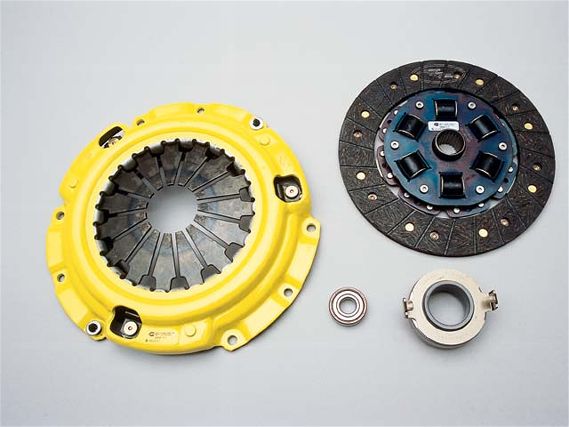
When you're gunning your car down the road, a lot of variables have to converge properly in order to complete that fast and furious gear change. Putting the power to the transmission means relying on a disc that's a mere 5mm to 8mm thick. The disc is abused in unfathomable ways. At launch, it's at a standstill one instant, then it's smashed between two pieces of billet-aluminum and spinning at 4000 to 6000 rpm. The shock, friction and heat generated by this act make the clutch one of the more remarkable automotive component systems.
Bare Basics
The basic clutch setup consists of two sub-assemblies--the clutch disc and the clutch cover--the latter of which is home to the prized pressure plate and diaphragm spring. The clutch disc lives between the flywheel and the pressure plate and its front and back surfaces are made up of friction material. The disc is ground zero, where the engine and transmission are physically joined. The disc is connected to the transmission input shaft via splines in its center section. The clutch cover is connected to the flywheel.
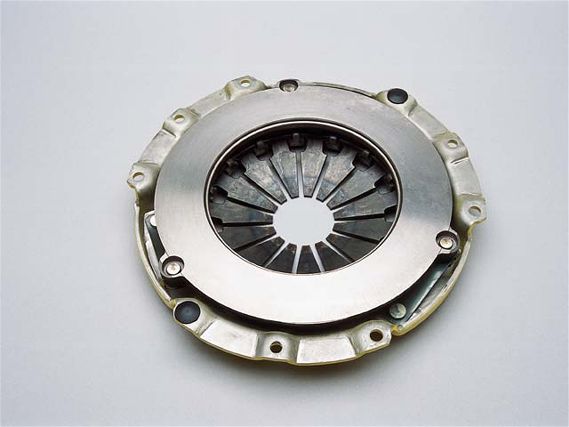
In a static state, the engine and transmission are connected. When the driver pushes the clutch pedal in, either a hydraulically actuated piston or cable release pushes in on the release fork, which presses the throw-out bearing (aka release bearing) against the center portion of the finger-like diaphragm spring. As the spring is compressed inward, an array of pins or other mechanisms on the outside of the unit work to lift the pressure plate off the clutch disc. Think lever effect and you're on the right track. In this instance, the clutch disc is freewheeling on the transmission shaft, where it slows considerably, allowing for gear changes.
When the driver takes his foot off the pedal, the pressure plate re-engages the clutch disc and the engine and transmission are connected. The center hub of the clutch disc is fitted with springs, which help lessen the shock of re-engagement.
Beyond Basics
We hooked up with Dirk Starksen, the president/CTO of Advanced Clutch Technology Inc. We asked Starksen 11 questions yielding answers that should shed light on clutch selection and manufacturing of performance clutches.
Turbo: What are the determining factors of clutch selection?
Starksen: Torque capacity, engagement quality, heat (abuse) tolerance, clutch life, personal noise tolerance, pedal effort, inertia, SFI certification and cost.
T: What are the compromises between a high-horsepower clutch and a lower-horsepower clutch?
