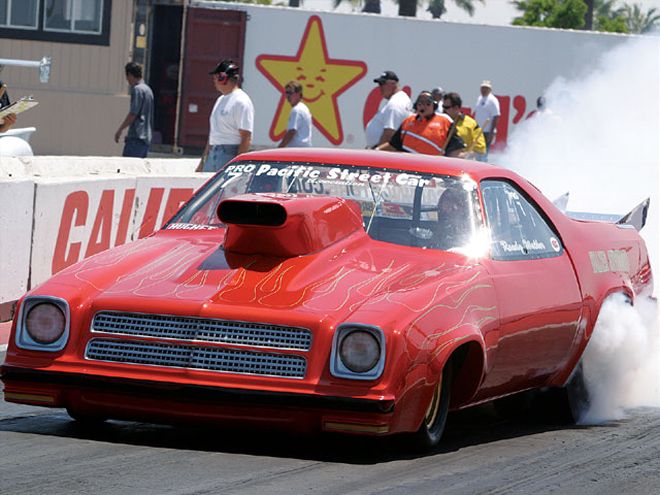
| improving Combusting Engine custom Car
Since the first combustion engine was built, we have been striving to improve its performance. To help understand the simplicity of a combustion engine, we need to think of it as an air pump. To increase the output of an air pump, it needs to be less restrictive when the air is going in and the exhaust exiting. Restriction is the major contributor to handicapping an engine's performance.
FOUR-STROKE ENGINE: 1. Intake Stroke (Intake Valve Open) 2.Compression Stroke (Both Valves Closed) 3.Power Stroke (Both Valves Closed) 4.Exhaust Stroke (Exhaust Valve Open) Four Strokes = 1 cycle of the engine. EZ Bolt-On Horsepower Components:1. carburetor, supercharger,2. intake manifold single-plane, dual plane, hi-rise 3. carburetor spacers4. fuel injection, throttle body, multi-port injection5. cylinder heads, cast-iron, aluminum6. rocker arms 1.5 - 1.87. camshaft8. exhaust manifold, tube headers, mufflers9. electronic ignition10. flex fan, auxiliary electric fan
What Makes It GoCarburetors have been the combustion engine's air/fuel distribution center for decades, controlling the air/fuel mixture on demand. As air enters the carburetor or carburetors-atop the intake manifold-the throttle plates are opened at the bottom of the carburetor; the engine's internal suction is created when the piston travels down the cylinder during the intake stroke. The suction draws the air/fuel mixture down into the intake manifold. The air/fuel mixture tumbles and swirls down the textured, equal-length runners of the intake manifold. The internal size and shape of the runners will control the air/fuel flow and velocity as it is directed to the intake valve ports, located in the cylinder head or heads. As the cylinder head intake valves open, the air/fuel mixture is drawn into the combustion chambers during the piston's down stroke. When the piston reaches the end of its intake stroke-known as bottom dead center (BDC)-the intake valve is closed. As the piston begins to travel upward during the compression stroke, the air/fuel molecules are compressed, and when the piston hits the top of its stroke-known as top dead center (TDC)-the air/fuel molecules are compressed to their maximum. The spark plug delivers a high-energy spark, igniting an explosion inside the combustion chamber, forcing the piston to travel down the cylinder producing a power stroke, which rotates the crankshaft. With the intake valve closed as the piston begins its travel up inside the cylinder the exhaust gases are compressed. The exhaust valve is then opened allowing the cylinder full of exhaust gases to be purged out of the cylinder and into the exhaust manifold or headers.
Intake Manifolds:There are three types of intake manifolds: single plane, dual plane, and high-rise.
A single plane intake manifold is designed with an open plenum directly under the carburetor/fuel injection throttle body mounting flanges. All intake manifold runners and engine cylinders share the air/fuel mixture from the same common plenum cavity.
Dual plane intake manifolds are also known as a two-plane intake manifold. This intake manifold design tends to be more throttle and torque responsive at low and mid-range engine rpm. The dual plane manifold is fed from half (one side) of a two- or four-barrel carburetor. Each plane feeds half of the engine's left or right banks. A plenum divider is used to isolate half of the carburetor from the other half of the manifold. The intake manifold runners are designed so that the cylinder's firing will draw first from one plane, then the other.
A high-rise intake manifold is designed to align the cylinder head port angle more directly with the intake manifold runner. This will create the straightest downward path, eliminating restrictions from the carburetor to the intake port.
