Monoblock wheels are all the rage and with great weight savings and a mean demeanor, they've also become the best option for cars that sport high "positive" offsets. When you have a car that can't accommodate a large lip, multi-piece wheels can make your car look limp or narrow. On the flipside, Monoblocks bring out the beast in your ride and whereas we normally judge the width of a wheel based on the "lip" of the wheel, Monoblocks show off width through a deeper center "cone". In addition to being lighter than most of their multi-piece counterparts, Monoblocks are less susceptible to leaks from faulty seals and when it comes to looks they typically look larger than they really are since most designs carry the spokes to the outer edge of the lip. But if you're worried about design options then don't think that you'll be stuck with single tone finishes. Custom paint finishes, two-tones, three tones and mutli-paint application are available and the only thing that'll ever limit your Monoblock options is a budget. So catch a budget and break bread. Here are a few shots of some Monoblocks being cut over at the Savini factory.
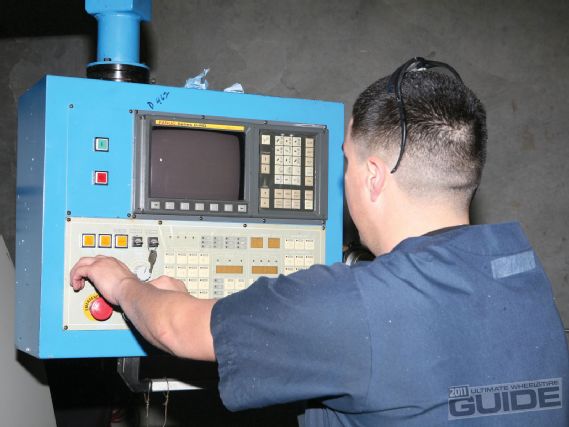
All lathe blanks made of T6061, heat-treated, forged air-craft aluminum.
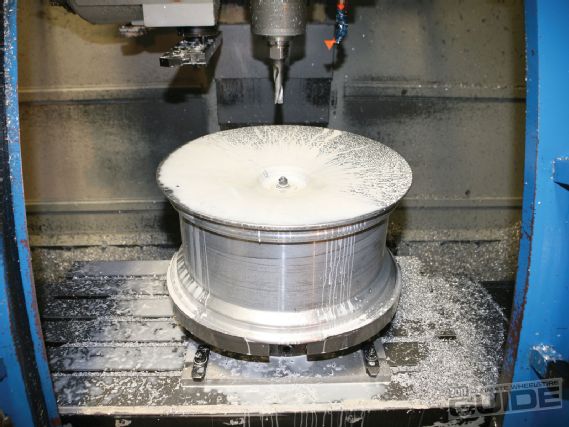
The starts cutting utilizing the largest bits first, from there it transfers to smaller bits and starter holes are opened up using a one inch bits.
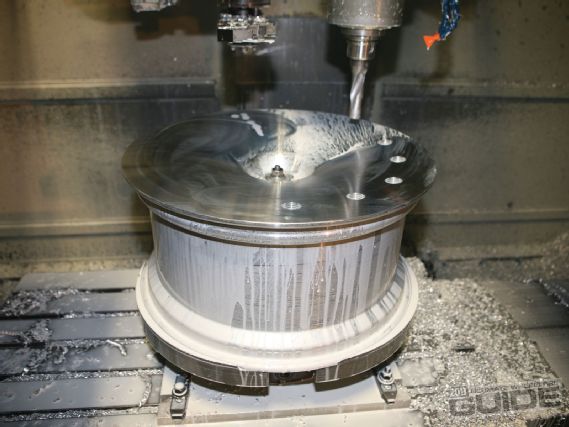
Seven smaller drill bits are used to make the details on the wheel and groves.