S: Torque is the real measurement for a clutch. In general, clutch capacity is not rpm relative. Horsepower is rpm related; torque is not. It's hard to come up with an easy answer; there's always a compromise. Let's start with the basics. The formula for torque capacity is:
T = P x F x N x R
where:
T = torque in ft-lbs
P = pounds of clamping force
F = coefficient of friction
N = number of surfaces (generally 2)
R = radius of gyration (mean radius of the friction surface)
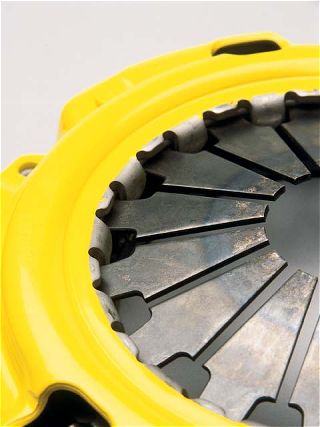
You can see from the formula that each variable has equal effect on the torque capacity. It's simple multiplication. Each variable has benefits and drawbacks when you increase the number to gain torque capacity.
If we could totally redesign every clutch, flywheel and operating system, the compromises would be fewer. Because we have to work with the stock linkage, bell housing, etc., more compromises are necessary to hold higher-powered engines. You'll notice that even high-powered sports cars or high-torque diesel trucks don't generally come with fancy clutches. Conventional diaphragm-type, single organic disc clutches are the norm. This isn't because of cost, but because it produces the least amount of compromise by design. Now, back to the formula and each variable.
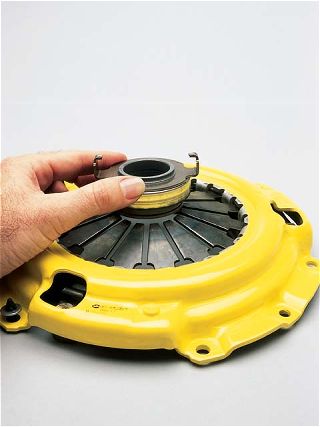
T (torque capacity)
By selecting a clutch that has a higher torque capacity than needed, you can shorten transmission life (depending on driving habits) and endure unnecessary design drawbacks (possibly higher cost, pedal effort, wear rate, chatter, noise, etc).
P (clamping force)
Clamping force is a function of diaphragm spring force and fulcrum points that multiply the spring's force through increased leverage. Since the release bearing pushes directly on the spring, the higher the spring's force and the higher the pedal effort are. The fulcrums don't have any effect on pedal effort since they're downstream of the diaphragm spring. If you alter leverage alone, you proportionally shorten clutch life and increase required travel just like you would in a simple lever.
This method is common with our competitors, but I consider it a shortcut that gives marginal benefits with little effort. Our stronger spring will produce a longer working range, so we typically can also incorporate a small fulcrum change with no reduction in clutch life. We prefer a large increase of spring force rather than a large change to leverage. Using a stronger spring is also the automakers choice for factory vehicles, such as turbo vs. non-turbo models.
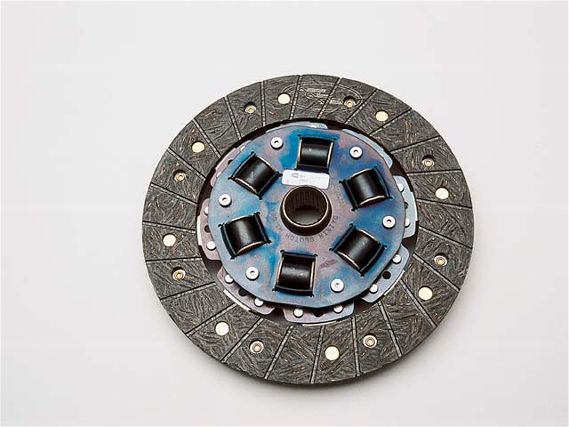
F (coefficient of friction)
This can get pretty deep, but in general, the higher the friction, the higher the wear and worse the engagement quality (chatter). We calculate organic materials at around .25 and our ceramic at .36 (we advertise .32 but changed materials), but these are general numbers for dynamic coefficients and will vary greatly depending on the testing method. We've verified our results to be fairly accurate on dyno tests. Sintered iron has the highest friction we've tested so far, at about .40.
N (number of surfaces)
A single disc has two. If you double the number of discs, which increases N to 4, you double the torque capacity. It sounds good, but the problem is that a simple racing-type double disc doesn't separate the surfaces, so you encounter shifting problems on synchro-type transmissions.
