The carbureted car and truck era phased out by the early '90s. Carbs are still in use today on a few motorcycles, lawn mowers, and other power equipment, but electronic fuel injection (EFI) is standard equipment on almost everything we drive. So we're going to review EFI's basic operation, the different types of systems, and more recent technology.
Let's start from the beginning with a refresh on carburetors. Carbs were produced in numerous shapes, sizes, brands, and models, with some bolted on top of a V-8's intake manifold, others mounted directly to the rear of a motorcycle's straight-four cylinder head. There were single-barrel carbs, two-barrels, and four-barrels, with performance configurations like dual quads (two four-barrels), a six-pack (three two-barrels), and so on.
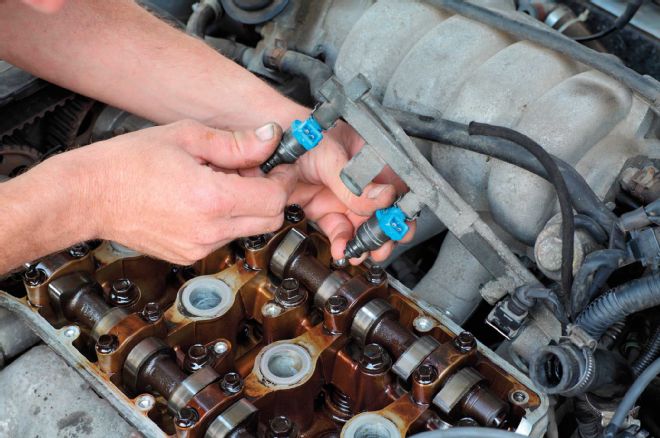
| It's important to have a basic understanding of fuel injection systems when you work on modern pickups. Sequential fuel injection systems, as seen here, are currently the industry standard.
Each carburetor's barrel is a focal point. This is where air flows through the throat of the carb and into the engine. Airflow is regulated by the carburetor's throttle plate, opened and closed by means of a cable routed to the accelerator pedal. Each barrel utilizes the physics of what's known as the venturi effect. The inside diameter of each barrel is narrower in the middle, compared to the top and bottom. This design speeds up airflow and creates an area of low pressure. This low air pressure draws fuel up from the carburetor bowl through passages, where the fuel mixes with air forming a mist (atomization). This air/fuel mix, which is ideal for combustion, travels through the intake manifold and past the engine's intake valves, then is compressed by the pistons and ignited by sparkplugs.
Carburetors, in some respects, are more complex than fuel injectors. Some use a secondary venturi within the primary of the barrel. There are variable venturis; high numbers of air and fuel circuits and jets; variable jetting with metering rods, calibrated automatic choke, and cold-start enrichment setups; and idle control linkage arrangements. Even computer-controlled carbs were on the market for a period of time.
Electronic Fuel Injection (EFI)
As opposed to a carburetor, which mixes fuel with air by means of a venturi, a fuel injector requires high fuel pressure. This pressure is typically delivered from the tank by an electric fuel pump. The injector itself is a simple electric solenoid (open/closed valve), which is normally closed, that opens with power and ground applied. With a specific amount of fuel pressure at the input side of the injector and the solenoid activated (open), fuel is put out through a nozzle in a fine, umbrella-shaped spray pattern. This process provides better atomization of the fuel, which improves combustion.
The leading advantage of EFI is its precise control of fuel delivery to reduce tailpipe emissions while improving both performance and fuel economy. Each injector receives power with the ignition on, but the on/off command that completes the ground side of the circuit is applied by the Powertrain Control Module (PCM) in a rapid pulsing fashion. This is referred to as pulse width modulation, or the amount of time the injector is commanded on in milliseconds. The duty cycle is the ratio of on time compared to off. A 60 percent duty cycle means the injector is commanded on, injecting fuel 60 percent of the time.
The textbook air/fuel ratio is 14.7:1 (stoichiometric mixture). This is where combustion burns almost 100 percent of the fuel entering the engine. As we've learned from many other automotive electronic systems, three basics are required: data input, an electronic control unit to decipher the data, which is finalized by accurate output commands from the same ECU.
