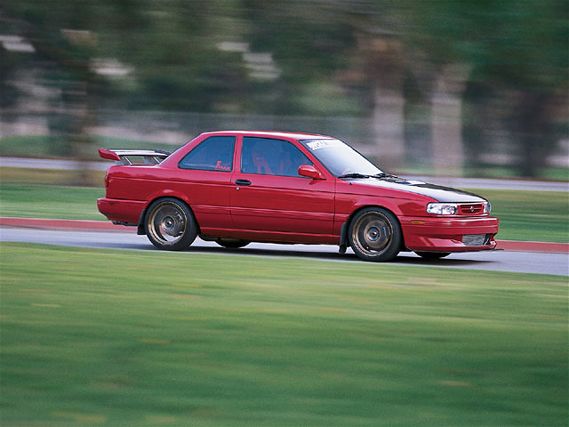
In our last edition of Project SE-R Revisited, we got our car running again with a turbo kit in place. The base Turbonetics turbo kit produced gobs of power, making the car a terror on the street, even with a paltry 10-psi of boost.
Getting the car boosted was one part of our story; in this installment, we're going to probe the limit of what can be done with bolt-ons to a stock SR20DE.
As we have said many times in this series, it's a little-known fact the SR20DE was designed from a clean sheet of paper as a factory turbo engine and is one of the strongest four-cylinder compact car engines you can buy. How tough is the stock SR? We'll find out. We're going to add some additional bolt-ons to enhance our turbo kit, turn up the wick on the dyno and see what she will do.
To ensure we have enough exhaust flow for our heavy breathing turbo engine, we constructed a custom 3-inch diameter, stainless-steel exhaust system using mufflers and components from Magnaflow. Since no 3-inch system was made for this car, we had to build our own. We used a Magnaflow polished 304 stainless 3-inch ID straight-through perforated core muffler and pre-silencer for maximum flow. Despite the large pipe diameter and straight-through design, the Magnaflow mufflers were relatively quiet. Their polished exterior and polished 4-inch diameter tip dressed up the look of our car as well.
We also obtained an assortment of 3-inch 304 stainless mandrel bends and stainless hangers so we could construct a rust-free, all-stainless system. We wanted to keep a cat in the car so we would not be considered gross emitters of pollutants. We also used a Magnaflow 3-inch inlet and outlet high-flow cat, making it quickly detachable from our exhaust system with Turbonetics V-Band quick-release clamps. When we go to the track, we loosen two bolts to drop the cat and either run uncorked or put in a 3-inch bypass pipe.
Wayne Zotti, owner of Speedway Muffler, and Mike Saiki of Motivational Engineering, fabricated our Magnaflow system. They cut sections out of the mandrel bends and tacked them in place with a MIG welder before seam-welding the parts with a TIG welder using stainless welding rods to match our stainless tubing. If you live in the Gardena, Calif., area and need a properly made mandrel-bent system, Speedway does good quality work.
With Magnaflow components, we were able to have our own custom system built with better quality than any system currently available for this car for a reasonable price.
To help get the good stuff into the engine and the bad stuff out, we installed a set of JWT's S3 camshafts. The S3 is a mild street grind designed to use the stock valve springs. JWT uses sophisticated computer modeling and harmonic analysis to develop a lobe profile that both maximizes the area under the lift curve and ensures valve train stability at high rpm.
With a fairly short duration and high lift, we figured these cams would be fine for a turbo engine. The S3s are ground on new billets with a great deal of precision. Finger follower valvetrains with hydraulic lash adjusters like what the SR20 is equipped with need to control camshaft base circle run out to several 10-thousandths of an inch to avoid problems with rough idle and low cranking compression. Too much run out causes the lash adjuster to pump up, holding the valves slightly off the seat and causing problems. JWT takes great pains to ensure this precision in the grinding of its camshafts.
A turbo lives and dies in the power wars by the amount of boost pressure the engine is force-fed, and, for us to up the ante, we needed a boost controller.
Simple is better in this case, so we selected a GReddy PRofec-B. The PRofec B was selected because of its ability to not only control boost easily from the driver's seat, but to improve throttle response and to reduce turbo lag as well. A properly set up electronic boost control can do this because it can pinch off the air reference signal to the wastegate with a duty cycle stepper motor valve.
When the driver's set boost level is reached, the boost controller will send all of the pressure signal to the wastegate, blowing it open quickly. Normally, when the wastegate boost reference line is merely attached to the manifold, the wastegate opens slowly, well before the set boost point to prevent boost overshoot or overboosting. Overshoot is prevented, but because the wastegate valve is opening slowly before the actual set point, boost builds more slowly as well. Manual bleed type valves like the infamous aquarium valve can raise the boost level but also make boost response sluggish for the same reasons.
The PRofec also can be set to control the boost control pressure to both sides of an external wastegate's diaphragm. This allows the use of a lightweight spring in the wastegate, allowing a large latitude of boost adjustment. We have a 6-psi spring in our wastegate, but due to the PRofec's ability to put control pressure to both sides of the diaphragm, we can adjust our boost from 6 psi all the way to 22 psi from the cockpit. The PRofec-B also has the unique feature of being able to adjust its response speed to the wastegate's response time. This feature allows the user to tune the Profec for maximum boost response speed without boost overshoot. Because the Turbonetics Racegate is a responsive external wastegate with a big poppet valve, we set the PRofec for its quickest response level for the most aggressive possible boost curve.
