If you build your own engine, you'll want to cover these important steps with your machine shop when preparing your block.
A new engine block is fantastic to work with, but they can be a bit spendy, and are only offered for a few popular platforms. Most engine builds in the rodding and restoration world rely upon original un-reconditioned blocks, which means working with a machine shop to bring decades-old factory castings with iffy tolerances and unknown abuse up to spec. Sounds scary, right?
That's why it's important to work with a reputable and qualified machine shop to ensure that your block comes out with better specs than it had originally. That's not a tall order considering how far off from ideal most vintage blocks tend to be. Remember, most of what we use for hot rodding fodder was originally cast and machined with much looser tolerance than what would be considered even marginally acceptable today. Uneven bores, and out-of-square blocks are not uncommon, especially the further backward in time the date of production.
So what magic goes on in a machine shop to take a hunk of heavy, hard cast iron, and what are these "specs" we speak of? No worries hot rodders, we're about to give you a primer on what a block goes through on its resurrection to buildable status. The most important thing to take away here is that you don't have to be a trained machinist to have a solid grasp of what goes on in a machine shop. And armed with that, you'll have the very best thing you can walk into any machine shop with: the knowledge of what they do, why they do it, and what to look for in terms of equipment.
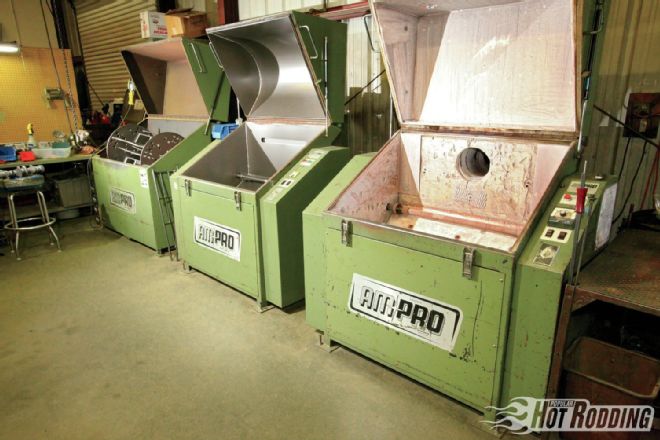
1. Before They Start - Getting the gunk off is the first step to reusing any old block; at home that means using stuff like chemical degreasers. A machine shop, however, will use an arsenal of tools to clean a block to the point where there is nothing left but iron. This can include chemical tanking with hot water or solvents, thermal cleaning, tumbling, and shot peening.
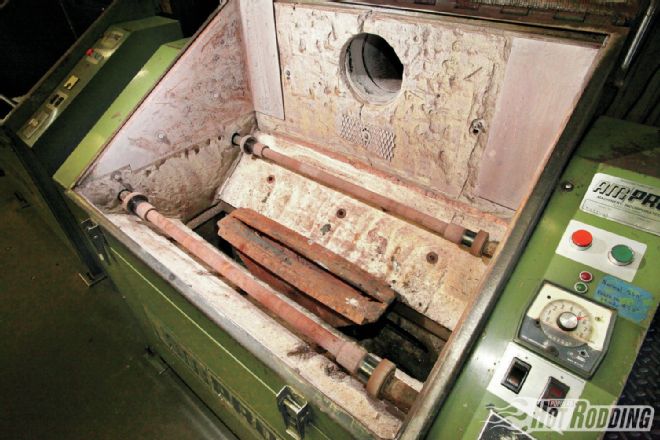
2. Thermal Cleaning - Thermal cleaning is pretty much exactly what you’d expect; the block is loaded into a large oven and baked at a temperature of about 500 degrees. The heat burns off all of the oil, grease, carbon, old paint, and other residue that simple washing won’t remove. Think of it like the self-cleaning cycle on your home oven. Once it’s done here, we’ll be back to clean cast iron.
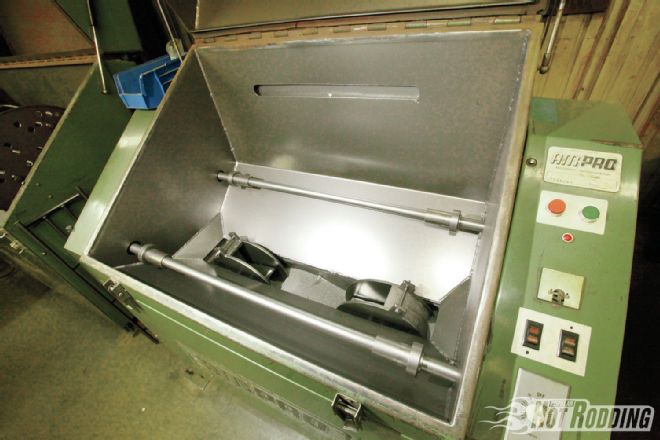
3. Shot Peening - Shot peening involves firing thousands of tiny steel pellets at high velocity at the block. (Note the high-speed blast wheels.) While thermal cleaning will get all of the goo, shot peening will remove surface contamination such as rust, scale, and even some small irregularities in the casting to create a clean and smoother surface finish. More than simple aesthetics, shot peening makes it easier to detect surface and subsurface defects. The same process also acts like mini ball-peen hammers pounding away that the block to impart additional strength through compression.