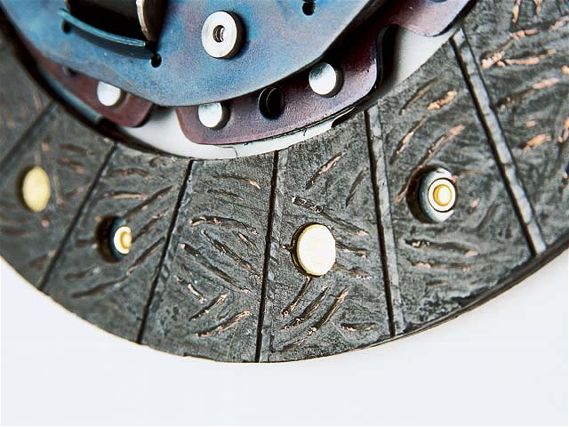
In order to get a multi-plate clutch to operate properly for a synchro-type transmission, a wear-compensating lift mechanism has to be built into the pressure plate and floater. To do this right, it gets really complicated. The earlier NSX had this special lift feature figured out, but it was later abandoned on the six-speed in favor of a less troublesome single-disc clutch. The old 928 Porsche also switched back to single disc after experimenting with a twin.
On a simple multi-plate clutch, noise is also a factor since they generally don't use straps to center the pressure ring or floaters. When the clutch disengages, the parts rattle badly from the torsional vibrations of the engine. In racing, we've seen success on synchro trannies with the Tilton carbon/carbon clutches because the super light weight of the discs make up for the surface drag of a simple twin. Few people can stomach the $4,000 price tag, and clutch life is not fantastic for street use. Note this isn't surface area but number of surfaces. Surface area has very little to do with torque capacity and everything to do with heat capacity.
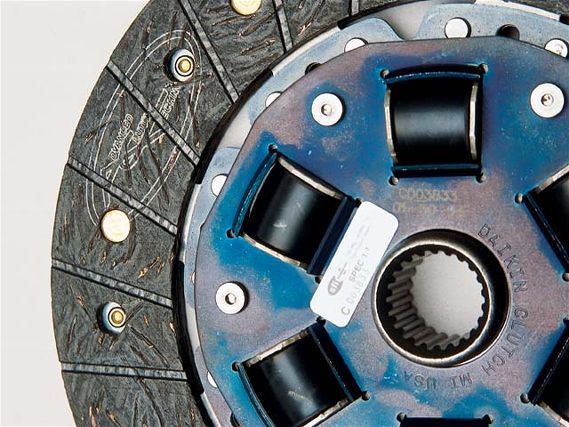
R (radius of gyration)
Radius to middle of friction surface measured in feet. Sometimes clutch size can be changed fairly easily but most of the time it's not a practical option. The '89 Civic, for instance, can use a '90-and-newer flywheel and clutch. It gains not only torque capacity, but also heat capacity, along with broader clutch choices--a no-brainer. The tradeoff of a larger clutch is increased inertia, which may result in slower shifting or possible friction lining burst failures. A larger disc will give more room for larger, tougher dampers (which adds weight).
T: What are the different friction materials used by ACT and what do they do?
S: We like to use the term "disc types." We have three street versions, depending on application. Our stock disc is just that. Sometimes there's no reason to change a design, so we don't. The customer saves money. The RX-7, for instance, has great friction material with high-burst strength. We may be able to improve a little on it but the cost outweighs the benefits. It's a great disc to begin with.
Our modified disc is a stock disc that has less marcel (cushion spring between the backing and lining) to reduce travel requirements. They're meant to complement our pressure plates, but again, the friction material is unchanged.
We have performance street discs for most popular applications that feature a premium organic material that has slightly increased friction and high copper content for better heat transfer. They're also steel-backed for great burst strength and durability. The resin used in bonding the friction material gives higher heat tolerance than most organic discs. These discs are also modified with reduced marcel for faster action to complement our pressure plates.
We provide torsional dampening on all of our street discs (unless stock is not dampened). Our race discs have a much higher friction (see above) but tend to engage more harshly. With the high metal content of the friction material, it's considerably heavier and more heat tolerant than organic. Less material is generally needed or desired, so puck- or button-type designs are used. For drag race applications using a clutchless transmission, we have sintered iron discs capable of great torque and heat capacity. They're full-surface discs that are very heavy and therefore aren't practical for synchro-type transmissions.
