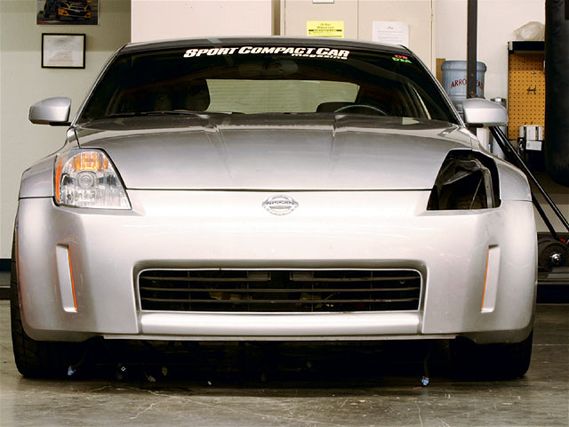
We haven't got as far as we had previously promised. Project Z still hasn't made its date with the dyno, but there's a good reason. Building a 350Z to properly support the power and meet the lofty goals we've set requires a significant amount of hardware-too much to mention in just one project car installment.
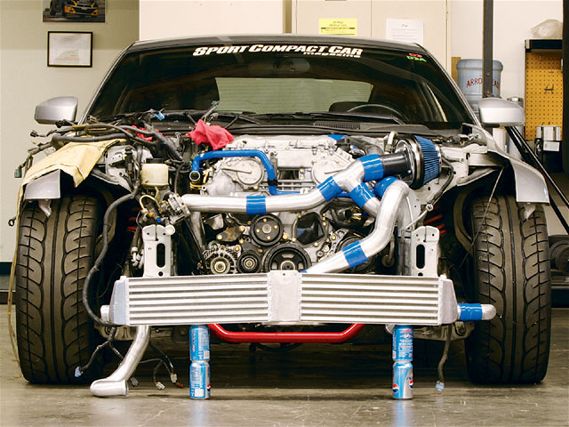
As we dream of building the poor man's exotic-killer, the story of Project Z's construction is best told with a somewhat corny analogy. When building a house, it's important to start with a strong foundation. If the project car we're building is to hang with the venerable Corvette Z06, it had better be one stout brick. We did just that in our last installment of Project Z, when we went through the engine's long block with fortified components to ensure reliability under boost.
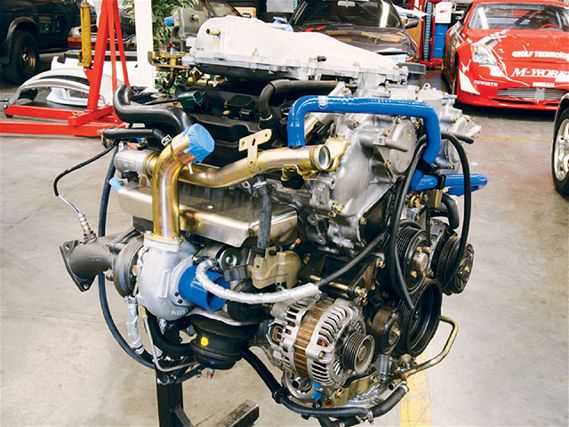
With the engine's internals squared away, we turn our attention to the all-important peripheral ancillary components to achieve our goal of 500 wheel-hp and Z06 humiliation. After rescuing the Z from VRT's shady clutches, it was readily apparent that it had been turned into a sad basket case. Extensive work from a crew with plenty of competent mechanical skill was needed to put our project back on the road.
The car and assembled engine were brought to Steve Mitchell and his team at M-Workz in Gardena, California, for final assembly. The staff at M-Workz includes ex-personnel from Nissan's engineering department, who chose not to make the move when Nissan relocated its North American HQ from Southern California to Tennessee. Mitchell is also well-versed in aftermarket work on 350Zs, G35s and all sorts of GT-Rs, as well as racing one of the fastest time attack Zs on the continent (see page 38), powered by a larger version of the Jim Wolf Technology kit about to go onto our Z. Who better to work on our car than the people who helped bring this to fruition?
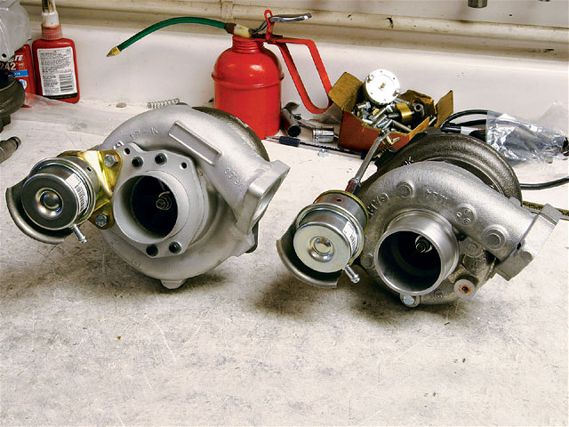
Turbos
The critical component in the equation is turbocharging. Jim Wolf Technology provided one of its complete turbo set-ups. The JWT 700 system, (700 for 700 wheel-hp) is noted for its OEM-like attention to detail and completeness, as well as performance.
