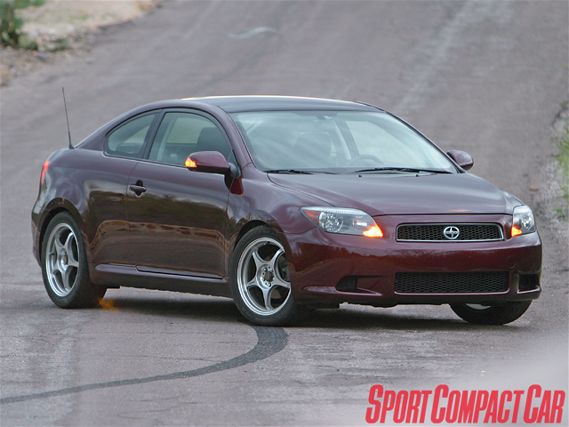
We have a love/hate relationship with our Project tC. We all seem to love hating it. From the beginning, I've cursed the tC for its lack of an LSD, excessive torque, sluggish throttle response and susceptibility to heat soak. The sentiment lasted until I took it to a NASA Southern California Chapter track event. Although these drawbacks became ever more glaring with every 30-minute session of track-beating, Project tC's brilliance in coping with the abuse made all its flaws seem relatively minor.
I spent three laps at Buttonwillow Raceway chasing down and catching some showboating yahoo in a Boxster. After an Evo MR, the plain-Jane Boxster was the fastest in our run group and I had finally worked through the traffic to get on its bumper. It was dead even on the straights, but the Boxster would pull away through every high-speed sweeper on account of its better balance.
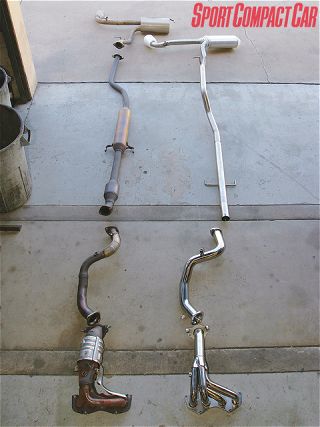
Project tC, in contrast, had the upper hand in mid- and low-speed corners with its superior braking and instant torque, despite always spinning the inside wheel. The chase was on as we played cat-and-mouse, corner after corner. Every bend's exit where our tC had the upper hand to pass led frustratingly into a no passing zone. For three more laps this continued until I finally got the point-by and started to pull some distance from him. That's when I decided Project tC was near completion.
Although my victory over some Kraut rocket is fresh in my mind, I'm back to hating it while driving on the streets. The rear suspension bottoms out all the time, the supercharger heat-soaks and the notchy shifter and throttle make smooth driving impossible. Only its track manners have validated our work so far. So let's focus on that instead.
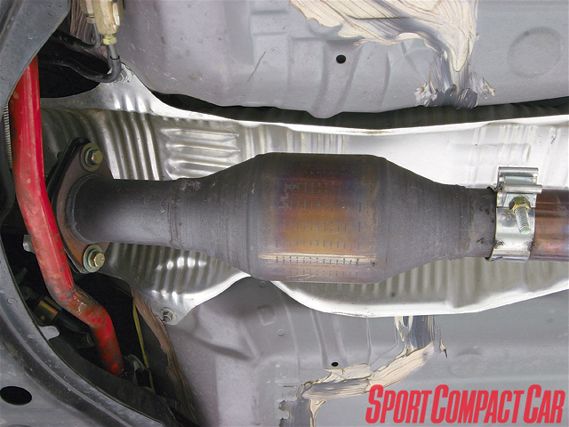
More boost
When you look at the compressor map of the Vortech V5 F-trim supercharger TRD used, it's clear that, at 7psi, the blower isn't in the optimum efficiency range. We don't blame TRD's engineers for choosing this figure since they have to make the kit smog-legal and reliable enough to warranty, but we had a hunch that, with more boost (a higher pressure ratio), the supercharger would operate with more efficiency, especially in the mid-rpm range we use most.
To test this out, we increased the boost with Zero Point Industries' (ZPI) billet aluminum 9psi pulley, which bolts on in a matter of minutes. The smaller-diameter drive pulley spins the supercharger compressor wheel faster per engine rpm, which essentially provides slightly more boost at any engine speed. The tC's hydraulic tensioner makes changing to a shorter belt unnecessary. With just a new pulley, our tC now makes 219 wheel-hp and 189 lb-ft of torque. That's a gain of 17 horsepower.
