One of our favorite trends in the truck world is a deep, inset wheel on the back of any truck. It’s nothing new, as truck owners from all over the world for as long as most care to remember have always wanted a wide wheel and tire combo on the rear of their truck. Prior to the 1999 to current 2014 GM trucks, wide wheel and tire combos were fairly easy to obtain as the rear differential was narrow in relation to the bed’s outer sheetmetal. Back when General Motors introduced their new line of pickups in the late 1990s the idea for more high-speed handling as well as load capacity was addressed by adding more track width to their vehicles. This pushed out the mounting surface, thus leaving the “deep lip” styling behind with the earlier-model vehicles.
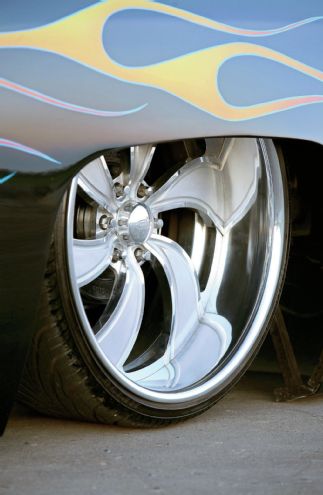
| Narrowing GM Truck Axles To Fit Deep Dish Wheels
Enter the custom truck enthusiast, whose goal is to customize his or her vehicle to their own liking in a quest to stand out from corporate vehicle conformity. One of the top modifications on the dream list usually is to narrow the rear axle to allow deep lip wheels. A point to clarify before we go on is that this modification isn’t just for owners of 1999-and-up GM trucks; narrowing an axle to fit a deep lip wheel knows no boundaries when it comes to age. Most of the same modifications are performed on earlier-model differentials to obtain the same result. The only real limitation is wheel availability. But with 20x15 or 24x12 wheels a web click away, you can pretty much let your imagination run wild.
With any modification, there are extremes. Based on past trends, rear differentials were narrowed to the point where it appears that the tires join together like something out of the Flintstones. For argument’s sake those applications have their place in time, but having that much rubber on the road as a daily driver comes with some drawbacks, most of which involve cornering, high-speed instability, and heaven forbid, a rainstorm that will turn a “Texas Steamroller” into a slip and slide in a hurry.
With that in mind, how much is too much, and how little makes it cool? That’s what we set out to find when we stopped in at Fearless Gear located in Fresno, California. Known for having transformed more ’99-up “slim jobs” than anyone else around, we wanted to get the skinny (no pun intended) on how to narrow a GM rear end. It was important to us that we have the best of both worlds: the look of a deep wheel, while still maintaining some of the OEM specs. Follow along as we take a look at how that happened by the pros at Fearless Gear.
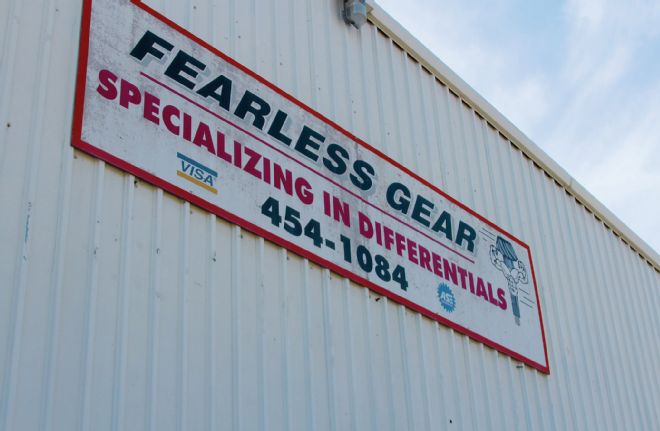
| 01.
01: Known across the land as the place to go to narrow your diff, set up gears, or even build a one-off off-road creation, Fearless Gear is located on the outskirts of Fresno, California, and performs so many ’99-up GM narrowing jobs that they keep all of the necessary parts in stock to perform the work.
