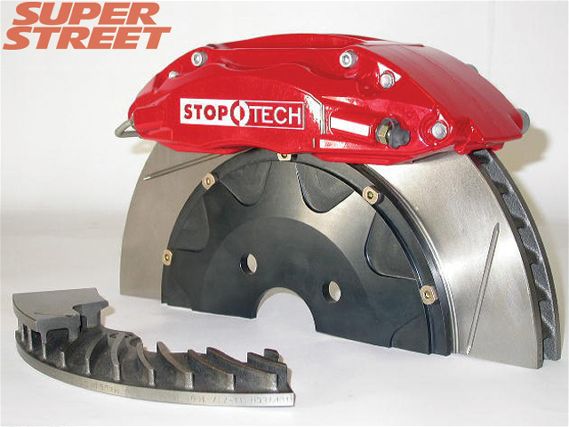
Big brake kits are often times the most overlooked, but most important, upgrades when it comes to customization. Aside from the aesthetic beauty of having large rotors landscape your new wheels, brakes play a key roll in stopping vehicle with large hp gains, bigger wheels or simply for those who live in cold-weather conditions.
Upgrading to a big brake kit generally means that you run a larger brake disc, a caliper with more clamping force, as well as brake discs, which are either vented, slotted or sometimes a combination of both. But to better understand braking technology and the important factors to consider, we were able to get some very useful information from Dan Barnes over at StopTech. The following information will give you a better understanding on what to look for as well as some of the key components of what make big brake upgrades so important.
While almost every current passenger car is capable of a single stop from maximum speed at or near the limit of tire adhesion, the braking systems of most passenger vehicles and light trucks and some sports cars are not adequate for hard or sport driving or for towing. Most stock brake systems lack sufficient thermal capacity; the system's ability to absorb and transfer heat by conduction, convection and radiation into the air or surrounding structure during severe driving. In addition, many stock calipers and their mountings are structurally not stiff enough at higher line pressures and the resultant higher clamping loads.
That's why even though there's enough front brake torque to lock the front wheels at highway legal speeds, caliper flex at the increased system pressure required to stop the car from high speed may prevent wheel lock-up. Needless to say, most OEM brake pads are also not designed for severe use, since cold stopping performance and quiet operation typically are considered more important to new car buyers.
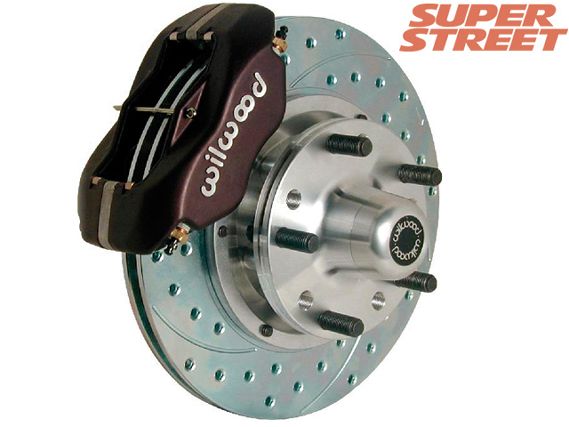
There are a few basic facts that must always be kept in mind when discussing brake systems:
1) The brakes don't stop the vehicle, the tires do. The brakes slow the rotation of the wheels and tires. This means that braking distance measured on a single stop from a highway legal speed or higher is almost totally dependent upon the stopping ability of the tires in use, which, in the case of aftermarket advertising, may or may not be the ones originally fitted to the car by the OE manufacturer.
2) The brakes function by converting the kinetic energy of the car into thermal energy during deceleration, producing heat, lots of heat, which must then be transferred into the surroundings and into the air stream.
The amount of heat produced in context with a brake system needs to be considered with reference to time, meaning rate of work done or power. Looking at only one side of a front brake assembly, the rate of work done by stopping a 3,500-pound car traveling at 100 mph in eight seconds is 30,600 calories/sec or 437,100 BTU/hr or equivalent to 128 kW or 172 Hp. The disc dissipates approximately 80-percent of this energy. The ratio of heat transfer among the three mechanisms is dependent on the operating temperature of the system.
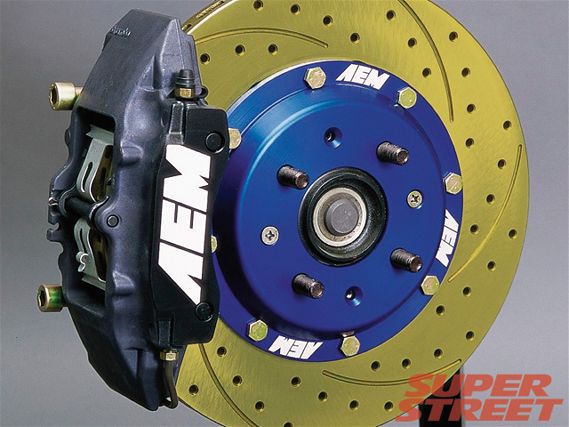
The primary difference being the increasing contribution of radiation as the temperature of the disc rises. The contribution of the conductive mechanism is also dependent on the mass of the disc and the attachment designs, with discs used for race cars being typically lower in mass and fixed by mechanism that are restrictive to conduction. At 1,000 degrees F, the ratios on a racing two-piece annular disc design are 10-percent conductive, 45-percent convective and 45-percent radiation. Similarly on a high performance street one-piece design, the ratios are 25-percent conductive, 25-percent convective and 50-percent radiation.
Braking performance is about more than just brakes. In order for even the best braking systems to function effectively, tires, suspension and driving techniques must be optimized. For maximum brake potential, vehicles benefit from proper corner weight balance, a lower CG, a longer wheelbase, more rear weight bias and increased aerodynamic down force at the rear.