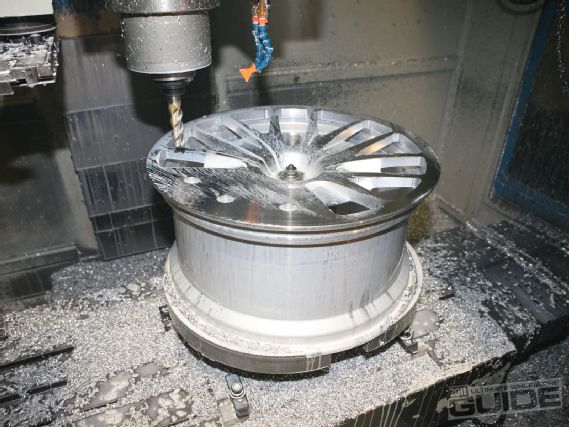
After most of the wheel is drilled out. An End Mill bit is used to clean out the roughness that the Rougher Bit has caused.
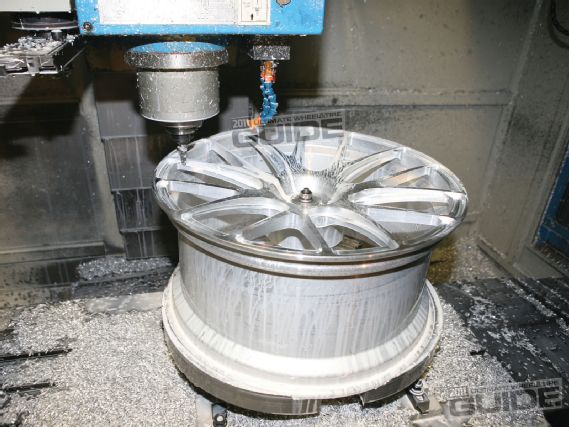
It takes a total of 45 minutes to drill out a Monoblock.
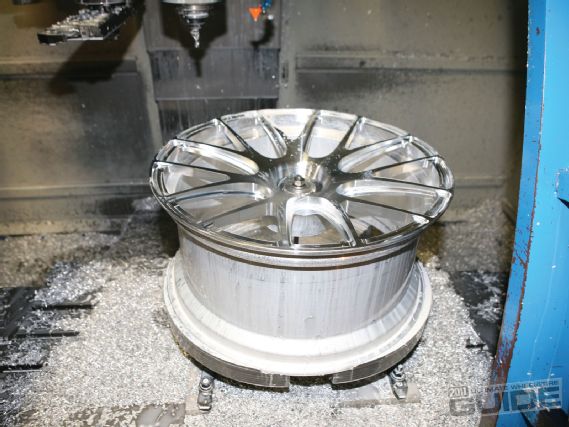
After most of the rough cuts are made to cut out the "windows" or face of the wheel, the machinist then uses an end mill bit to clean up the "rough" edges. From there, the rest of the edges are shaved by hand.
- A 20-inch Monoblock lathe blanks weight in at 50 lbs and by the time they are done it will weigh in at it's lightest in the low 20-pound weight range depending on design.
- The biggest Monoblock available is 22 inches by 13 inches wide.
- If you need wider or taller applications they can be made custom ordered.
Monoblocks have less chance of failure due to fewer variables. Monoblocks consist of one piece whereas multi-piece wheels have more variances in parts (inner lip, outer lip, bolts, face, seals, etc...)
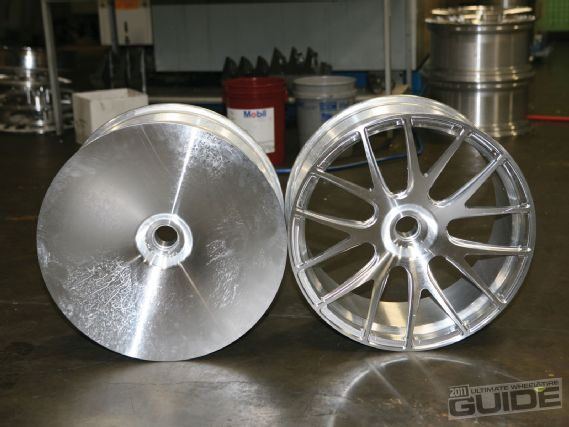
Monoblock wheels can handle more
horsepower and torque vs. a cast or
multi-piece wheel.