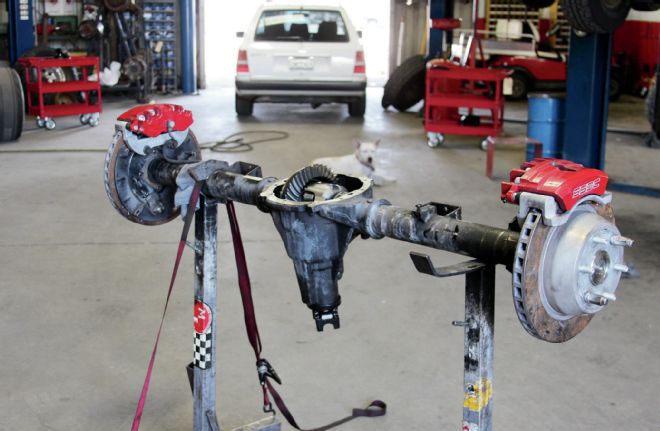
| 02.
02: Rear differentials are shipped from all over the country as this customer did from Southern California. The crew at Fearless Gear can usually turn around the job in a day or so.
03, 04, and 05: The first step is to disassemble and examine the rear differential. Upon the inspection of this housing, the staff at Fearless Gear used a fixture bar made from a solid piece of steel, sliding it into the housing and tightening it down to the main caps of the differential. They found that the housing was way out of true and needed repair, so the repair started by cutting off the axle flanges as close to the seam weld as possible using a Porta-Band saw.
06, 07, and 08: Next, the housing was affixed to Fearless’ housing fixture where tension is applied to the end of the housing as the axletube is carefully heated using a torch. They watch the amount of heat carefully and where to place it as a dial indictor guides them until the fixture bar reads true all the way around.
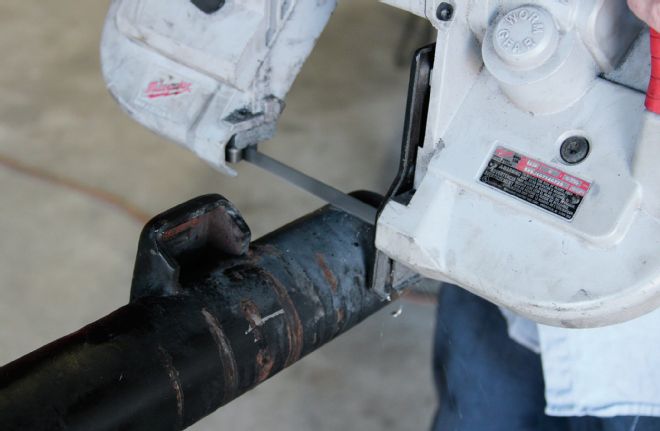
| 09.
09: Now is when the fun part begins, as 1½ inches are cut off on both sides resulting in 3 inches overall being removed.
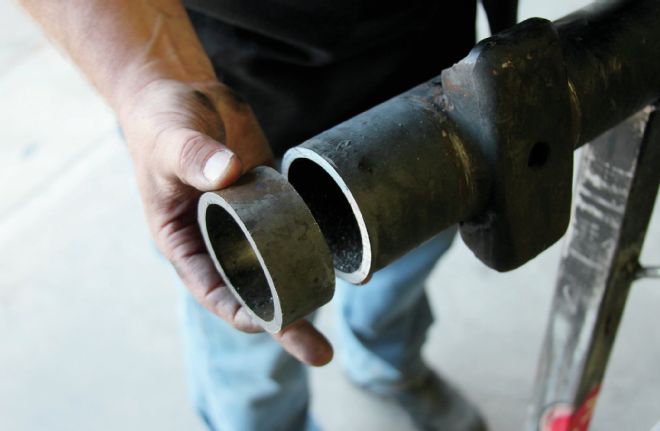
| 10.
10: On a 10-inch-wide rim, running a 295- to 305-spec tire, the back spacing will equal 6 ½ inches, giving the look of a deep wheel, without cutting the wheelwells.
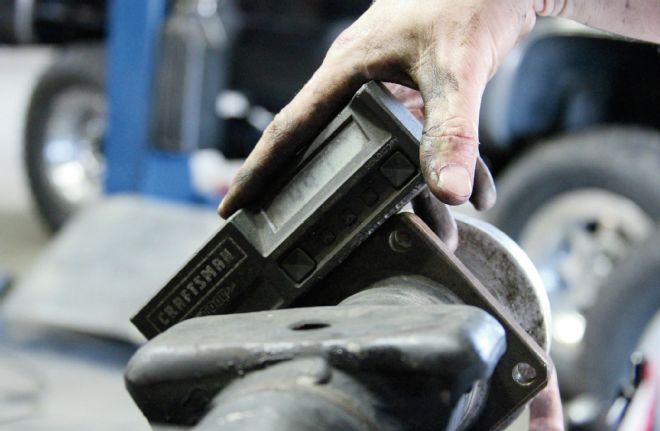
| 11.
