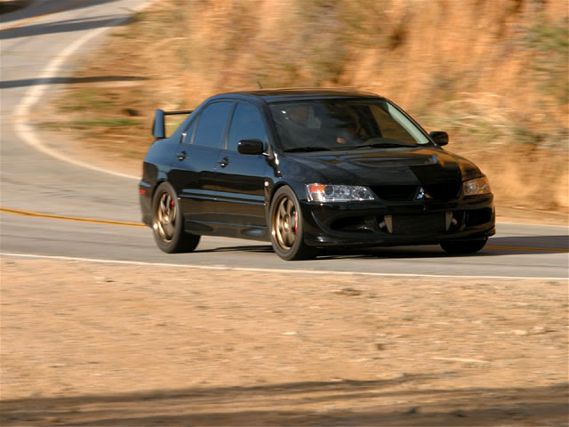
We love the EVO VIII. It's the most well balanced, all-around car we've ever driven for any price. It has reasonable power with tons of upgrade potential in its well-developed bulletproof 4G63 engine. Then there's the handling-it's so easy to drive hard at the limit. The stock tires have near-race-tire grip, the balance between under and oversteer is just right, the steering is quick and responsive and the car has an honest, non-computer aided linear feel. The brakes are firm, fade-free and powerful. Even when driven clumsily, the EVO still makes the inept look good.
Others share the same opinion. Turbo's sister publication "Sport Compact Car" tested the EVO against offerings from Porsche and BMW and it still came away the overall winner, much to the teeth-gnashing chagrin of brand-conscious, Euro-status-car-driving yuppies around the country.
The EVO's construction is equally impressive. It's easy to tell it was designed at the factory for WRC Rally punishment. The chassis bristles with beefy tower and underchassis braces stock. The front crossmember is a huge perimeter unit that dwarfs anything we've seen. The massive rear crossmember is cast from stiff aluminum alloy. The crossmembers bolt to the chassis in numerous places with big bolts. The suspension pivots and ball joints are huge. The unibody has many heavily reinforced points with multiple layers of metal and stiffening ribs and buttresses. This baby was born to run.
So how do we improve on this batch of automotive goodness? A car this good can be easily spoiled with too heavy a dose of tasteless aftermarket bling-bling. The trick here is a carefully engineered package of properly selected aftermarket parts. Our goal is to make the ultimate daily driver, at least at first.
We want to enhance the overall driving experience of the EVO, not just increase its power or give it stick in the corners. Lag and throttle response must remain crisp and the ride must stay compliant if we're going to attempt to make the car uncompromisingly better- a hard task, indeed, considering the lofty starting point. Let's dig into our EVO and get to work.
Wheels And Tires
To stay inline with our goal of streetable performance, we ruled out the simple way to improve grip, like throwing on a gummy set of R-compound race rubber. Instead, we obtained the stickiest non-racing tires we could find-the BFG Comp TA/KD 245/35-18 . When testing other projects, we drove the KD against other sticky rubber and were amazed at the tire's grip and predictability at the limit. Only full-race DOT rubber could surpass the KD in performance and then by not much. Amazingly, the KD has a UTOG tire wear rating of 220, far better than the 160 or less typical of sticky street rubber.
We scrapped the EVO's stock ultra-light Enkei roll-forged wheels for the lightest, strongest wheel we could find. Putting a wider rim on the car would help keep the tread flat on the road, so we chose Volk TE37 wheels, sized 18x8.5 with a 30mm offset and weighing only 18 pounds. The Volks are a true forged wheel, in which aluminum billet is smashed into a die with tremendous force, squeezing it into a wheel. This violent process refines and aligns the grain of the metal and is the strongest possible process to manufacture an alloy wheel. The aluminum gains strength and ductility during forging, so the wheel has thinner section widths without sacrificing strength.
Our choice of big meats wasn't going to fit in the stock wheel wells without rubbing. We sent Project EVO to Brian Kono of Afterhours Automotive fame to have the wheel wells massaged. He subtlety flared our fenders to clear the tires without rubbing and repainted the inside of the wheel wells. Although it's a lot of work, the killer looks and the traction these tires afford are worth it.
The grip of the tires is amazing, so much that it threw the balance of the car' suspension off. The once taut and flat-cornering EVO now leaned in the corners like some sort of base sedan because the added grip increased cornering speeds and allowed a lot more weight transfer to the outside tires. Also, the increased grip made the car's once-firm suspension feel soft and floaty.
We tried slapping a set of lowering springs on it in hopes this would firm things up, but these lowered the car too much and didn't stiffen it enough. Although the car looked sharp lowered, its handling was now worse than stock and the ride was rough for the level of cornering.
