1993 Custom Toyota Mini Truck - Project Dragged Daily, Part I
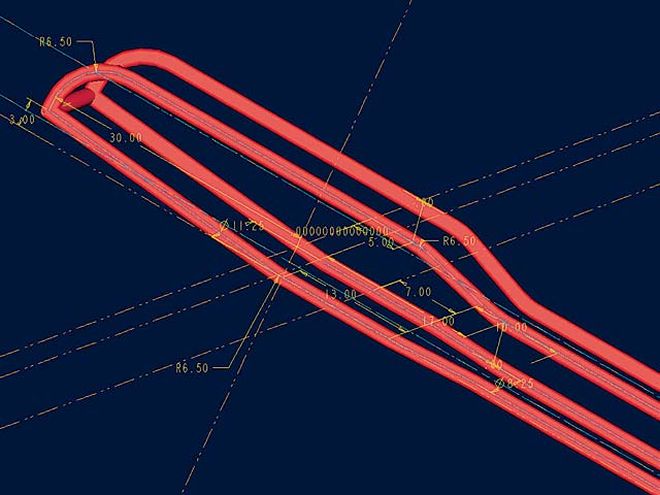
| 1. After Aaron calculated all the pertinent measurements from the stock frame (wheelbase, body mount locations), he put those measurements to use and begin to build the new frame from scratch.
As you've probably seen by now, Project Dragged Daily is in the full build-up process. Since we want to try and bring you as much of the action as possible, we're breaking up the buildup into as many parts as necessary to show you the complexity of building a frame from scratch--engineering at its finest.
For Part I, we'll show you how Aaron Iha is able to pump out a one-of-a-kind chassis in less than a day. Obviously, we're not talking about the suspension and a full rolling chassis yet, but just the frame skeleton alone in six hours is more than impressive. Aaron has a background in engineering, and when armed with his TI-85 calculator and Pro-Engineering program he is able to seriously push the limits of truck customization.
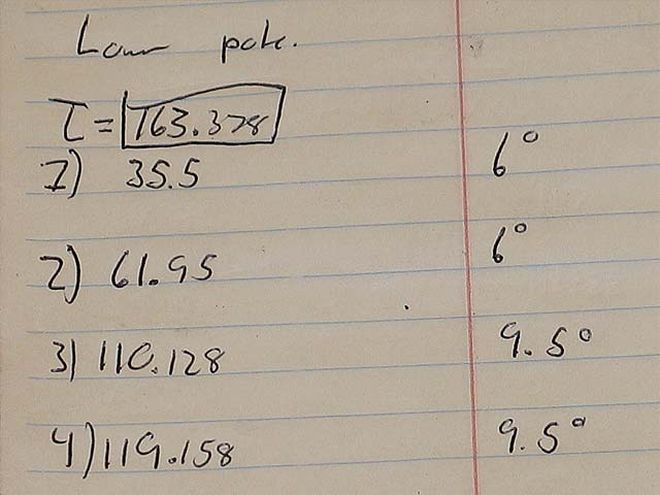
| 2. With the frame designed on the computer first, Aaron was able to calculate the exact length he'd need each piece of tubing to be, and where and how he'd want to make all the bends. Armed with his trusty notepad, he wrote down all the pertinent measurements.
When approaching a full chassis buildup, Aaron tackles every single truck with a fresh eye. He likes to keep the trucks he builds as individual as their owners, so he won't get stuck in the usual rut of building the same type of setups over and over. Rather, he begins by assessing the reason behind building a new chassis. For this particular project, we're after a super-low truck (body-dropped past the pinch) with a stock floor because we'll need the headroom when it comes time to chop the top. Therefore, after a week of brainstorming, Aaron decided he wanted to build an extremely narrow, full-tubular frame to run down the center of the truck so we would still have plenty of structural integrity and not have to cut out much of the floor. The really cool thing about his engineering knowledge and programming capabilities is that it enables him to build 3-D framerails that don't have to be cut and welded in various places because he can actually map out the entire frame and calculate each bend before he cuts the first piece of steel.
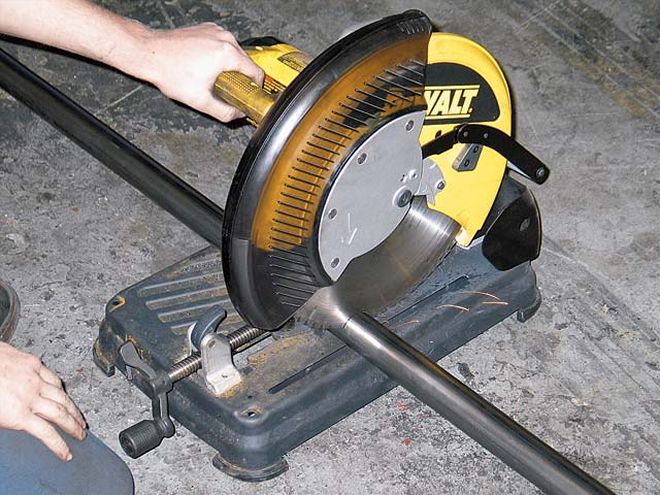
| 3. With the measurements in hand, each rail was cut to the appropriate length.
This pre-mapped frame-building technique drastically reduces the amount of trial and error involved in one-off frame building. After Aaron spends a couple of hours designing each tube, he can then take all his measurements and put them to work on the actual metal. In no time at all, he is able to take four sticks of 1 3/4-inch tubing and turn them into a 3-D frame that has numerous bends and contours and matches the shape of the drivetrain. He also keeps the suspension setup in mind and the amount of lift we're looking to get, so he leaves plenty of room for suspension design. Follow along as we show you how advanced our sport is getting, and see for yourself the latest in truck customizing. For more information, contact Aaron using the info in the source box on Page 2.