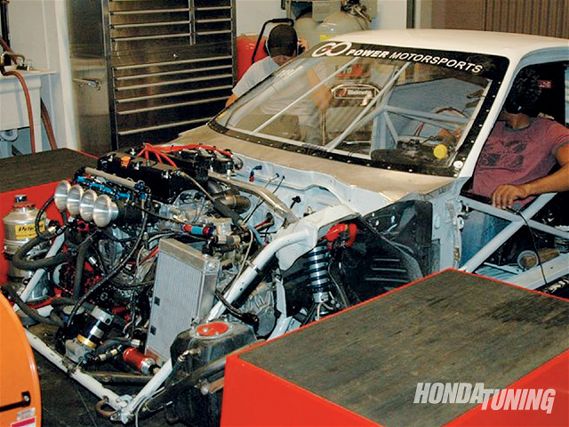
Individual Throttle Bodies
Often taken for granted, producing power from a naturally aspirated engine is difficult. Simply put, there are fewer options when compared to forced induction applications where, often times, all that's required is more boost and more fuel. To harness ever last bit of power, each part of the system must be scrutinized. Long used by racing engineers for generating more power from all-motor setups, ITBs, (individual throttle bodies) have become all but commonplace within the Honda world. But similar to how different turbochargers and superchargers can differ from one another dramatically, not all ITBs are the same. John Whatley, Nalani Whatley's all-motor drag racing team's crew chief, knows this, as he's tested numerous throttle body configurations as of late. The team's most recent showdown: its current TWM Induction 54mm configuration versus Kinsler Fuel Injection's legendary 62mm ITBs.
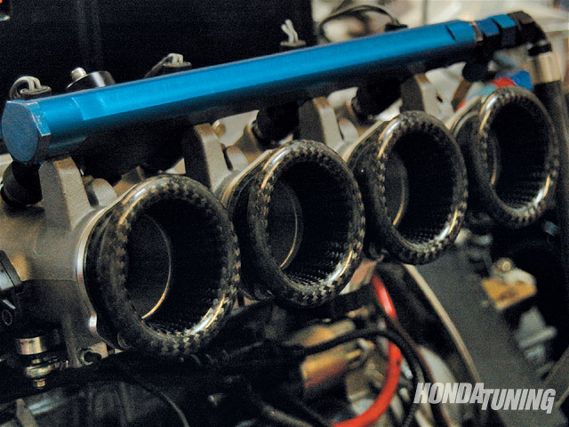
The History
You don't need to look far to see the prominence of ITBs within the racing world. But because of their complexities, ITBs are not conducive or cost-effective in terms of production vehicles. Of course, there are exceptions. BMW was the first manufacturer to incorporate ITBs into a production level engine, first in its mid-engine '78 M1 and later in its '85 E28 M5. Shortly after, Nissan would follow suit with its '89 Skyline GTR's RB26DETT engine. The company kept the ITBs and this very design until the end of 2003. As far as Honda goes, you have to delve into the aftermarket tuning industry to get a taste of ITBs. Factory-backed tuners like Mugen and Toda have relied on such throttle body setups within their automotive racing programs since the early 1990s. They've even implemented them on motorcycle engines. In the early days, cost-effective engine management systems-which are needed to control an ITB setup's fuel injectors-were few. Cost-effective ones were even fewer. But as stand-alone ECU prices began dropping and import racing teams' budgets began to rise, more teams and engine builders turned toward ITBs.
