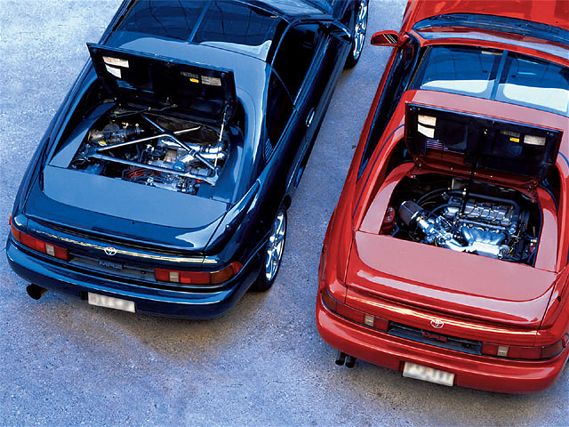
In Project MR6, we swapped a 1994 3.0-liter Toyota Camry 1MZ V6 into a 1991 mid-engine MR2 turbo. In various Toyota and Lexus platforms, this motor is good for 185-225 hp. With the new engine in place, we tuned and tested the vehicle with various power boosters, including: 1) a TRD supercharger system, 2) a custom Majestic-based turbo system, 3) both power adders compounded at once 4) naturally aspirated, with neither power booster installed.
We compared and contrasted the 2.0-liter MR2 turbo four-banger vs. a stock 3.0-liter 1MZ V6, the Majestic turbo vs. the TRD/Eaton positive-displacement blower, and the effect of both at once. We achieved our goal of 600 rwhp in Part 6.
In Part 7 we recap the project, test the engine compounded at high boost, bump the power to a new peak in the most optimal configurations, fill in a few holes in our knowledge of power levels at medium boost, dyno test the Random cat at high and medium boost, take stock of what we learned, and finally, complete a project that began nearly three years ago and first appeared a year and a half ago in Turbo.
For Part 7 dyno testing, we made a 400-mile round-trip from Austin to Dallas in record-setting 101-degree high-humidity Texas weather with the A/C working its heart out the whole way. Then we ripped off some high-boost turbo-only and compound turbo-supercharged dyno runs-which seemed to demonstrate fairly conclusively that this is a street car, not a dyno queen.
This car is something of a transformer robot: The modified TRD blower kit can be removed or replaced in less than an hour. The twin-entry turbocharger uninstalls in about 90 minutes with a "turbo-replacement pipe" plumbing from the twin-entry flange into the 3-inch exhaust turbine-out downpipe and muffler-and the car is a torquey, fun ride naturally aspirated. A Random Technology catalytic converter becomes an optional part of the exhaust upstream of the Borla muffler, installing or uninstalling in less than five minutes.
The Final Frontier-High-Boost Compound Turbo-SuperchargingFor the final test configuration, we started by backing away from the copper head gaskets. With good combustion chambers, great intercooling, an efficient turbo and race gasoline, we didn't encounter gasket-killing knock problems, but we were suffering from tenacious coolant leakages past the custom copper gaskets.
After Kotzur Racing verified the block deck and head surfaces were dead flat, we returned to stock gaskets, and removed the now useless inner wire O-rings. The outer O-rings fell at or just within the edge of the stock gasket's metal fire rings, which would increase clamping force and help prevent the head gasket's metal fire rings from being forced outward under extreme combustion pressures.
While the engine was apart, we replaced the main and rod bearings, repolished the crank, and disassembled and serviced the oil pump. Clutchmasters changed the multi-disc clutch facing to a new, experimental super-duty material that should improve torque-holding capability and make for excellent streetability.
Then we installed additional sensors. Fortunately, beside the standard engine temp and air temp inputs, the Motec M48 ECU is equipped with an auxiliary temp input, which thus far, we hadn't been using. We drilled and tapped the blower plenum downstream of the rotor assembly. Then we did the same for the air cooler inlet tank for the GM Delco 3500 Ohm air temp sensor.
Combined with the air temp sensor located just upstream of the throttle body, we could track air heating from the Eaton M62 during a dyno pull, and could, alternately, datalog turbo compressor discharge temperature upstream of the air cooler unit for post-dyno analysis of intercooler efficiency.
We measured exhaust backpressure during turbo boost and, alternately, intake pressure upstream of the throttle body on either end of the air cooler when the supercharger was installed so we could separate boost produced by the supercharger from boost produced by the turbo.
