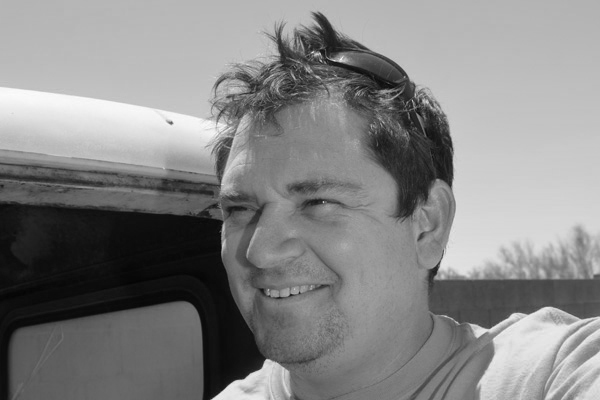
Verne Simons
Senior Editor, Jp
Building a Jeep for hard use off-road means that failures can occur. Generally you can plan to deal with a few common failures. For example it's a good idea to carry a spare fuel filter or U-joint or two, but when we broke our rear axlehousing in two several months back ("Unintended Consequences,"July '13), there wasn't much we could do except drag the Jeep home and start looking into a replacement. Fast forward a few months and we showed you the fancy new Dana 44 that Dynatrac built to replace our old shattered Dana 44 in "Next Generation Dana 44,"(Nov. '13). That article opened the book of tricks that a custom axle builder like Dynatrac can toss at a replacement axle for a 65-year old Jeep, and once it arrived in our hands we spent hours drooling over the sexy, super strong next generation Dana 44. The truth is we wasted so much drool and time that it took us a while (remember the other articles we were working on for your favorite magazine…neither do we) to get the sexy hunk of steel under our old tan Willys. Never able to pass up an opportunity to answer our readers' questions, we decided to show and tell how we installed our new axle under our old Jeep. We also are not good at leaving things as they are, so we stretched the wheelbase of the CJ-3A a few inches using an old and tricky set of leaf springs. We'll show how we set the pinion angle and clamp the leaves to the axle. We also added a redundant air system because our engine driven Harrison R4 air compressor always scared us a little and with two air-operated locking differentials we wanted to be sure we would have some air pressure and thus traction to get down the trail. Follow along as we take this awesome axle and get it under our old-school custom rockcrawler.
Mounting Shocks
PhotosView Slideshow
We occasionally get questions on mounting shocks, and like how there is more than one way to skin a cat there is more than one way to mount a shock. If space allows (that is if you have relatively wide axles), it's easy to run the rear shocks outside the framerails. This allows you to either use long upper shock mounts or if your cage is tied into the frame use the cage ties as an upper shock mount. Our Dynatrac axle came with new lower shock mounts, but we modified the old beat-up lower rear shock mounts as upper shock mounts. We did this by cutting the mounting point off the old mounts and welding it to one of our cage frame tie in runners. Here we'll let the pictures do the talking.
Step By Step

Our new next-generation JK-based Dana 44 from Dynatrac arrived all crated up. We arranged for the axle to be delivered at a friend’s place of work where they have a loading dock. That helps save shipping costs since if the axle was delivered to our house we would have to have paid an unloading fee. Once our buddy called to tell us the axle had arrived we rushed over with our ’78 J10 pickup, Piggy the Pig truck, and a couple of ratchet straps.

Once we got home we started getting ready to swap the axle in place. Dynatrac has years and years of experience setting up their custom axles so that they are an easy bolt in affair…that is assuming you are keeping your suspension setup the same. We knew we wanted to change things up a little to get just a touch more wheelbase out of our old Flattie. To do this we sourced a pair of used front springs from a ’74-or-newer FSJ.

Late model FSJ front leaf springs are similar to YJ lift springs. Only difference is that FSJ springs like the ones we have are a little bit longer in overall length. But more importantly the centerpins are offset a couple of inches from the center (top), while YJ leafs have a truly centered centerpin (bottom). That means installing these in place of YJ springs will move the axle two inches forward or backward. Our plan was to use the main and second leaf from the FSJ pack supplemented with four other leaves borrowed from some spare YJ lift springs we had. This should allow us to stretch the wheelbase of our Willys that used to run 3.5-inch YJ lift springs.

After pulling our very broken axle, we used a friend’s huge hydraulic engine hoist to unload and uncrate the axle. It’s lighter than a semi-float Dana 60, but heavier than the old school Dana 44 it replaces. The crate is pretty darn nice. We contemplated turning the crate into some shelves for extra storage in our garage…or keeping it as an inexpensive alternative to a coffin just in case we kick the bucket any time soon.

Dynatrac’s U-bolt Flip Kit allows for more ground clearance all in a well-engineered and stout product. Pushing the axle back on the modified spring perches meant we had to drill a new centerpin hole in the lower plates of the Dynatrac U-bolt Flip kit. Our old axle was pushed back an inch from the center of the spring with offset spring plates so the new spring plates from Dynatrac were also drilled to so the axle would sit in the same location…before our leaf spring stretch.

The passenger side of our new offset rear axle has the centersection basically butted up against the leaf spring. This means we had to set the Dynatrac U-bolt flip kit like it was a front axle. Dynatrac sent a raw upper U-bolt retaining plate with the metal rod keepers not welded in place and a longer lower U-bolt plate. We welded the rods to the plate offset a little to clear part of the cast centersection and drilled the lower plate for our offset centerpin.

With the axle in place and the U-bolt flip kit modified we bolted everything back in place, tightening the U-bolts enough to suck everything together, but not so tight that we could not get the axle to rotate on the spring perches. This allowed us to put the weight of the vehicle on the axle and set the pinion angle using a rubber mallet and a by raising the jack under the pinion snout. In a Jeep with leaf springs and a double cardan rear shaft, you want the pinion one to two degrees below pointing directly at the output of the T-case.

Once the pinion angle is set, double-check that the axle is centered side to side and tack weld the spring perches to the axle. You may have to remove the U-bolts to fully weld the perches. We were able to weasel the tip of our welder in to the right place without unloading the axle and pulling the U-bolts. Once everything is welded in place, you can torque the U-bolts to spec and chop off the excess threads.

The last few steps in installing the axle in our flattie involved bending up and flaring some hard rear brake lines and installing a set of TJ rear soft brake lines. Dynatrac included a few little tabs for all this to go on the axle cleanly. We also added some big ol’ bumpstops that a neighbor gave us to the top U-bolt flip kit plate and finally installed our shocks.

When we learned our rear could be built with 35-spline shafts, we knew we wanted to go ARB Air Locker. So having a reliable air source was a must. We mounted this ARB High Output Twin On Board Air Compressor to our passenger-side rear fender and plumbed it to our rollcage/air tank. It turns out this was good insurance, as our engine-driven Harrison R4 compressor that we converted as an air compressor died on our shakedown run.

One other issue we had to deal with as a result of the rear axle stretch was our existing rear driveshaft from Tom Wood’s Custom Drive Shafts was now too short, so we called Tom back up for a little longer replacement. As for retirement for the old shaft, it won’t come soon. It seems to have just enough slip-spline to work in a pinch, so we’ll carry it as a trail spare. Can you tell which one is the new one? Here’s a hint: It’s a little longer. Oh, and the old one is slightly beat up.