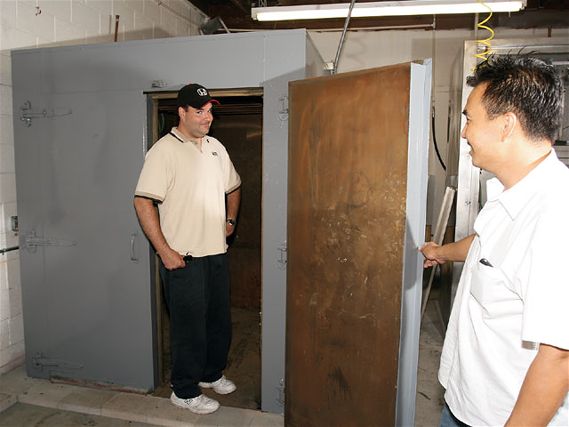
If you have been into this scene for very long, chances are that you might have some carbon-fiber parts on your car. Do you know what carbon fiber is? Do you know what makes it special? Do you know how carbon parts are made and how that affects its performance? If you are interested in all of that, read on, we hope we can explain some of the intricacies of carbon parts and carbon construction techniques.
You might think, carbon fiber is carbon fiber and it's all the same. If you want something made out of carbon just go to eBay and get the cheapest thing right? WRONG. Like a cat, there is more than one way to skin carbon fiber and there are cheaper ways as well as better ways to do it.
Well you might want to know what exactly carbon fiber is and why it is rad stuff. Carbon fiber is amorphous carbon, which means its molecules are arranged in a random interlocking manner making the overall material very strong. This differs from other arrangements of carbon molecules like graphite where the molecules are laid on top of each other in a regular crystalline pattern making it soft so you can write on it with a pencil.
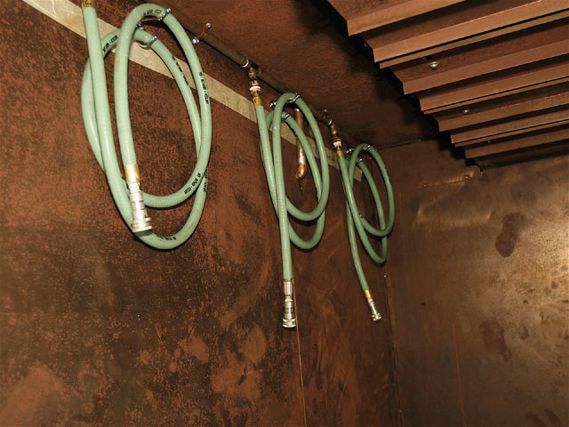
Carbon filaments are made by the oxidation and pyrolysis of polyacrylonitrile. In English, it is like baking kinda the same stuff your socks and sweaters are made of until it chars. Polyacrylonitrile molecules are formed in long chains that when heated in the correct conditions (usually in a pressurized methane rich environment like Andy's underwear), the non-carbon parts of the material evaporate away forming chains of nearly pure carbon molecules in the form of hollow filaments of carbon left where the threads of the polyacrylonitrile material were. These filaments are then spun into thread or yarn and then woven into carbon-fiber cloth. This is much like how the more common fiberglass cloth is made out of fine fibers of glass.
So now that we've probably caused your eyes to glaze over, let's get to the real reason why carbon stuff is so prevalent in the high-performance world. Carbon fiber's most important attribute is its mechanical properties. From the chart below you can see that carbon fiber is three times stronger and four times lighter than steel:
TensileStrengthDensityCarbon Fiber3.501.75Steel1.307.{{{90}}}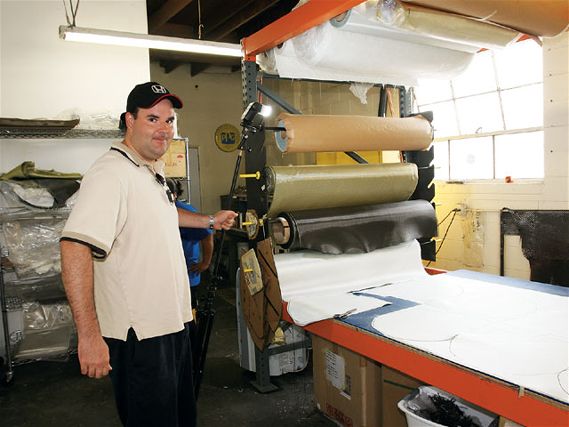
Sometimes the carbon filaments are combined with other fibers to alter the properties of the finished material. Kevlar, the ultra strong fiber used in bulletproof vests, is commonly combined with carbon to make it more impact and abrasion resistant. Spectra, another ultra-strong fiber, is sometimes used in this way. Boron can also be used to make the material stiffer. For the most part, in the automotive world Kevlar is the most common fiber to be combined with carbon.
