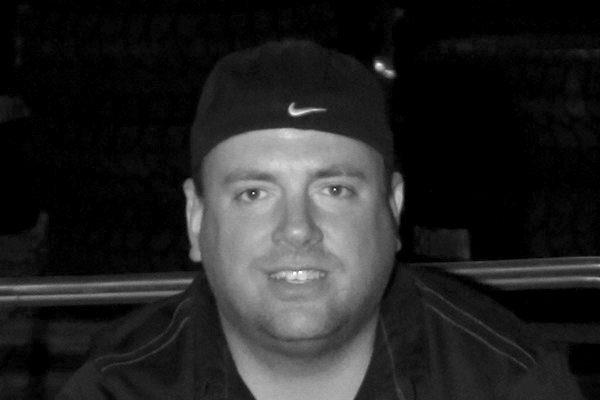
Pete Trasborg
Brand Manager, Jp
After six days on the Rubicon Trail, playing here and there, camping at the springs, and wheeling back out past Loon Lake, we hit the road at about ten o’clock at night heading to our hotel about 60 miles away. We had planned to go out through Cadillac Hill and end up at Lake Tahoe, so that’s where we reserved our hotel. We knew we’d be on the trail all day long and at best would be hot, sweaty, and tired. Instead, we had an even longer day on the trail, and then got to run about 50 miles of highway to get to our hotel or lose the money from the reservation. Of course, as soon as we hit the road, we were greeted with a new vibration and a noise that we’d never heard before.
The Jeep was caked in trail mud, but we dove underneath and started investigating all the usual suspects—to no avail. Then, dirtier and even more tired, we hit the road, keeping our ears peeled for the noise getting worse. We got into the hotel at around 2 a.m. with nothing going boom and just crashed. First thing in the morning, we pulled a week’s worth of camping gear from the back of the Jeep to get to our tools and started testing and pulling parts to find the problem. We eventually discovered that the factory front driveshaft’s double-cardan joint bit the big one after 140,000 miles and a decade of hard wheeling. We pulled the shaft, but still had a vibration which we eventually discovered was a bad axleshaft U-joint. We decided it was time to go retro with this Jeep.
We turned to Omix-Ada for a hub lockout kit. Now, with a simple flip of the switch, we can stop the entire front end spinning. Sure, it means we have to get out of the Jeep to actually have 4WD, but after that trip we think it is worth it. Another added benefit of disconnecting the front end should be a mileage gain, but one benefit we are sure of is that without those parts spinning all the time, everything will last longer.
The kit replaces the unitbearings with spindles and serviceable bearings. If you are the kind of guy who thinks “grease gun” is a dirty word, this probably isn’t for you. Unlike unitbearings, the new wheel bearings might need attention from time to time. But, we like being able to check that sort of thing rather than just running it till it dies, and we have several grease guns, so we are good to go. Also, the kit replaces the factory shafts with chromoly ones for a huge increase in strength there.
We didn’t want to change our 5-on-41⁄2-inch bolt pattern, and we didn’t want to mess around with custom machining brake rotors like some 5-on-51⁄2-inch lockout kits force you to do. So even though it isn’t as strong as the bigger bolt pattern might be, the company rates it to a 35-inch tire, which just happens to be the size that we were running. The kit includes chromoly Alloy USA shafts, some cool Alloy USA U-joints, and all the parts needed for installation. Once we had that installed, we turned to Tom Wood’s Custom Driveshafts to replace the non-greasable factory one. Here’s how it all turned out.
Step By Step

This Jeep has been wheeled, so after wire brushing the mud away from the unitbearing and hosing it down with penetrating lubricant we still couldn’t break the bolts loose without using the trusty double wrench trick.

This kit is incredibly complete, but there is some assembly required. While the instructions state to use a hydraulic press and a special aluminum tool for this particular bearing, we had neither. So, instead, we used a brass drift while sitting in our driveway.

After seating the inner and outer bearing races, we packed the bearings by hand (yeah, don’t have that tool either) with Royal Purple’s Ultra-Performance grease. This stuff is so sticky it makes marine grease look like eel snot.

The kit comes with both regular C-clips and full-circle C-clips. Since the new chromoly shafts were machined for the full circle clips, that’s what we used. Another neat thing is that Omix included five clips per U-joint. Yeah, apparently that company has experienced the unidentified flying C-clip phenomena.

We had the first U-joint in the axle by the time we went looking for the clips. We found the full-circle clips (which hold the joints in way better) and knew we had to use them. So, we got to pull the U-joint out of the axleshafts. Remember no press? Our brass hammers and drifts hate us.

We rediscovered this trick on the second lap. In a pinch you can use a vice as a makeshift press. Also note that the U-joint caps all feature holes: those are for zerk fittings. We should never have a problem with dried-up and powdered bearings in these axleshafts.

We didn’t want to pull the ARB Air Locker and ring gear out of the pumpkin. Instead, we vacuumed out the axletubes to get the extra dried-up mud out of the tubes after wire brushing them. Don’t tell the girlfriend.

The spindle is custom-designed to bolt into the unit bearing spot on the outer knuckle. We had to fish through several drawers of sockets before finding on that would allow us to drive the captured needle bearings into the spindle.

Once the spindle was ready to go, we got back to our rotor. The hub was pressed into the rotor when we got it, despite the instructions telling us to do so. We put the packed inner bearing in, and gently drove the inner seal home.

We couldn’t get the metal dust shield onto the outer axleshaft to save our lives. Maybe we should pick up a press. We ended up heating it up with a propane torch. Because we were doing the install on a 40-degree day, that was enough to let us gently tap the dust shield onto the shaft.

You need to reuse your factory bolts. We applied a small dab of red-tinted thread locker to them. But once they were in and tightened to 75 lb-ft, we were worried they would interfere with the rotor turning. After a quick test assembly and rotor spin, we had no problems.

The spindle nut socket on the right is the one that was included with the kit. The silver thing is the spindle nut included with the kit. Fortunately, one tool we did actually have was the spindle nut socket on the left. We prefer this newer style of spindle nuts to the older, hex-shaped ones.

Just like Dana 44s and Dana 60s, now our Dana 30 gets the inner nut torqued to 50 lb-ft. Then the lock washer goes in. And the outer spindle nut gets torqued to 150 lb-ft. While the instructions state 125 to 150 lb-ft, we found it easier to keep it the same as the other Jeeps and went right to 150.

The lockout hub just slides on over the studs and then the tire goes back on. Once we were done with that, our new Tom Wood’s driveshaft finishes off the fix. The double-cardan in this shaft is cold-forged, not cast like the factory one, so it runs cooler and lasts longer. It’s also greasable. While we were at it, we upgraded to a U-bolt style pinion yoke—also from Tom Wood’s.