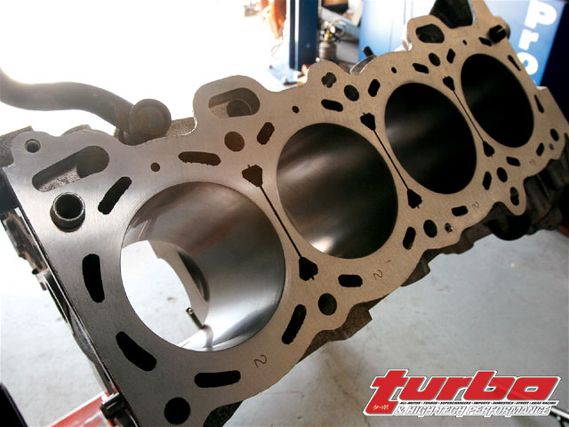
In our last edition of Project Low-Buck SR20DE, we stated our goals of obtaining a decent amount of naturally aspirated horsepower and good track day driveable reliability from an underdog plain jane SR20DE-without breaking the bank. Fulfilling these goals would also create an engine with excellent street driving characteristics. Our engine work will be done on the cheap with a tight budget in mind, but with plenty of attention to minor details that can really help an engine live under the stress of track day pounding-perhaps the most abusive environment that a grassroots enthusiast will subject his engine. Unlike drag racing, a car driven on a road course is pounded to the redline for 20 to 40 minutes at a time. This requires attention to detail for the engine to survive. In our first installment we selected Eagle Rods and SR16VE pistons for our build. We modified the pistons for more piston-to-valve clearance, applied optional thermo barrier, and antiwear and antifriction skirt coating. For the budget-minded drag racers or for pure street use, the stock rods will also work pretty well, being rock-solid safe up to 8,000 rpm. To save a few bucks and still obtain respectable results, you can live without the coatings and piston machining.
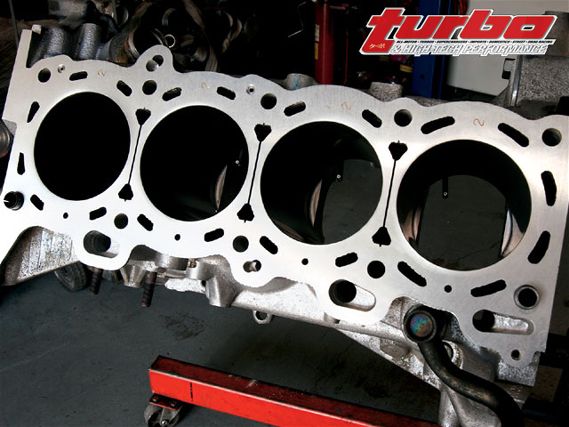
Since we're retaining the standard bore with the SR16VE pistons, we avoided the expensive task of boring the SR block oversize. The SR20 block suffers from severe bore distortion when the head and transmission are bolted in place. The bore can distort as much as 0.0015 inch, an amount that can really affect ring seal or even contribute to piston scuffing. It's important to use a deck torque plate and bolt a transmission bellhousing to an SR block when it's being bored and honed to keep the bore's roundness accurate. Not too many shops in this country can do this sort of work on an SR, and packing and shipping your block to places like Jim Wolf Technology in California or Mazworks in Florida can be very expensive.
Fortunately, in most cases a stock SR exhibits very little bore wear, even in 100,000-plus mile motors. In this case our free core engine was pulled from a friend's NASA SE-R Cup car, where it was raced for two seasons. Although the rings were worn, the bore was in excellent shape. We simply used a ball hone to clean the bore up so new rings could sit easily, and we were done. The Swain coating we applied to our piston actual brought our piston-to-wall clearance in on the middle tight side of stock-perfect. Finally, Technosquare then lightly decked the block, removing about 0.003 inch of material to ensure a flat surface for the head gasket. For optimal sealing, Technosquare used very fine cuts to create a smooth surface that would be compatible with an MLS-type head gasket.