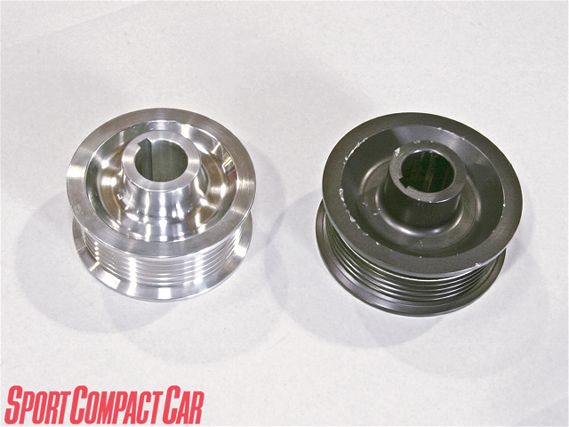
To verify this, we plotted the operating line of the two pulleys on the compressor map. Supercharger efficiency is defined by the ratio of input temperature to output temperature. So let's say, for example, the air entering the supercharger is 90 degrees F and after it's compressed (where some energy is stored as heat) it comes out at 100 degrees F. Divide the temperature in by temperature out and you get 0.9, or 90 per cent efficiency. Unfortunately, even the best centrifugal superchargers can only reach 80 per cent. Refer to the compressor map for the V5-F supercharger and you'll see that it peaks at 76 per cent. That's basically where we want to be.
Compressor maps are basically graphs that show how efficiently the compressor is operating for a given airflow and boost (calculated as pressure ratio). The horizontal axis is the airflow in terms of mass flow rate, like pounds per minute (lb/min), or a volumetric flow rate such as cubic feet per minute (CFM).
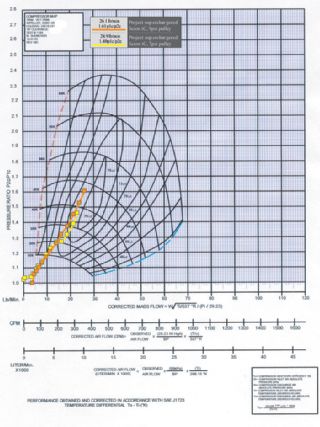
On the vertical axis is the pressure ratio, which is a ratio of the absolute intake pressure (roughly 14.7psi for ambient) divided by the compressed absolute pressure. Manufacturers draw little ovals, called efficiency islands, to show how efficiently the compressor would operate at a given flow rate and pressure ratio.
Most designers size a turbo or supercharger by looking at its peak operating point, i.e. the maximum flow and peak boost, to see if the compressor is operating efficiently. The difficulty with mapping a crank-driven centrifugal compressor (supercharger) is that it builds boost exponentially as the revs climb. Unlike a turbo, which spools up, boosts to a regulated pressure and holds it, a centrifugal blower will keep increasing boost to the redline. And not in a linear fashion, either.
To see how our compressor is doing throughout the rev range under real-world conditions, we have to measure three variables: boost pressure, airflow, and rpm. With newer cars, this turns out to be easy, since the ECU reads all these values and spits them out through the OBDII port. In theory, you can plug in a scan tool and read the values as you make a pull on the street or on the dyno. Theory never works out quite right, though. Government mandates only stipulate that the OBDII port communicate at a woefully slow rate, since it's primarily used for diagnostic purposes. It will refresh maybe once per second, which isn't very useful as Project tC will make a third-gear pull to the redline in about eight seconds. So we resorted to measuring boost with our own data logger and a MAP sensor connected to the fuel pressure regulator vacuum line, since it's really the only accessible vacuum source available. Airflow is a little harder. You can't just splice in and data-log the voltage coming off the MAF meter, because there's no way to accurately convert voltage to airflow. We begged the very helpful engineers at TRD to lend us their proprietary factory-issue scan tool that not only allows us to read the ECU, but also logs and exports the data for us to chart.
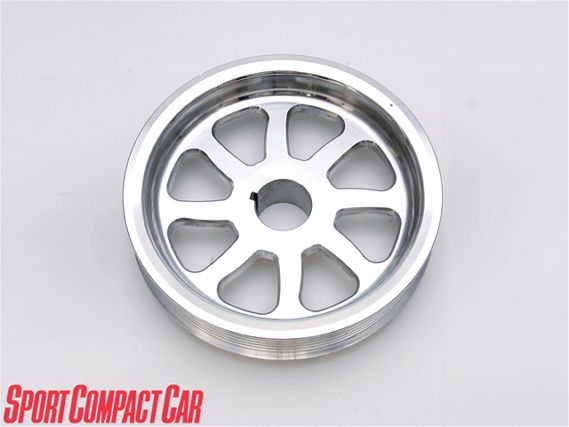
We plotted the operating points for every one-second increment for both pulleys, in addition to data-logging the ignition timing. Although the car made more power on the dyno with higher boost if the ECU pulled out more ignition timing (on account of knock activity), the gain in power would not be worthwhile as it only gets worse as the supercharger heats up. Looking at the two operating lines on the compressor map, you can see that although we're still in the same efficiency island, the pressure ratio is much higher, and we are slightly closer to the surge line (the dotted red line on the left.) In theory, if we could generate more flow, we would be able to move into the 76 per cent efficiency island. With the same intake air and coolant temperatures, the nine-pound pulley only pushed the ignition timing half a degree more, to 13 degrees BTDC, compared to the stock TRD seven-pound pulley. We didn't see any detectable knock activity with the Toyota scan tool, either.