Up to this point, we had dedicated the Aux Volt Motec input to a 1-Bar MAP sensor providing barometric pressure compensation. We could free up the aux volt port to measure backpressure or compressor-discharge pressure by reconfiguring the load calc scheme to provide barometric pressure compensation using a manually entered parameter. By swapping out the 1-bar GM MAP sensor and installing a Delco 3-bar or Data Instruments 100-psi pressure sensor, we could datalog exhaust or compressor-discharge pressure to approximately 33 or 75 psi.
New Dyno Results
Dyno Run #1
We performed our dyno testing at Alamo Autosports with Brice Yingling and Bob Norwood, and started with a nice, low-boost pass. We unscrewed the wastegate adjustment bolt almost completely. The boost table was set to bring in a full 170 kPa (10 psi) of boost at 3500 rpm on 93-octane.
We connected the water cooler to a tap water source, with a total-loss drain-back into the sewer, the blower-discharge sensor to the aux temp port on the Motec, and a pressure gauge to the front bank exhaust pipe.
In the "soft" dyno run, boost increased to 175 kPa at 3500 rpm and fibrillated between 185 and 200 kPa at more than 6000 rpm. No one watched the new backpressure gauge on this run. Torque was fairly flat, from 3750 rpm at roughly 365 lb-ft, before falling off gradually above 5600 rpm. Peak power of 394 hp occurred at 5900 rpm. The auxiliary temperature in the blower discharge climbed from 108-degrees Fahrenheit to 124-degrees Fahrenheit. The intake air (air-cooler discharge) temperature stayed at 82.4-degrees Fahrenheit.
Dyno Run #2
The next run was a "hard" dyno run, with power up by 20 hp and torque up approximately 15 lb-ft over the same range. We were again on 93-octane pump gas.
At this point, the torque leveled off at 4100 rpm and stayed fairly flat to 5600 rpm. Boost (MAP) climbed to 212 kPa at 4100 and fibrillated to 207 kPa at 6700 rpm. Peak power of 415 hp occurred at 6200 rpm, with peak torque measuring at 390.3 lb-ft at 4300 rpm.
This time, we watched as the turbine-inlet exhaust backpressure, which was insignificant in the early run, climbed to 15-20 psi at peak power. It was difficult to tell exactly because exhaust pulsations made the needle flutter.
The blower temperature sensor seemed to have heat-soaked to 118 degrees at the beginning of the dyno run. The blower air temperature climbed steadily to 126 degrees by 5750 rpm, then increased to 140 degrees at 7000 rpm.
Dyno Run #3
With the MR6's fuel tank nearly empty, we added five gallons of 118-octane race gasoline.
Previously, we discovered that with the wastegate adjusted to the minimal 6-psi setting, exhaust backpressure pushing against the wastegate poppet valve prevented the turbocharger from making more than 22-24 psi boost because the wastegate was opening prematurely. The obvious answer was to clamp down on the wastegate adjustment bolt to preload the wastegate actuator spring a little harder. However, we were about to discover that this solution produced blowback in a new problem.
We screwed in the wastegate adjustment bolt almost completely, which would normally increase nominal boost from 6 psi to, say, 9 psi. The Normal (side) and Deltagate (top) wastegate actuator reference hoses were routed to the turbo compressor discharge located below the air-cooler unit and above the throttlebody. Because the reference source was the compressor discharge rather than the intake runners, we expected the minimum boost possible would be 6-9 psi plus about 3-5 psi of output from the blower, for a total minimum boost in the 9-14 psi range.
Bob hammered the throttle and ripped off a new dyno run. The boost controller and turbo combined to reach a MAP of 230 kPa at 4150 rpm, whereupon MAP "fibrillated" fairly flatly to 5450 rpm. At this point, the boost controller duty cycle climbed steadily to 100 percent in an effort to limit boost, while MAP subsequently climbed from 235 kPa at 5750 rpm to 292.9 kPa at 6500 rpm.
In retrospect, clamping down on the adjustment bolt was clearly limiting the opening travel of the wastegate poppet valve; when the exhaust volume became too high for the restricted poppet valve to bypass, boost crept to 28 psi.
The Catch-22: With too little wastegate adjustment pressure, we can't make boost above 24 psi due to backpressure forcing open the wastegate. With too much adjustment pressure, we can't stop overboost due to severe limitations on the wastegate opening travel. The answer is a stronger wastegate spring.
During the dyno pull, backpressure climbed to as high as 35 psi, as measured on a pressure gauge tapped into the front bank exhaust. Torque was virtually flat at a little more than 400 lb-ft from 4000 to 6100 rpm. Power peaked at 471.6 rwhp at 6500 rpm.
The auxiliary temperature-apparently already heat-soaked prior to the run-climbed from 52.1 to 58.5. Air temperatures exiting the intercooler remained in the 28-30-degrees C range throughout the run, even though we'd forgotten to turn on the tap water to cool the air cooler.
