How do you improve on something that's good to begin with? The Evo is blessed with one of the best standard equipment brake systems found on any production car. In stock form the Evo has big Brembo four-piston front and two-piston rear brakes and big ventilated rotors on all four corners. With the normal brake modifications, such as high-temperature fluid, braided lines and upgraded brake pads, the stock brakes can handle just about any situation you would likely find on the street, including spirited driving in the twisties. With an aggressive high-temperature brake pad, the stock brakes can also handle abusive track duty, even with R-Compound tires. The stock brakes even look good. No wonder many Evo tuners overlook the brakes when building fast Evos.
Why in the world would we mess with our brakes then? Since our plans for Project Evo IX include some serious track use, we considered the idea of upgrading our brakes. With the stock Evo being relatively heavy at close to 3,200 pounds, the stock brake pads must be exchanged for some aggressive heat-resistant pads for track use with sticky R compound tires to avoid fade. The trouble with these kinds of brake pads is that they aren't streetable.
The aggressive friction material of racing brake pads has a high metallic content, including materials like powdered iron, bronze, and copper with friction modifiers like ceramic and carbon powders used to maintain a high coefficient of friction at the near metal melting temperatures that brakes sometimes see at the track. Naturally, this sort of brake pad is very abrasive.
So race pads don't instantly wear out the rotors, they depend on high temperatures so they can develop what is called a transfer film on the rotors. A transfer film is a thin layer of metallic oxides that bonds to the rotor. The transfer film is formed under the high temperatures and pressures of brakes being pushed to the limit. The aggressive pad material rubs on the transfer film instead of the bare iron of the rotor, and the film protects the metal from rapid wear. Think of the transfer film as a wear-resistant coating for the rotor that exists at high temperatures.
When used on the street, the temperatures don't get high enough for a transfer film to form and the abrasive pad material does a handy job of machining your nice rotors down to nothing in a shockingly short time. We've seen race pads completely ruin a set of rotors in 200 street-driven miles. We won't say who did this (ahem), let's just say we have up close and personal experience with this. Another minus is that race pads generally don't work well when cold, as in the type of cold that's seen in your first few stops in the morning or when driving on the highway for miles without touching your brakes. This might lead to dangerous situations when the brakes are cold. Finally, racing pads give off obnoxious, sticky, cleaner resistant and corrosive brake dust. This gummy black powder just loves to eat up polished alloys or burn through powdercoat if it isn't washed off frequently.
Driving to the track and switching the pads before starting out is not that big of a deal but the hassles of registration and mandatory drivers meetings make race mornings somewhat hectic without having to scramble to switch pads. After all most of us don't have a pit crew to help out on track days. What we wanted were some brakes that had enough capacity so that we could drive to and from the track and run on the same set of pads. To stop 3,200 pounds of Evo with streetable pads meant going big, real big.
Many companies make upgraded brake systems for Evos but we choose to stick with Brembo's GT kits to upgrade our front and rear brakes for several reasons. The first reason was engineering. Brembo is an OEM supplier and their brakes meet stringent OEM quality standards. Brembo is standard equipment for most of the exotic cars built on the road and most ultra high-performance road cars for that reason. Brembo is also one of the standards in braking performance in the motorsports world, from F1 to MotoGP. The second reason is that our car is being built to be a bit of a sleeper with all of the mods having a low visual profile from the outside. Although our brake system is eye catching, so is the stock Brembo system. The uninitiated can easily overlook our brakes.
When evaluating front brake kits we chose Brembo's top-of-the-line GT kit with a huge 355mm front rotor and huge six-piston monoblock front calipers. This is the biggest thing they could fit under our 18-inch Volk CE28N wheels. One of the best things a genuine Brembo kit has over many other performance brake kits is that the Brembo kit is engineered to maintain the correct hydraulic proportioning. Brembo matches the caliper piston diameters so that the correct hydraulic ratio of front-to-rear braking force in maintained in all of its kits. A side benefit of having proper piston matching is that the pedal stroke will stay correct as well. Many other kits simply use an off-the-shelf racing caliper, usually with more piston area than stock. This results in the brake system having too much brake bias and a mushy long brake pedal to boot. Poorly engineered kits often have significantly worse stopping distances than stock for this very reason. We once drove an Evo from an unnamed company in an Evo tuners shootout event and were dismayed to find that the fancy-looking huge brake system on the car was way worse than stock for this very reason.