Suspension
We want the ability to adjust ride height and to cornerweight our car, so coil-overs are a must.
When HKS's Hyperdamper II suspension system became available, we grabbed it. From previous experience, we knew the Hyperdamper would have a huge adjustment range and a base valving that was firm, not rock-jarring solid. This is the exact daily-driver-friendly setup we're looking for.
The Hyperdampers feature 30-way damping adjustment, which increases both compression and rebound damping externally with an easy turn of a knob. They come with pillow-ball mounts, allowing adjustable camber up front and eliminating all the gushy rubber in the stock mounts. This ensures that all wheel motion will be damped instead of dissipated in flexing rubber, letting the car bob.
The front struts use an inverted shaft, a feature that's compatible with the EVO's WRC DNA. The inverted shaft has the strut shaft upside down inside the strut tube and the shock body appears to be the shock shaft that attaches to the upper pillow ball mount. This method of building shocks is many times stronger than the normal conventional way with the body down and the shaft up.
The Hyperdampers feature hard-anodized and stainless hardware to eliminate rusting and sticking of the adjustment collars. They bolted in easily like stock factory pieces. The Hyperdampers featured a reasonable 30-percent stiffer spring rate, which wouldn't break our teeth. The front springs are rated at 5 kg/mm, up from the stock 3.8 kg/mm. The rear springs are 6 kg/mm, up from the stock 4.8 kg/mm.
One of the coolest things about the Hyperdampers is they have a 1.5-inch shorter body and thus lower the car without reducing wheel travel. This is a huge advantage for both ride comfort and handling.
We demanded that all of our suspension elements have racecar-like adjustability. To further reduce body roll and give us more tuneabilty, we called upon Nukabe products for a set of Cusco anti-roll bars. The Cusco bars are currently the stiffest EVO bars on the market. They fit like a charm. The front bar installation, however, required we remove the lower engine and transmission crossmember, steering linkage and exhaust. The front Cusco bar is 25mm, compared to the EVO's stock 23mm, and offers a 123-percent increase in roll resistance over the stock bar.
The rear Cusco bar is 23mm, compared to the stock 18mm, and features three-way adjustment, which allows fine adjustment of oversteer and understeer. The adjustment range is 108 percent, 122 percent and 138 percent more roll resistance than stock in each of the three positions. We expect to use the adjustable feature to help us set up the car rapidly at the track.
The EVO's suspension is amazing. The suspension links are all constructed of strong, light and stiff forged aluminum. The rear suspension is multi-link and most of the rear suspension pivots in a spherical bearing that are sealed against the elements and float in a thin layer of hard rubber for noise isolation.
There's little "sticksion," little flex in the wrong direction and long life to boot. It's just about impossible for the aftermarket to improve on these pivots. However, the rear trailing arm bushings have a huge gushy rubber front pivot and the front lower control arms pivot in soft rubber. These bushings are probably concessions toward ride comfort.
To help hold our wheel geometry in line with our newly installed, bigger, stickier tires (while avoiding a spine-compressing ride), we replaced the non-bearing gushy rubber pivots with hard polyurethane parts from Energy Suspension. The urethane bushings were used for both lower control arms bushings, the rear suspension trailing arm and the front anti-roll bar.
When installing the big front lower control arm bushing, it's necessary to chamfer the lower control arm hole with a .200-inch radius, or it's almost impossible to press the bushing in. The instructions say to merely chamfer the control arms' hole's lead in. We lightly chamfered the hole, but weren't able to get the bushing in. We slowly removed more and more material until the bushing popped in.
We also installed Energy's bushings in the differential carrier and differential moustache bar. These hard bushings will help prevent any wheel hop our sticky tires may create on launch or when powering hard out of a corner, by greatly reducing differential movement and wind up. Getting rid of this will greatly extend the life of other drivetrain components. Unlike other hard differential bushings, Energy's urethane parts didn't transfer any more noise or vibration into the cabin.
Once we installed our suspension, we drove Project EVO to West End Alignment to have Darren Nishimura align the car. Darren is well known in the local So. Cal. road racing scene as the guy to set your chassis. Darren set our front camber at -2 degrees, and the front toe slightly out. The rear camber was set at -1.5 degrees with 0 rear toe.
Darren also set the corner weights for 0 cross weight with 200 pounds in the driver's seat. We also set the front Hyperdampers at 25 clicks, nearly fully stiff, and put the rear shocks at 20 clicks. We set the rear Cusco bar in the middle setting as well to keep close to the stock balance between front and rear roll stiffness.