We adjusted the wastegate spring out a bit and mashed the pedal. The turbo compressor had exploded. What was left when the compressor failed at 28 psi boost was the compressor hub, broken off where the shaft emerged through the compressor back-plate, totally stripped of compressor blades, and a bunch of blade shrapnel in the bottom air cooler tank.
Fortunately, the intercooler trapped the metal and kept it from entering the engine. The compressor backplate was hugely distorted and bulging outward toward the center section of the turbo. The turbine side appeared undamaged, and the turbine wheel spun freely as always on the hot side shaft.
Regrouping
OK, time to regroup. We put the turbocharger on a bus for Majestic Turbo in Waco, Texas. We installed the turbo-eliminator pipe that enables the MR6 to run without the turbo installed. Then we drove to Austin, where we pulled the wastegate off the car and installed a secondary inner spring to raise the opening pressure of the wastegate from 6 psi to about 18 psi.
In the meantime, confronted with a scored-up compressor housing, Majestic decided to enlarge it for a T-70 compressor wheel.
Back on the Alamo dyno, the plan was to optimize power in turbo-only mode, and then throw the blower on to see what that did to low-end power. During dreadful early-summer Texas weather (more than 100 degrees with extremely high humidity), the MR6 performed a series of dyno runs to about 450 whp. Datalogs revealed significant compressor surging, with manifold pressure jumping between 18 and 28 psi, and in one case momentarily crashing to atmospheric pressure before immediately building again into the 2-3-bar range.
All centrifugal compressors run the risk of surging if the compressor is loafing at relatively low air volume and high pressure ratio. Unlike a positive-displacement supercharger like the Eaton (in which the design makes it physically impossible for air to move backwards through the blower), turbos make boost by accelerating the air to extremely high speeds with a set of fan blades turning at 100,000 rpm or more.
If a large compressor is turning too slowly but making too much boost, air can suddenly change direction and explode backwards through the compressor. That momentarily releases the head of pressure produced in the compressor discharge, sounding like a series of minor explosions and air disruptions.
Anything, like an overly restrictive air cleaner/intake tube, that decreases air pressure at the compressor inlet can intensify any tendency to surge. We realized the 6x5-inch conical K&N air cleaner we'd jammed into the MR2's driver's side engine air intake was more appropriate for a 225-hp naturally aspirated engine than a 600-hp compound monster.
Final Dyno Testing
On the Alamo Dynojet, with five gallons of 118 octane in the tank, we installed a Majestic T-61 turbocharger. Since the T-70 suffered surge problems and was operating within 5 percent of the surge line at high boost in the 5000- to 6000-rpm range, we needed a smaller turbo. The candidates were the T-66 and T-61. Limited to a threshold of 65-percent thermal efficiency, the T-61 was good for 640 flywheel hp and the T-66 for 680 hp. Limited to 60-percent efficiency, the T-61 could manage 670 hp, while the T-66 could do about 710 hp.
With the MR6's excellent air-to-water intercooler, on the day we could return compressed-air temperatures to that of the tap water we were using for cooling, we decided to go with the T-61, which would provide excellent response and fast spooling.
We hooked onto the dyno again with the turbo-only application. In one and a half days, we ran 46 dyno runs, with Alamo owner and chief tuner, Brice Yingling, at the laptop searching for the optimal fuel and timing. With an additional spring in the Majestic wastegate, the first run (no electronic wastegate controls) made 325 whp at 9 psi boost, which is an estimated 375 to 410 flywheel hp.
We methodically worked our way to 22 psi of boost, working with the dyno, the dyno's wideband air/fuel logging, and the Motec M48's internal logging capability, and making changes to fuel, timing, boost and other factors.
At 22 psi, we still didn't have enough wastegate spring to keep the gate closed against exhaust pressure as boost increased further, and we were forced to again begin adjusting the wastegate spring compressor bolt to clamp harder on the spring (simultaneously limiting wastegate travel). With Brice's tuning, the 1MZ managed 455 whp at 22 psi, an estimated 525 to 575 flywheel hp.
Pushing on further, the trick was to dive under the car on the dyno, adding additional turns to the wastegate adjustment bolt, and then make a run with fingers crossed, ready to jump off the throttle on the next dyno run if boost ran away.
Boost never ran away. As we pushed to 28 psi boost, the turbo was out of juice, and we stalled at just below 500 whp. So we disconnected the air-cleaner/air-intake system entirely from the turbo, directing a fan to blow cool air toward the compressor inlet blades under the car. After a few more tuning runs, we clamped on the wastegate bolt, mashed the gas and recorded the results.