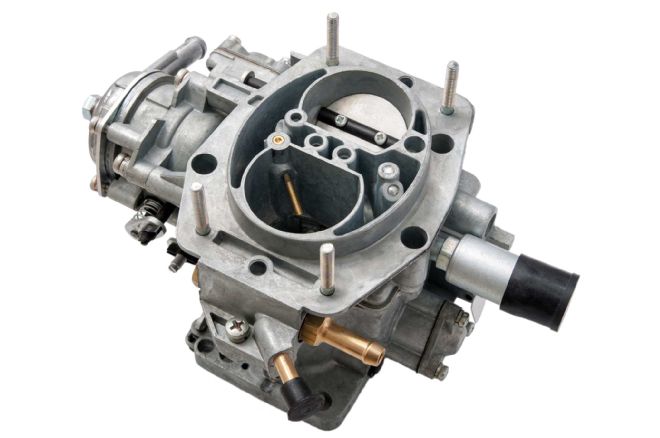
| Throttle-body fuel injection is best thought of as a transitional technology between carburetors and modern port fuel injection.
Data Inputs for EFI Control
- Crankshaft speed/timing
- Camshaft speed/timing
- Mass airflow
- Manifold absolute pressure (vacuum)
- Exhaust oxygen content
- Intake air temperature
- Coolant temperature
- Throttle position
- Barometric pressure
- Evaporative emissions canister purge status
- Fuel pressure
The PCM processes incoming data and commands the appropriate duty cycle to the injectors, attempting to stay as close as possible to a stoichiometric mixture. This is accomplished at a high rate of speed in order to maintain an optimal air/fuel ratio under various driving conditions. Usually, cruising at 55 mph on the highway under light throttle is as efficient as it gets. Punching the gas pedal to the floor requires a much higher duty cycle to provide full power under high demand. Oxygen sensors, interpreting air/fuel ratio by the amount of O2 remaining in exhaust gasses, are critical in fine-tuning fuel distribution and maintaining an elite level of fuel economy and low emissions.
Single-Point Injection
At first glance, early mass-produced electronic fuel injected engines looked very much like they were carbureted. Single-point injection used a throttle body unit similar in base-structure to a carburetor, including a throttle plate(s) to control airflow, but with one or two extra-large fuel injectors mounted on top. The atomized fuel then traveled through the intake manifold's runners to each cylinder's intake valves-just like a carburetor. Single-point injection made economic sense because older carbureted intake manifolds could be used with light modifications. The throttle body unit also incorporated an idle air control valve (IAC) and a throttle position sensor (TPS). One of the few throttle body performance setups, Cross-Fire Injection, was produced by GM from '82 to '84 on some 5.0L and 5.7L V-8 Corvettes, Camaros, and Firebirds. Two throttle body injection units were affixed to a modified intake manifold, each feeding the four cylinders on the opposing side of the engine-therefore, Cross-Fire.
Multiport Fuel Injection
Multiport injection is the basis of today's EFI systems. An individual injector is provided for each cylinder, located in the intake manifold just before each intake valve. The input ends of the injectors are connected to a common regulated fuel rail, so the sole high-pressure pump can deliver fuel across the board. And there's still a throttle body regulating airflow at the main entry to the intake plenum. The plenum is a chamber between the throttle body and where the manifold runners split up to each intake port of the cylinder head. The throttle position sensor and idle air control valve are still incorporated with the throttle body, along with a manifold absolute pressure sensor on some applications.
Early multiport systems used a batched injector command (meaning the duty cycle was applied to the injectors in groups) or simultaneous, in which all injectors were opening at the same time. This process would accumulate fuel on the back of each intake valve until that cylinder reached its intake stroke. The intake valve would then open and allow entry of the calculated air/fuel mixture. More current multiport systems take advantage of sequential injection. This enables each injector to spray fuel in the engine's firing order, while the PCM varies spray-timing with its designated cylinder's intake stroke. This technique is very similar to spark timing, where the plug fires in advance of the piston reaching top-dead-center of its compression stroke.
Direct Injection
Direct injection implies just that. More robust fuel injectors are mounted in the cylinder head and inject fuel under extreme pressure directly into each cylinder's combustion chamber, eliminating any fuel delivery through the intake manifold (upstream of the intake valve).
Just like all forms of internal combustion engine fuel delivery, the ideas and earliest direct injection systems go back more than a century.
