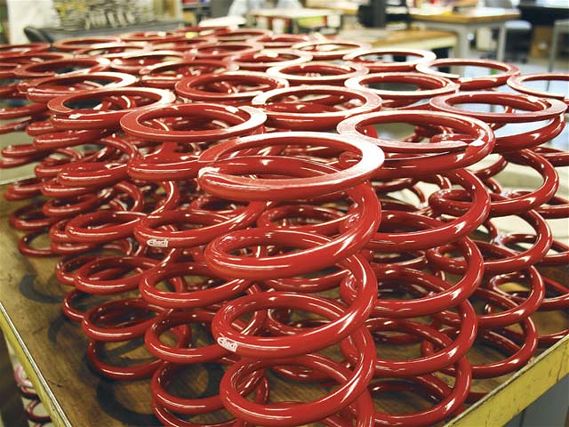
Eibach is arguably one of the most prominent and prolific vehicle spring makers on the planet, but this wasn't always the case. The German outfit began humbly enough some 55 years ago making varieties of industrial springs, like valve springs for diesel engines. In the '70s, the company focused some of its efforts on spring apps for motorcycles and motorsports, and in the following decade, that led to supporting tuning companies like Schnitzer and AMG. The '80s also saw Eibach enter the aftermarket fray with its own Pro-Kit and Sportline series offerings.
Fast forward to 2006, where Eibach has grown into a massive multimillion-dollar business with production in Corona, Calif., and Finnentrop, Germany, and warehouse distribution facilities in the UK, South Africa, Australia, Korea, Japan, Canada, and Mexico. In addition to suspension springs, Eibach now also hawks valve springs (again), dampers, stabilizer bars, wheel spacers and alignment components. It has also developed into an OE supplier for the likes of Kia and others. Quality has become synonymous with the Eibach name, largely because of its Million-Mile warranty, an assurance offered by no other spring maker in the market.
Recently, we were given a tour of the Corona facility to answer the question, how is a spring born? The Cali plant is where roughly 90 percent of the Eibach parts sold in the U.S. are made, and at any given time, the facility has over 200,000 pieces in stock. Since Eibach is the only suspension company in the country to house R&D and manufacturing in one spot, we figured they might know a little about how a spring becomes a spring.
1.
Suspension springs, like all parts, begin with research and development. Prototype sets are engineered by vehicle weighing and key elements like ride height, spring rate, factory suspension limitations and tire and fender well clearance. The trial springs are then subjected to test sessions where dynamics are analyzed. Eibach tests its suspension springs on a cycle tester (pictured), a mechanism that is designed and programmed to repeatedly compress the coils, and valve springs in a device called the Spintron, which is an electrically driven V8 motor with limited internals that can mimic several engine environments. When a spring design is finalized, it moves to the manufacturing process.
2.
Spring wire stock is stored in 2,000lb rolls and fed to the coiling machines via large spools. The spools are loaded in what appear to be tanks and reloaded by means of an elaborate rail network that runs throughout Eibach's plant. Since Eibach does valve and motorcycle suspension springs in addition to automotive coils, they generally have raw material ranging from 1 to 42mm in diameter. Because of their stricter standards, quality conscious outfits like Eibach will generally use only select mills for steel wire.
3.
Eibach Corona employs seven German-built Wafios high-speed compression spring coiler machines to spin and cut its wire stock. The devices are CNC-programmed, and each is dedicated to working with a specific diameter range of wire stock. Essentially, the machines use servomotors and hydraulic drives to compel several dies that pull in the programmed length of wire from the spool and twist it into shape, and then a cutter to chop off the freshly wound spring. Applications that require a flat surface go to grinding afterward; in grinding, springs are placed on an enclosed turntable that spins at high speeds with grinders above and below it moving in the opposite direction.
4.
Springs head to the shot-peening machine after grinding. Described as akin to a massage, shot-peening is a process that exposes the surface of the coil to metal shot moving at high velocities in order to relieve internal stresses in the wire, remove imperfections and leave a dimpled foundation for the powder coating to stick to. At Eibach, the spring sits on a conveyor belt as it moves through the machine and each spring is shot from three different angles. Shot-peening is said to extend spring life by something like 200 percent, which is why most of the top-dog makers think it's so critical.
5.
Every spring made in-house is pre-set several times in a spring compressor, that is, compressed so all the coils are touching. This gives the spring a permanent set and ensures it will not settle during its service life. In production, a spring is actually made to a longer free, or uncompressed, length than required because the spring gets shorter during the setting process, thus bringing it down to specifications. Pre-setting is time consuming, though, so many spring manufacturers will skip it altogether. Once Eibach pre-sets a lot of springs (about 100), several are randomly selected to go through quality control, then the bulk go to powdercoating and labeling.
6.The last stop on the tour takes us to a room filled with spring raters. The raters are actually utilized at several points throughout the R&D and manufacturing processes; samples are tested after coiling, after shot-peening, after powdercoating, and one final time by quality control. With a linear, single-rate spring, the graph on the computer monitor pictured should ideally reflect a straight line; a spring with a problem, though, say binding before it should, would reflect something other than a straight line on the chart.