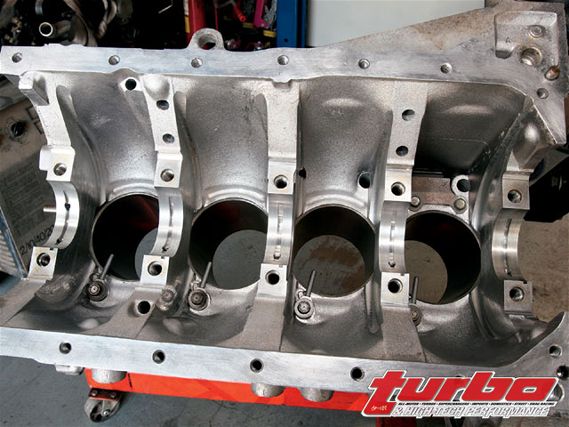
SRs are known to be hard on rod bearings. If the engine's oil is constantly monitored and maintained right at the full mark on the dipstick, no more and no less, usually the bearings are trouble free even under hard use. However, later versions of the SR20, like the SR20VE and some turbo SR20DET engines, have improved oiling for the rod bearings. This is done by adding a groove to the main bearing saddle in the block that intercepts the oil feed hole coupled with the use of SR20DET main bearings, which have additional oil feed holes in the upper bearing shell. This assures that the rod bearing feed holes in the crank receive a good supply of oil for a full 180 degrees of crank rotation.
Jim Wolf Technology performs this modification to SR20 blocks that don't have the groove from the factory using a cutoff wheel and a simple guide jig. This could be duplicated with a little skill and patience. This mod isn't absolutely needed and many a fast SR has been built without it, but it's a good detail to help engine life under hard use.

Next, piston coolers from an SR20DET were installed. Piston coolers are nozzles that shoot oil from the main galley up to the bottom of the piston to help keep them cool under hard use. Aluminum loses much of its strength past 350 degrees and piston coolers help a high-compression engine stay cool under extended wide-open throttle use. Keeping the piston cool can also reduce the chances of an engine experiencing detonation under hard use. The piston coolers have a spring-loaded check valve to make sure that oil pressure isn't lost under low rpm and idle, but open at higher rpm when the oil pump's bypass circuit is activated. The stock SR20 block has bosses for the piston coolers already cast in place. The bosses must be drilled, tapped, and spot faced so the coolers can be installed.
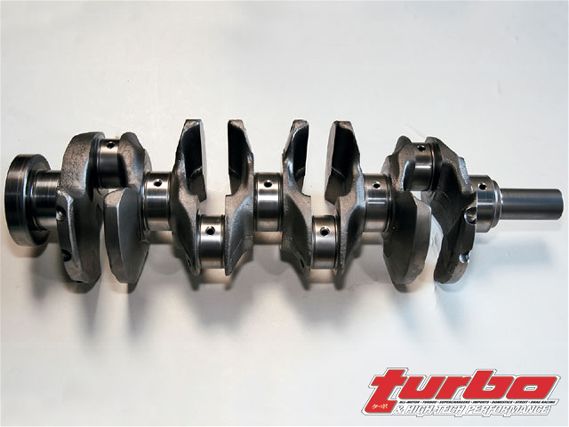
Jim Wolf Technology routinely does this operation and it's pretty simple for any machine shop. Care must be taken to spot fact the bosses enough so the coolers' body clears the crank and the nozzle clears the piston skirt. SR16VE pistons have a notch in the skirt to clear the coolers but if you use some other piston, be careful and check this clearance when assembling the engine. Quite a few people have made this mistake and later wonder why their engines suffer from low oil pressure when the piston skirts shear off the nozzles! Like some of the other mods discussed here, piston coolers aren't absolutely needed for street or drag use but are a nice low-buck touch to help reliability under extreme conditions. The Nissan factory also uses piston coolers in its high-compression naturally aspirated motors, so perhaps there's a good reason for this.