The PRofec-B also has a cool remote trigger feature. This is a radio frequency controller you can attach to your steering wheel for easy reach and allows you to remotely toggle between high and low boost. This is very handy with a high-powered FWD car; you can launch at low boost and when in higher gears, easily switch to high boost at the touch of a handy button. With the radio frequency controller, there are no complicated wires to install. Just strap it on and it's ready to go.
To monitor the boost pressure, we installed a JWT boost gauge using the gauge pod for a Twin Turbo Z. Surprisingly, the pod almost fit. We heated it with a heat gun to soften the plastic slightly so we could mold it into shape to fit our Sentra a little better. The JWT gauge can read up to 30 psi, which is more than we ever anticipate running.
California's new 91-octane gas is bad news for turbo lovers. The 91-octane fuel is like light beer, and turbos don't seem to like it much. With the poor quality gas, most of us in this state have had to lower our boost pressures by several pounds or retune our engine management systems to tolerate the fuel at the cost of much lower performance.
To help us with our fuel dilemma, especially since we are running a higher compression stock engine, we looked for new ways to suppress detonation without compromise.
Our savior in this case was an Aquamist competition water injection system. Aquamist water injection systems have been used in FIA rally cars for years, enabling lots of boost pressure and advanced spark with reliability.
The Aquamist system uses a sophisticated solid-state piston-type pump that pumps the water at 130 psi. At this high pressure, there is little likelihood boost pressure can reduce water flow significantly, a problem that plagues other water injection systems which only run a typical 10 to 20 psi. If you only have a 10 psi water pump and are running 15 psi of boost pressure, the resulting positive pressure differential ensures you won't get much water out of the system!
Water injection relies on water's naturally high specific heat, which means it requires a lot of heat to change liquid water-to-water vapor (steam). The high specific heat is one of the reasons water is an excellent coolant. When injected into an engine, water does several things. When it is first injected, some of the water vaporizes, absorbing heat from the incoming intake stream. This helps cool the hot intake charge in much the same way N2O injected into the intake of a nitrous-equipped car does. Once inside the combustion chamber, the water is fully vaporized into steam. This vaporization absorbs a tremendous amount of heat from the combustion reaction, helping cool the engine internally to prevent hot spots that can be areas of self-ignition where detonation propagates. The heat absorbed from the water's phase change also acts to buffer the combustion event, slowing it down. Thus the water helps regular pump gas behave much like slow, controlled-burn, high-octane race gas.
The super-heated steam also acts like a powerful steam cleaner inside of the engine, removing compression rising, hot-spot propagating carbon deposits from inside the combustion chamber. As water does absorb power-producing heat, it does not produce quite the same horsepower per lb. of boost as race gas does, but it does allow quite a bit of additional boost. The water also goes a long way to eliminate engine-damaging detonation.
The Aquamist water injection system uses a unique proprietary atomizer nozzle to introduce the water to the intake air stream. The nozzle produces a range of droplet sizes from a fine fog to a coarse mist. This helps the water work more efficiently. The fine water fog vaporizes almost immediately, helping reduce the intake air temperature by about 20 to 30 degrees. The larger droplets don't vaporize until they reach the combustion chamber where they can cool and buffer against combustion. All the droplets are small enough where the even distribution of water throughout the manifold plenum is ensured.
Most modern fuel injected cars have manifolds that are designed to flow dry air only, not a mixture of liquid and air so the maintenance of correct water droplet size is critical for even cylinder-to-cylinder water distribution.
The common, old-school water injection system typically available makes no attempt to atomize the water. As a result, unequal distribution and over injection of water occurs, creating bogging and other driveabilty problems with still poor suppression of detonation.
The Aquamist system works so well the Euro Ford Sierra Cosworth uses this system as original equipment from the factory. The Aquamist system can be tuned using different sizes of jets ranging from 0.40mm to 1.0 mm. Because the SR20 engine has a relatively high (for a turbocharged engine) compression ratio of 9.5:1 stock and is burning 91-octane unleaded pee water, the large 1.0mm orifice jet with a flow rate of 335cc per minute was selected. Since the SE-R has a large windshield washer reservoir, it was tapped with a pick-up for the high-pressure water pump.
To partially offset the power reducing internal cooling produced by the water, it's possible to run a leaner fuel-air mixture and more ignition advance.
Clark Steppler of JWT integrated the water injection to the Engine Control Computer he reprogrammed for us in the last project installation. Using a microprocessor containing a daughter board interfaced to the ECU to control the water injection pump, Clark programmed the daughter board to turn on the injector pump at a mass airflow meter voltage approximating 8 psi of boost whenever the water injection master arm switch was activated.
When the water pump is activated by the ECU, the ECU automatically switches to a new fuel and spark map after about 120 millisecond delay. This gives the water injection system time to prime before going to the more aggressive fuel and spark maps. The fuel map is leaner, and the spark map has more advance, optimized for water injection.
