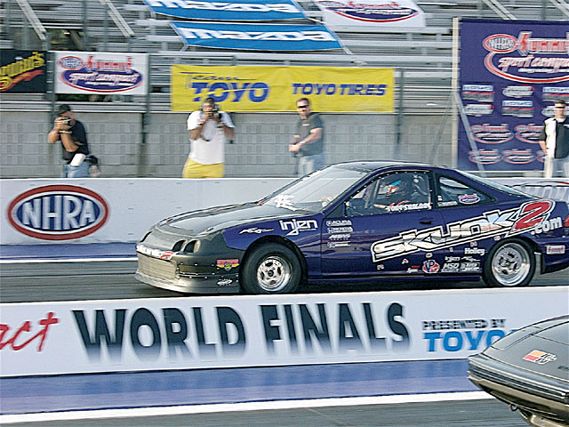
Skunk2 has some secrets to share and it's ready to tell the world. Divulging secrets is an anomaly in an industry characterized by closely guarded shops and companies that don't want even a whiff of their production practices publicized. After all, if company Y discovers how company X makes power, then company Y will copy company X and steal its business. There's some truth to it, but it nonetheless makes for a competitive environment without much unity or cooperation. Where's the love?
Skunk2, a company with a long-standing history of innovation, is throwing caution to the wind and releasing its secrets for the B-series engine. Skunk2 is revered for its horsepower-producing, all-motor vehicles, particularly those using the Honda B-series platform. People have long wondered how Skunk2 puts down such impressive dyno numbers, all the while on naturally aspirated engines in this age of turbo power.
The company is now ready to face the world and explain its strategies. Turbo was fortunate enough to soak up this knowledge and pass it on to our readers. Skunk2 is confident of its products and racecars and isn't afraid of revealing industry secrets; it's not known to back down from such risk-taking ventures.
Our day began in the farmlands of Norco, Calif., at the headquarters of Skunk2 Racing. For those who think the Los Angeles area is all fake tans and convertibles, drive an hour out of town and you can hang out with the cows as if you're in Wisconsin. By the time we rolled up to Skunk2, we were thanking the air conditioning gods because the weather was scorching.
Frank Balogh, the marketing director, and Dave Hsu, the managing director and Skunk2 mastermind, took us straight to the workshop. Engineers were working furiously on the yet-to-be-seen RSX racecar. Also in the facility were the DC2 front-drive racer and the Civic RR, which were at various stages of build.
We sat down with Dave and pumped him for all the information he had on the B-series engine.
Turbo: Dave, why share Skunk2 B-series secrets with the racing community? Are you guys leaving racing?
Dave: That is so far from the truth. We've been in hibernation, but have been busy at work building a new RSX racer. Also, we're comfortable with our development with the B-series engine and we've moved on with development on the K-series engine.
T: So will the original DC2 racer still be using the B-series engine or the K-series engine?
DH: Both the RSX and DC2 will be using the K-series engine.
T: Where do you get your inspiration for building a high-output, normally aspirated engine?
DH: The obvious inspiration is F1. For example, most of us are revving our normally aspirated drag race engines at about 10,000 rpm. The F1 guys are taking their engines to 19,000 rpm. And they're generating 300-hp per liter compared to our World Challenge engine that makes about 150-hp per liter. So we're quite a ways off from F1 standards.
T: Since you brought it up, let's first start with Skunk2's B16A Speed World Challenge engine. Does the B16A utilize all stock parts?
DH: Yes, we use factory pistons, connecting rods and crankshafts. However, all the components have been thoroughly massaged.
T: What do you mean by massaging?
DH: For starters, any endurance engine must start off with a good bottom end. We balance and blueprint the entire bottom end, check all the clearances on the bearing and usually try to build a slightly looser-than-stock-specification engine.
The pistons' valve pockets are fly-cut to allow for greater valve clearance so we can run larger cams. Not many people know this, but the factory Honda pistons are incredibly durable and the piston-to-wall clearance is extremely close, about .0015-inch, compared to many forged pistons that require much more clearance.
The key to building a high-output engine is containing all the compression gases within the combustion chamber prior to ignition. The ring tension is only about 10 pounds so trying to contain several hundred psi of compression with 10 pounds of ring tension isn't that easy. The next logical choice is to run extremely tight piston-to-wall clearances. The cylinder walls must be extremely cylindrical so the pistons ride smoothly along the walls. We usually outsource the coarse machine work and perform the final machining in house.
