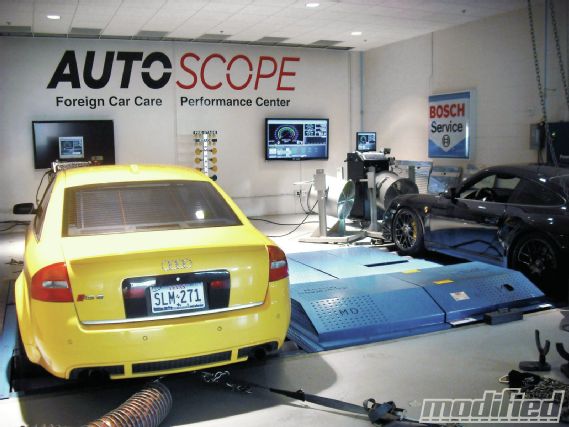
Chassis dynamometers (or what we commonly refer to as a dyno) have become an essential tool in the pursuit of maximum engine performance, regardless of whether you’re building a modified street machine or a full-on race car. Before the widespread use of chassis dynos, the street car crowd was dialing in its ignition and fuel timing on the street, a potentially dangerous and even illegal activity, given the need to make repeated wide-open throttle blasts to redline in third or fourth gear. Thanks to companies like Mustang Dynamometer, highly accurate chassis dynos are now able to simulate real-world driving conditions in a safe and controlled environment, making precise tuning of today’s highly advanced engine management systems a widely available and surprisingly affordable reality.
To better understand how exactly a chassis dyno works and is able to simulate the conditions and loads your car sees on the street or at the track, I connected with Jeffrey Wheeler and Steve Engelman at Mustang Dyne for an inside look at the technology they build into their industry-leading roller dynos.
But before getting down to the inner workings of a Mustang dyno, it’s important to understand that a roller-based chassis dynamometer reports the power, force and speed experienced by the dynamometer’s roll shaft(s) as they’re spun by the test vehicle’s drive wheels. As Steve from MD explains, “A power figure obtained for an engine using a test stand [engine] dynamometer will inevitably be higher than the power figure obtained using a chassis dynamometer, for (among others) the following reasons: on a test stand, there are no torque-converter/clutch, transmission, driveshaft, differential or axle bearing losses; no losses between the tires of the vehicle and the rolls of the dynamometer; some or all of the engine accessories may be disconnected; the engine intake air, water and oil supplies may be externally controlled; and the exhaust may be different than the exhaust system used on the vehicle.”

At the heart of every Mustang dyno is an air-cooled, eddy-current power absorption unit that’s designed to provide load in a very quick and responsive way. As marketing director Steve Engelman put it, “A Mustang dyno’s vehicle simulation capabilities are made possible by using powerful eddy-current power absorbers and torque-sensing load cells that provide an ultra-fast, closed-loop signal to the dyne controller [computer]. Eddy-current dynamometers use an electromagnetic brake to apply variable loading to the test vehicle [via the roller shafts]. An eddy-current power absorber (PAU) is a frictionless, air-cooled device controlled entirely by electric current. A torque arm extending perpendicular to the PAU and attached to a load cell provides for precise real-time torque data feedback to the dyne controller. Eddy-current PAUs provide the extremely fast response times required for precise vehicle simulations.”
Although the eddy-current PAU is the key piece of hardware around which Mustang builds its chassis dynos, as Steve alluded to above, their highly sophisticated closed-loop controllers are also a key ingredient to simulating real-world driving conditions. In fact, Mustang’s PowerDyne software comes complete with every type of test you could ever need for tuning or for developing power-adding modifications, from constant force, constant speed and constant horsepower tests to standing-start acceleration, idle/2500-rpm mode, and even emissions test simulations. Add to that the all-important ability to do to loaded steady-state testing and tuning in real-time at specific rpm, and you’ve got a dyno capable of doing everything except changing gears for you and tuning the ECU.
Another key piece of technology Mustang uses to differentiate its dynos from the competition is its Virtual Inertia controller. “Virtual Inertia is a patented method of simulating driving conditions on a chassis dynamometer,” Steve says. “This technology makes true road testing and accurate elapsed time simulations possible without leaving the safe confines of the dyno cell. This technology takes into account the test vehicle’s weight and its horsepower at 50-mph drag coefficient figure to dynamically adjust the loading to reproduce the forces the vehicle would experience on the road or track. The “hp at 50 figure” is an EPA figure that represents the horsepower required to maintain a constant speed of 50 mph on a flat and windless road surface. This number varies according to aerodynamic characteristics of different vehicles and represents the effect that wind has on a vehicle at increasing speed; higher speed equals higher wind drag, and thus, a need to increase load to accurately reproduce road or track conditions.”