Diesel Direct Injection
When discussing direct injection, mass production has always focused on diesel engine applications. Lower-compression gasoline engines allow the air/fuel mixture to enter the cylinder past the intake valve, compressed by the upcoming piston and then ignited by a spark. High compression diesel engines (no spark) use the heat developed from the compression of air to ignite the mixture. Therefore, the fuel must be injected at precise timing with the compression stroke. Otherwise the air/fuel mix would ignite too early and trash the combustion process.
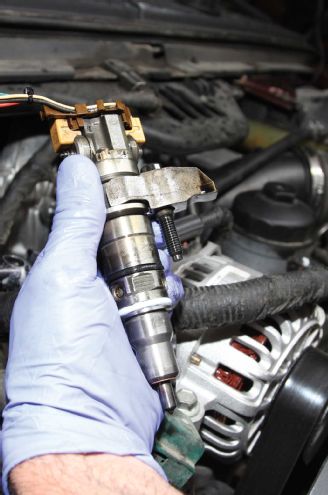
| High-pressure common-rail diesel injectors are very precise and very expensive. Seen here is one from a Ford 6.0L Power Stroke.
The most common means of automotive diesel injection for many years was mechanical, with the use of an injection pump. Just like a spark-engine's distributor, the injection pump is driven by the crankshaft/camshaft. As the pump rotates, it applies bursts of fuel past spring-loaded injectors calibrated to open at a specific pressure, in time with each cylinder's compression stroke. The fuel ignites the moment it reaches the combustion chamber. Unlike gasoline engines, diesels use a wide-open air intake (no throttle body), and engine speed is controlled strictly by fuel delivery.
Modern diesel engines use complex electronically controlled systems utilizing the age-old basics. The high fuel pressure is still supplied by a mechanically driven pump, but the injectors are now PCM-controlled electronic solenoids. Many additional data inputs are used in the algorithm, and both fuel pressure and injection timing are dynamically applied, with fuel pressure at the injectors reaching as high as 36,000psi.
Gasoline Direct Injection
Automakers are in the early stages of a gasoline direct injection transition, just like we moved on from carburetors to EFI. The technology has been out for quite some time. About 15 years ago we questioned a GM engineer on the delay of gasoline direct injection production. GDI was already known to improve both performance and fuel economy, so the answer was simply "cost". Heavy-duty injectors, which can hold up to high fuel pressure, combined with extreme combustion pressures and heat, were expensive. Plus a much higher-pressure fuel pump with matching pipes and rails had to be added to the standard multiport injection configuration.
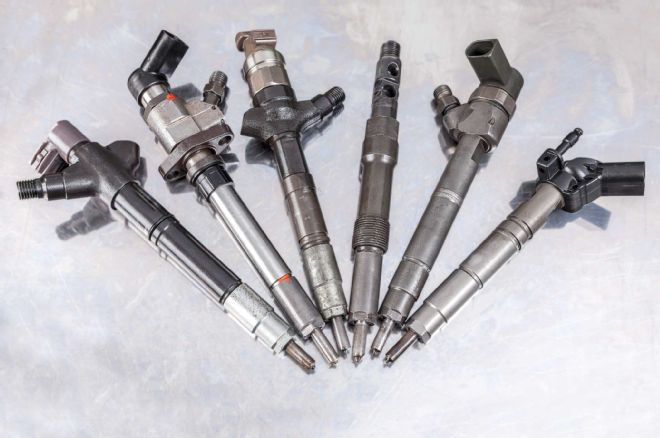
| While diesel engines have had direct injection for many decades, it's a fairly recent development on gasoline engines.
Electronic throttle control is currently standard equipment on most production multiport-injected cars and trucks and will continue with GDI.
Multiport injection fuel pressure can vary in the 35-65 psi range, supplied by the electric motor driven pump in the tank. That same device is considered a fuel feed pump for direct injection. A lot like diesel injection, the electric pump now feeds a volume of fuel under moderate pressure to a hydraulic pump driven by the crankshaft or camshaft. The mechanically driven pump can output 500-3,000 psi depending on engine speed. With the optimum pressure directed to all injectors at the fuel rail, the duty cycle command is applied to meet the driving condition. GDI edges out multiport injection with more accurate timing of fuel direct to combustion, without the external delay of the intake manifold. Direct injectors often use nozzles, which aim fuel to deflect off the piston-top architecture and create turbulence for a more efficient burn.