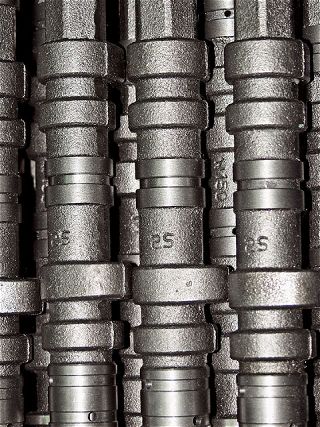
In 1994, Skunk2 started out as Group-A Autosports, Inc. It was primarily a racing development and performance parts distribution company that focused on selling highly specialized racing components. In '98, Group-A took on the Skunk2 identity and established the Skunk2 Racing line of products to meet the demand for street-based performance products. The company quickly became recognized as being run by enthusiasts for enthusiasts.
Throughout its life, Skunk2 has been deeply involved in motorsports and invests heavily in technology, both to illustrate the durability of its products and to continually push the development envelope. They also believe that racing provides them with the data necessary to produce high-performance parts utilizing innovative design, advanced composites, cutting-edge manufacturing methods, and stringent quality control measures. With this in mind, Skunk2 subjects its products to road and race testing to ensure proper performance in the harshest conditions.
As a cam maker, Skunk2 has been a leader. Notable Skunk2 innovations include being the first U.S.-based performance company to "chill cast" billet camshafts for Honda engines in 1999, and is currently developing camshafts utilizing its AMAX and fast ramp technologies. Dave Hsu, of Skunk2, recently gave us a guided tour into the world of camshaft manufacture.
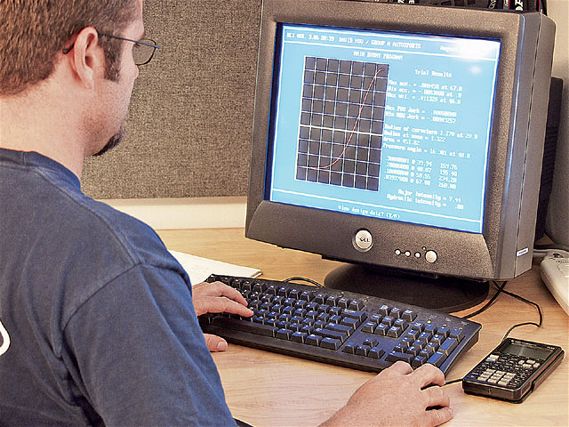
After a company decides to produce a camshaft for a given application, research and development begins typically by determining how a particular cam profile will work in the given engine under specific conditions, with a goal in terms of output, or horsepower and torque. Most engineers will use several forms of development software that essentially allow the designer to model the valvetrain, design the cam profile, and simulate the performance on a computer. The simulation programs work by simply plugging in the cam profile figures or other engine specs into the program, then the simulation software calculates theoretical output and efficiency. Once a desired camshaft profile is designed on the computer, engineers use CAD to render blueprints and cam profile lift tables to be entered into the CNC grinding machines.
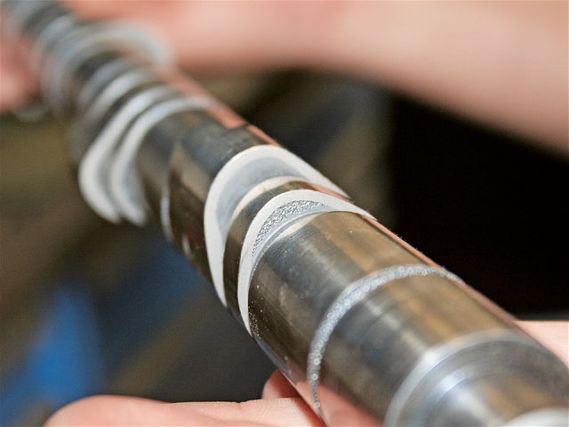
Next, prototypes are manufactured for engine dyno testing. Many of their prototypes are made using hardened steel billets or hard welding and grinding the lobe face of an existing production camshaft. Extensive engine analysis and dynamic testing is done on the engine dyno, and then final versions are agreed upon after the evaluations reach the desired results.
