and progressive break-away characteristics for consistent lap times. Based on our previous experience, we decided on the g-Force Sport tire from BFGoodrich. Although the Sport is not as sticky as its predecessors, it is a better reflection of a street tire that a serious performance-oriented street tuner would buy. The added grooves in the tread pattern also enhance wet traction as well as take the peakiness out of the tire. Tire wear is also extremely reasonable with a UTQG rating of 340 AA A. It’s also affordably priced. The guys at BFGoodrich made this entire test possible by providing us with 20 brand-new 255/35/18 tires so that we could test each wheel on the same day under the same conditions.