More pulleys
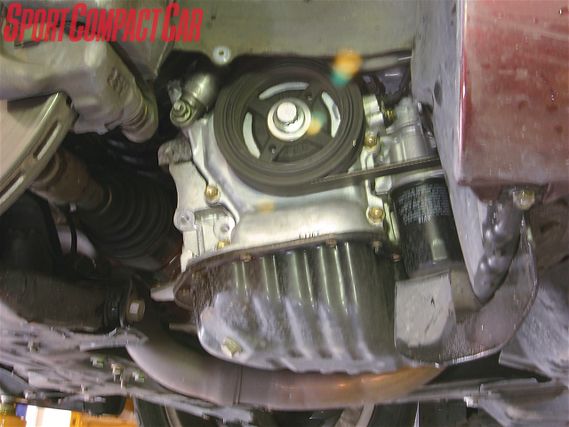
Older Scion tCs have a nasty, laggy throttle feel. The electronic throttle with Camry-like programming makes throttle response sluggish at best. Since few tuners bother retuning the ECU that controls the e-throttle map, the only option is to reduce the inertia of the driveline's rotating assembly. There are three ways to do this: get a lightened flywheel, knife-edge or lighten the crank, or fit a lighter crank pulley. Guess which one we chose? Since we opted not to tear the engine or transmission apart for a limited-slip diff, flywheel and clutch, that leaves changing the crank pulley. ZPI also makes a billet aluminum crank pulley, which hastens throttle response by reducing rotational inertia. The new aluminum unit weighs 0.8 pounds, compared to the stock steel pulley's 4.4 pounds, and gives just enough extra pep for decent throttle blips when shifting and balancing the car through a corner.
Lots of shiny piping
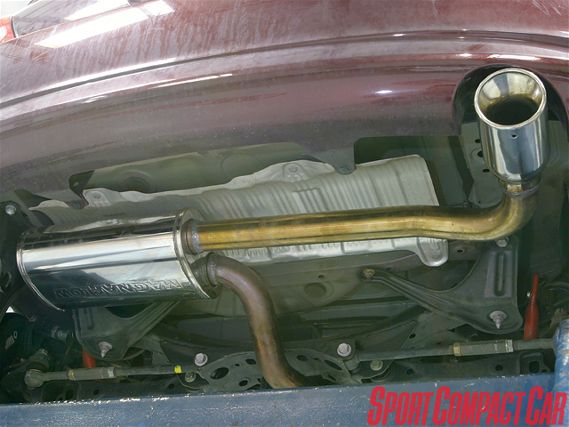
Even with supercharged cars, where air is pushed into the cylinder and all the pumping work comes from the crankshaft, an unrestrictive exhaust can give significant gains by reducing backpressure, which increases charge scavenging through the cylinder. Backpressure, the pressure of gases trying to pass through the exhaust, is an indicator of how much resistance exhaust gases have to push against as they exit the cylinder. With less resistance, the piston is able to push out the combusted gases faster which, for the brief moment when both intake and exhaust valves are open (at the end and beginning of the exhaust stroke and intake stroke), allows more fresh air to be sucked in. This is because when the hot high-pressure combusted exhaust gas leaves the cylinder, it causes a mild drop of pressure inside. This helps breathe more fresh air in before the intake valve closes for the next combustion cycle. The faster the exhaust blows out, the more the pressure drops. That's scavenging. This differs from turbochargers, which benefit more from an open exhaust - less back pressure means more exhaust energy to spin the turbine.