The car made a mighty groan as rpm pushed through 3000, and then the engine suddenly went nuclear and torque increased 300 lb-ft in the next 2000 rpm. When the run was over, we looked on the Dynojet computer monitor, and the mighty turbo 1MZ had managed 537 whp at 5400 rpm on 28.5 psi of boost.
We bolted on the TRD blower kit with the wastegate still clamped shut. This time the engine was much stronger, ahead by 20 to 40 whp most of the way up the speed range, until compound power stabbed steeply through 500 whp just above 4500, and Brice aborted by 5000.
Backing out on the wastegate bolt, we did several more runs, managing 524 hp across a broad range, from 5500 to nearly 7000 rpm-and doing it on 23 psi of boost.
Then we substituted the Random Tech cat and Borla muffler. On the dyno, the power was down from 525 to 478 whp. That was 47 hp, or less than 10 percent, with most of the loss due to the cat. Five or 10 percent wasn't bad, leaving the car still capable of 550 to 600 flywheel hp at 23 to 26 psi of boost.
Conclusions and Additions
1)The cat/muffler begins to make a difference at 4500-plus rpm, and from 5000 to 6000, makes a maximum of 10-percent difference in power. The cat and muffler robbed 46 hp in the peak power range around 6000 rpm compounded, and 39 hp in the turbo-only configuration at the peak power range around 5500.
2) At 4800 rpm and 19.7 psi of boost, exhaust backpressure into the turbine exceeds 26.46, on the way up to 35-psi peak exhaust backpressure. We couldn't measure much more pressure with the MAP sensor since it went out of range. Exhaust pressure exceeds MAP under all circumstances.
3) Naturally aspirated, the Toyota 1MZ is losing torque after 4500, and the redline is 6250. This motor desperately needs more cam for huge power.
4) The supercharger was critically important in making power in the 5800 to 6500 range on the 1MZ. Viewed as a black box, the combination of the blower and engine has greatly improved volumetric efficiency in the high end. The blower acts like a big cam for the top end.
5) The supercharger is always adding boost. It isn't true the Eaton blower isn't working once the turbo is really cooking. Whereas the supercharger never made more than 5 psi by itself, the blower component of boost is as high as 9 psi in the compound configuration. We don't know why.
6) The Majestic T-61 turbo proved itself able to make 537 rwhp, which is between 620 and 675 flywheel hp. This is exactly the predicted range of the turbo as revealed in the T-61 compressor map, which provides enough air for 640 flywheel hp at 65-percent thermal efficiency, 670 hp at 60-percent efficiency.
Even with the wastegate clamped shut, we couldn't get the turbo to make more than 29.5 psi of boost, and to do that, we had to remove the turbo intake plumbing, which then made another 40 wheel hp. The average boost from 5000 to 6500 improved from 24.7 to 27.5 psi. If you're running your turbo to the ragged edge, you need a great free-flowing intake.
7) We added a second 3-bar MAP sensor that could be used to track exhaust backpressure more effectively, turbo compressor discharge pressure upstream of the intercooler, plumbing and throttle body.
8) We still didn't have enough wastegate spring to keep the wastegate from being blown open by exhaust pressure at high-power settings. The addition of a second spring inside the Majestic wastegate increased nominal boost from 6 to 9 psi. Beyond that, all additional boost was provided by the Motec-controlled pulsewidth-modulated electronic controller feeding a percentage of boost to the Deltagate side of the wastegate actuator, helping hold the wastegate actuator closed to higher pressures.
We used the higher pressure compressor discharge as a vacuum/boost source for the boost controller, but this was never more than 3-4 psi above manifold pressure, so that was the maximum pressure that could be used in our configuration to keep the wastegate closed against exhaust pressure.
We considered disconnecting the manifold pressure reference to the normal (non-Deltagate) wastegate port, and thus greatly multiplying the effect of boost pressure to keep the wastegate closed at high exhaust pressures. However, we were running very near the top of the MAP sensor, and seemed near to falling off the edge of the world in several ways at such high boost. We couldn't make more than about 22 psi of boost just using the boost controller.
9) We saw high injector duty cycles near 600 flywheel hp in initial rich configurations. However, after tuning, and at peak torque and peak power under all circumstances, we had injector duty cycle left once we began to lean out higher power levels and add timing as the power rolled over. The only place duty got tight was in the high-power turbo dyno run 036 near redline, above 6750 rpm, above peak power and torque, when we began to run out of time for injection, and hit 100 percent duty cycle. The most duty required in the compound configuration was 88-percent required above 6500, again, as time got short.
10) Turbocharging the supercharged engine was like turbocharging a bigger engine with better top-end VE.