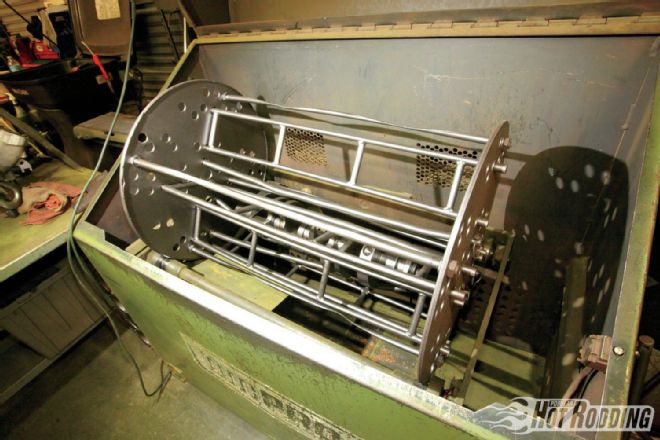
4. Tumbling - Once the block has been shot peened, it spends time in the tumbler to work out all those tiny particles that have been fired at it. It’s not a particularly technological stop, but it is a critical one since more precise machine requires zero remaining debris.
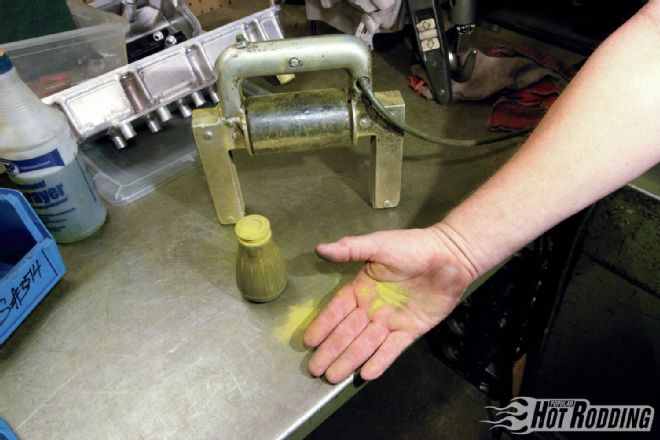
5. Magnafluxing - Magnaflux is actually a brand name of the Illinois Tool Works, and is one of several types of Magnetic Particle Inspection (MPI) systems, but it is so widely used that “magnafluxing” has become the slang term for the process. To locate cracks too fine to be detected with the naked eye, you can expose the block to a strong magnetic field and apply a ferrous metal dust. The dust is attracted to the pole ends of a magnet, so if a crack exists, the dust will gather around it. This is one of the most critical steps on a vintage block since hairline cracks are common. The key thing here is to identify an unusable block before additional operations are performed.
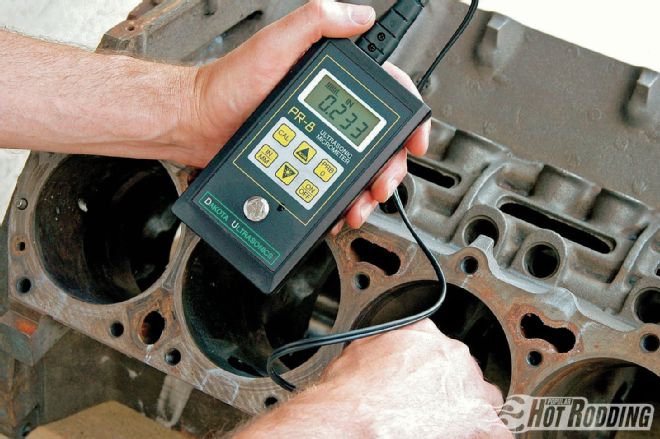
6. Sonic Checking - Sonic checking—an ultrasound process—is employed to find thin areas of a block that are inaccessible to conventional measuring equipment. Cylinder walls are the most commonly inspected areas since core shift can render a block unusable. To find any hidden thin spots, a probe is placed at the area to be checked, and electronically generated sound waves are passed into the block. Those sound waves are reflected back to the probe and the amount of time required is converted to a dimension by the device. Different blocks have different minimum specs, but the key idea is that higher power levels will require thicker cylinder walls. Some types of cylinder blocks, for instance production 400ci small-block Chevys or small-block Fords, should be measured before receiving any appreciable increase in bore when horsepower is expected to rise significantly.