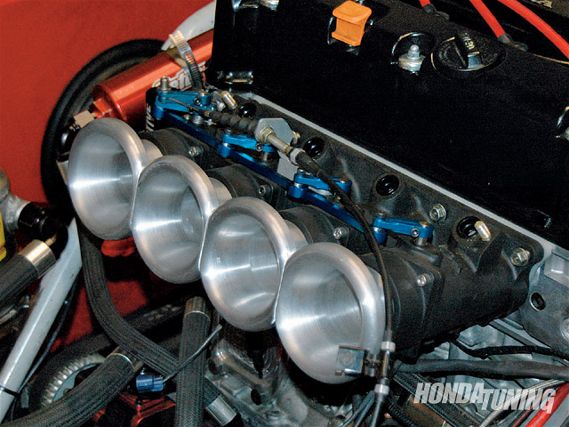
The Theory
Naturally aspirated engines don't have the luxury of boost controllers or the knack for swapping in bigger nitrous jets but they do have the innate ability to scavenge power from things like compression, displacement, cylinder head ports, and valve angles, even through intake design. It's no secret that air travels most effectively through a straight path. This simply isn't possible with a conventional intake manifold that uses just one throttle body. Here, air travels through a single port but must feed four separate cylinders, all of which are spaced in different proportions from the throttle body. Similar to how exhaust manifolds are designed, equal distance runners is an important factor when considering intake manifolds. Depending on the distance between the throttle body and a particular runner, the manifold plenum's effectiveness, air speed and volume, as well as fuel flow characteristics, one cylinder can vary from the next. ITBs solve all of these issues, allowing air to be distributed equally among all cylinders, independently from one another. The results increase air speed and volume for each cylinder. As you'd expect, all of this translates into more power and a more usable torque curve. But there's more. Well-thought-out ITB setups can be angled to match the cylinder head's intake ports and its fuel injector locations can be moved to more evenly distribute and better atomize the gasoline, a feature that's especially useful with high-compression race engines. For example, as static compression ratios rise, the intake plenum's effectiveness diminishes. The same holds true for when cylinder head ports or camshaft duration are heavily modified.
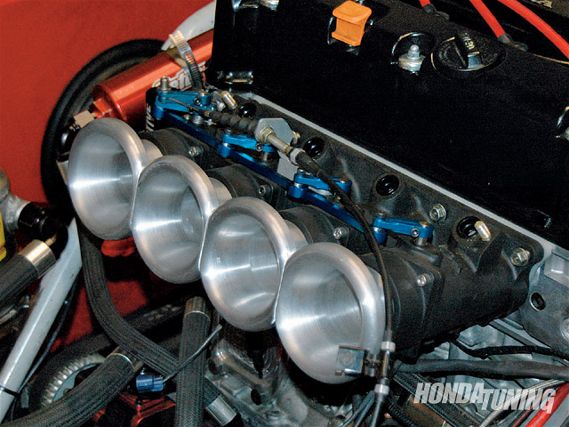
The Hardware
But not all ITBs are the same. We'll spare you the math lesson, but understand that serious equations are involved when determining the proper throttle diameter, injector location, and flange angle for a well-thought-out ITB configuration. The results optimize peak torque, peak horsepower, and the overall powerband. TWM Induction was one of the first companies to produce Honda-specific, off-the-shelf ITBs, and was who Whatley relied upon for several seasons of racing. But as the Whatleys' engine program progressed, so has its need for a custom-built set of ITBs. Whatley says that the new engine wasn't responding to adjustments that would otherwise prove positive. The power curve remained flat from 8,000 rpm onward and gradually dropped shortly thereafter-not exactly ideal for a 14.2:1 engine that's designed to spin well past 10,000 rpm. After viewing the dyno results, Whatley knew he needed larger throttle bodies. If you're unfamiliar with ITBs, simply imagine swapping your B16A intake manifold for an ITR one.
