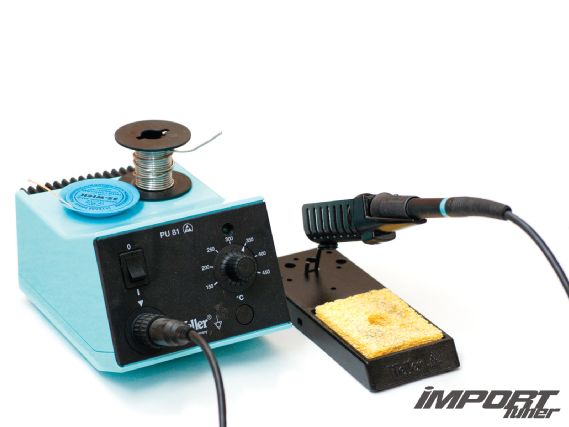
The most fundamental skill needed to assemble any electronic project is that of soldering. Basic soldering is a skill that's easy to learn and not too hard to master but misconceptions on the proper procedures also includes many individuals having no clue on where to start. Soldering is accomplished by quickly heating a metal or metallic alloy to join metallic surfaces together. A good soldering job can be rewarding while a poor job can lead to electrical failures and frustration. These steps will help improve soldering skills along with teaching you the basics and importance on how to perfect your soldering skills. Doing the job right the first time eliminates the need for costly rework.
1. Always use a quality soldering iron. We recommend an iron with a ceramic element core. Keep in mind that total power or wattage of the iron is less important than its thermal recovery ability. Thermal recovery is the ability of the iron to "recover" to proper temperatures immediately after soldering. Ceramic elements have been known to be better at maintaining proper temps. Although they are designed using lower wattage, they tend to heat much faster. A "cheap" soldering iron is usually constructed with a wire coil element. Wire coil units typically lose heat when used and are slow to recover from the initial temperature drop delaying usage. We recommend also refraining from using butane torch/battery-type soldering irons unless portability is crucial.
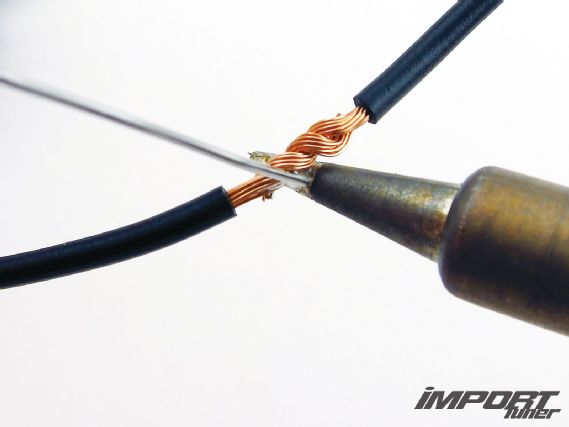
2. Proper solder tip sizes and shapes are very important in getting a good solder connection. When soldering wires, we prefer using the flat tipped ones (sometimes called "spade tips"). Avoid the rounded conical tips, which are primarily used to repair or solder very small IC chips on PC boards.
When working with wires, you want a tip that is about as wide as the wire you will be working on. A little bigger or smaller is fine, but too small and you will have trouble heating up the wire quickly or at all.
3. Always use quality type/brand solder. For electronics, solder is traditionally comprised of a mixture of tin and lead. Although 60/40-tin/lead solder is most commonly found on the market, we prefer 63/37 eutectic solder, which solidifies almost instantly. A 60/40 solder typically cools inconsistently as areas remain soft or semisolid once applied until fully cooled.
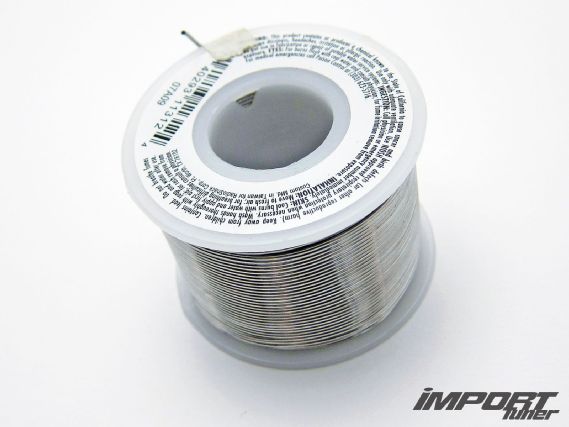
4. Pre-tinning the wires or components (coat with a thin layer of solder) or fills the wires or connector contacts with solder so you can easily melt them together. It also prevents the need to hold heat to components for too long. Pre-tinning is accomplished by applying a thin layer of solder to the individual parts before fusing the wires together. When tinning wire, you want to make sure the solder flows all the way to the center, from the end of the wire to the edge of the insulation where you stripped it back.
5. Use the right amount of solder; do not glob it on. More doesn't necessarily mean better. On the flip side, not using enough solder is just as bad, which can make the connection physically weak. A good solder joint will be smooth and shiny. If the joint is dull and crinkly, the wire probably moved during soldering and might require a do-over.

6. Keep your iron tip clean by wiping it off regularly with a damp sponge or rag both before and after making connections. A dirty tip can prevent your solder from making proper contact with the parts and can slow down heat transfer to components.
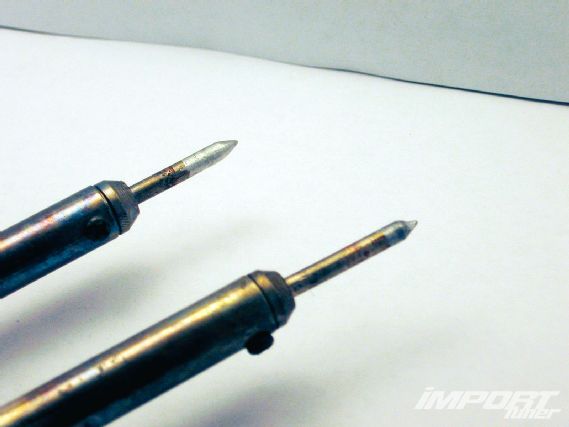
7. In between making connections and immediately after turning off the soldering iron, coat the tip with solder to protect it. Coating prevents the tip's protective metal coating from oxidizing and cracking or wearing away. If you see the coating of solder on the tip discoloring and turning dull gray, add more solder to re-tin the tip, or turn off the soldering iron if you will not be using it very soon (a discolored tip with a rainbow color pattern means the tip is too hot).
8. Clean up the solder with isopropyl alcohol or denatured alcohol to remove used flux when done soldering. Alcohol evaporates and dries quickly, does not leave impurities behind, will not corrode metal, and will not hurt electronics; whereas water can take days to dry and can corrode parts or leave impurities behind.
9. Lastly, use heat-shrink tubing to complete the soldering process to protect the wires.
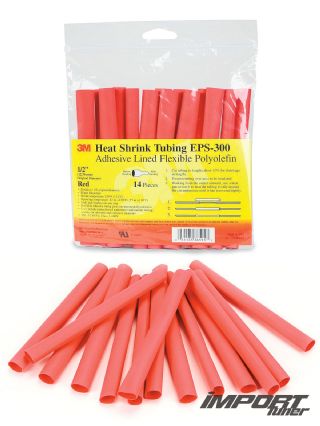