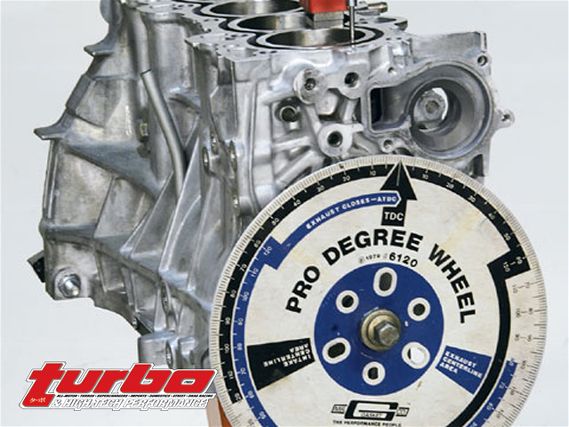
I always got along fine in math class. It could have been because I thought I could apply what I learned to the stuff I did everyday. Whether it was junior high geometry or college calculus, I found it all to be undeniably useful. How often do you apply the skills you honed in second semester French? Not that I ever took French though, but if I did, I doubt I'd use it much. And unless you've ever been grilled by Alex Trebek, when was the last time you actually needed to know who killed Macbeth?
You: Shakespeare for $500, Alex.
Alex: I killed Macbeth.
You: Who is Macduff?
Alex: Correct!)
But we all use math; and not just math professors, but also everyone from accountants to carpenters, scientists to automotive engineers - even magazine editors. Take any component of the modern day automobile and no doubt there's some form of number crunching going on. Geometry in particular plays a vital role in regards to engine block mechanics, top-end configurations, suspension characteristics, and body and chassis aerodynamics. Differential calculus even has its place when trying to sort out the intricacies of engine internals. Don't worry though, we're not going there this time. For now we'll check out bottom-end geometry. There are several useful algebraic formulas that, if applied properly, can save you from your new stroker crank shoving those forged pistons into your valves - or ending up with an unusable rod/stroke ratio that won't let you rev past five grand on the dyno.
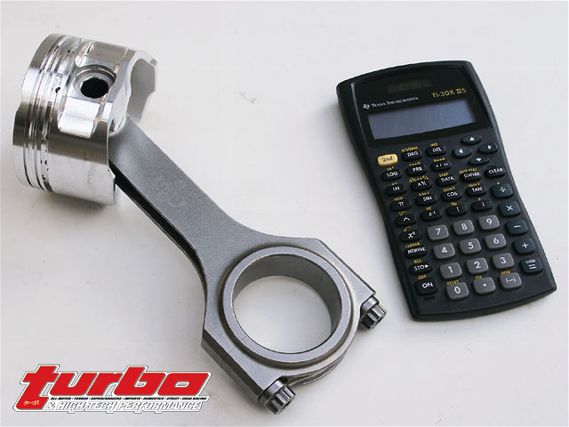
Bore, Stroke And Displacement
Comprehending the basics of engine size is pretty easy. It's usually measured in terms of liters, cubic centimeters or cubic inches, and it's often mistaken for one's sense of manhood. You only need to refer back to the no-replacement-for-displacement motto of the muscle car era to know this. Aside from the fact that there are clear replacements for displacement nowadays (we like to call them turbochargers), it's still helpful to understand the dynamics of engine displacement - for example, how it's calculated, which is what we'll look at here.
At the risk of going back to the basics, a definition of bore, stroke and displacement should be mentioned. An engine's bore size is simply the diameter of its cylinders, and can be expressed in any quantifiable value of distance, but is usually measured in inches or millimeters. Stroke is the distance the piston travels from top dead center (TDC) to bottom dead center (BDC) or vice versa and is measured with the same units as bore. You could also say it's the overall distance the connecting rod journal of the crankshaft causes the piston to move when rotated halfway. You may be wondering why you'd ever want to change an engine's stroke value. For one, larger strokes increase the crankshaft's leverage, which means you have the potential for more torque. But smaller stroke crankshafts take better to high rpms and are generally easier on the connecting rods. This can be more confusing though when you take into consideration rod lengths, and it almost always stirs up controversy as to which method works best.
