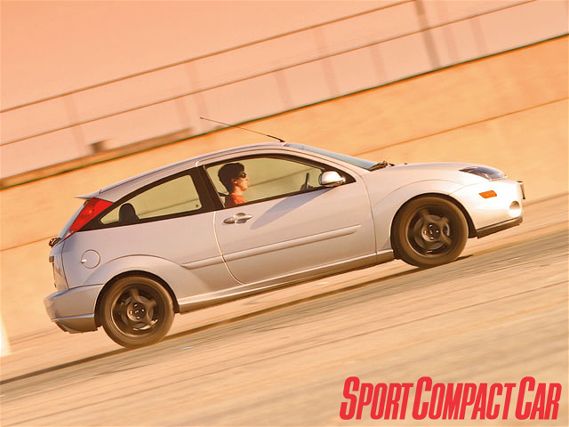
Two-and-a-half years later and Project Focus SVT is finally running again. After the last installment's full engine build by FocusSport in Placentia, California, we're now only steps away from our goal.
The problem is, no one really remembers what the goal was. Back in 2003, when the car was still in production, Coleman and former editor Jacquot started the project when they went to the plant in Mexico and had a car custom-made without sound deadening material and insulation. Coleman's big aim at the time was to build an SVT that could beat a stock Mustang Cobra of the same vintage in acceleration, power, braking and, most importantly, at the track--all while costing less than the MSRP of a Cobra. It was the ultimate middle finger towards muscle car guys from the world of sport compacts. It seemed like a good idea at the time.
As we waited for our stock bottom end to be rebuilt (after Holstein blew it up), we took advantage of the time and got some custom head porting done by Cosworth, put in a Quaife limited-slip differential and built an editor-proof bottom end. This made a hefty addition to our tab and probably wouldn't have been done if the engine wasn't already torn out.
On top of that, the brake rotors were completely rusted through. We're still on the stock suspension and wheels, and still running a stock exhaust--essentially, all the basics anyone would start with at the beginning of a bolt-on build-up.
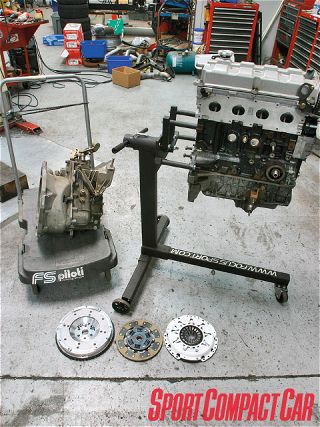
Meeting our price ceiling and still beating a Cobra now seems so unrealistic that we're starting to question what Coleman got us into in the first place. Even by the second installment, he realized he was in well over his head and a little drunk on past project car successes. But winning by the skin of our teeth isn't new to us, so we'll shoot for a victory with equal power, less weight and a lot of tire.
Clutch and Flywheel
Not knowing what kind of power the new engine and additional boost would be capable of prior to tuning, we decided to install a new clutch, while dumping the old steel dual-mass flywheel for a single-mass aluminum piece. With any other performance-oriented sport compact, finding a lightweight flywheel and higher torque-load clutch is a simple web search away.
Not so for the SVT. Even stock replacement clutch parts dried up from the OE supplier just three years after production stopped.
Clutchmasters picked up the slack, redesigning a completely different clutch and flywheel package, saving the small but dedicated cadre of SVT owners from a fate worse than owning a vintage Alfa Romeo. Because OEM parts are scarce, Clutchmasters' changeover package comes with a different flywheel, friction disc and pressure plate, which only work together as a set. The changeover flywheel won't work with clutches made by other manufacturers, nor will the Clutchmasters changeover clutch work with the stock flywheel.