11: The cut-off axle flange is set back into the axletube and held in place by a Fearless-built fixture to align the flange with the axletube properly.
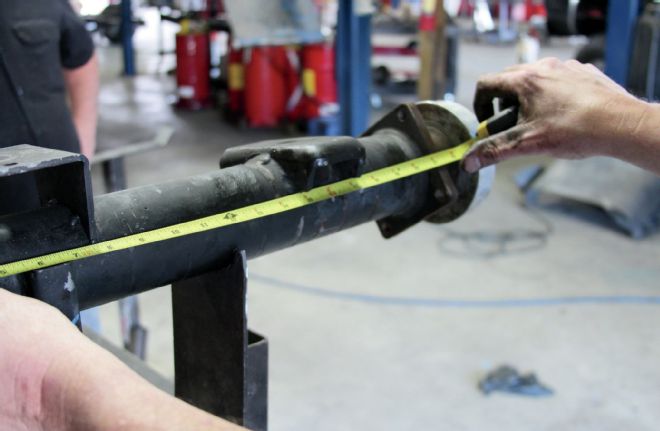
| 12.
12: The axle flange is set back to the stock location and checked with an electronic angle finder, before it is double-checked, and then triple-checked for the proper measurement. This is critical that the measurements be right in spec, as the housing specs must match the axle’s specs or there will be big problems later.
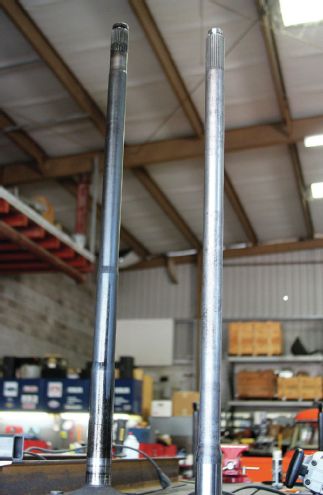
| 13.
13: Here’s a great look at the difference between the stock axle on the left and the narrowed axle on the right. Of course, one can see that the narrowed axle is shorter.
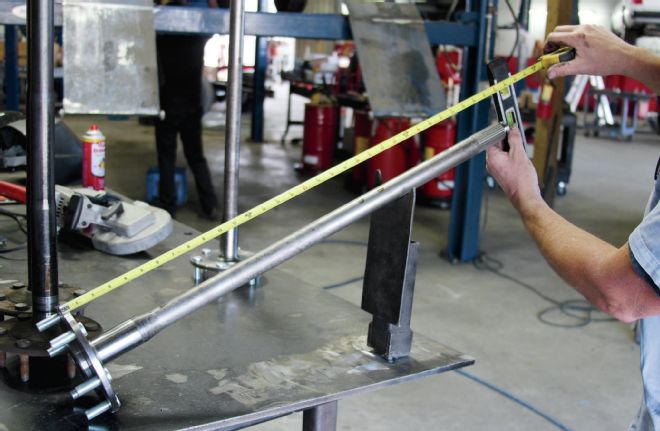
| 14.
14: What your eye can’t see, however, is the strength of the forged axles that Fearless makes specifically for this application. Before installation, the axle length is double- and triple-checked and compared to the housing measurements. The axles are paired with the housing at this point in the build.
15, 16, and 17: To ensure strength at the axle flange, the crew at Fearless chamfers both the axletube end as well as the axle flange. Forming a V-groove allows the welder to properly penetrate both pieces while maintaining just the right amount of heat, so as not to distort the axletube. The process begins by grinding the axletube on the fixture, to around a ¼-inch-wide chamfer. In order to get a consistent chamfer on the axle flange, the flange is chucked into a lathe and spun while an angle grinder trims down the material to form the chamfer.
18, 19, and 20: With both the axletube and the axle flange chamfered, the two are set in place again using Fearless’ axle end fixture plug to form a ½-inch V-groove that is now prepped for welding. Before welding the axle flange back into place, another measurement check as well as setting the axle flange back into the factory position is made. Finally the axletube and flange are joined back together by carefully welding them together.
