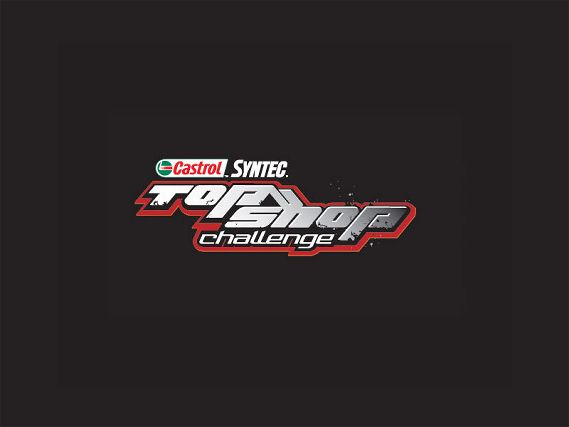
It's time to wrap up our Castrol Syntec Top Shop Challenge VQ35DE engine build. The opportunity to work with Cosworth Engineering has given us a lot of insight as to what it takes to design and build a race engine, but with the competition just around the corner, it's time to wrap it up. Now that the bottom end is built and the Cosworth CNC heads are bolted down, all that's left is to look at the gas exchange process, or sucking and blowing as we call it. This should be the part that's most interesting to tuners since manifolds, cams, and how they provide the most efficient and useful gas flow through the combustion chamber is what we have some margin of control over. Since few of us are engine builders, making the most of the bottom end is all that we're left with. Unfortunately it's a black art of sorts. But instead of just telling you to buy this part and bolt it on because it makes power, we want to talk about what the manufacturer has to account for in order to make a part that makes power. Knowing more about the process will help you figure out the difference between duds and truly engineered pieces.
In our case, much like any aftermarket product, there are certain constraints when it comes to cam and manifold design. The displacement, compression, fuel octane, valve sizing and, most likely, peak RPM is already set. This actually makes life easier when designing parts instead of starting from a blank sheet. We will now explore the "black arts" in the detail-design process that are necessary in order to maximize peak horsepower and the area under the power curve while running on 100-octane fuel. Since we're keeping it naturally aspirated, enhancing the gas exchange process is crucial to our success.
The rules of the valvetrain game
One of the most important systems in the gas exchange process is the valvetrain system. As it is the primary passageway in and out of the combustion chamber, properly designing valve operating characteristics, or cam profile, is essential to a high-performance engine. Three important characteristics describe valve dynamics: valve lift, valve event duration, and valve event phasing. Theoretically, we would like to open the valve as far as possible instantaneously and at different points in the combustion process, depending upon engine speed and load. But that's a pipe dream since most modern engines are of an interference design where the valves can hit the piston near the top of its stroke. Physics also makes life hard because there are mechanical limitations to how fast we can open the valves. Instantaneously opening a valve requires infinite acceleration and thus infinite force!
So the first rule is that we must face reality and have smooth, gentle valve motion. Since the engine is a complex, dynamic system, the physics driving engine characteristics change based on engine speed and loading. Since we are more interested in power than fuel economy, the discussion from here on out will focus only on wide-open throttle or full-load operation.
Valve Lift
Our first foray into the black art of cam design concerns valve lift. Keeping as many things constant as possible - valve event duration, maximum brake torque (MBT) timing, A/F ratio, etc. - we see that during low lift, there is less flow separation from the valve and valve seat walls (See Figure 1). Since the air/fuel mixture "sticks" to the walls and valve shape, it takes up most of the flow area and has a high discharge coefficient (discharge coefficient is the ratio of actual flow to theoretical flow). Also, since the flow is somewhat restricted by the small flow area available, the air/fuel mixture moves with a lower velocity through the port reducing frictional losses against the walls of the engine. Furthermore, as the air/fuel mixture squeezes by the small space between the valve and the valve seat, the gas velocity increases, promoting good mixing in the cylinder and improving torque.