Carbon-fiber cloth by nature is soft and floppy. To make it stiff so that useful stuff can be made out of it, the fibers within the material have to be locked together in a matrix. Usually that matrix is a plastic resin. The carbon cloth is soaked in resin and laid in layers to make a laminate of carbon-fiber cloth bond together with resin. When the resin cures or hardens, you have a stiff strong piece of carbon-fiber stuff.
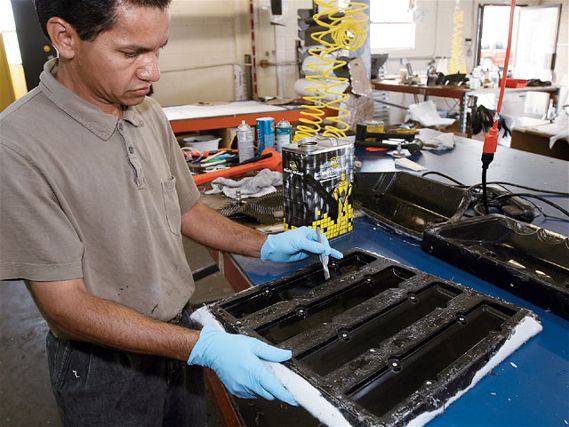
Less expensive carbon parts are usually made with polyester resin. Polyester resin is cheap, finishes well and is easy to work with. Most of your typical aftermarket performance parts for street cars are made with polyester, which is fine for many consumers. However, polyester-based carbon laminates tend to be brittle and can shatter when something is hit hard. It is also more likely to stress crack. To get the most out of carbon fiber's superior strength properties it is best to use a higher performance resin like epoxy. Epoxy is much more flexible, tougher and stronger than polyester, although it is harder to work with and has a yellowish cast that some find ugly. Epoxy also tends to turn yellow and chalky with UV light exposure so it should be clear-coated.
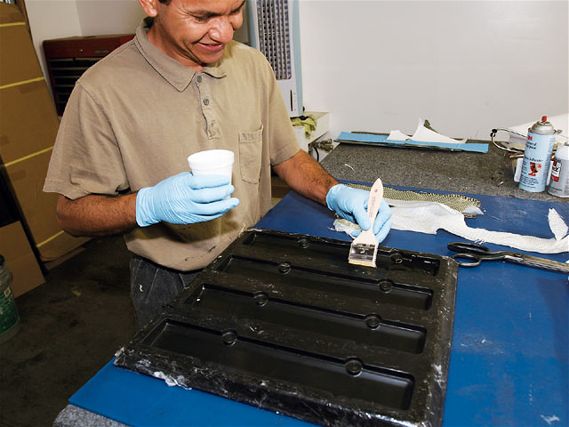
Carbon-fiber stuff is made in several ways. The cheapest and easiest way is called a wet layup. This is simply laying the carbon-fiber cloth in a mold and then saturating it with liquid resin. Additional layers of carbon or fiberglass are laid on top of the first layer so that each layer gets saturated with more resin. Typically inexpensive carbon parts have only the top layer that you can see made of carbon. The under layers that give it stiffness are made of cheaper and easier-to-form fiberglass. The best, strongest and lightest fiberglass to use for this is cloth, but sometimes fiberglass batting or chopped fibers are used. Batting is often preferred since it is thick and fluffy, which adds a lot of thickness in one labor step. Chopped fibers can be shot out of a gun to build up thickness and make parts quickly. Batting and chopped fiberglass is heavier and much weaker than fiberglass cloth. Although using fiberglass seems like its cheapening the part, good parts that exploit the superior strength of carbon fiber can still be made this way plus it does make large parts like a hood more affordable.
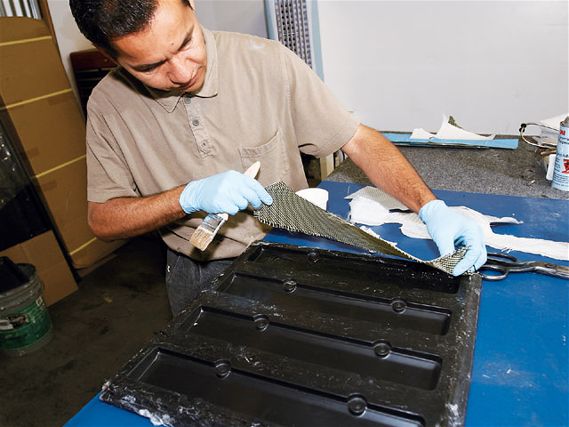
When the needed thickness of the layup for strength and stiffness is reached, the excess resin is squeegeed off and the part is set aside to cure. Sometimes a layer of gel coat is first added to the mold before the carbon cloth to assure a smooth top layer finish. There is nothing wrong with wet layups and many good parts are built this way. The advantage of wet layups is that they can have a nice glossy surface finish. The disadvantages of wet layups are that they weigh more because it is impossible to squeegee all of the excess resin out. There is less compaction and interlocking of fibers between layers of material and there are more voids within the material, making a wet layup less than optimally strong. Wet layups are the fastest, easiest and cheapest way to build a part.