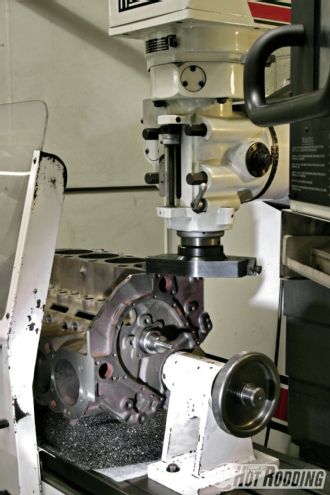
7. Deck Surfacing - The sealing surface of the block is the most critical gasket surface in an engine. That’s especially true when mating aluminum to iron due to the different expansion rates. Historically, the recommended surface finish was 60 to 120 micro-inches Ra (roughness average) with cast-iron heads, or 20 to 50 micro-inches Ra with aluminum. Modern high-quality milling machines, like the Rottler shown, can achieve really low Ra numbers which work nicely with multilayer steel (MLS) head gaskets. Paul Higgins of the University of Northwestern Ohio says they prefer to run in the range of 15-20 Ra with MLS gaskets for either cast iron or aluminum heads. Most importantly, however, deck surfacing ensures that the cylinder volume and compression are consistent from hole to hole. Older engines that were originally mass produced on a transfer line are notorious for wide variations between cylinders. When the power level rises, discrepancies in volume and compression between cylinders can cause all kinds of headach
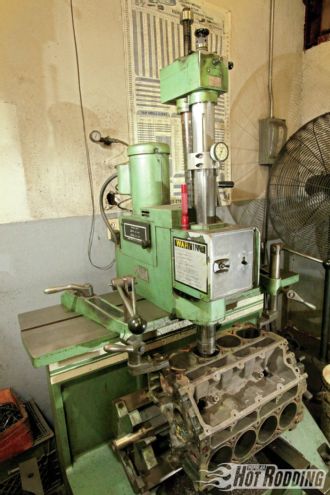
8. Cylinder Boring - For the most accurate cylinder boring, the block needs be located off the crankshaft centerline to ensure that cylinders are bored exactly 90 degrees perpendicular to the crankshaft. Jon Kaase of Jon Kaase Racing tells us that on vintage blocks it’s not uncommon for cylinders to be slightly angled or for one cylinder to require a larger overbore due to damage. Thanks to modern custom pistons, it’s possible to simply bore the single damaged cylinder out further and use a different size piston versus boring all the cylinders to their maximum. Kaase has done this with a valuable vintage Boss block recently. “The engine doesn’t care what size the bores are,” Kaase stated, “as long as everything is balanced.”
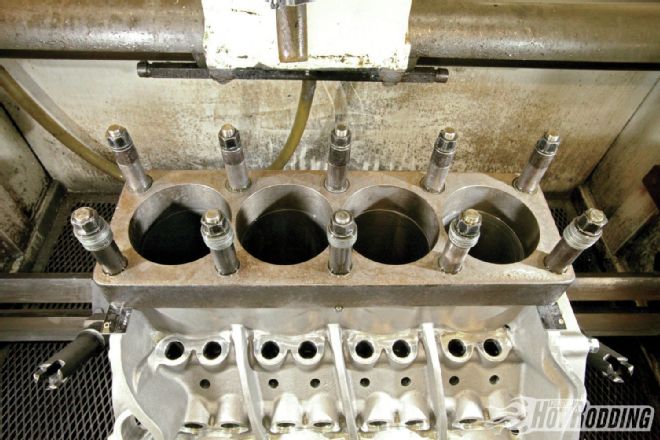
9. Torque Plates - An engine block may seem completely inflexible, but studies performed by gasket companies and aftermarket engine block manufacturers have proven that even the best blocks are slightly distorted by torqueing down the cylinder head. To emulate that distortion, a thick steel plate called a torque plate is torqued down on the block with head bolts. This allows the block to be close to perfectly cylindrical once the heads are bolted on.
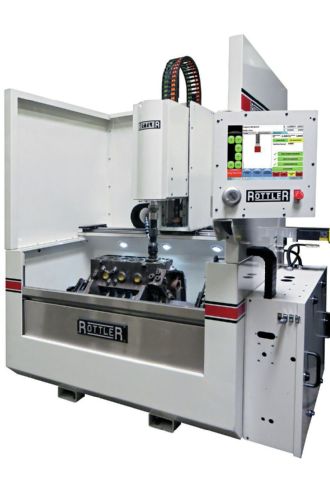
10. Cylinder Honing - Most machinist shops will bore the cylinders to within 0.004 or 0.005 of the final bore size to account for the material that honing will remove. “Ring and boring technology has improved a great deal in the past few years,” Chris Bennett of the School of Automotive Machinists told us. “Cylinder walls can be slicker, and modern 1mm rings can be used even in vintage engines.” The ring pack needs to be decided upon before the machine shop performs the honing so that the machine shop can tailor the grit of the stone to the proper bore surface finish. This is imperative if the rings are going to seat properly.