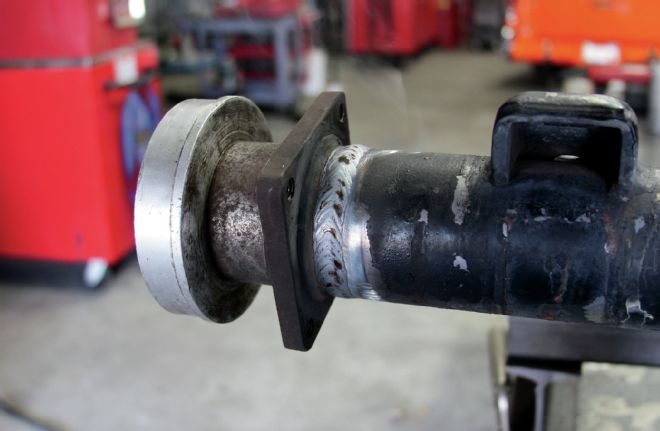
| 21.
21: It takes a team of two guys to get these results, as one turns the housing in the fixture as one welds the seam back in place.
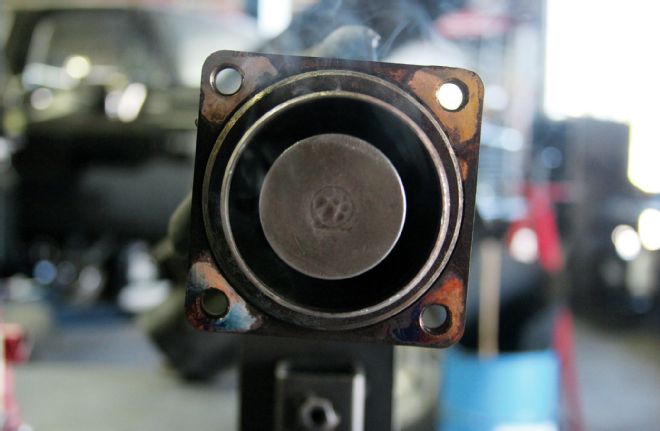
| 22.
22: The synchronized system results in a stronger seam than the factory seam was in the first place. As the seam cools, a close eye is placed on the fixture bar that is still in place to ensure that the heat from the welding hasn’t disrupted the axletube’s true setting.
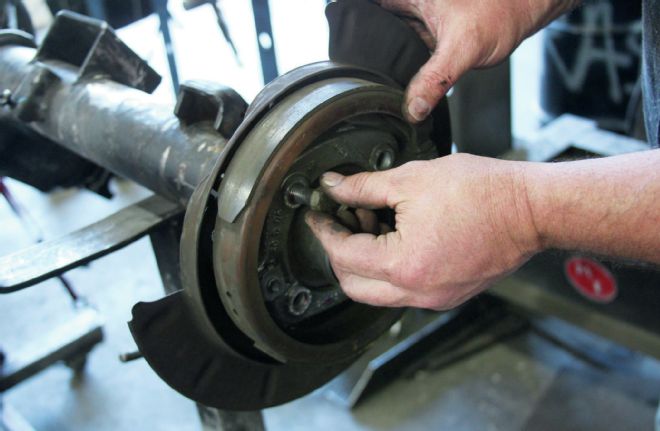
| 23.
23: After both axletubes have been welded and cooled, the next step is to install the backing plates, axle bearings, and axles themselves.
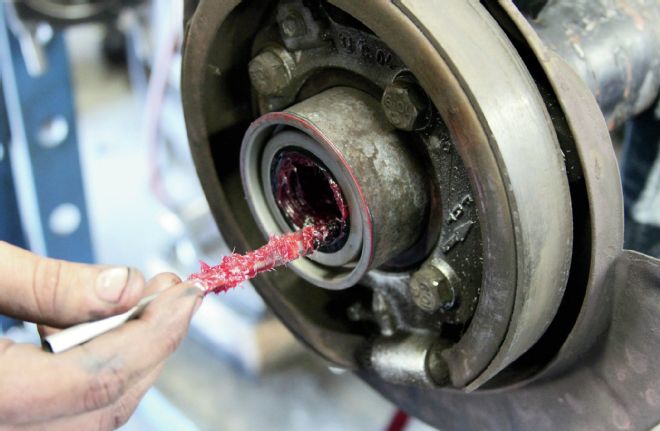
| 24.
