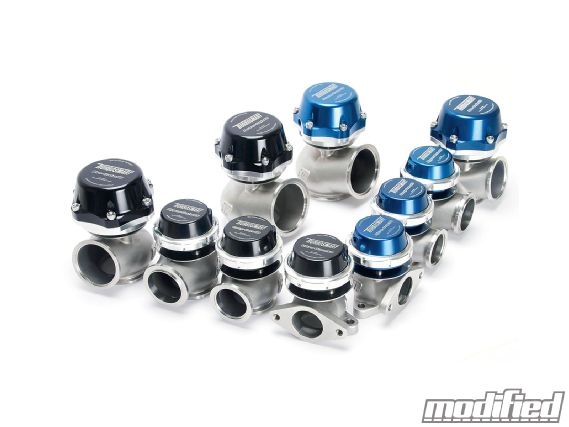
Send your letters to PlanetDave@me.com
It's been a while since I've tackled a subject related to forced induction, and with boost pressure taking center stage in the magazine this year (expect to see a number of our project cars turn up the boost, plus we've got a new project in the works that's going to be making some serious turbocharged jam), now seems like an opportune time to look a little closer at one of the most important components of any turbocharger system: the wastegate(s).
For some deeper insight into the function of wastegates and the challenges associated with designing and producing wastegates robust enough to handle high horsepower and big boost builds, I've turned to industry leader Turbosmart and its U.S. General Manager, Marty Staggs. Marty and the entire team at Turbosmart are real go-fast enthusiasts like you and me, but their passion for turbocharger control systems runs so deep that they now employ some of the most talented engineers in the business, use the best FEA and CFD computer design software available, work with state-of the art multi-axis CNC machinery, and use specific alloys and materials to produce the bulletproof wastegates they're so widely respected for. Keep in mind, some of the fastest and most powerful time attack cars in the world run Turbosmart products, including FXMD's Buttonwillow record-holding Acura NSX, which uses Turbosmart wastegates as well as blow-off valves, fuel pressure regulators, and silicone hoses.
Before we dig deep into the world of wastegate engineering (some of which will come in Part 2 in our next issue), let's quickly review what a wastegate's job is and how it accomplishes said job. As Marty explained, "A wastegate is a valve that controls the flow of exhaust gas from an engine to the turbocharger. It is an exhaust gas regulator. By controlling the flow of exhaust gas to the turbine of the turbocharger, the wastegate can control the boost pressure provided by the turbocharger to the engine. So basically, by throttling the exhaust gas flow to the turbo, we can regulate the shaft speed of the turbo and the byproduct of this shaft speed control, boost control."
Physically, a wastegate consists of an inlet port, an outlet port, a valve, and a pressure actuator that's linked to manifold pressure. As most of you probably know, a wastegate is typically held shut by a spring inside the actuator canister. When the spring's pressure limit is exceeded, the actuator progressively opens the wastegate, allowing exhaust gases to bypass the turbo and in the process regulating boost pressure to the set level. Sounds simple enough, but given that the wastegate is one of your engine's key defenses against overboosting (and the big kaboom that often follows), the importance of a properly engineered wastegate simply cannot be overstated.
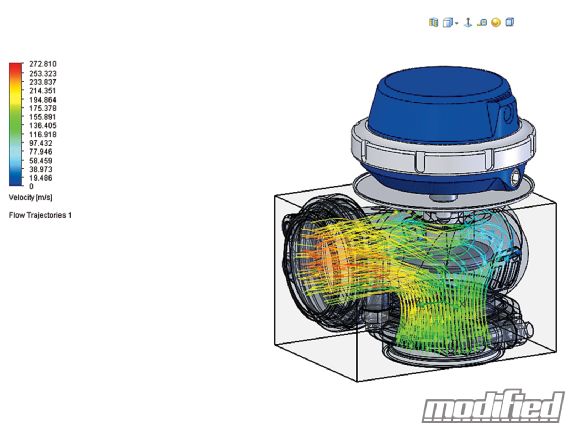
A big part of the challenge faced by wastegate manufacturers is controlling extremely hot exhaust gas (often over 1,000 F), a job that understandably requires some very high-quality materials and clever engineering. According to Marty, Turbosmart's process begins with computer-aided design and CFD analysis, with the goals being maximum flow, control, and durability: "Once a wastegate is designed and modeled, it undergoes various computer software simulations to analyze loads and material stress, heat handling characteristics, and flow capabilities. The model can then be altered to address any areas needed in order to achieve the goals of the design. The simulations are then rerun until the model is acceptable."
Once a new wastegate design has completed this process, prototypes are manufactured to conduct physical testing and validation. As Marty explained, "This is very easily accomplished at Turbosmart, due to keeping all engineering, manufacturing, and assembly in-house. This is something we are very proud of, since it helps us ensure a very high-quality product. Once the prototypes are made, physical testing begins. The wastegates are subjected to cycle testing to ensure consistent and smooth valve travel while also testing critical areas subject to potential wear. The prototype is then heat and flow tested to validate the information provided in our simulations, and then it is finally installed on various test vehicles for control and durability testing."
Once a new design has proved itself on the street and at the racetrack, Turbosmart reconvenes to evaluate the gate for any other areas where they can improve upon it. According to Marty, "New designs are not approved for production until we are satisfied that our team has done all that they can to produce a very high-quality product that will provide real benefits to you, our end user."
One area of design Turbosmart is especially obsessed with is the overall size and weight of its wastegates. As I noted earlier, Turbosmart's employees are racers themselves (everything from drag racing to rallying and road racing/time attack), so these guys know all too well the importance of fitting the right sized gates into the tight engine compartments of the sport compact cars we love so much, keeping their mass to a minimum in the process. They also learn a lot from their extensive motorsports sponsorship programs, working with top tarmac racing teams as well as aircraft and watercraft racers. Turbos work well in the air and on the water, too? Who knew?
But in all seriousness, Turbosmart is understandably proud of the fact that its wastegates are among the lightest, highest-flowing, and most compact on the market today. As Marty explained, "This allows our wastegates to be installed in the ideal location for good control with the added benefit of weight reduction against the competing brands. In many cases, Turbosmart wastegates are up to half the weight of competing brands of a similar size. There is also the added benefit of manifolds being less prone to cracking due to their lighter weight."
Now that I have a better understanding of the design and manufacturing considerations that go into building a world-class wastegate, a lot of new questions come to mind. How, for example, do we select the proper wastegate size and installation location? Is this based strictly on turbo sizing and exhaust gas flow characteristics, or do other factors come into play? Is bigger always better, assuming we've got the space for it? And what about the whole internal versus external wastegate debate? Is one approach "better" than the other, or is it more of a case of choosing the right type of gate for the system being built?
These, and likely a number of other questions my fever-addled brain hasn't yet imagined (OMG flu season GTFO already!), will be discussed next issue, again under the skilled guidance of our turbo control Sherpa, Mr. Marty Staggs at Turbosmart USA. And in the meantime, if you have any turbo-related questions, don't be afraid to shoot me an email or hit Turbosmart USA up on its website. These guys have an excellent tech section online and always make themselves accessible to their customers online or on that low-tech device called the telephone.