With the addition of the daughter board, we added the feature of having multiple fuel and spark maps optimized for different modes of operation.
We now have the option of four different maps. Pump gas, race gas, pump gas with water injection and race gas with water injection. These modes are activated simply by two toggle switches, one enabling the water injection function, the other to switch between high and low fuel octane maps. The JWT ECU has a great amount of flexibility for the user.
The water injection system is almost like having a tank full of race gas all the time except without the $5-per-gallon race gas penalty. After all water is cheap, nearly free. For once in the history of hot rodding, something can be done for nearly nothing.
As an interesting side note, water injection also reduces toxic oxide of nitrogen emissions by reducing combustion temperatures. All of this and cleaner air, too.
We think the Aquamist system will help just about any car saddled with fuel octane limitations. The system will be a great aid to any turbo tuner in California.
With the additional detonation-free boost available, a new problem appeared: ignition-related misfire. At the higher, difficult-to-ionize cylinder pressures induced by turbo boost and with the presence of conductive water molecules, the stock ignition system was hard pressed.
Closing the plug gap to 0.020 inches helped to 12 psi, but misfires prevented any higher boost. The stock Nissan ignition is quite powerful in stock form; it doesn't perform well with more than 10 psi of boost and water injection, resulting in misfire.
After experimenting with a few other ignition systems on Project SE-R with mixed results, we substituted a Crane Hi-6 DSR multi-spark CD ignition box for the stock power transistor.
The Crane has the reputation for being one of the most powerful CD-type ignition systems on the market, capable of firing up to 12 sparks for 20 degrees of crank rotation and giving a greater chance of ignition.
Crane provided us with its low-impedance LX92 coil that is optimized for Hi-6 ignition. This combo jolts the plugs with a heart-stopping 510 millijoules of energy per spark and up to 1200 millijoules of energy per sparking sequence.
The Crane ignition also had some other features we liked; the circuitry was all the latest surface-mount technology, surface-mounting electronic components makes a part less susceptible to vibration damage.
The Hi-6's internals were also completely potted with polyurethane to further protect them from heat, dirt, vibration and moisture. The Hi-6 also has a cool self-diagnosis feature where a blinking LED can tell you if anything is wrong with the system. Not having to guess makes troubleshooting a snap.
We used this feature to trace a pickup problem that turned out to be a bad wire. The feature saved us several hours of aggravation.
Unlike many other aftermarket ignitions, the Crane ignition didn't require an adaptor box for our fuel injection and tach to work. We always welcome not having to find the place to put yet another control box under the hood of our cars.We used some other cool features on the Hi-6 DSR including a two-step rev limiter. We connected the rev limiter switch to the clutch pedal so we could use the lower pre-set rev limit as a launch control.
When the clutch is depressed, you can simply mash the gas pedal to the floor and the Hi-6 will hold the engine to your pre-set launch rpm. With the throttle wide open, the turbo starts to spool, building a few pounds of boost along the way. When the clutch is released, the rev limit reverts to the normal rev limit of the engine. We also used Crane's TRC-2 timing controller as an anti-lag system. When the clutch is depressed, the spark is retarded up to an adjustable 20 degrees. This increases the exhaust gas temperature and helps spool the turbo or keeps the turbo spooled during shifts. The engine pops and backfires, but that's normal.
In fact, if you listen, most modern turbocharged rally, Indy and hill climb cars will also do this as they use similar systems to help improve response and reduce turbo lag. Our Crane ignition system will also allow safe full throttle upshifts with very little turbo lag. When experimenting with other cars, we found this can take as much as two to three tenths off of the quarter-mile time.
With the Hi-6 and the LX92 coil using the Aquamist water injection, 17 psi was reached on a cool day on 91-octane pump gas before detonation became a problem. The boost could still be turned higher because no misfire was present, but since the engine was stock, we didn't press our luck any further with pump gas. The normal daily running boost pressure was reduced to 14 psi.
To see just how much power Project SE-R was really producing, we took a short trip to R&D Dyno, the tuning shop of the stars, to see what our little car could do. On 91-octane pump gas, at 17 psi the car spun the Dynojet rollers to the tune of 304.4 hp and 290 lb/ft of torque-not bad for a stock motor. Three hundred hp in a 2,400-pound car is a lot of fun, almost too much fun. Almost any street machine you come up against is no match for our little giant killer.
To see what our little SR20DE could put out with a little help from some decent fuel, we added a tank full of VP C16 racing fuel to the mix and turned the wick up on our PRofec-B to 22 psi. Our bone-stock SR20DE responded by cranking out 379.7 hp and 352.7 lbs/ft of torque. This from a bolt-on street turbo kit on a basically stock engine.
This is enough power to easily punt Project SE-R into the 12s with slicks in full street trim. Project SE-R: The terror of the road course.
Stay tuned. In the next installments of Project SE-Revisited, we'll put together braking and suspension systems. With this much power, these areas of the car are woefully lacking and need serious work to keep the car a well-balanced machine.