Next, we focused on the crank. Fortunately the stock forged steel, fully counterweighted SR20DE crank is one of the stoutest units in the business and really doesn't require much work at all to sustain the highest power and revs. Usually an SR20 crank has very little journal wear and doesn't require much work for reuse. In most really low-buck applications, it can simply be inspected and reused. Since we anticipate some hard use, however, we sent our crank to Joe Castillo of Castillo's Crankshafts to have the journals polished and balanced, and the counterweights lightened and profiled for less windage drag. That last step isn't really necessary.
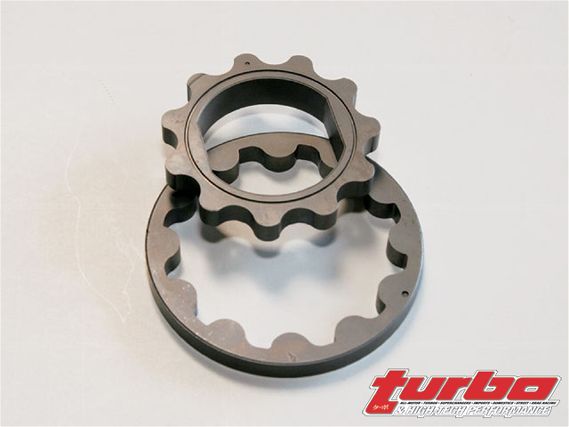
After magnaflux checking our crank for cracks, then inspecting it for other possible damage and straightness, Castillo put our crank on a lathe and profiled the counterweights. This removed a pound of weight and gave the counterweight a more aerodynamic contour. This should help reduce windage power losses in the crankcase, as the crankshaft has to spin in a dense cloud of turbulent air and oil. Since we anticipate a lot of high rpm long-term use, we didn't go crazy with lightening the crank; we simply removed from the counterweights about what was reduced on the pistons and rods.
Castillo then drilled out the oil passage plugs in the crank to facilitate cleaning and tapped the holes so screw-in hex plugs could be used. This is much safer and more secure than the stock pressed-in plugs. The journal oil holes were chamfered to create a reservoir for oil from the main bearing feed to improve oil flow to the rod bearings. Bob weights of the same weight as our rods and pistons were bolted to the crank, and the whole assembly was dynamically balanced. As a final step, all of the crank journals were micro polished to reduce friction and help improve bearing life. Although all of these steps aren't needed in a low-buck engine, they aren't particularly expensive either.
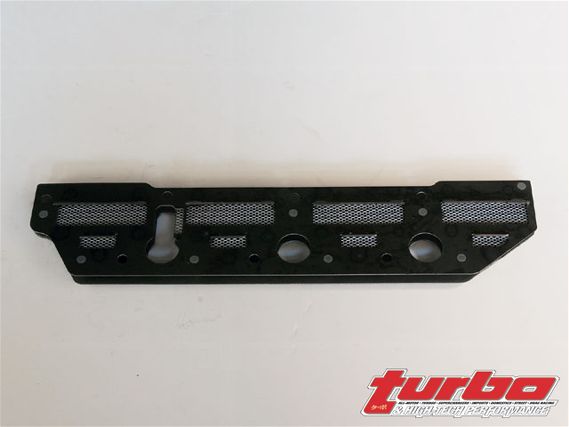
Prior to assembly we sent our crank, rings, oil pump gears, camshafts, cam followers, valvesprings, and block off to be WPC treated. WPC treatment is a Japanese-born process, where metal surfaces are bombarded with a very tiny ceramic shot at extremely high velocities. Special antifriction additives like tin or zinc powder and molybdenum disulphide are added to the mix and embedded into the surface. The result is an extremely smooth, friction-free surface with self-lubrication properties. The shot also compresses the metal on a molecular level near the surface, refining the grain, and creating a zone where it's very difficult for micro fatigue cracks to propagate. In this way WPC works very much like shot-peening for increasing fatigue strength of parts but on a finer scale. When applied to the crank, WPC improves upon the surface finishing of the journals and toughens the fillets of the crank, where most failures occur. On the cylinder walls, WPC reduces friction and the micro dimpled surface helps the rings seat instantly. The dimples hold oil, which helps ring and bore life, and reduces friction as well.