Throttle Body:A throttle body is the air delivery component of the fuel delivery system for fuel injection. The throttle body is mounted atop the air-distribution manifold on a port injection system with injectors in the manifold close to the intake ports. The throttle body consists of a throttle lever, throttle plates, and a throttle position sensor. When the throttle is activated, the airflow is increased. Like carburetors, throttle bodies come in different air intake sizes, measured in millimeters (mm), to create more volume and a higher airflow rate. By creating a greater airflow rate, matched with the correct injectors, an increase in throttle response and horsepower will occur.
Electronic Fuel Injection (EFI):This has become today's fuel delivery system. The system is controlled by a computer module that monitors vital information gathered by a number of sensors in order to determine exactly how much fuel is required by the engine at any given time. After retrieving the information, the computer opens the injectors to get the correct air/fuel mixture into the combustion chamber. Electronic fuel injection has three components: a computer, sensors, and injectors.
Computer:Using the power of an integrated circuit board, the engine controllers will monitor everything from barometric pressure, ambient temperature, and throttle position. Each sensor determines just how much fuel the engine needs. The computer makes necessary adjustments accordingly.
Sensors:The information retrieved from multiple sensors located throughout the engine compartment is vital to the adjustments made by the computer. The basic sensors used in an EFI are rpm sensors, the manifold absolute pressure sensor (MAP), the mass airflow sensor (MAF), the O2 sensor, and the throttle position sensor (TPS). The coolant temperature sensor controls cold starting and an ambient air temperature sensor will change the air/fuel ratio according to weather conditions. There is also a barometric pressure sensor that measures the air density when driving at different altitudes.
Injectors:Following information received by the various engine sensors, the computer will decipher the information and precisely determine how much fuel is required for a given driving situation. The fuel injector operates by allowing a very specific amount of fuel into the combustion chamber according to the computer data. Most engines used today use one injector per cylinder. As the engine idles, a small plunger inside the injector opens at a given amount of time-referred to as pulse width-to allow pressurized fuel to flow into the combustion chamber.
A carburetor depends on a combination of engine vacuum and mechanical pieces to deliver fuel to the combustion chamber, making carburetion less accurate than a computer-controlled, sensor-activated EFI system.
Electronic Fuel Injection Improvements:The key to performance is maintaining the proper air/fuel mixture: not too rich, not too lean. You can't increase the engine's fuel delivery until you increase the airflow. Once the engine's airflow is increased, the fuel-delivery capabilities need to be raised. The factory injectors have a reserve capability that can sometimes be tapped into for increased fuel delivery. Larger aftermarket injectors with a greater delivery capacity will increase fuel flow, creating a better balance and greater performance.
Multi-Port Injection:These systems come complete with a high-flow throttle body intake manifold or fuel rails with injectors located precisely over the engine's intake valves for maximum power. An electrical control module monitors the engine's air/flow needs and controls the injector timing.
Cylinder Head:Aluminum cylinder heads are a major contributor to engine performance because they weigh less than cast-iron cylinder heads. Also, the aluminum material is denser than cast iron, which improves the internal port texture, creating better velocity and flow rate. Smaller-volume intake ports tend to be very responsive to filling the cylinder at mid-range and low engine speeds. Larger intake ports have a reputation of being sluggish and not as responsive. Let's classify a small intake port to a large intake port. A small intake port starts at 163 cc, which can be machined or ported to 180 cc, improving the port velocity. Intake ports between 180 cc and 195 cc will create more power in the mid range between torque and peak rpm. Large intake ports begin at 200 cc and continue up. These larger ports will become more effective during high rpm, but there is a trade off: less low-speed and mid-range power. When it comes to creating more horsepower with aluminum cylinder heads, it is not the port volume, but velocity and port flow that are important.
Pushrods / Rocker Arm (Ratio Geometry):The engine's pushrods link the camshaft's lobe profile to the rocker arms, which determines the intake/exhaust valves' timing: the distance between their opening and closing cycle. The length of the pushrod will dictate the valves' timing cycle.
The rocker arm is responsible for transferring the camshaft's lobe profile, which is linked by the pushrod, to the intake and exhaust valves. The rocker arm must have proper geometry to ensure the maximum benefit of the cam lobe profile design. The camshaft base circle, block deck height, cylinder head design, and lifter design all contribute to possible errors in the valvetrain geometry. Any valvetrain geometry error can be compensated by altering the pushrods' length.
When installing a longer rocker arm, it is also necessary to install the correct pushrod length. With a higher rocker arm arc, the pushrod needs to be moved closer to the rocker arm stud. It then becomes necessary to check the clearance between the pushrod and the head where the pushrod passes through the cylinder head. To ensure more clearance, a smaller-diameter pushrod can be installed.
By altering the valvetrain timing, we are giving the intake and exhaust valves increased time and distance, allowing a greater volume of air and fuel to enter the combustion chamber and then be exhausted.