Brembo calipers also feature differentially sized pistons. What this means is that the front, leading edge pistons are smaller in diameter than the trailing pistons. The reason this is done is to reduce taper wear of the brake pads. Brake pads, especially long pads like the ones found in our front calipers, tend to use and wear the leading edge of the brake pad more heavily than the trailing edge. The front leading edge of the pad bites harder and wedges itself to the rotor due to the tipping moment (or lever arm in non-engineer speak) between the wearing surface of the pad and its backing plate resting against the caliper piston. The rear area of the pad is somewhat unloaded due to this phenomenon and is also lubricated by the boundary gasses of the vaporizing pad material created by the leading surface of the pad. This results in the front surface of the pad wearing faster than the rear, or taper wear. With differential piston sizing, the hydraulic force is less in the front with its smaller pistons and greater in the rear of the pad with the larger pistons. This compensates for the uneven forces acting on the brake pads, which will now wear evenly across their face. In some cases the brakes will actually be capable of producing more braking force as well since the pad is being used more efficiently.
We chose the Brembo monoblock caliper because of its superior stiffness, which will yield a firmer brake pedal. A monoblock caliper is just what it sounds like, a caliper machined from a single solid aluminum casting. Although it is much more difficult and expensive to machine a caliper like this, the performance gains can be worth it for the serious enthusiast.
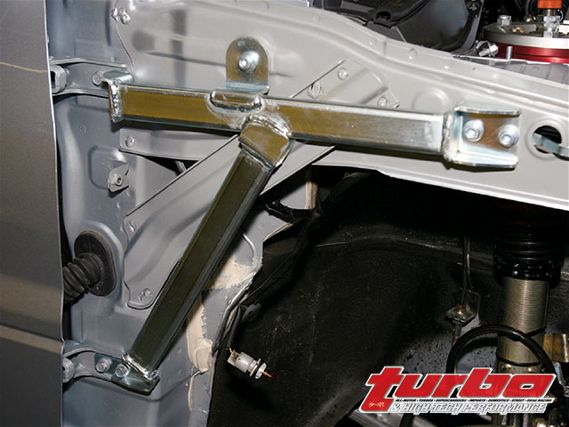
The front rotors are 355mm, or 14 inches, in diameter and made from Brembo's proprietary cast-iron alloy. This alloy has a consistent coefficient of friction over a wide temperature range and is dimensionally stable of a wide temperature range as well. Brembo offers the rotors drilled or slotted. We opted for slotted because of the heavy expected track use. The slots offer an escape path for the vaporized pad material that is created under extreme use. Under really hard braking conditions this boundary layer of ablated material can actually act like a lubricant and the pad can hydroplane on the rotor surface. The grooves act like grooves on a tire and give the material somewhere to go so the pad's surface can have better bite on the rotors themselves. Brembo's GT rotors are also zinc chromate coated. This gold coating resists rust so you won't have rusty water dripping out of your brake vents and staining your expensive wheels every time you wash your car. The unrubbed areas of the rotor also won't get all rusty and crappy looking as time goes on. If your car is all detailed out, you might appreciate this feature.
The rotors are bolted in full-floating style to aluminum alloy hats. The alloy hats save a considerable amount of weight. Full floating refers to the fact that the rotors are attached to the hats with shouldered bushings that allow about 0.012 inch of free movement between the hat and the rotor. The advantages of floating the rotor are a reduction of stress on the rotor as it thermocycles. This makes the rotor much less susceptible to warping as the rotor is allowed to expand and contract without binding forces at the hat. The rotor wears more evenly over its service life if it is floated for these reasons as well. Floating rotors also keep the rotor at true centerline of the caliper, which reduces caliper piston knock back. Piston knock back is when the rotor warps or bearing play in the hub or flex in the spindle allows the rotor to knock the pistons back into the caliper when the brake isn't being engaged. Brake piston knock back is a serious issue in performance cars and can cause the brake pedal to be low and mushy unpredictably. Sticky race tires can also exaggerate the hub and spindle weaknesses and tend to make knockback worse.
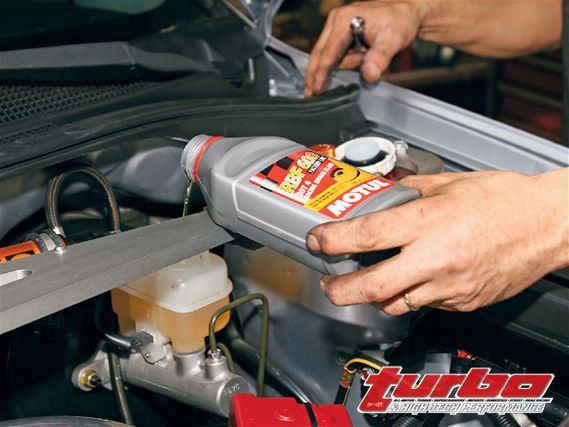
A major drawback to floating rotor technology is that they cost more to produce. Tighter tolerances must be held in the machining of the rotor and hat. This means greater cost to the consumer. Another disadvantage is that floating rotors are typically noisy in use; the rotor tends to move around making a rattling noise when the car is driven. Those who are picky about odd noises in their car can be driven nuts due to this. Brembo has a unique, simply elegant solution to getting rid of most of this noise. They use a tension spring mounted to every other bolt to keep the rotor captured so it's still free to expand and contract but won't bang around and make much noise. This allows race floating rotor technology to be used on a kit for a fussy customer.
