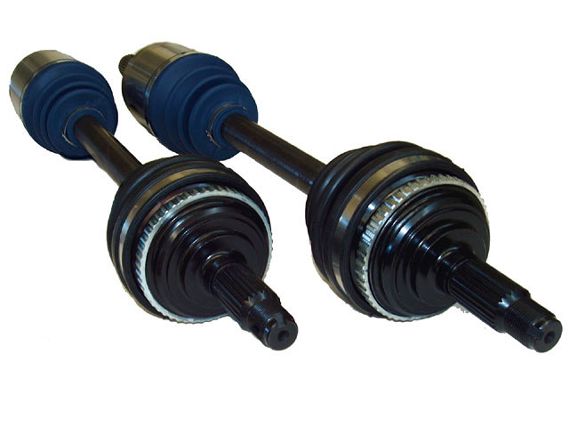
Ever wonder where aftermarket driveshafts come from? Surprisingly, race car axles that can handle massive power and more timid everyday street varieties are made much the same way, and, in the case of the Driveshaft Shop, in the same place. DSS has been around for over 30 years and handled everything from manufacturing competition shafts to being one of Long Island's larger local axle re-builders, at one time doing over 6,000 axles a month. In 2005, Driveshaft Shop owner Frank Rehak and his crew traded in their island roots for some Southern barbeque and opened a 22,000 sq. ft. facility in North Carolina to focus on its racing and aftermarket axle lines. Recently, we had a chance to speak to Rehak about the DSS operation and what goes into making a killer shaft.
Establishing a line of driveshafts for a given application begins by looking at what came as original equipment. Spline sizes are checked, and then the factory units are sent out for a quantative analysis to determine what it's made of and how it was heat treated. With this info DSS can deduce what the stock axles will handle and what is needed to improve them.
DSS admits it's a challenge to see which of their sponsored teams will push the limits of its product. It takes a lot of brain power to rate each axle accurately. However, with the likes of Norris Prayoonto, Skunk2 Racing, and even Spoon Sports putting its axles through their paces, DSS can breathe a little easier knowing it's done its homework. That testing has resulted in developments like larger splines, selected chrome-molys, and specialty heat treatments.
The end result is usually sent out and tested by a destructive tester before final prototypes will be used in a test car. The lab will twist the axle to destruction, and based on torque, tire size, and weight of the car, DSS can determine if the axle has met the mark set. This particular graph is a reflection of the test between Driveshaft Shop's new 2.9 level 26-spline outer CV against a larger 28-spline unit from an RSX/Prelude.
Which materials to use? That all depends on whether or not there's enough room to go to a bigger spline, and if not, what material can be used as a suitable replacement. The same philosophy is applied to the CV boots as well; DSS has sourced some of the best materials offered in this area, and have come up with a boot that is not quite plastic or rubber. It's a thermal material that handles speed very well, but also has superior sealing qualities.
For DSS, deciding what stage or level to make its shafts is no real secret; if the car is a Honda, generally they need to make all levels! Level 1's are made like stock-nothing real fancy just a good replacement. Then we move onto the level 2.9 axles that have Driveshaft Shop's killer new outer constant velocity (or CV) joint, which features one of the wildest heat treats know to man, able to hold a purported 475 hp at the wheels. Beyond the 2.9's, it's DSS' 600HP 3.9's and then the pro level 5.9's that both boast larger outer CV's and custom hubs to hold them.
Sources
The Driveshaft Shop 704/633-2380800/564-2244 www.driveshaftshop.com