The friction material used has to do several things: produce adequate friction; have enough strength to carry the torque and withstand desired rpm; give desired engagement and wear properties; and tolerate heat (and recover quickly from overheating).
Kevlar, for instance, is known for its insulating properties. As a friction material, this is a problem. Kevlar doesn't recover from overheating very fast because it doesn't transfer the heat off of the surface. The result is a material that can cook the mating surfaces (flywheel and pressure plate) and has a lower-than-stock coefficient of friction to boot. Yes, it lasts a long time if treated right, but it's not ideal.
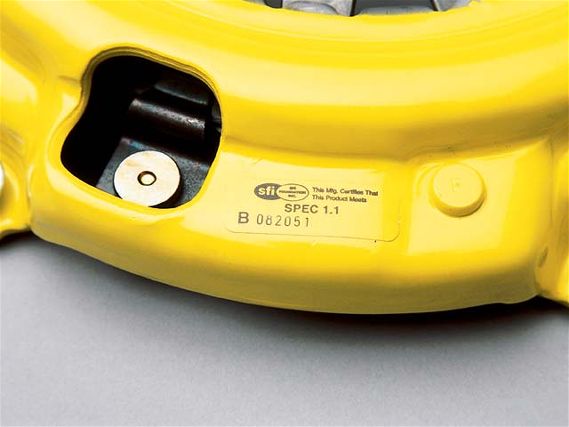
T: What's the difference between a sprung and unsprung center hub?
S: For a traditional flywheel design (not dual mass), springs are placed in the center of a clutch disc to reduce transmission noises caused by the torsional vibrations (rotational pulses) of the engine. A spring center disc will operate quieter and reduce wear on the center splines of the disc. A rigid center disc, being lighter, will shift faster, engage smoother with high-friction materials, and avoid spring failures. They're race parts and aren't intended for high-mileage applications, since the splines tend to wear out prematurely from the vibration.
Torsional vibration will increase with fewer cylinders, higher compression, hotter cams, higher boost, timing, lighter flywheel, or many aftermarket harmonic balancers.
T: Do ACT clutches work with the factory flywheel?
S: They're intended to be a direct replacement. Of course, the ACT flywheel is preferred.
T: Do ACT clutches require modification of the bell housing to allow for installation?
S: No.
T: Does ACT use a new or refurbished pressure plate/disc in its clutch lineup?
S: Only new. We manufacture many of our own pressure plate components, including diaphragms, drive straps and ductile castings. We make our Integra pressure plates from scratch because we found too many faults (and expense) in the existing design. We also manufacture our own race discs from scratch.
We mostly make our street discs from stock or modified stock discs. We use our own friction material on our performance discs and have some discs custom-made to our specs. We scrutinize which discs will give us the best product.
Troubleshooting
T: What causes clutch chatter?
S: A high coefficient of friction, bad motor mounts, an incorrectly machined flywheel or faulty pressure plate, spring-centered race disc (aggravates chatter), and contamination (oil, grease, or rust).
Chatter is basically the engine winding up in the mounts as the clutch is engaging and then bouncing off the mounts, disengaging the clutch for a brief moment before engaging again and winding up again. No matter how aggressive a clutch is that would normally chatter severely on a normal street car, it generally won't chatter at all on a car with solid mounts and a rigid disc because there is no wind-up effect.
T: What causes clutch slippage?
S: Oil contamination, worn friction material, inadequate friction or clamp load for power.
T: What results in poor shifting, a shifter with a clumsy feel to it?
S: A faulty pressure plate (won't lift from disc), damage upon installation causing a bent disc, failure to adjust a clutch pedal or cable properly, or poor choice of parts (sintered-iron disc, wrong double-disc setup).
T: Why is clutch break-in so important?
S: We recommend 200 to 300 miles of mellow usage for our street discs. The purpose of breaking in a clutch is to engage the disc in a controlled, consistent manner to ensure the disc, pressure plate and flywheel all make full surface contact. It's also a chance for the friction material to experience normal heat cycles.