Even though the kit is huge, the rotor is much bigger and the caliper holds brake pads nearly twice the size as stock. The entire front brake assembly is 2 pounds lighter than the stock brakes, thanks largely to the elaborately machined monoblock calipers and alloy hats. Brembo warned us that the kit might not fit cars with 18-inch wheels. When we installed the kit, the calipers were very close to the inner rim of our CE28N wheels, there was only about 0.08-inch clearance, slightly under the 0.12 inch Brembo recommends.
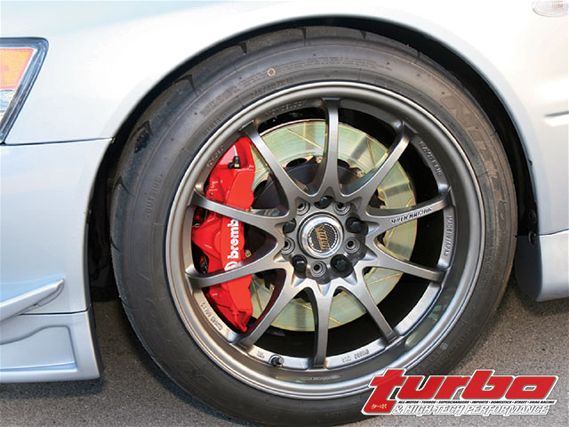
The Brembo GT kits comes with there own brand of high-performance pads designed for high-performance street and limited track use. There are a number of other pads available in just about any compound under the sun from many providers of racing brake pads. Brembo recommended using their pads first and then deciding if a higher level racing pad material is needed. The kit also comes with braided steel brake lines. Braided steel lines improve brake feel, as they don't expand when pressure is applied to them. Thus they transmit more force from the user's feet to the brake pads.
With the ultimate front brake kit now in place, our attention was turned to the rear of the car. We wanted to upgrade our rear brakes to keep balance between the front and the rear brakes, something ignored by many tuners and Brembo had a really cool off-the-shelf solution for us. The Brembo rear kit uses a four-piston rear caliper that uses a pad over twice the size of the stock rear caliper. A huge 328mm, or 12.9 inches, slotted rotor is bolted full-floating style to an alloy hat with an integral parking brake drum. Since the parking brake drum is hard-anodized aluminum, it's meant to be used only for emergencies or to hold the vehicle stationary when parked. For rally or drift use where the parking brakes are used to initiate slides, Brembo has a special order optional hat with a steel liner in the alloy hat. Our Evo is never going to see the dirt we hope, and who the heck would waste the Evo's sophisticated FWD system Evo by drifting one.
Since the four-piston caliper is so much larger than the stock caliper, the rear brakes ended up weighing 4 pounds more than stock. However, we think a total weight gain of only 2 pounds total for all four brakes is well worth having tons of braking power. It might seem that all of this brake system is overkill but if you look carefully, many expensive and exotic cars of about the same weight as the Evo have the same size brakes as standard equipment.
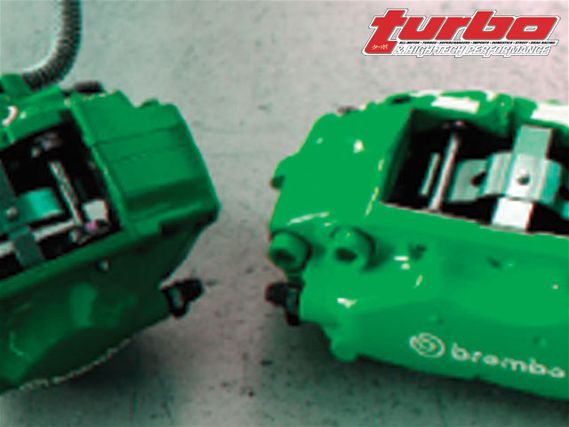
We bled our brakes and flushed the system with Motul RBF 660 brake fluid. Motul's RBF formula is one of the best fluids, performing nearly as well or better as ber expensive exotic stuff like the legendary F-1 brake fluid standards Castrol SRF and AP650. When brake fluid gets really hot it boils. Boiling fluid has bubbles in it that are filled with compressible gas. The compressible gas causes the brake pedal to drop to the floor. This is another type of brake fade that must be avoided.