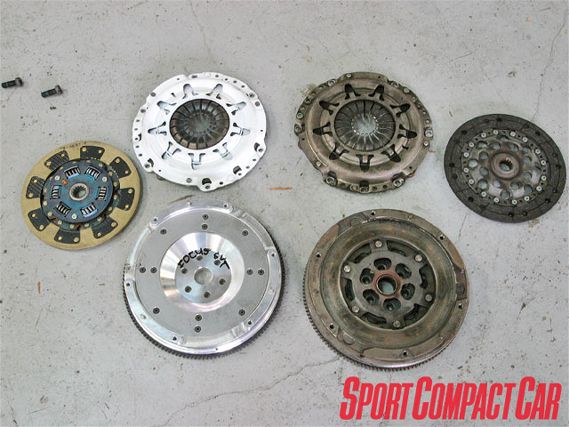
We chose to try out Clutchmasters' FX300 (or stage three) clutch kit. This includes a sprung center hub, which eliminates the need for a damped dual-mass flywheel and a full disc lined with trapezoidal Kevlar friction material. The trapezoidal part refers to how the composite Kevlar fibers are laid down and oriented to each other. According to Clutchmasters, Kevlar offers superior tolerance to high temperatures that cause slip during hard launches, as well as a better friction coefficient. The drawback is the 500 break-in miles required, which few owners are willing to deal with. Combined with a pressure plate handling 1800 pounds of clamping force, the new clutch assembly is now rated for 110 percent more torque than the stock hardware.
The lightweight billet aluminum flywheel weighs 13 pounds, compared to the 24.25 pounds of the stock unit. Going by Coleman's rotational inertia equation written in his Technobabble column several years ago, taking over 11 pounds off the flywheel should be equivalent to the acceleration gained from gutting the interior. We never got to test this dubious hypothesis as the car never ran before. Regardless, the lower rotational inertia and directness of the single-mass flywheel design can be felt in acceleration throughout the rev range and requires quicker, more accurate shifts. And, with less inertia, the engine will be more responsive to throttle inputs and less prone to turbo lag.
New Plumbing
Our hunch on what blew up the old motor isn't actually Holstein. He was just the lucky guy behind the wheel at the time and we like to blame him, even two years after the fact. Most likely it was the mass airflow (MAF) meter mounting location.
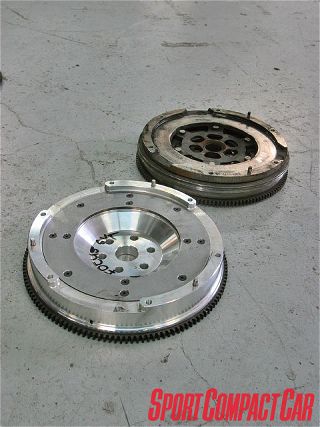
The PTE kit included new plumbing intended for the stock MAF meter to be mounted after the turbo, just upstream of the throttle body, so the air that's measured going into the engine is already pressurized. It's a rare and obtuse method of laying out a critical engine management sensor, and is often prone to aerodynamic turbulence, flow reversal and signal noise issues (something we also see in our Project MR2 Spyder, which is prone to random detonation, even after multiple re-tunes).
The noise and metering error in the original mounting probably caused the engine to go lean repeatedly and just beat the stock pistons into a pulp. Advocates of this type of sensor mounting cite the advantages of metering response and accuracy, as well as eliminating the need for a recirculating BOV. Ultimately, which way is better depends on the MAF meter itself, its mounting location, the distance from the intake or turbo, the throttle plate and the overall geometry of the charge piping.
From what we've seen, most turbo kits seem to prefer mounting the MAF on the suction side instead of the boost side. Using a blow-through meter on the boost side is only an option when there are mounting constraints, like not having enough laminar flow length between the air filter and turbo to get a clean signal, or when the factory MAF sensor harness isn't long enough.