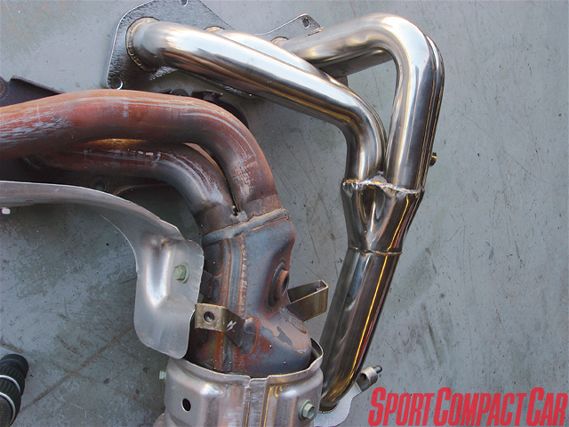
Although Project tC came with a stainless steel TRD cat-back exhaust, we decided to replace it with a Magnaflow unit, which eliminates the stock resonator. The new exhaust uses slip fittings and clamps to hold each connecting section together, so variations between vehicles won't cause fitting issues. The drawback is that, if not properly installed, the slip joints can rotate or lose their seal. Unfortunately, our exhaust has done that because the factory rubber exhaust hangers are rather loose and tired, causing the piping to occasionally rattle against the rear heat shield. So we removed the heat shield.
On the bright side, the Magnaflow exhaust replaces much of the factory B-pipe that other cat-back exhausts don't replace. Scion uses another catalyst underneath that's integrated into the factory B-pipe. We took a hacksaw and cut off the pipe three inches behind the cat, so it will slip into the new exhaust. The result is a tC with one catalyst, the one cops look for.
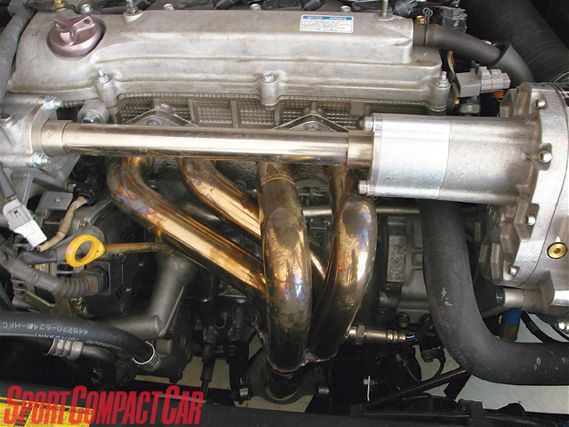
We also installed a Megan Racing 4-1 T-304 stainless-steel racing header and 2.5-inch S-pipe with the help of Mark at MD Automotive in Westminster, CA. Megan's header eliminates the close-coupled cat on the stock headers and uses a slightly more efficient collector to join the primaries. Although the welding isn't spectacular, the fit is great for both parts and the elimination of the first cat and reduction of backpressure meant we were able to pull another 11 wheel-hp.
That brings our total to 230 wheel-hp with quarter-mile times in the range of 14.8 seconds and trap speeds at 96mph, compared to our previous best run of 15.1 seconds at 93mph. Not bad for a budget econo-box.
Installation is straightforward, with the exception of removing the nut and stud nearest the passenger side, which holds the exhaust flange. Without removing the alternator (there isn't much tool clearance), we ended up just chiseling off the nut turn by turn. It's easier to remove the stud and replace it with a bolt when you get the header on.
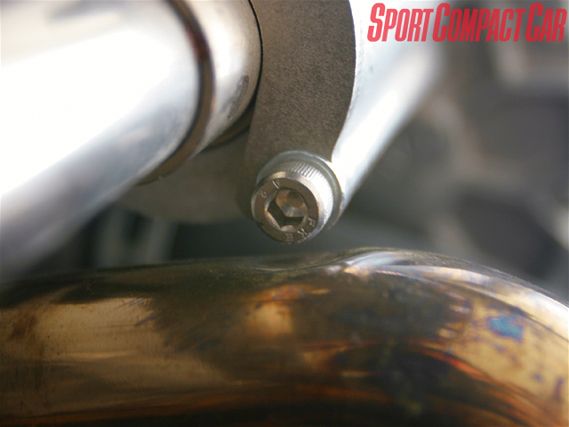
On the recommendation of Megan Racing, we also added an adaptor from Road Race Engineering to the rear oxygen sensor. This acts as a buffer between the sensor and the exhaust flow so the sensor doesn't detect the air/fuel fluctuations, which are much more severe now that the close-couple cat is removed. This little trick seems to work well since we haven't seen an 'engine check' light come on during all of our testing.
Up Next
As stated, Project tC is near completion. It doesn't make sense to spend much more money. We'll head out to the track and measure our Scion against a mildly-tuned Acura RSX Type-S. In the meantime, we're looking to find someone to tune it, insulate the tubular exhaust header, (which sits just beneath the supercharger) and make some mild suspension adjustments to further reduce understeer.