On the other hand, at high lift, we have large flow separation from the valve and valve seat walls leading to a reduced flow area along with dead recirculation zones that do not contribute to fluid flow (aka, the combustion chamber). As the restriction to fluid flow is now minimized, the air/fuel mixture now has a high velocity in the port, leading to higher friction losses against the wall and the potential for choked flow. Compared to low lifts, the mixture velocity past the valve at high lifts is relatively smaller, leading to non-ideal mixing and a reduction in torque. So then why would anyone want to run higher valve lifts? Let's throw RPM into the previous discussion. At low RPMs, increased valve lift improves performance (torque) since the intake system and port are not limiting air flow. Although the discharge coefficient might drop from a lower lift specification, the increase in theoretical mass flow more than compensates for this.
At high RPM, larger lifts can be a detriment to performance. The intake system and port now become the bottleneck due to high gas velocities increasing friction and leading to possibilities of recirculation and choked flow around the valve. This is where valve sizing and valve seat profile come into play and exactly why Cosworth's CNC ported cylinder heads use larger intake valves and more valve angles and radii for smoother flow transitions.
Valve Event Duration
Valve event duration for peak power is more straightforward than valve lift. Longer valve event duration is usually sought after as it increases the time for gas exchange and consequently increases the time to open and close the valve. Mechanically, acceleration ramps can be less aggressive, leading to lower forces throughout the valve train. Lower forces are beneficial by increasing durability and reducing mechanical friction, allowing more power to end up at the crankshaft. Keeping things constant, a longer valve event duration at low RPM can lead to decreased performance as the fresh air/fuel mixture can "short circuit" the cylinder and go straight out of the exhaust. A longer valve event duration at high RPM is advantageous as it exploits the inertia of the air/fuel mixture through the "ram-air" effect. This forces more of the fresh air/fuel mixture into the cylinder, increasing power output. Traditionally, this trade off of lumpy long duration cams, reduces bottom end torque in exchange for top end power.
Valve Event Phasing
Intake Valve Opening (IVO) usually occurs 10 to 25 before top dead center (TDC). It should open before TDC so that cylinder pressure does not dip early in the intake stroke. This timing is usually set to optimize full load output. Intake Valve Closing (IVC) is one of the principle factors that determine high RPM breathing. IVC usually occurs 40 to 60 after bottom dead center (BDC) in order to take advantage of ram-air effects. However, at low RPM where the charge has less inertia, IVC can affect torque output by allowing the piston to push air and fuel back into the inlet port.
Exhaust Valve Opening (EVO) usually occurs 50 to 60 before BDC and is a tradeoff between pushing the exhaust gases out in time and extracting the work from the burning gases. For example, with an early Lancer Evolution, the high-pressure exhaust gases take advantage of blow down and then have extra time to rush out of the exhaust valve and equalize with the exhaust back pressure. Thus, when the piston rises back up from BDC, it has to do less work to push the remaining burned gases out. However, reducing the pumping work comes at the expense of extracting work from the burned gases. Exhaust valve closing typically falls between 8 to 20 after TDC. It should occur after TDC so that cylinder pressures do not rise and prevent fresh mixture from coming in. A late EVC favors high power since it ensures a large valve overlap (both valves open at the same time) allowing as much burned gases to exhaust while bringing in fresh air and fuel.
Following the preceding discussion, there is no one set valve timing that is right for an engine. Since engine loads and speeds are constantly changing, valve timing requirements also change. This is why race cars that are tuned for peak power and constant high RPM operation typically struggle at lower engine speeds.
Being a newer engine, the VQ35DE has the additional benefit of using Nissan's Continuously Variable Valve Timing Control System (CVTCS), which will help mitigate the "short circuiting" at low RPM. With CVTCS available on both the intake and exhaust camshafts, continuously changing the valve event phasing during engine operations will allow us to optimize the VQ35DE over a large operating range, increasing the area under the horsepower curve. Valve event phasing will also allow us to compensate for low RPM overlap, valve to valve, and valve to piston clearance issues that come with using high lift and duration cams.