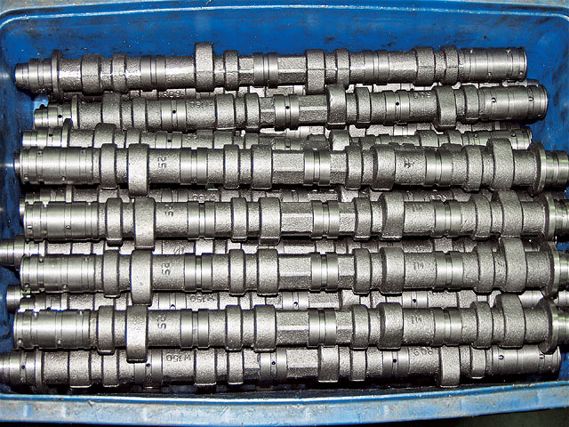
The blanks, or cores, are then cast at specialized foundries. The big question among cam makers at this stage is: which material is best suited for the valvetrain the cam is going into? In the Honda world, generally speaking there are 2 types of valve trains:
Ones where the rocker arms are the follower or sliding variety (where the cam slides along a pad on the rocker arm), like in B-, H-, and D-series engines.
Ones where the arms have rollers, or roller rockers, as in the heads of F20/22s and K-series mills
Each type of valvetrain requires cams made from different material, based largely on wear resistance and suitability of manufacturing for the projected volumes. Depending on application and whom you talk to, blanks will generally be either some form of chilled cast iron, steel billet, or ductile iron alloy. The performance of each material can further be improved by adding or subtracting certain component elements found in the material alloy and also through optimizing the heat treatment parameters.
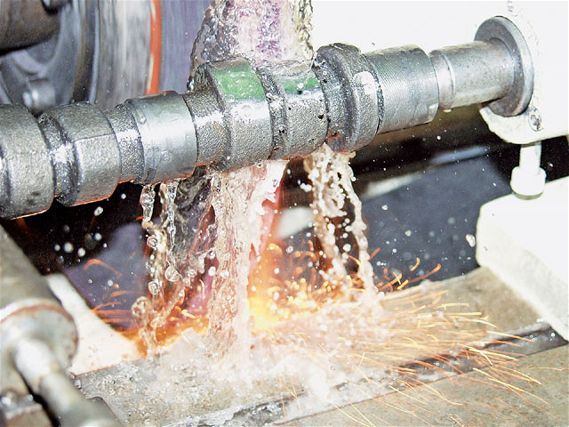
First, the journals are ground. Then the camshafts are "rough" ground and ultimately, "finish" ground. Different stones at differing speeds are utilized depending on the stage or material being ground. Traditionally, lobe profile grinding requires using a cam lobe master that is plugged into a cam-grinding machine. A follower mechanism traces the master as the grinding wheel grinds the exact profile of the master onto an un-ground cam, like copying a key. Skunk2 uses CNC master-less cam grinding machines that grind cam profiles directly from the computer generated design data. When compared to traditional cam grinding, CNC grinding is much quicker, more accurate, and eliminates human error from the grinding process. Skunk2 makes a point to use CBN (cubic boron nitride) grinding wheels for superior accuracy and surface finish.
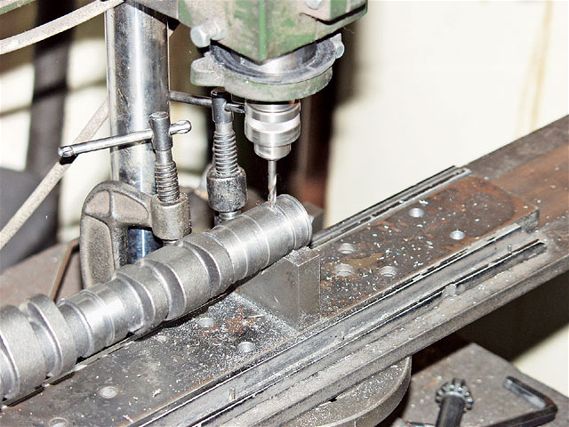
To reduce mass and provide passageways for the oil to penetrate the shaft (for cooling) in certain applications, some manufacturers, like Skunk2, use as-cast or rifle-drilled hollow cams.
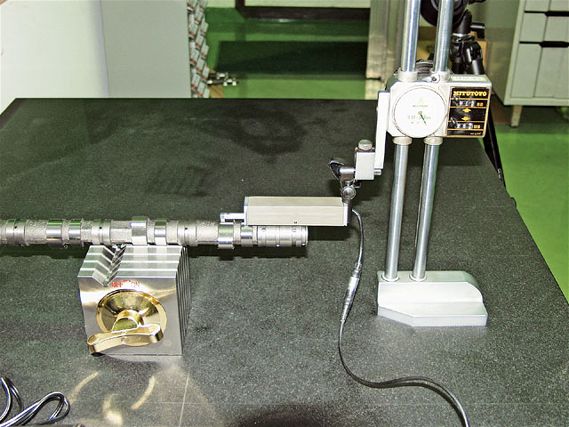
Finally, each cam is checked for straightness, and profiles for accuracy. Then, in many cases, they receive a final polish and some form of corrosion resistant finish.