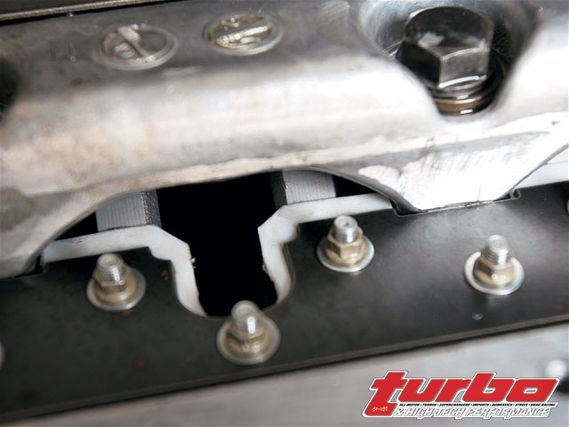
WPC is a little known secret that sees a lot of use in Champ Car, NASCAR, JGTC, and F1, where it's highly effective in reducing friction and improving the life of parts. A drawback is that the process is somewhat expensive and costs around $800 to apply to all of the engine's rubbing parts. While this isn't needed for a budget motor, we've heard very favorable reviews of the process increasing both power and component life from our friends at XS Engineering, Cosworth, and in the professional racing world. When we received our parts back from WPC we were amazed by the silky smoothness that they exhibited. We can hardly wait to see how this process works.
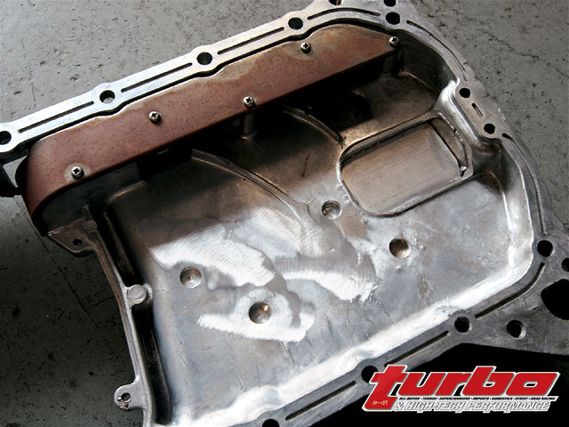
We used Calico-coated Clevite bearings for the rod and main bearings, using SR20DET bearings for the mains to make use of the extra oiling holes and regular SR20 bearings for the connecting rods. Our friends in the world of professional racing had good things to say about the Calico bearings so we decided to give them a try. Clevite bearings are tri-metal, meaning that lead, copper, and zinc are alloyed in various ratios and applied in layers to the steel shell to create a bearing with a wide range of characteristics. This creates a hard bearing for superior load that can still be embedded like a soft bearing to make it a little more forgiving for dirt and contaminates. The bearings then have Calicos CT-1 coating applied in a 0.0004-inch thick layer to provide additional protection and friction reduction. The CT-1 dry-film lubricant coating is technically engineered to withstand extreme performance pressure. CT-1 coated engine bearings are claimed to increase horsepower and efficiency while extending bearing life.
Strangely enough, most Nissan engine bearings were Clevite but in an effort to become a more green company by eliminating the use of lead, Nissan discontinued their use in the early '90s. The new bearings, with less potential for pollution, are vastly inferior for performance, especially in regards to temperature resistance. The eco-friendly Nissan bearings begin to deteriorate with oil temperatures as low as 280 degrees. It's common for an SR driving at the track on a hot day to see sump temps in the 300-degree range!
With the Calico-coated bearings, our bearing clearance worked out to be slightly at the tight side of the middle for factory spec-perfect and actually pretty normal for a typical slow-wearing used SR motor.
