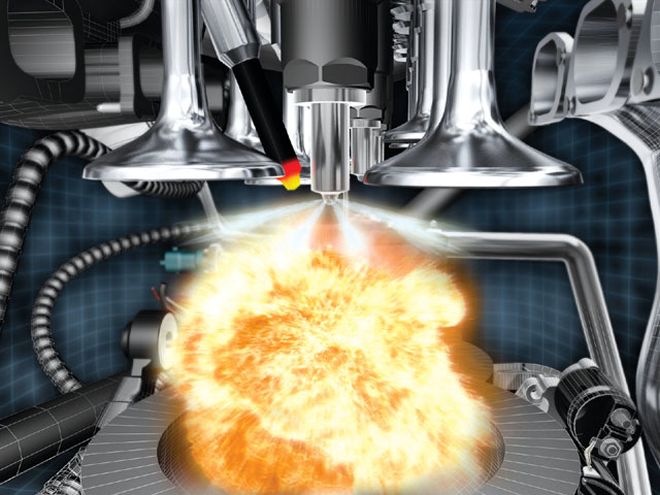
| bosch Diesel Injection System injection System
You can always tell a diesel truck is headed your way from the "diesel rattle," right? Well, not so much anymore. Significant technological advances have eliminated much of the rattle we associate with older diesels. Today's new generation of light-duty diesels has been transformed into vehicles that are nearly as quiet as automobiles powered by conventional gasoline engines.
What has changed? New and improved diesel-system technologies like common-rail injection allow the use of electronic fuel-management controls, one of the primary advances that has quieted the diesel. Developed primarily by firms such as Robert Bosch and Siemens, these systems are in use in new light- and medium-duty diesel automobiles and light trucks around the world. The common-rail system (and other new-generation diesel systems) allows fuel to be injected in multiple pulses into the engine combustion chambers during each injection cycle instead of one large pulse. The multiple injections soften the normally steep pressure rise in the combustion chamber, which was responsible for the rattle in older diesel cars and light trucks.
Bosch, the world leader in diesel fuel and engine-management systems, provides advanced diesel components and systems for millions of automobiles and trucks. Bosch has been a major player in diesel-injection components since making the diesel engine as we know it viable by introducing the first series-production, inline, fuel-injection pump in 1927.
State-of-the-art injection engineering transforms diesel engines into economical, silent, and high-torque drive systems. The latest-generation common-rail diesel system, for example, effectively lowers the exhaust emissions of diesel engines by up to 20 percent in comparison to previous generations and alternatively increases the achievable engine output, reduces fuel consumption, and lowers engine noise. A special feature in the third generation of Bosch's common rail is the rapid-switching piezo injectors.
Diesel engines compress air in the cylinders to as much as 20:1 (or higher) compression ratios, while the normal gasoline internal-combustion engine compression ratio is usually around 10:1. The extreme compression makes the air very hot, and when fuel is injected into this hot, compressed air, combustion occurs.
In older-generation diesel engines, pressure buildup from the pump in the fuel lines opened spring-loaded injection valves at about 5,000 psi. The sudden injection of fuel into the cylinder caused a steep pressure rise to suddenly build in the cylinder and combustion chamber. Sounding much like a series of small explosions, these were heard as diesel rattle. The use of pre-injection pulses and "shaping" the main pulse in today's diesel lessens the sudden pressure rise-and the diesel rattle.
The higher pressures (over 26,000 psi and climbing) currently utilized by the new electronically controlled common-rail systems allow the injectors to deliver a finer atomization in the injected fuel, which improves combustion efficiency while reducing particulate emissions.
Today's diesels are more sophisticated than ever before, but the basic principles of operation remain the same. Truck diesels are growing in popularity. In 2004, the light-truck market represented about 3 million vehicles in the United States and is expected to grow to 6.8 million by 2008.