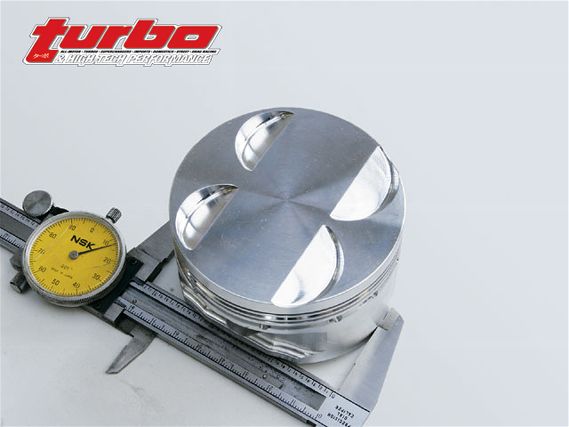
Engine displacement, then, is the volume within an engine's cylinders that's swept by the pistons as they move from TDC to BDC, or vice versa. It's directly determined by how far it sweeps - the stroke - and the diameter of the cylinder swept - the bore. To figure out engine displacement, you've got to know the engine's bore and stroke. You also have to keep all of your units of measurement the same. Meaning, if you're going to measure bore in millimeters, you've got to measure stroke in millimeters also. The rest is easy. If you plan on keeping your bottom end relatively stock, you'll find this engine displacement calculation we're about to give you somewhat useless as you could just open up your service manual for the same answer. But if you like playing with your calculator, or plan on modifying bore diameters, crankshaft strokes or connecting rod lengths, you should know this stuff, or at least have it written down somewhere. It can save you from ending up with pistons that don't quite make their way up the cylinder or from getting kicked off the track on race day because you signed yourself up in the wrong displacement category. (fig. 1)
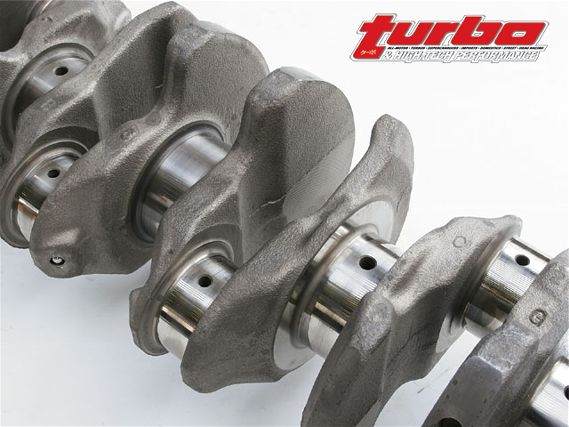
Rod Length, Rod/Stroke Ratios And Deck Height
It's rather obvious what we're talking about when we throw out the term "rod length." But what might not be so obvious is the right way to measure a connecting rod's length, which should be read from the center of the small end to the center of the big end. Like bore and stroke, this is usually expressed in inches or millimeters. An engine's connecting rod length won't tell you a whole lot by itself, but if you also know the stroke value you can come up with a pretty powerful figure - the rod/stroke ratio. An engine's rod/stroke ratio is its connecting rod length divided by its stroke and is expressed in ratio form like 1.68:1 or something like that. Generally speaking, a higher ratio is better than a lower one. You should also know that a rod's length is proportional to its angularity within the cylinder, which means as rod length increases, the side load of the piston against the cylinder wall decreases - a good thing. Engines with low rod/stroke ratios - short rods or large strokes confined to low deck heights - are prone to premature piston skirt or cylinder wall wear because of their harsh angle and often increased piston speeds. Engines with higher rod/stroke ratios are generally high-rpm friendly.
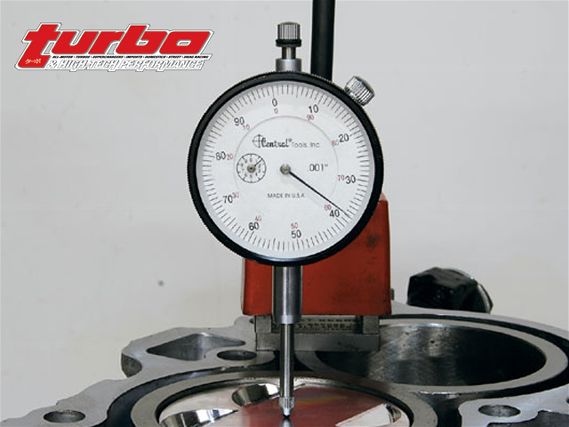
There are two ways to increase an engine's rod/stroke ratio: you can either put in a longer connecting rod or reduce crankshaft stroke through the offset grinding process. A special piston with a relocated pin is required with the first option since the longer rod will otherwise poke the piston out of the block, while the second option requires a custom or reworked crankshaft and rods to fit if piston pin location remains equal. Of course both methods could be combined for an even higher rod/stroke ratio. We should mention that higher is not always better and for some engines there is a point of diminishing returns when it comes to rod/stroke ratios. Other factors must be considered like camshaft(s), the longer piston dwell time at TDC in relation to the flame front, and whether or not the engine is able to even take advantage of the higher-rpm capabilities of a high rod/stroke ratio design. But we digress, as this is going a bit beyond the scope of this simple math lesson. (fig. 2)
Of course connecting rod lengths and rod/stroke ratios must all coexist within the confines of the engine block, meaning that the deck height of the block itself will ultimately determine how long of a rod will fit. The deck height is the distance of the center of the crankshaft's main journal to the surface of the block itself. Sure there are deck extension plates that increase overall deck height, essentially allowing for a longer connecting rod to fit, but more often than not there will be clearance issues inside the block due to the relocated crankshaft rod journals. Certain engines won't allow for much of a stroke increase without notching something inside the crankcase so the crank can spin. Fortunately there's a calculation we can use to see what will fit, at least deck height-wise. (fig. 3)
Piston Speed
Vehicle speed and engine speed are both obvious quantifications we consider every time we turn the ignition over and step on the gas. But piston speed is something just as important, and is more often than not forgotten about. It's usually measured in feet per minute and is the rate at which the piston travels up and down the bore. But the rate changes, as you might expect, alongside rpm changes. At high rpm, the piston can reach speeds over 100 mph as it nears the center of the cylinder and then slow down to a near stop at the top or bottom of its stroke. It's not hard to see the abuse both the rods and pistons undergo from this extreme acceleration/deceleration process. The strains imposed by these excessive speeds can snap connecting rods and crack piston skirts. Another not so serious side effect is that power can be lost due to the piston outrunning the flame front. Piston speed is related to crankshaft stroke, so being able to calculate it can potentially help you steer clear of a dangerous situation before swapping in that stroker crank on your next buildup. (fig. 4)
bore = /displacement / (pi/4 x stroke x cylinder count)
stroke = displacement / (pi/4 x bore x cylinder count)
(The calculation pi/4 is part of the formula for finding cylindrical volumes. Got a problem with it? Take it up with Euclid.) CONVERSION FACTORSinches to millimeters multiply by 25.40millimeters to inches multiply by .03937cubic centimeters to cubic inches multiply by .0610 cubic inches to cubic centimeters multiply by 16.387