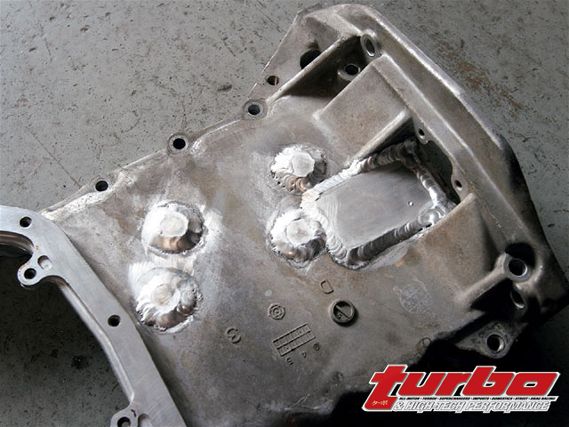
Track-driven SRs abuse their bearings if the oil level is allowed to drop one bit below the full mark on the dipstick, it's common to see the oil pressure fluctuate in hard corners with a car modified with good suspension and sticky R-compound tires. This makes it very temping for an SR owner to slightly overfill the crankcase to reduce the chances of this happening. This is also bad. A crankcase that's even slightly overfilled helps create a maelstrom of windage around the spinning crankshaft that both saps power and overheats the oil enough to torture the bearings. If you can imagine riding a bike underwater, this is what your crank experiences. This is the main reason why track-driven SRs run such high sump temps. When experimenting on the dyno, overfilling the crankcase by a measly half a quart caused a drop of 6 whp on an SR20. Having piston coolers that shower the crank with hot oil dropping from the pistons simply adds to the problem.
To help reduce the engine's sensitivity to oil level, gain power, and reduce sump temperatures, we installed a crank scraper and windage tray from Ken Johnson at Ishihara-Johnson Crank Scrapers. The crank scraper made of sheetmetal and cut to closely follow the contours of the crankshaft. It bolts to the main girdle. The crank scrapers job is to strip oil off of the rotating crank assembly so it can be retuned to the pan instead of flying around in a dense cloud, getting hotter and more aerated. We opted for the full-race scraper, which includes a Teflon insert that can be adjusted until it's actually in light contact with the crank so that it does the best job of stripping the oil cloud.
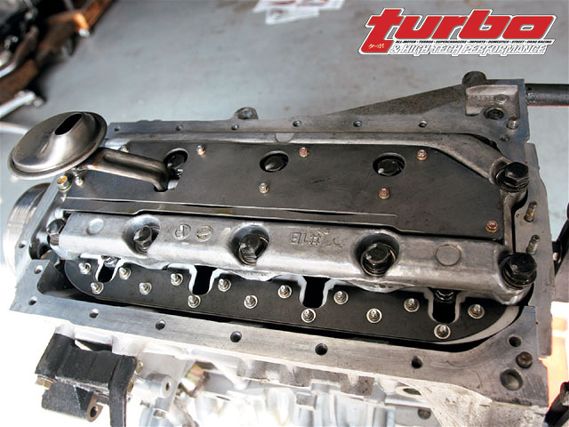
We also opted to run the full-race windage tray. A windage tray is a louvered plate designed to capture oil from the windage cloud that surrounds the rotating crank, and return it to the sump before it gets hot and frothy. The full-race windage tray goes completely across the engine's bottom end to strip as much windage from the crank as possible. However, the full-race windage tray requires some cutting and welding of the oil pan for clearance. Ishihara-Johnson also makes a three-quarter length street version of the windage tray that doesn't require pan modification.
The windage tray and crank scraper work together to greatly reduce the amount of windage in the crankcase. Eliminating the turbulence and oil mist generally gives a power increase of 5 to 6 whp and reduces the sump temperatures by 10 to 15 degrees. Oil with less entrapped air also does a much better job of lubricating the engine's innards. With less oil getting thrown around, the engine's oil consumption goes down and the rings aren't overcome by the volume of oil thrown on the cylinder walls. Although this part isn't absolutely necessary for a low-buck build, it's reasonably priced and gives a free gain in power, something that is hard to overlook in an all-motor build.
With our engine's bottom end details taken care of, we've still managed not to spend too much money. In our next edition of Project Low-Buck SR20DE, we'll massage our cylinder head and design some really cool headers for our budget build.