Back in Part 1 of our Cam the Ram series on the 5.7L Hemi, we subjected the bone-stock test motor to a simple cam swap. The wrecking yard motor was run on the engine dyno using a Fast XFI/XIM management system in two configurations, first with the stock cam, then with a mild Comp cam. Equipped with the stock cam, the 5.7L produced 370 hp and 407 lb-ft of torque. These numbers jumped to 401 hp and 427 lb-ft with the installation of the 260H-13 Comp Cam. The cam not only improved the peak power numbers, but offered consistent gains through most of the rev range with no loss in low-speed torque. Hot off the success of camming our Ram, we decided to take things to the next level. Looking to continue the theme of impressive torque production without sacrificing drivability, we elected the tried and true method of increased displacement. Basically we’re adding inches to get pounds—foot-pounds of torque.

| When building a motor to maximize torque production, bigger is always better.
As much as we hated the thought of tearing into a perfectly good running Hemi, out came the wrenches and sparks began to fly. The 5.7L was disassembled and sent over to L&R Automotive for machining and assembly. To increase the displacement, Scat Enterprises helped us out with a stroker assembly designed specifically for the 5.7L Hemi. Unlike the larger 6.1L, the displacement of the 5.7L was limited by a combination of the small bore size and the ability to dramatically increase it. The majority of the additional displacement came from increasing the stroke from 3.578-inches to 3.795-inches. Even larger stroker cranks are available for the 5.7L block but cost and complexity increase with displacement. The combination of the 3.795-inch stroker crank and 3.937-inch (.020-over) bore resulted in a final displacement of just under 370 ci. This combination nearly matched the displacement of the larger 6.1L, but with a different bore/stroke combination (the 6.1L combined the stock 3.578-inch stroke with a 4.055 bore). In addition to the hike in displacement, the forged rotating assembly provided a bulletproof short-block that was capable of withstanding some serious punishment.

| 1. The 5.7L Hemi stroker featured a forged crank, rods and pistons from Scat to produce a bulletproof bottom end. The .020-over, (small dome) forged pistons from Probe Racing combined with the 3.795-inch forged steel crank and 6.215-inch 4340 forged steel connecting rods. Total Seal provided the ring package for our Hemi stroker combination.
The Scat and Probe crank, rods, and pistons were combined with a set of new rings from Total Seal, and bearings. To get things started, we installed the 260H-13 cam on the 5.7L, but don’t worry, we had a wilder cam waiting in the wings. The cam was installed using new cam bearings, but we elected to reuse the factory lifters, despite the 5.7L being equipped with MDS and our intention of eventually running a high-lift, long-duration cam. In addition to the cam, Comp Cams also supplied a new double-roller timing chain—an important component on a motor that eventually made power all the way to 7,000 rpm. To feed our newfound displacement, we elected to have the stock 5.7L Hemi heads ported by the flow experts at Total Engine Airflow. The stock heads already offered sufficient airflow to support more than 525 hp, but when searching for added performance, more flow is always a good idea. Besides, the ported head might support the additional power we have planned for the future. Porting the heads improved the flow rate by more than 50 cfm, bringing the intake flow from 260 cfm to nearly 320 cfm. The exhaust flow improved by just more than 35 cfm to 205 cfm (both measurements at .600 lift). The heads were secured to the stroker short-block using ARP head studs and Fel Pro MLS head gaskets.

| 2. L&R Engines was responsible for the machine work and assembly of the short-block. To ensure adequate sealing once we add boost, we secured the cylinder heads with ARP head studs and Fel Pro Multi-Layer Steel (MLS) head gaskets. The factory MDS hydraulic roller lifters were carried over from the original 5.7L.
In terms of the oiling system, we installed a new stock oil pump, but augmented the system with a Milodon oil pan, pickup, and windage tray. In preparation for Part 3 of this adventure, we welded a drain tube in the Milodon pan for our future turbo motor. We also replaced the factory injectors with a set of 75 pounders using the stock fuel rail. It was necessary to install spacers under the rail to make room for the taller injectors. As with the 5.7L cam test, we utilized a set of SRT8 exhaust manifolds feeding short extensions. Long-tube headers would help this combination substantially, but it was interesting to see the power produced with the stock manifolds. Another carryover from our original 5.7L cam test was the manual throttle body (converted from drive-by-wire). The motor was run with both the stock plastic truck and STR8 aluminum intake manifolds, and both managed to produce the same peak power (with both cams). This came somewhat as a surprise, as we expected the truck intake to offer more low-speed power but lose out on top compared to the SRT8. Run with the 260H-13 cam, the 370-inch stroker 5.7L Hemi pumped out 454 hp and 453 lb-ft of torque. True to form, torque production from the stroker exceeded 425 lb-ft from 3,900 rpm to 5,600 rpm. Best of all, the stroker improved the power output (over the 5.7L) throughout the rev range, offered improved idle quality (with the same cam), and looked just like the stock motor. The additional displacement increased the power output by 53 hp and 26 lb-ft over the 5.7L equipped with the same cam (the 5.7L produced 401 hp and 427 lb-ft in Part 1).

| 6. While we had the engine apart, we elected to upgrade the oiling system. Milodon supplied not only a new pan, but a windage tray and matching pick up.
Despite our success with the stroker combination, we couldn’t help but wonder if the extra cubes might respond to wilder cam timing. Additionally, would the expected improvements in peak power come with a penalty down low? To find out, we installed a much more aggressive cam profile. The custom hydraulic roller cam from Comp Cams featured .589 lift (both intake and exhaust) and dual-pattern duration specs of 239/247 degrees at .050. The LSA checked in at an idle-friendly 114 degrees. As we experienced in Part 1, cam swaps on the Hemi were a breeze on the engine dyno. After the swap, the new cam offered some serious power gains, increasing the peak numbers from 454 hp and 453 lb-ft to 526 hp and 451 lb-ft. Impressive as the numbers sounded (and they were), they did come with a cost. The trade off for all that top-end power was a loss in torque below 5,100 rpm; as much as 38 lb-ft. Which cam offers more appeal depends a lot on the intended use. If you are looking for maximum acceleration, then the big cam is the way to go, but most street drivers might be better served by the smaller cam. Of course, you can always venture somewhere in between. Check back with us next month, when we take our boost-ready stroker and pump up the volume with a single turbo kit.

| 10. Lacking headers for this test, we again relied on the SRT8 exhaust manifolds. Dedicated headers offer as much as 15 hp over the stock manifolds.
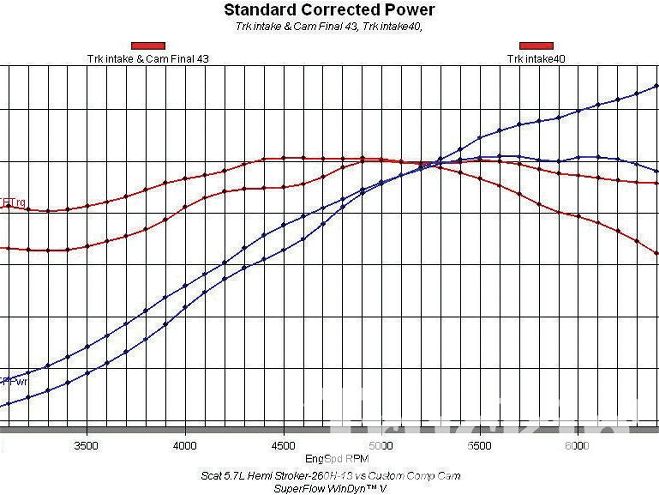
| hemi Performance Cam Swap Part 2 comp Cam Dyno Results