Putting it all together
Designing a cam that meets all the above conditions is the entire challenge in cam design. Cams with high lift provide more flow, but have low RPM limitations, more wear and inertial loads as well as potential valve contact issues. Using longer durations valve events require cam profiles that maximize time at peak lift. These aggressive ramp profiles have more severe inertial loads as well as valve contact issues. Add on top the possibility that cam phasing can potentially be tuned so that the valve might hit the piston during overlap and you have a very complex problem.
Since Cosworth didn't build the motor for just the Castrol Syntec Top Shop Challenge, several different cams were used during development. Ultimately, this motor will be destined for use in the European motorsport market. Cosworth engineers tested a few different profiles and intake and exhaust cam combinations with higher lift and longer durations. Their verdict was that non-staggered intake and exhaust cams with near identical durations worked best for this engine. Our cams will be a prototype set with 300-degrees of duration and a peak lift of 12.0mm on the intake side and 296-degrees and 12.0mm peak lift on the exhaust side. Almost 50 degrees more duration than the stock 256 degree intake and exhaust cams and up to 3mm more peak lift.
Other Valve Train Considerations
Aggressive cams typically require RPM to work better. Wringing out every last bit of horsepower from the VQ35DE will require spinning the motor to higher RPMs (up to about 10,500 RPM). As a consequence of running more valve lift and duration, compounded by a higher RPM ceiling, valvetrain stresses and dynamics will change. This is why the Cosworth CNC head also has lighter weight titanium retainers that reduce inertial loads and improve dynamic response of the valve train. Stiffer dual valve springs are also necessary to prevent valve float at the engine speeds that the original valve train was not designed to operate at. Intake/Exhaust Systems
Assuming the Cosworth cylinder heads are no longer the flow restriction, we have to address other restrictions further up the intake and down the exhaust path. Echoing much of the general trends in engine operation, intake and exhaust system requirements change as the engine operating characteristics change. For peak power optimization, the intake air box, or plenum, must be of considerable size in order to feed all of the cylinders without becoming the bottleneck. Also, smooth transitions and equal length runners help balance the mass of air and fuel that enter and exit each cylinder. In a perfect world, we would have a variable geometry intake and exhaust system to parallel the variable valve system.
For a performance engine, infinitely variable intake and exhaust systems might be overkill; optimizations within the power band will have to suffice. The Cosworth Twin Plenum intake system targets peak power production with a larger plenum volume. To increase intake port flow velocities at low rpm, velocity stacks, or venturies, are used, which will maintain a broad torque curve since they prevent flow separation as air enters the stack.
On the exhaust side, Cosworth stepped out of their norm to design and build this one-off exhaust manifold specifically for this challenge. While Cosworth Engineering has the know-how and technology design to test and build the ideal exhaust manifold, the cost to do that is something only a race budget can warrant. So, instead, their gas flow geeks took a best guess and built a 3-to-1 design that focused on creating equal length primaries that optimized top end power. The first manifold used 35-inch primaries which didn't work quite as well. Ultimately, the manifolds were modified with shorter 31-inch primaries which are near the space limitations of the chassis.
The Verdict
Although Cosworth can model and simulation much of this intake, exhaust and cam tuning, these tools exists only to predict behavior and act as a guideline. Ultimately, everything still requires bench testing in order to validate the design since no simulation can completely predict all the dynamic complexities involved in an engine. If you've been holding your breath all this time to find the final outcome and our VQ power numbers, flip ahead to the special insert in this month's issue. Inside, you'll find the final power numbers of every engine entered and who finished where in competition (all entrants were tested on an engine dyno).
But keep in mind that while other competitors can build one-shot dyno queen motors that make stupid power, our Cosworth VQ would be the only one we'd race on for its useability, as well as durability. In the real world, that really does count for something extra.