Use Great Caution-Extremely High Pressure!These diesels sometimes need tender loving care. They are no problem to keep running if you know what you're doing, but proper training in diesel diagnosis and service is absolutely essential. It could be worth your life. No matter how good of a wrench you are, that isn't a gasoline engine under the hood of your diesel truck, and if it needs service, take it to a specialist. Why? You have to use great caution when working around diesel-fuel pressures. Today's common-rail-type diesels run up to 29,000 psi. You can no longer use the old technique of loosening an injector line to check for a dead cylinder. Doing so could end your life! At that extreme pressure, the fuel could easily cut through you!
A look at the Diesel engineFirst, let's take a look at what makes a diesel a diesel. You might be surprised to find that none other than Rudolf Diesel, a German engineer who developed the idea for the engine in the late 1800s and patented it in 1892, invented the diesel engine. Diesel sought to build an engine with greater efficiency than the crude gasoline engines of that time, which were notoriously inefficient.
The diesel engine, unlike the gasoline engine we all know so well, is a compression-ignition engine. In this type of engine, the diesel fuel is ignited by being injected into the cylinder, which contains extremely hot pressurized and compressed air.
This "diesel cycle" can use many different fuels, and Diesel's first working engine, demonstrated at the 1900 World's Fair, ran on peanut oil.
Today's diesel engine uses Diesel's concept of the fuel being ignited by introducing it into a very hot combustion chamber filled with compressed air at extremely high cylinder pressures. The diesel fuel is delivered to the combustion chamber by pressure-activated injectors in a highly atomized state.
When a gas is compressed, its temperature rises. Air is drawn into the cylinder of a diesel engine and compressed by the rising piston, and the air temperature is 700-9,000 degrees Celsius or 1,300-16,500 degrees Fahrenheit. The fuel is injected into the combustion chamber at extremely high pressure through an atomizing nozzle and mixes with the hot, high-pressure air. The resulting mixture ignites and burns very rapidly, and this combustion causes the gas in the chamber to heat up rapidly, increasing its pressure and forcing the piston down.
Basic Operating PrinciplesLike most gas engines, most diesels are reciprocating, four-stroke, piston engines with intake and exhaust valves. However, there are many major differences. Diesels operate at nearly twice the compression ratio of most gas engines, and the fuel is typically heavier, more oily, and injected directly into the cylinder. It is ignited by the heat of compression rather than by a spark plug. Diesels have a relatively narrow power band, developing most of their power around 2,000 rpm.
Prior to electronic fuel-management systems for diesels, pressure generation and the provision of the injected-fuel quantity were typically coupled to each other by a cam and pump plunger. The resulting characteristic was that injection pressure increased with increasing speed and injected-fuel quantity. During the actual injection process, injection pressure increases and then drops again to the nozzle-closing pressure at the end of injection.
With today's common-rail-type systems, the injected-fuel quantity is as low as possible at the start for ideal combustion with its pilot and main-injection features. Solenoid-actuated injectors are triggered by an electronic diesel control (EDC) well before top dead center (TDC) to smooth the combustion process, resulting in smoother and quieter operation.
The evolution of electronic diesels with a common fuel rail system, similar to gas engines, began with the Ford Power Stroke in 1994 and Bosch's common-rail system on the '01 Duramax and '03-and-later Cummins. The Power Stroke, an International engine, delivers fuel through an internal passageway in the cylinder head, and fuel pressure is actually created at each injector with hydraulic oil pressure. In Bosch's common-rail system, the distributor or inline-injection pump is eliminated. Instead, high pressure forces fuel up to 1,800 bar (180 MPa, 26,000 psi) into a "common rail." The common rail is basically a tube, which, in turn, branches off to computer-controlled injector valves, each of which contains a precision-machined nozzle and a plunger driven by a solenoid or even by piezo-electric actuators.