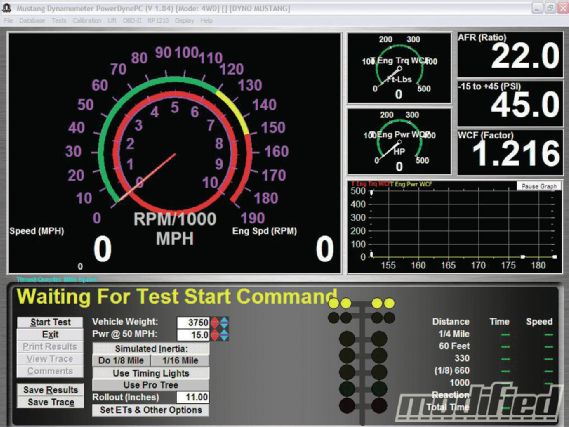
One of the cooler features Virtual Inertia makes possible is the ability to reproduce a quarter-mile run to within 0.01 seconds from actual time slips you’d see at the track, something Mustang has proven time and time again when working with pro drag teams that have gotten their cars dialed in to the tenth or even one-hundredth of a second. As Jeff from Mustang Dyne told us, “The Nickerson Performance alcohol Beretta runs 8.20s all day long at the strip, and using our quarter-mile simulation on a Mustang Dynamometer MD-1100, ran a 8.22 while doing the exact same transbrake launch at 6300 rpm they use to launch the car at the dragstrip.” For video evidence of this beast in action on the dyno, search YouTube for “Transbrake launch on a Mustang Dyno MD-1100.”
One of the more interesting engineering challenges faced by Mustang has been the development of its AWD chassis dynos. “The key to designing an AWD dynamometer properly is to understand the methodology currently being used by manufacturers in the field of AWD drivetrain technology,” Steve says. “A dynamometer that can accommodate various types of AWD vehicle transmissions and wheelbases without excessive complication and, more importantly, without risking damage to a client’s AWD system is paramount. Full-time AWD vehicles are designed to provide maximum performance regardless of road conditions. In cases where traction is less than ideal, a vehicle may be designed to guard stability and traction at the expense of power. This means reducing torque to a spinning wheel or retarding of timing. In order to properly test an AWD vehicle for peak performance, an AWD chassis dynamometer must therefore be able to simulate ideal road-load conditions to the vehicle.”
To achieve this, Mustang’s AWD dynamometers incorporate a mechanically linked internal drive system that synchronizes the front and back rollers to simulate a flat, dry road condition. Synchronization, or linkage, ensures that the front and rear rollers are always spinning at precisely the same road speed. This process eliminates the possibility of activating a vehicle’s traction control system and also ensures that a vehicle’s torque management system is operating under the assumption that the vehicle isn’t skidding, turning or slipping. Mustang has a number of different mechanical linkage designs that are all field-proven to synchronize front and rear roller speeds; its fixed-wheelbase designs incorporate multiple rollers and extreme-duty belts, while its moveable-wheelbase design incorporates OEM-grade gear and driveline based transmissions to synch the rollers perfectly.
Mustang Dynamometer has unquestionably raised the bar when it comes to providing the marketplace with chassis dynos able to accurately simulate real-world driving conditions. Mustang has also gone the extra mile for its customers by partnering with The Tuning School so that its customers get the most of out their Mustang dyno. As Steve explains, “We saw a real need to bridge an information gap for our customers that either already owned a dyno or were considering the purchase of a dyno. We’ve found that by exposing new dyno owners to these classes, they benefit in two ways. First, by seeing how the loading features of the dyno are used to tune a vehicle under part and wide-open throttle conditions they immediately learn a tremendous amount about the capabilities of their new dyno and learn how to use some of the more advanced features and tricks of the trade. Second, they learn how to use a program like HP Tuners to open up even more potential revenue sources for their business.”
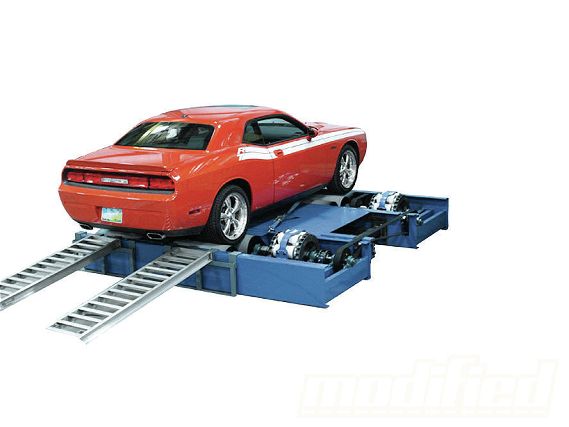
For most of us, the idea of owning a chassis dyno is both impractical and unnecessary, but it’s still very useful to understand how chassis dynos differ, especially when it comes time to choosing the dyno shop you want to have your car tuned at. If all you care about is tuning during wide-open throttle runs up to the redline, then a shop with a basic inertia-style roller dyno will suffice, but if you want to be able to tune your ECU across a full range of engine speeds and throttle positions for maximum driveability, there simply is no substitute for a dyno capable of reproducing the load your car experiences out on the road or at the racetrack.
Send your feedback to [email protected]
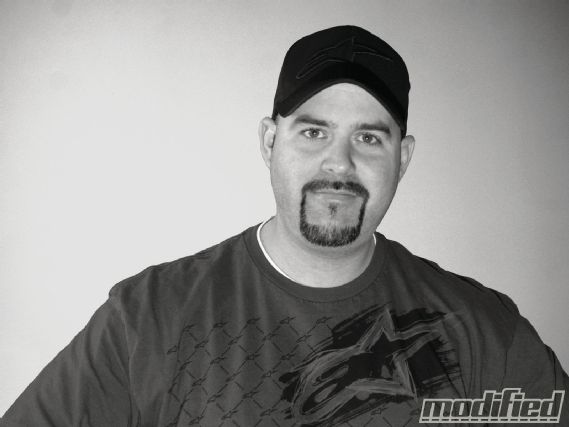