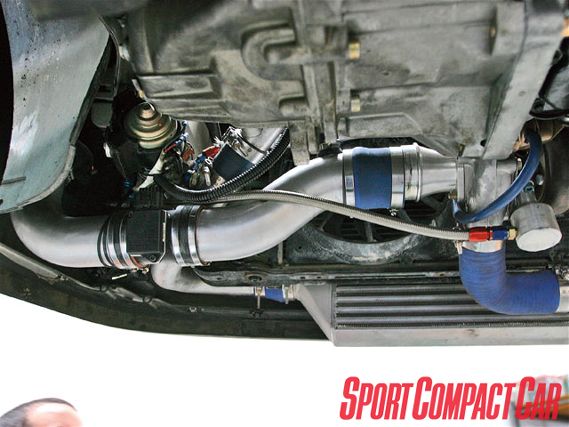
Our original PTE kit has the air filter coming right off the compressor inlet, which is mounted low, in front of the engine, almost at the level of the oil pan. This places the intake tube and the newly relocated MAF sensor low in the body with no undertray to protect it from debris. Not the best thing, but far better than popping another block. An aluminum plate was welded over where the MAF sensor originally sat and now houses the independent stock intake air temperature (IAT) sensor.
Tuning
We started the 500-mile break-in for the new engine and clutch while still on the original tune the car blew up with. We learned from our past mistake and kept out of the boost, since we had no idea how far off the calibration was with the relocated MAF meter.
With 500 miles covered and a fresh oil change, we sent the car back to FocusSport for a retune using the original SCT tuning software. In theory, the new bottom end should be capable of serious power on account of the forged internals and lower compression. But there are plenty of other limitations to the 2.0 SVT Zetec engine that kept us below our target of 300 wheel-hp. For starters, 300 wheel-hp is a lot of power to put through 225-width street tires, even with the Quaife limited-slip differential. Keeping the front tires from lighting up and torque-steering all over the place would be an issue.
Even with a proper tune, we would actually be making less power than the stock engine because the lower-compression pistons would have lower peak combustion cylinder pressures, resulting in a less powerful combustion stroke. The point of low compression is to reduce the knock threshold so more air can be shoved in at higher boost levels. Since boost was still at the stock 10psi (as regulated by the internal wastegate) we would need a simple manual boost controller to increase boost and move more air.
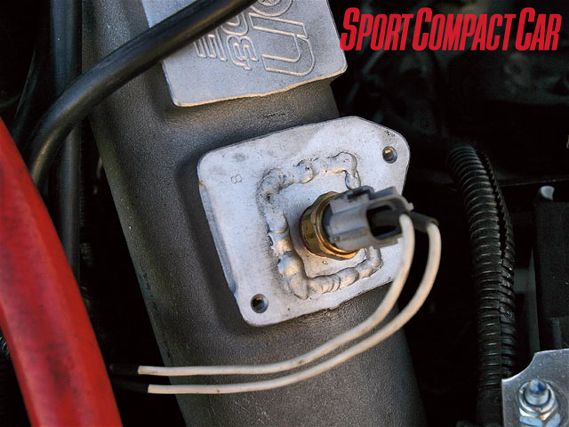
We installed a Turbosmart Boost Tee manual boost controller in line with the stock wastegate diaphragm. The unit is just a needle bypass valve limiting the amount of pressure going to the wastegate so it opens later, allowing the turbo to generate more boost. Setting the boost is a matter of experimentation with a pressure gauge temporarily plumbed in-line to check boost pressures as the car was tuned on FocusSport's Dynojet dyno. The Boost Tee also comes with a nice set-screw feature to prevent tampering after setting the boost level.
More boost comes with a series of other problems, especially on the SVT engine. To measure the additional air properly, the MAF meter has to be able to read the amount of air being ingested. At 10psi, the MAF meter was already pegged out at its highest output of five volts. While the limitation isn't because of flow restriction from the MAF meter orifice diameter, the signal sent out from the sensor and read by the ECU would just read a constant five volts, even if airflow continued to increase. The ECU only sees that the flow limit is exceeded and trips into a fault mode, not knowing that there is still more air going into the engine. It will continue to deliver the same amount of fuel until the mixture goes lean enough to cause detonation and melts the pistons again.