Camshaft:The purpose of a camshaft is to time each valve opening and closing in relation to the piston and the combination process to every degree of the engine's 360-degree rotation. In order to achieve accurate timing, the camshaft's timing gear has to operate at exactly half the speed of the rotating bottom end.
Cam Lobe Lift: As the camshaft rotates, the cam lobe raises and lowers the pushrod, which also lifts and lowers the rocker arm, opening and closing the intake and exhaust valves. As the rocker arm is lifted, it multiplies the lobe lift by the rocker ratio that determines the actual distance the intake or exhaust valves are opened off of the valve seats.
Cam Lobe Duration is the duration of time a camshaft lobe keeps the valve open from the valve seat. When the time of the duration is increased, the engine's maximum top-end potential is increased. As the intake and exhaust valves are open longer, they allow a greater air/fuel mixture to be passed through the cylinder.
Overlap is the amount of time that the intake and exhaust valves in the same cylinder are both open simultaneously. Overlapping of the intake and exhaust valves is required to take advantage of an engine's maximum potential.
Lobe Separation Angle: When speaking of lobe separation angle, we are referring to the amount time between the intake and its maximum lift and the exhaust at its maximum lift. Both of these maximum lift movements of the intake and exhaust valves are in conjunction to the camshaft's duration, which determines the amount of time it takes the lifters to travel to and from their maximum lift points.
Exhaust System:When the piston approaches top dead center, the spark plug fires, igniting a fireball just as the piston rolls over, beginning the power stroke. The piston transfers the energy of the power stroke to the crankshaft as the exhaust valve begins to open during the last portion of the power stroke. The exhaust gas pressures are up around 70 to 90 psi, causing a rapid escape of the gases. As the valve is opened, it causes a pressure wave that continues to increase as the vales open. Exhaust gases can travel at a high velocity, more than 350 feet per second, but the pressure waves travel at the speed of sound (761 mph at sea level).
Exhaust manifolds are the most hindering factors to the exhaust system's overall perfromance. As the gases are purged from the exhaust ports and enter the exhaust manifold, the exhaust gasses are directed to make an abrupt 90-degree turn before impacting the outside internal wall of the exhaust manifold. This action disturbs the exhaust flow, the pulsation rate, and the velocity of the exhaust gasses, causing restriction and backpressure, which mean loss of torque and horsepower. The exhaust system is the one performance segment that cannot be restricted for optimum power to be produced. The best-flowing factory exhaust manifolds is the Ram Horn. This design has a smaller degree angle, creating less reflection of the exhaust gasses when exiting the cylinder heads exhaust ports.
Headers: Headers produce the most efficient power gain in the exhaust system. They empty the exhaust gasses from the cylinder head exhaust ports with less restriction than that of an exhaust manifold. As the gases travel through the individual primary tubes, they merge at a cone-shaped collector. As the gasses merge together, a low-pressure area is created where the primary tubes come together, affecting the exhaust gasses' flow rate and velocity. A larger tube known as the "collector" intersects and merges with the header's primary tubes. The tubes are cut at an angle, and as the tubes come together, the points of each primary tube form a cone shape. The length of this cone will direct the exhaust gasses and affect the low-pressure "scavenging" area of the collector, determining the exhaust gas pulsation rate and velocity.
There are two schools of thought when it comes to collector designs: A large collector doesn't restrict the flow but tends to cause some scavenging due to the low-pressure area where the individual exhaust gases exit the primary tubes and come together.
Another theory of collector design is to reduce the diameter size of the collector before it flows into the exhaust pipe. As the air passes through the small center section, a venturi effect occurs: The gas flow velocity is increased, improving the scavenging of the exhaust, meaning a higher air/fuel mixture can be pulled into the combustion chambers. More fuel means more horsepower as long as everything else is optimum.
Mufflers: Mufflers are installed into the exhaust system to decrease the velocity of the exhaust gas flow, increase backpressure, and isolate sound waves. When it comes to performance, the ultimate would be no muffler at all. A quality performance muffler will reduce engine noise without generating excessive backpressure or choking the engine. Increased backpressure can rob the engine of 30 to 40 horsepower.
Performance mufflers are designed with a straight-through, perforated tube wrapped with fiberglass, ceramic, or stainless steel packing to absorb sound. Other designs feature unique baffles and plates within the muffler chamber to deflect the sound waves. Another design is a 180-degree muffler, which directs the exhaust gasses 180-degrees out of phase so that when the sound waves collide, they cancel each other out.
In today's high-performance aftermarket, there are many ways to create overall torque and horsepower from an engine without tearing it down for a complete rebuild. By purchasing bolt-on engine components, the sky's the limit to creating kick-butt horsepower.