T: Let's move to the top end. What modifications do you perform on the head?
DH: We start with a stock B16A head and then port and polish the cylinder head. The factory head flows extremely well and we only perform small amounts of porting, especially around the fin area and valve pocket seat. The fin area that separates the runner into the two valve faces needs to be narrowed, and the valve pockets need to be ported for better flow. The rest of the area needs to be polished for smoother flow.
We also mill the crap out of the cylinder head to reduce the combustion chamber volume. We mill the B16A head about .080 inch, which transforms the original B16A circular combustion chamber into one similar to a GS-R, a squared combustion chamber. That's why it's important to fly-cut the pistons so the valves don't hit the pistons.
The most important part of the cylinder head is a good valve job. It goes back to cylinder sealing. The more pressure you can seal within the combustion chamber in the compression stroke, the more power is generated when the mixture is ignited. The head is obviously outfitted with all Skunk2 vavletrain hardware that includes stainless-steel valves, high-tension dual-valve springs, titanium retainers, Stage 3 camshafts and adjustable cam gears.
T: We notice you didn't mention cutting the portion of the valve guide that sticks out of the head. What's your take on that?
DH: We do see better flow with cutting the guides, but reliability issues are also of concern. The guides are so short that oil leaks are more common through the guides, so we choose not to cut them.
T: Any work done on the induction end?DH: We use a Type R manifold that's extrude-honed and mated to a 66mm Skunk2 throttle body.
T: With all the information you told us, anyone can build a 252-hp B16?
DH: I wouldn't say anyone. The combination has been good on the engine dyno for 252 hp and on the chassis dyno for 210 hp. The engine is at about 12.0:1 compression, so race gas is a must. It's not your ordinary street engine.
T: Moving on to your B-series drag engine that you used in Project Beta (DC2 Integra): What was done on the bottom end?
DH: First, we started with a B18C bottom end because of its structural integrity compared to the LS. The block was bored to 86mm while using a 95mm crankshaft from a 2.0-liter Prelude engine. The combination computes to a 2.207-liter engine.
We even experimented with an 87mm with a 99mm stroke engine. The problem we found with the combination was that piston speeds were too fast and the piston was outrunning the flame, causing poor power output. We eventually went with a 1/2-inch deck plate with a rod length of 155mm, giving a fairly decent rod-to-stroke ratio of 1.63.
T: What type of pistons do you run?
DH: The factory pistons were out due to the large bore. We opted for a set of forged pistons with an extremely flat dome. There has been much improvement over the years with forged pistons for sport compacts, and you can run much tighter piston-to-wall clearances today than three to four years ago. They're also much lighter. A forged piston is much stronger than a factory piece. Similar to the B16A engine, we outsource all coarse machine work and perform all the final machining in-house. We balance and blueprint the entire engine to our standards.
T: Anything else special about the bottom end?
DH: For the drag engine we run an electric water pump to reduce drag and run the smaller water pump gear. Also, we had to change the tensioner placement due to the deck plate.
T: Anything different on the top end compared to the B16A?
DH: The B18C head we use is a blend of the B16A and B18C design. We added material to the intake runners to raise the short turn of the port. That way the intake charge has better direct flow into the combustion chamber instead of having to make a 90-degree turn into the chamber. Again, we concentrate on the fin area and valve pockets for better flow. The rest of the port is polished for smoother flow. The head is also milled to reduce combustion chamber volume.
T: What did you use of the valvetrain?
DH: We tried a couple of different combinations. First, the head is fitted with our springs, retainer and adjustable cam gears. The first combination we ran was a two-lobe design, eliminating the middle lobe. But we found that running only the third lobe to operate both valves was much better.
T: So on the induction end, you weren't limited to the factory manifold we noticed you had on the TWM setup. Any trick things there?
DH: We started with a TWM manifold, but we tuned the manifold on an engine dyno. We played with manifold length for best overall power.
T: Thank you, Dave, for your time and information. We're sure the B-series guys also thank you for your knowledge and wish you the best in 2004 with Project Delta. Any last words?
DH: You're welcome. It was my pleasure. When we came out with the Project Beta, we raised the bar of what's possible in front-wheel-drive drag racing. We plan to raise the bar again with Project Delta (RSX), and we're confident the information we gained with the development of the K-series engine will make a statement. Our first race is at NHRA Moroso, so be on the lookout.