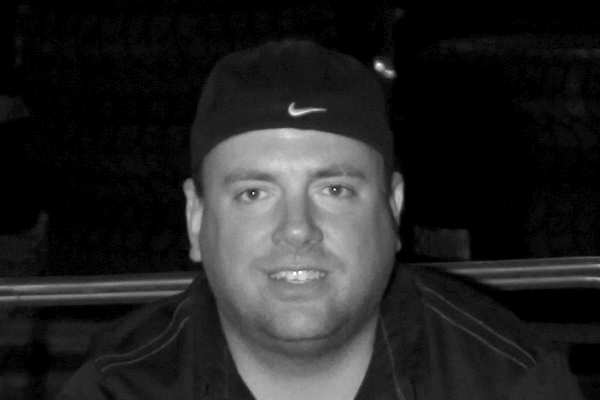
Pete Trasborg
Brand Manager, Jp
It all started innocently enough. We wanted our ’01 Wrangler to perform better both on- and off-road. To that end, we got rid of our 41⁄2 –inch short-arm suspension and went with the LCG long arm kit from Teraflex (“Long Arm Lowering Kit,” Oct. and Nov. ’10). But at the time, Teraflex didn’t offer a kit that was low enough for us. We wanted to go to 33-inch-tall tires and felt like we didn’t need the 4-inch kit. So we played guinea pig and went with 3-inch springs and shorter shocks. We couldn’t go any lower without cutting the floor to clear the rear upper control arms. While the kit we went with never ended up in production, the company did start making a LCG Pro kit with no shocks and springs (PN 1149075) that you can add springs and shocks to.
We were happy with our lowered TJ on smaller tires with a long-arm suspension. It crawled better, climbed better, and performed much better on-road too. But eventually inchitis got us and we started asking ourselves “What if?” As in: “What if we could get it to perform better yet?”; “What if we could toss those 33s for 35s and not lift the Jeep more?”; “What if we could stop smacking our bumpers so hard coming off of and approaching obstacles?”
That series of questions led to swapping gas tanks, adding corner armor and new rocker guards, and stretching the wheelbase out to 971⁄2 inches (“Stealth Stretch,” Apr. ’12). While we were at it, we threw some 35s on the Jeep and set our bumpstops lower to keep the new meat out of the fenders at full bump and some limiting straps in the rear to keep the shocks from topping out. We got all of our “What if” questions answered, and we were very happy with the suspension on our low and long TJ. It still looks like a Jeep and performs very well on- and off-road.
But, in the year and a half that we’ve been running it like this, we’ve noticed some things that bugged us, most of the issues are up front. So over time, we’ve chipped away at this problem or that problem, eventually cobbling together a custom steering, track bar, and bumpstop setup by trial and error. At times it seemed like we opened a can of worms and we wished we could go back and just live with the issues. But a year after starting, we are very happy with what we ended up with. Here’s what we learned along the way.
Step By Step

It all started with the track bar. We had a HD Currie Enterprises track bar in the Jeep which features a Johnny Joint at the frame end and aside from some minor drilling is a direct bolt-on. However, when wheeling the Rubicon Trail, someone noticed that the axle end of the track bar was hitting the axle-side bracket and had been doing so for long enough to both bend the bracket and wear a groove into the track bar. Once we got it home, we noticed that the hole in the frame-side mount was hogged out as well.

Currie Enterprises offers axle-side track bar ends with more of a bend in them to fix the problem we were having. Of course, we didn’t know this at the time. Also, we are a big fan of our suspension stuff being in a double-shear configuration rather than the single-shear factory style mount. For that reason, we ended up at the doorstep of T&T Customs. It wasn’t easy, but we cut off the hogged-out frame-side track bar mount, welded on a T&T mount, and swapped track bars. In addition to the double-shear at the frame, the new track bar is 13⁄8-inch, 0.219-wall tube.

Here’s a look at another problem with that ball-style mount that Jeep put in the TJs from the factory. While this is a 1-ton tie-rod end, all ball-and-socket style joints share this issue. That issue being that maximum articulation is about 20 degrees off center. It is really easy for a Jeep with a flexy suspension to max this out. While the frame-side Johnny Joint on our Currie track bar might have had more than this, the hole was still hogged out. We aren’t sure if we hogged it out by over-articulating the joint, or if it was from the axle side end repeatedly hitting the mount there.