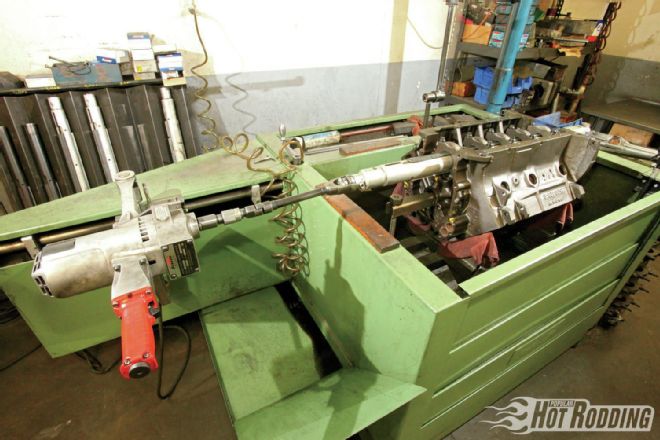
11. Align Honing - Align honing the crank centerline ensures that the main bearings and crankshaft race have a perfectly aligned and concentric path for the crank to spin inside. Align boring—different from align honing—should only be done if measurements determine it is absolutely necessary to achieve alignment and concentricity. Align boring requires the main caps to be cut, so the resulting bore operation causes the crank-to-cam centerline distance to be slightly less. This necessitates an undersized timing chain, which may or may not be available for your engine family. Align honing is preferred, and gets the job done 99 percent of the time.
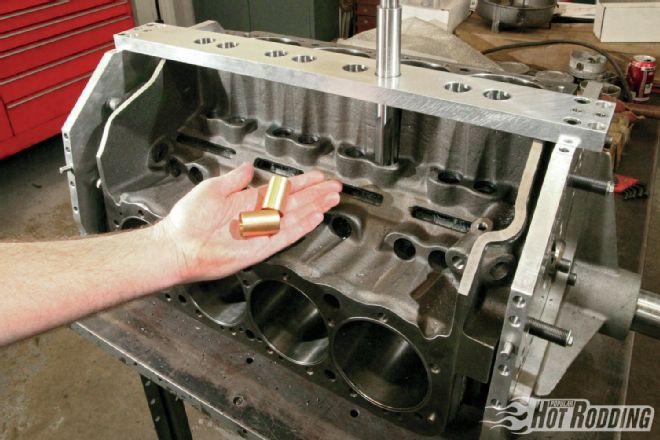
12. Lifter Bores - Lifter bore diameter is one of the most critical dimensions on a block, and occasionally a block will need one or more lifter bores to be sleeved with a bronze guide and honed to size. Moreover, high-lift flat-tappet cams with aggressive lobes can benefit from larger diameter lifters, which require a boring, sleeving, and honing procedure shown here. Paul Higgins, instructor at the University of Northwestern Ohio, tells us that lifter bore diameters vary greatly, even in the same engine family, depending upon when the block was produced. His maximum acceptable tolerance for engines built at UNOH would be in the .010-.012 range.
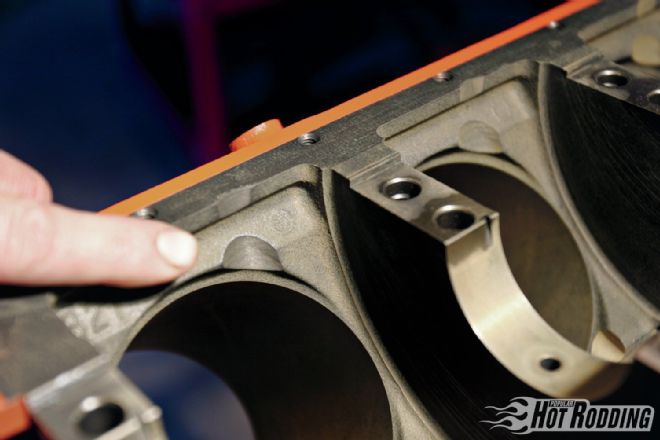
13.Stroker Clearance - If rebuilding a stock engine, a stroker rotating assembly will give you a significant power boost with almost no increase in cost, so we almost always recommend going for more. Depending upon the block, a stroker kit may require some clearancing at the bottom of the cylinders to make way for the rod bolts due to the longer throw of the crank. While the DIY guy can do this at home using caution, many machine shops can perform all or most of the operation for you.

14. Final Cleaning - Once all machine work is finalized, the block goes through a thorough blowout, steam cleaning, and drying to ensure all debris from machine work is removed and the block is ready to go into a clean room for final assembly.