Dodge fuel systems became electronic in 1998, using the Bosch VP44 fuel-injection pump with its 5.9L Cummins engine. 2003 marked the first year that Dodge vehicles were fitted with Bosch's common-rail system. General Motors became electronic in 1994, using the Stanadyne DS fuel-injection pump and went to the Bosch common-rail electronic system in 2001 with its 6.6L Duramax engine for Chevrolet and GMC vehicles.
In older diesel engines, a distributor-type or inline-injection pump, regulated by a governor, supplied bursts of fuel to injectors, which are simply nozzles through which the diesel is sprayed into the engine's combustion chambers.
Required Electronic ComponentsWith most common-rail accumulator fuel-injection systems, pressure generation and fuel injection are completely de-coupled from each other. The injection pressure is generated independently of engine speed and injected-fuel quantity. The fuel is stored under pressure in the high-pressure accumulator (the "rail"), ready for injection. The driver defines the injected-fuel quantity, and the start of injection and injection pressure are calculated by the electronic control unit (ECU). The ECU then triggers the solenoid valves so that the injector at each cylinder injects accordingly.
The ECU requires sensors for the system to function. Sensors providing data to the ECU can include a crankshaft-position sensor, a camshaft-position sensor, throttle-position sensor, boost-pressure sensor, rail-pressure sensor, coolant sensor, and mass air meter. Using the input signals from these sensors, the ECU measures the driver's requirements (accelerator-pedal setting) and defines the instantaneous operating performance of the engine and the vehicle as a whole.
The mass air meter provides the ECU with data on the instantaneous airflow in order to comply with emissions regulations. For engines equipped with turbochargers and boost-pressure control, there is also a boost-pressure sensor. Diesels respond especially well to turbocharging. At low outside temperatures and with the engine cold, the ECU applies data from the coolant-temperature sensor and the air-temperature sensor to adapt set point values for the start of injection, post injection, and parameters to the particular operating conditions. Taken together, these basic functions control the injection of diesel fuel at the right moment, in the right quantities, and with the correct injection pressure to ensure that the diesel engine runs smoothly and economically.
Glow Plugs to Improve PerformanceGlow plugs, which provide the initial heat to create combustion to start a diesel engine, contribute significantly to the new, smoother diesels.
In many older diesel engines, current to the glow plugs is shut off after they have reached the minimum diesel starting temperature (15,620 degrees Fahrenheit), and the ignition is turned to the start position. Since the late 1990s, however, most diesel-engine control systems are designed to keep the glow plugs "turned on" while the engine is cranking and for a brief period after the engine begins to run. This feature, called post glow, enhances engine combustion for improved emissions and provides for a smoother idle during initial cold-weather start conditions,
The post-glow heating phase generally runs from 20 seconds up to 3 minutes, dictated by the vehicle specifications, ambient air temperature, engine temperature, and the glow plugs themselves. Bosch's Duraterm technology and glow plug construction, for instance, utilizes a self-regulating system that reduces glow wait time by more than 50 percent and allows the glow plug to stay "on" longer for more efficient diesel startup. With Duraterm technology, glow plug damage due to overvoltage and heating is virtually reduced for maximum service life.
Ford diesel unique operationsThe Ford Power Stroke engine's system-control module or a thermo time switch de-energizes the glow plug relay when they are no longer needed, cutting off power and shutting them down
The 6.0L Power Stroke fuel-injection system uses the engine-lubricating oil as a pumping medium. A dedicated high-pressure pump provides 3,000 psi lube oil to a common rail, then, in the injector itself, it's intensified by a ratio of 7:1 to 26,000 psi. This is intended to improve performance and fuel economy. Only at the tip of the injector does the system provide high injection pressure
An electronically controlled turbocharger adds engine responsiveness and efficiency by allowing an infinitely adjustable supply of air, acting like a small turbo for instant response at low speeds but operating like a large turbo when more airflow is needed at full power. A cooled EGR recirculates some of the exhaust gas into the engine intake to help reduce peak temperatures in the cylinder where nitrogen oxides are formed.