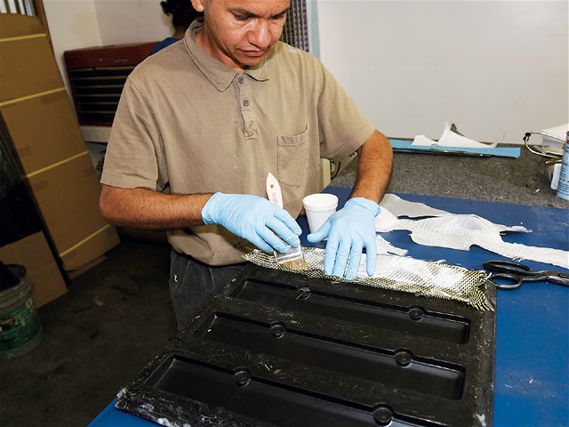
Vacuum bagging is the next way to build a part. The wet layup in the mold is covered with a layer of smooth perforated plastic called a peel ply. The peel ply is covered with a fluffy batting material called a breather. Then the whole thing is placed into a strong plastic bag and the air is sucked out of it with a vacuum pump. The hard vacuum compresses the layup, compacting it thoroughly. The excess resin is squeezed out of the pores of the peel ply and soaked up by the breather. When the layup is cured, it is removed from the plastic bag and the breather and peel ply are removed. This method is called vacuum bagging or vacuum infusion. Vacuum bagged parts offer superior strength due to their better compaction and lighter weight because excess resin is completely squeezed out. Of course vacuum bagging is more labor-intensive and thus more expensive. Vacuum bagged parts can still have some fiberglass layers to them.
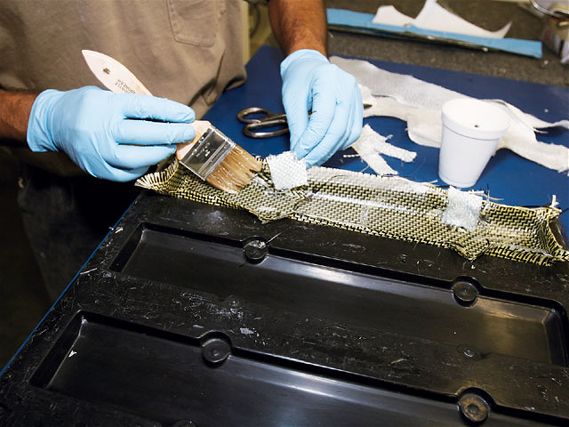
Finally there are parts made of prepreg. Prepreg is carbon cloth that is precisely pre-saturated at the factory with a high-grade of aerospace epoxy. The percentage of epoxy in the fabric is controlled precisely and has a lot to do with the final properties of the cured material. A higher percentage of resin gives a smoother surface but weighs more while a lesser percentage is lighter but has the dull porous look that some people call dry-carbon. Prepreg sheet is laid in the mold with the number of plies giving the desired thickness. Like vacuum bagging it is covered with peel ply and a breather and then placed in a plastic bag with the air sucked out. The major difference is that prepreg must be cured in an oven therefore the peel ply, breather and plastic bag have to be high temperature rated materials and the oven has to have vacuum fittings in it. To get the highest levels of compaction and to get rid of the greatest amount of excess resin, the prepreg is baked in a pressurized oven called an autoclave. This is the most expensive way to manufacture carbon parts but it produces the lightest and strongest carbon parts possible making them the best performing carbon parts. Unfortunately, due to cost in manufacturing, few parts in the performance aftermarket are made this way.
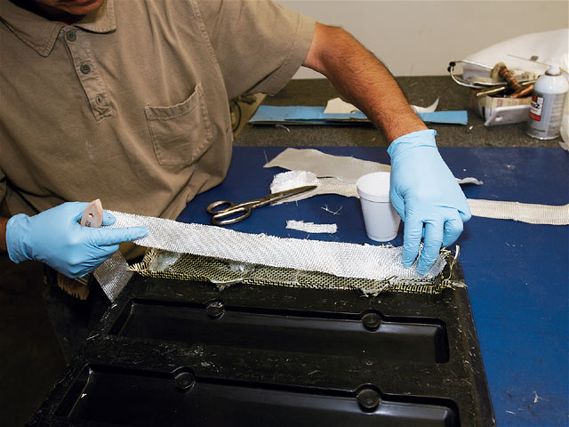
Until recently vacuum bagged prepreg parts have been the stuff that F1, IRL, Champ Car and WRC cars use. The lowly turner crowd mostly had to make do with mass-produced wet layup parts. Recently we had a chance to tour the carbon production facilities of Password:JDM. Password:JDM through economy of scale has found ways to mass-produce prepreg vacuum compacted dry-carbon parts and sell them for reasonable prices. Let us show you how some of these parts are made. All of Password:JDM's composite parts are currently being made through this process and you will be hard-pressed to find higher quality carbon parts.