24: The process begins by bolting on the backing plates to the axle flange. Once those are set in place, a liberal amount of grease is placed on the outer seal.
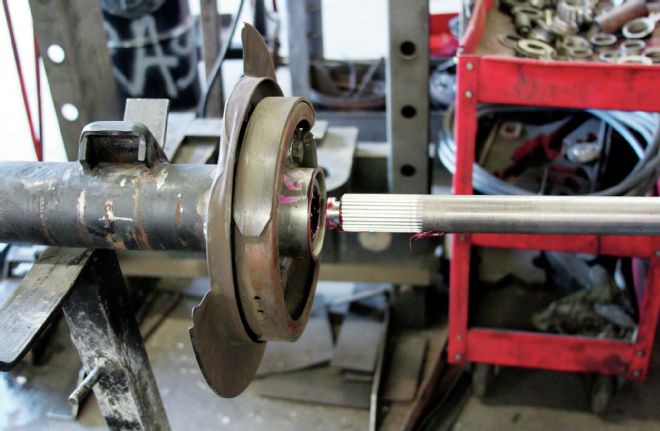
| 25.
25: Now the axles are carefully slid into the axletubes.
26, 27, and 28: From the look of the next photo you can tell that the term “C-clip” was pretty much a no-brainer when the idea came about in the early ’50s. The basic operation of these clips is to wedge between a collar machined into the end of the axle. They are held in place by a large pin that slides between the axles spacing the two axles from one another thus holding the C-clips in place against the carrier. Without these clips, the axles would slide out during cornering. The first step of their installation is to remove the fastener that holds the pin in place. Once that is removed, the pin can be pushed or pulled out of the carrier to allow the axles’ collars to be visible between the spider gears. Next, the clips are set into the groves of the axles and pulled back toward the outside of the housing to allow the pin to slide back in-between both axles.
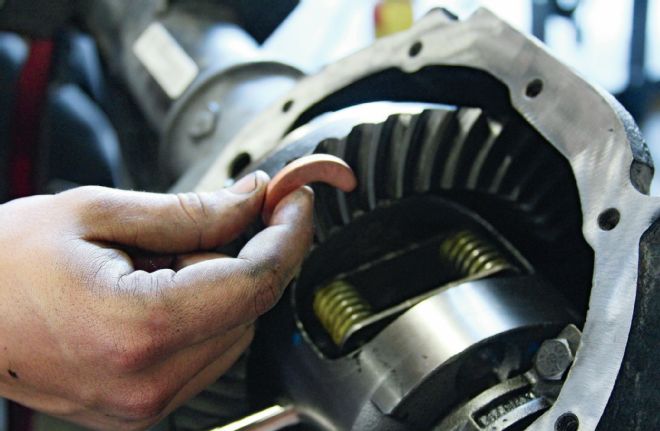
| 29.
29: Again, the pin will maintain a distance between both axles, which, in turn, keeps pressure on the clips. Don’t forget to install the fastener that holds the pin in place of the carrier!
30, 31, and 32: Now that the differential parts have been reinstalled, it was time to move on to reinstalling the brake components. The rotor slides right back over the axle studs, and the caliper bracket holds the rotor and caliper in place.
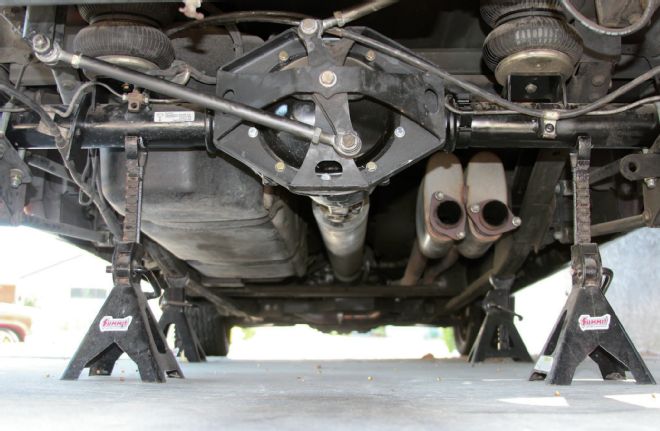
| 33.
33: With the process completed the differential was shipped back to its original location and reunited with the truck. If you want to find out more about the services provided by the folks at Fearless Gear, check out the contact information below.