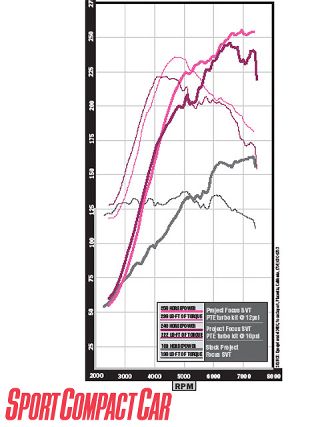
To meter more air and make more power, we needed to modify the signal from the MAF meter. This is only a good idea if you can also completely retune the ECU so it knows how much fuel to inject per the modified signal. DiabloSport, a Florida-based tuning company specializing in domestic tuning and ECU hardware, supplied us with its MAFia interface.
The MAFia is basically a variable potentiometer that plugs in between the stock MAF and the wiring harness leading to the ECU. By intercepting the MAF signal, the MAFia scales down the output voltage read by the ECU. This keeps the ECU happy as the output remains within its zero to five-volt constraints while maintaining the original MAF transfer function profile. The MAFia has eight selectable scaling factors for horsepower ranges up to 800hp.
For our purposes, modifying the airflow signal for up to 300hp of flow is acceptable, but only to an extent. Since the ECU will only read between zero and five volts before getting pissed off, scaling the signal to accommodate more airflow will decrease the resolution. For example, let's say the stock ECU was designed with 10 tunable points between idle and 150 stock horsepower's worth of air. That gives an accurate map to correct the fuel curve every 15 horsepower.
Moving 300hp's worth of air with the stock 10 calibration points can only control fueling between every 30hp's worth of airflow, which makes for a less accurate fuel tune map. Imagine what happens when correcting the MAF signal for 800hp. While the ECU can be modified to manage that kind of power, the large spread between tuning points would mean a rough engine that would offer questionable part-throttle driveability.
With the ability to measure more air, we also needed more fuel. The 42lb/hr (or 440cc/min) upgraded injectors added to our PTE kit operated happily at the 10psi peak boost off the wastegate, but if we were to add more boost, then we'd start to worry about needing larger injectors and, more importantly, replacing the stock fuel pump, which we think will only support up to 350bhp. The best way to find out was to start tuning and see how much more boost and fuel was needed.
There was yet one more limitation. The stock SVT manifold is a laughable plastic affair that uses crimp clamps to secure flexible hoses between the head and the manifold runners, unlike other solid metal or plastic manifolds. There was a good chance that these clamps (never meant for positive pressure) would pop right off if boost pressure went much further past the point we were already at.
After a whole day of 30-minute breaks while waiting for the ECU to reflash with a new program, we finally arrived at a decent compromise of 256 wheel-hp and 236lb-ft of torque at 12psi of peak boost. Just a 10 wheel-hp gain over the 246 wheel-hp the stock bottom end made before it grenaded. The low-rev difference in power is attributed to the change in compression.
While there's plenty more power to be made, 12psi of boost has pretty much maxed out the 42 lb/hr fuel injectors. We could have spent another $200 for a set of 60lb/hr injectors and continued to raise the boost, but based on FocusSport's experience, the manifold was only good for up to a reliable 14psi of boost. Two hundred bucks for two psi didn't seem worth it, so we called it a day.
At 256 wheel-hp, we're now on a level playing field with the stock Cobra, with hopefully less weight. If it sounds like we've shorted ourselves on the serious power that we'd need to beat the Cobra, we did. But 256hp to the wheels is seriously fast, especially when coming from a laggy GT2871R turbo. Much more and we'd waste effort fighting the car than trying to go fast. So, with the power issue resolved and potentially more power to come with an aftermarket exhaust, we're left to tune the chassis so it can stand a fighting chance against the Cobra.
Next time: brakes, cheater tires, suspension and maybe--just maybe--we'll be ready for the face-off. n