We're very impressed with this setup. The Hyperdampers ride with less harshness than the stock suspension, yet still resist roll. The easy compliance of the EVO's rally-bred suspension is still there, since the dampers' short bodies have ample wheel travel, but body roll is reduced by more than 50 percent to slightly less than stock, even with the sticky tires.
The EVO's precise steering is now razor sharp; turn-in is fantastic and the car only understeers with the most ham-fisted wheel motions. The EVO's natural balance is about neutral. Our setup will work for both autocross and road course work, which is unusual.
EVOs outfitted with fat R compound tires that are the same size as ours may desire a stiffer, more race-oriented suspension, but our setup can't be beat for total street and weekend warrior track dominance. We can't wait until the next NASA HDPE open track event to see how many supercars we can embarrass with this little giant killer.
The only downside is the car's cornering limits are so high, perhaps higher than any street car we've ever driven, that we can't safely probe the car's capabilities on the street. The final setup will have to be determined on the track.
Brakes
The EVO comes with amazing stock brakes. Big four-piston front and two-piston rear Brembo calipers clamp big rotors. With Brembos all around, the stock EVO brakes are better than many upgrade kits right from the factory.
Increase the grip with significantly bigger tires like we did and fade becomes a possibility. Although not a huge problem, we noticed a decline in pedal feel and an increase in pedal effort when pounding around the track. Also, the stock pads were noisy, and wore the stock rotors quickly to boot. Stock replacement pads were also expensive from the dealer.
We wanted to enhance our brakes to keep them steady and consistent. The EVO's Brembos didn't need serious upgrading, but we did tweak them in the interest of reduced fade and better pedal feel and modulation. We replaced our front rotors with Project 's two-piece front rotors. The rotor is pillar vented, which has more interior fin area, so that heat dissipates better than the stock Brembo vane type vents.
Pillar venting also makes for a lighter rotor. The rotor is grooved on the outside, which allows hot vaporized brake pad material to escape, preventing the pads from hydroplaning on the layer of vaporizing pad. This does the same thing as drilling the rotors but without the risk of cracking that drilling presents. The slots also give water a place to escape for wet braking, helping out first stops after a puddle in cold, wet weather.
The rotors also have a special heat-treating hardening process for longer life, with harder, more aggressive brake pads and increased warp resistance. The rotor's center part is machined of aluminum alloy and anodized blue to reduce heat transfer to the hub bearings and to remove several pounds of rotating and unsprung weight from the rotor.
For the rear, we used a trick rotor from Stillen. The Stillen rear rotor features pillar vanes like the Project rotor to improve cooling and reduce weight. They're also heat-treated to improve wear life and to reduce the chance of warping. They're slotted and have an integral drum to be perfectly compatible with the stock drum parking brake. The rotors feature rust- and heat-resistant paint on the hub and inside the rotors vents. They have stripes of temperature-sensitive paint so the rotor's operating temperature can be determined. This is very useful when selecting brake pad compounds.
For brake pads, Vishnu Tuning supplied us with some recommended Ferodo pads, which feature a wide operating range. We were assured these pads would be more fade resistant than stock, while running quietly with less dust and longer life.
For track use, Project M also supplied us with a pad that, although it's still streetable, it provides a steady coefficient of friction up to 900 degrees. We haven't evaluated these pads yet, but we've heard good things about them and look forward to that opportunity, probably during our first track event with the new suspension.
To improve pedal feel, Vishnu also supplied some of its braided steel brake lines. The braided lines don't balloon under pressure like the stock lines do; thus, every bit of pedal travel goes to the calipers. We were surprised at how much difference these lines made.
The pedal feels like rock solid like a real racecar; impressive, considering the stock pedal feel was quite good as well. It was a noticable difference. The car's ABS system seemed to like it as well, seemingly cycling faster with a higher resolution. We don't know if that's true or not, but the seat of our pants told us so.
Finally we replaced our stock Japanese fish oil brake fluid with Motul RBF 600 brake fluid. Motul's RBF formula is one of the best fluids, performing nearly as well or better as exotic fluids like the legendary F-1 standard Castrol SRF and AP550. Motul's dry boiling point is 600 degrees Fahrenheit. It works so well that racecars need only bleed the brakes once a season, instead of the typical once a race. Motul also resists absorbing moisture from the atmosphere better than most brake fluids, so the high boiling point lasts longer than most fluids.
Our impressive stock brakes are now even more impressive. We won't need to upgrade them further, no matter how involved we get with this project. The EVO has some of the best stock brakes we've ever sampled.
Our world-class handling and braking EVO is now in exotic stomping territory with our few simple mods. We didn't sacrifice any of the day-to-day pleasantness of driving this car in our quest to improve it.
In the next installment of Project EVO, we'll work on getting some power to back up our grip.