To go further it is necessary to understand some of the physics involved, and that requires some definitions.
1) Mechanical pedal ratio: Because no one can push directly on the brake master cylinder(s) hard enough to stop the car, the brake pedal is designed to multiply the driver's effort. The mechanical pedal ratio is the distance from the pedal pivot point to the effective center of the footpad divided by the distance from the pivot point to the master cylinder push rod. Typical ratios range from 4:1 to 9:1. The larger the ratio, the greater the force multiplication (and the longer the pedal travel).
2) Brake line pressure: Brake line pressure is the hydraulic force that actuates the braking system when the pedal is pushed. Measured in English units as pounds per square inch (psi), it's the force applied to the brake pedal in pounds multiplied by the pedal ratio divided by the area of the master cylinder in square inches. For the same amount of force, the smaller the master cylinder, the greater the brake line pressure. Typical brake line pressures during a stop range from less than 800 psi under "normal" conditions, to as much as 2,000 psi in a maximum effort.
3) Clamping force: The clamping force of a caliper is the force exerted on the disc by the caliper pistons. Measured in pounds clamping force, it's the product of brake line pressure, in psi, multiplied by the total piston area of the caliper in square inches. This is true whether the caliper is of fixed or floating design. Increasing the pad area will not increase the clamping force.
4) Braking torque: When we're talking about results in the braking department we are actually talking about braking torque; not line pressure, not clamping force and certainly not fluid displacement or fluid displacement ratio. Braking torque in pounds-feet on a single wheel is the effective disc radius in inches times clamping force times the coefficient of friction of the pad against the disc all divided by 12. The maximum braking torque on a single front wheel normally exceeds the entire torque output of a typical engine.
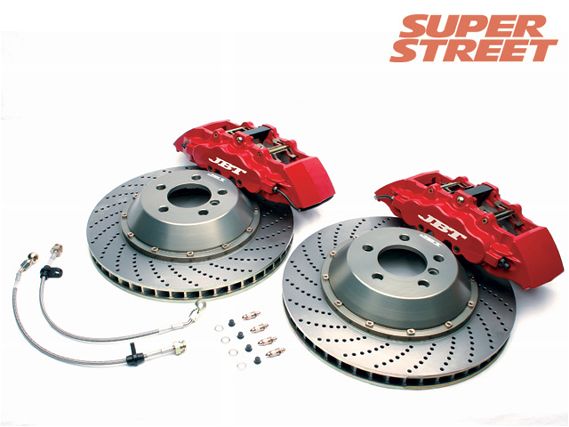
DRILLED VS SLOTTED ROTORS
For many years, most racing rotors were drilled. There were two reasons-the holes gave the "fireband" boundary layer of gasses and particulate matter someplace to go and the edges of the holes gave the pad a better "bite."
Unfortunately, the drilled holes also reduced the thermal capacity of the discs and served as very effective "stress raisers," significantly decreasing disc life. Improvements in friction materials have pretty much made the drilled rotor a thing of the past in racing. Most racing rotors currently feature a series of tangential slots or channels that serve the same purpose without the attendant disadvantages.
PAD AREA
We have seen that brake torque is directly proportional to Piston Area, System Pressure, Friction Coefficient and Effective Radii, and is not affected by pad area. Pad area and geometry are however important for several reasons:
1) Pad service life. Since pad material is consumed, an increase in pad area results in an increase in the time interval between pad replacements. OE designs often make slight sacrifices in pad life by including tapered ends for reduction of noise, vibration and pad taper. In some OE designs, the pads on the two sides of the caliper are even shaped differently, with the inside pad being shorter in arc-length in the direction of rotation and wider radially than the outside pad for system design and integration reasons.
2) Heat dispersion and dissipation over a larger surface area and greater mass. Although in the case of a larger pad, the pad masks a larger portion of the rotor face, absorbing more radiant energy and shielding the area from cooling that may cancel any actual benefit.
3) Geometry: Since rubbing speed between the disc and the pad is greater at the periphery of the disc, the pad geometry will sometimes be designed to reduce the area toward the center of the disc. This is done in an effort to produce even temperature and pressure distribution across the face of the pad.
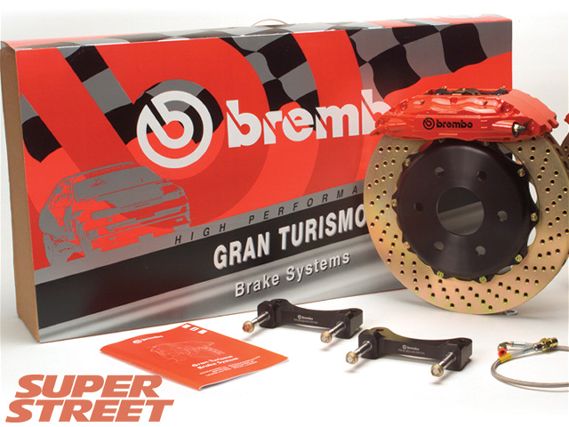
FLOATING DISCS
All metals "grow" when heated. The diameter of cast iron brake discs can increase as much as 2mm (0.080 inch) at elevated braking temperatures. When the disc is radially restrained from growing (as in all one-piece discs) the friction plates are forced into a cone shape as temperature increases, adversely effecting both temperature and pressure distribution within the pads and the feel of the pedal.
Racing and high-performance street discs are mounted on separate hats or bells, usually of aluminum. The fastening system is designed to allow radial growth and minimal axial float resulting in a mechanically stable system. Hats or bells should be made from 7075 or 2024 heat-treated aluminum billets that are pre-stressed and relieved, not from 6061 or from plate stock.