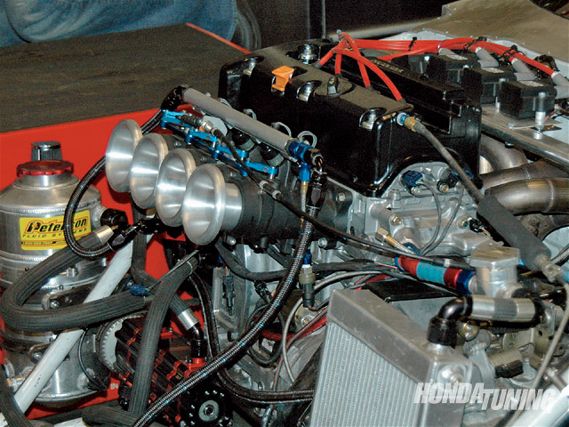
As a result, legendary Kinsler Fuel Injection was called upon for a set of its custom-built ITB configurations. Kinsler manufactures fuel injection solutions for all types of engines ranging from vintage ones to more modern Le Mans versions. The main difference between companies like Kinsler and TWM is that Kinsler has the capabilities to produce custom-built, one-off induction systems to guys like John Whatley's exact specifications. Kinsler's throttle sizes range from 51-67mm, and are offered in its standard aluminum or magnesium casings for reduced weight. Of course, weight is always an issue for drag racers, so Whatley opted for magnesium. Each runner is then precision machined and CNC ported for consistency.
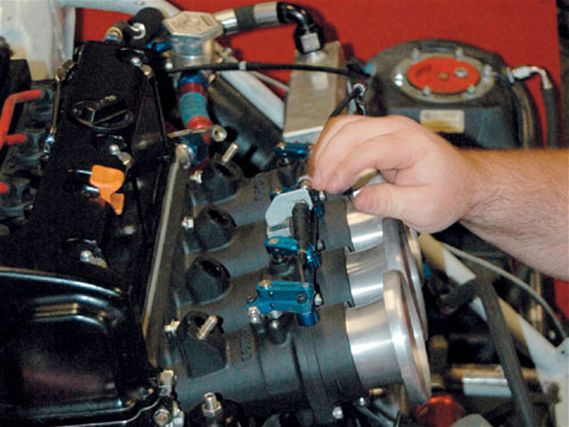
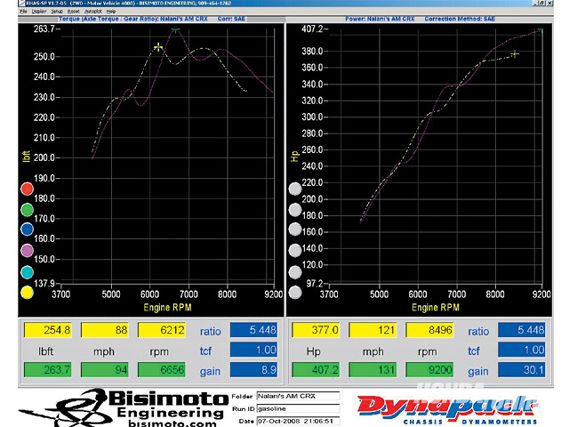
The Test
In order for such testing to be reputable, the process must be controlled and repeatable. Besides, Whatley wanted to ensure that his choice to swap throttle bodies was a smart one. As a result, the car was sent off to Bisimoto Engineering, where testing was conducted on the company's Dynapack 300 dynamometer. Step one involved baseline testing with the 54mm TWMs still installed. Immediately following, the TWM ITBs were pulled in favor of the larger Kinsler units. Each fuel injector was removed and reinstalled into its original port, thus eliminating any changes that could be injector-related. Additionally, fuel pressure and ECU variables remained constant for the initial tests. The first pass yielded an extra 17 hp, and some fine-tuning netted a total gain of 21 hp. To ensure that the results were as accurate as possible, three back-to-back pulls were made, all with water temperatures that were consistent with earlier baseline runs. Such attention to detail is important when dyno testing. Changes in water, air, or oil temperature can all affect power figures. The Kinslers allowed the engine to make power past what the TWMs were capable of and remain flat all the way to the team's target redline. A significant increase was realized at 8,500 rpm where the engine saw a 10-lb-ft increase in torque. Rest assured, this newfound power will be put to good use.
Team: Whatley Racing
Car: Honda Crx
Engine: K24a
Bore And Stroke: 89.5mm X 103mm
Compression: 14.2:1
Camshafts: Go Power Custom
Redline: 10,200 rpm