We knew that we were going to have to pull the driver-side coil, shock, and caliper to get in there to hack the welded-on cast mount out, so while we were in that far, we decided to fix another issue that was making our dentist rich: the front bumpstops. While they were set to perfectly keep our 35s out of our fenders bombing down a washboard road meant we were constantly smashing off the polyurethane bumpstops. Hard. While there are several active bumpstops out there, we knew we were going to be in them all the time and wanted something that would last. After a ride in some of Teraflex’s Speedbump-equipped Jeeps we decided to go with Speedbumps.

Of course, that required more saw blades and cutting discs. But the instructions are very well written and we had no problem setting the bumpstops so that our tires would stay out of the fenders when articulating. Just as a warning, these aren’t bolt-on. Not only will you have to cut your factory mounts out (and holy cow did we have a ton of rust in there) but you need to weld in the new mounts for the cans. That said, we’ve whipped on these things for over a year now, and we haven’t noticed anything except a much smoother ride up front than we ever had before. No fading, no weird noises, and they work today like they did when new.

Somewhere, somehow, and without our noticing until it was way too late we managed to tear not one, but both of the boots on our Currectlync steering setup at the knuckles. The clunking told us both tie-rod ends were shot. We’ve said it before, and we’ll say it here as well: We really like the Currie Currectlync steering. It might be the best bolt-on steering upgrade for TJs, LJs, XJs, and MJs. But, the company states that a minimum of 21⁄2 inches of lift is needed to run it, and with our 3 inches we were pushing that. Also, we decided we wanted to flip the steering up over the knuckles and maybe avoid more torn grease boots in the future.

If you don’t like cans of worms, turn back now. The decision to flip the steering up over the knuckles meant more cutting, custom machining, and welding. The end result is worth it in our opinion, but if you don’t want to go down that road you can order a Currectlync setup. If you do want to follow us down the rabbit hole, here’s where we went. This is T&T Customs 1-ton steering setup. It features 1 5⁄16-inch, 0.250-wall tube powdercoated in silver vein with 1-ton Moog tie-rod ends.

Flipping the steering over the knuckles requires either new knuckles or a tapered reamer. Fortunately for us, this isn’t our first time playing with these tie-rod ends and we had a tapered reamer on hand from Parts Mike. This is the company’s inexpensive reamer, and when we got it at least five reamings ago, the company told us to use WD-40 rather than expensive cutting fluid to lube it. So far so good. We haven’t chipped or dulled it in all that work, and it worked just fine here.

Once you flip the tie rod and drag link up over the knuckle, the factory axle-side track bar mount is in the way. Add to that a straight tie rod, and you can’t even get it installed without some more cutting and grinding. The kink in the factory steering is to clear the axle-side track bar mount. We like our steering non-kinky. Also, if you flip the steering up over the knuckle and somehow manage to leave the factory mount on the axle, you’ll have some wicked bumpsteer. The drag link and track bar need to be at the same angle for no bumpsteer.

Yes, T&T had us covered there, too. The company offers steering and track bar mounts for both over, and under the knuckle, so this was a no-brainer for them. We went with the over-the-axle, weld-on mount. That meant that the trackbar needed to get shorter, so the company sent us a weld-on end so that we could modify the track bar we already had. Since we had the welder out already, that saved us some coin.

The last night crawler in the box is the sway bar end links. With the steering up higher, it gets into the factory axle-side end link mounts. So, they need to move up too. This kit from T&T has a 3⁄8-inch-thick sway bar end link mount with a 1⁄4-inch-thick support tab, and it can be cut to length. Ideally, your sway bar will be within about 10 degrees of horizontal when the Jeep is at rest on level ground. If you can’t cut the weld-on mount to achieve that, you should look into modifying the length of your end links.

The first time we saw this setup we were skeptical. Not only did the track bar get shorter, but the over the knuckle setup leaves no space for a steering stabilizer. It wasn’t until T&T tossed us the keys to one of its TJs and let us bomb down a nasty potholed road that we were sold. We’d seen it work off-road, but after driving it on-road with no bumpsteer, we were convinced. Not only does it drive well, but the much bigger and heavier-duty parts should last us forever—that is, if we look at them and grease them from time to time.