Motul's dry boiling point is an amazing 660 degrees F. Motul works so well that our team's race cars need only bleed the brakes once a season, instead of the typical once a race. Most brake fluids absorb moisture from the atmosphere. When the brake fluid absorbs moisture its boiling point rapidly drops rendering it less effective. Even though the brake fluid is contained within the brake system, it still can quickly absorb a surprising amount of moisture from the atmosphere that is inadvertently drawn into the brake system. Some brake fluids can deteriorate greatly from this phenomenon with as little as one heat cycle of the brake system. Motul resists absorbing moisture from the atmosphere better than most brake fluids so its inherent high boiling point lasts longer than most fluids. If you do manage to boil Motul, surfactants in the formula cause the bubbles formed to rapidly dissipate and you get a recovery of your brake pedal feel.
Our stock brakes were powerful and inspired confidence. Our new brakes left us speechless. The pedal is rock solid and the brakes very easy to modulate with light pressure. Although we haven't had a chance to try our system on the track yet, we did test the system's balance twice in panic stop mode. Both times the gummy Nitto NT01's and the mighty Brembo brakes saved the bacon so there will be more segments of Project Evo to come.
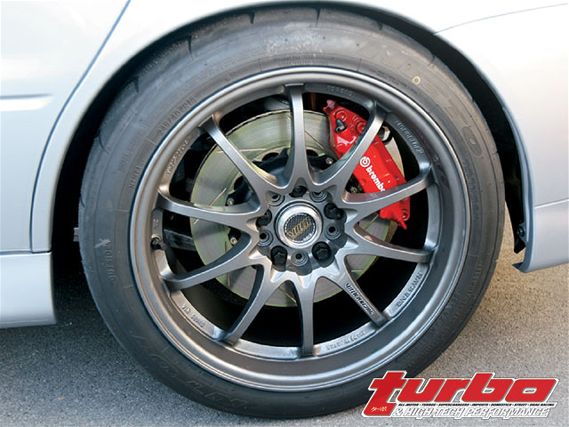
While we had the front of the car apart we decided to install Nagisa's Auto Gacchiri Supports under the front fenders. Nagisa is a small supplier of very trick suspension parts in Japan, specializing in bearing-equipped adjustable suspension links and braces to stiffen the chassis beyond the typical strut tower and lower control arm brace. We've always been impressed by the innovation and quality of Nagisa's parts and have used them successfully in several other street and race car projects over the years with great success.
The main problem with Nagisa's parts was that they were very hard to get in the U.S. We had to get one of our friends, who is stationed in Japan for a work assignment, to buy the parts at retail performance parts outfits and ship them to us. This was a hassle and very expensive. More Japan, which started to import and inventory many of Nagisa's trick parts right here in the U.S., has helped solve this problem. Now the parts can be bought with a phone call or a click of the mouse.
The braces require the removal of the front fenders and the entire front bumper fascia, which is slightly tricky because the Evo has a somewhat delicate aluminum front fenders and some hidden snap-type fasteners in the lower part of the fender that require some care to pop loose without distorting or scratching the fender. Work slowly and carefully here. The stock fenders are very light, probably lighter than many of the carbon or fiberglass replacement parts on the market. After carefully removing the fenders, the braces bolt to the door hinges holes, and the forward part of the brace bolts to the unibody about even with the shock tower using one existing hole and requiring that another hole must be drilled in the unibody at this point as well.
Once installed the Gacchiri brace triangulates this highly stressed part of the chassis, much like how extending a rollcage through the firewall does. Now the upper part of our unibody is reinforced with braces spreading torsional and bending loads over a wide area of the unibody.
Upon reassembly of the front end, we were simply amazed at the difference. We felt that these braces would make little difference because of the rigid and triangulated WORKS front-strut tower brace and the extensive matrix of Cusco Power Braces fortifying the underbody. We were wrong; these braces make a bigger difference in body stiffness than any one single brace that we've installed so far. We noticed a difference in ride comfort right away. A stiff chassis allows suspension to work better at absorbing bumps and, believe it or not, the braces made our stiff competition sprung Moton shocks and stiff sidewalled Nitto NT01 tires ride about as well or better as a stock Evo.
An Evo isn't known for refinement and they exhibit a pretty large amount of squeaks and rattles from the factory compared to a luxury car like a Lexus. Our Evo has had its share of squeaks coming from the dash and cowl area of the car. Amazingly, the braces stopped the majority of undesirable noises coming from this area. The stiffness is very apparent when jacking up our Evo compared to unbraced Evos. When jacked from one corner, our car doesn't flex or sag like stock Evos. The whole car lifts at once, much like a car with a rollcage. Even when one corner of the car is jacked by itself, the doors all open and close easily. When driving up steep driveways on a diagonal, sometimes one or two wheels are lifted off the ground.
When driven there's an amazing difference in the solidness feel between our chassis and a stock Evo. Our car feels much like a caged car and the steering response is tight and solid. Although these braces have zero bling factor since you'll be the only one who knows they're there, they're probably the first brace we'd recommend installing.
With our ultimate suspension and brakes, we will now have to focus our attention to the engine in our ongoing quest to build the ultimate performance family car.