Our kit came with JWT's Sport 700 turbos, which are based on Garrett GT28RS ball bearing turbos, otherwise known as the famed 'Disco Potato'. Compare that to the base Sport 530 kit, which uses smaller GT25 turbos. In theory, the 530 kit is capable of the 530 wheel-hp we're looking for, as long as the fuel system is sufficient and the bottom end strong enough. After consulting with JWT, we decided on the relatively quick-spooling 700 kit for the additional headroom, and the more progressive and track-friendly power delivery.
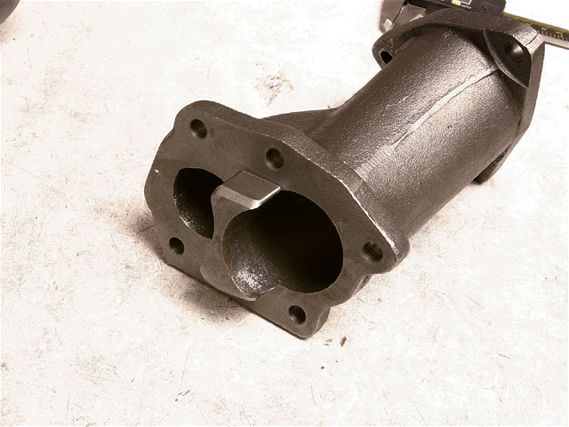
The Disco Potato features a 60-trim version of Garrett's ultra-efficient BCI-18 compressor wheel, contained within a T04B housing with just the right diffuser width for maximum adiabatic efficiency and a wide map. The turbine is a 76-trim, nine-blade NS111 wheel, known for its efficiency at converting hot exhaust gasses into shaft power. This allows the use of a large, free-flowing 0.86 a/r turbine housing.
The turbos' oil and coolant feeds are all plumbed with hard lines and all charge pipe couplers are heat-resistant, multi-ply silicone. During the build process, our block was modified to have oil return ports drilled into the lower sump so that turbo drain oil dumps in above the oil level for minimal restriction. JWT supplies a sump sandwich plate with the kit that adds one additional quart of oil capacity as well as return nipples that sit below the oil level. We plugged these up.
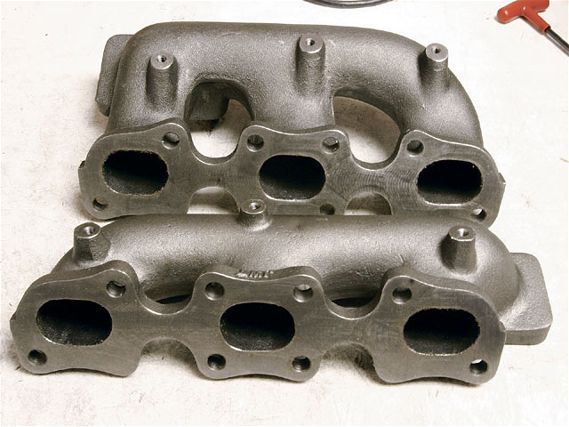
JWT modifies the compressor housing and wastegate brackets to fit within the tight confines of the Z's engine, as both turbos sit right next to the frame rails. These feature an internal wastegate and a friction-reducing ball bearing center section for less lag and better transient response. Even with its combined 700 wheel-hp potential, the two Disco Potatoes are relatively lag-free when coupled with the VQ35's displacement, which gives more than enough flow to exceed our power goals with ease.
Exhaust Manifolds
Cast exhaust manifolds, made from high-temperature-rated ductile iron, assure durability over many extended heat cycles. Ductile iron has a higher nickel content than regular iron, which helps with heat resistance and strength. Magnesium is also added to control the shape of carbon asperities within the metal to make it less brittle, hence the ductile nomenclature. The manifolds have stainless steel heat shields to help maintain a near-stock engine compartment temperature, a critical detail for extended durability of the car's underhood components.
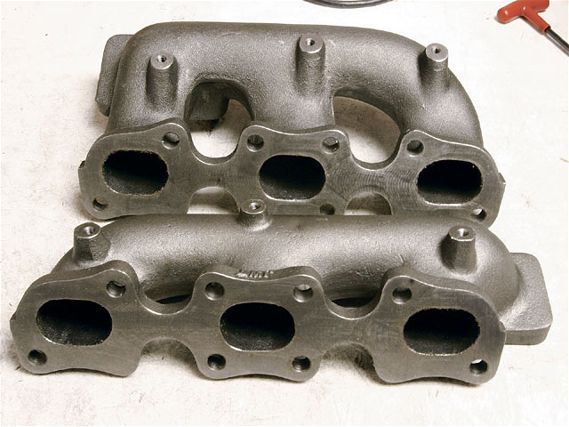
The turbos dump into cast O2 sensor housings with cast-in dividers to separate the turbine and wastegate discharge flows. These are the same as on the base JWT kit and modified to port-match the larger turbine outlet diameter of the 700 turbos, but still bolt onto the stock catalytic converters. Short nub extensions from the housings protrude into the turbine to separate the flow of the turbine and wastegate as much as possible. This little trick improves overall exhaust flow, helps reduce spool time by improving turbine efficiency and can be good for up to 30hp on a single Disco Potato when the wastegate discharge is separated from the turbine exhaust flow and re-merged over six inches downstream of the exhaust.
Normally, welding a separation plate into the turbine housing and re-merging the wastegate dump tube into the downpipe is something only high-end fabricators do. This cast extension on the JWT dump tube saves the trouble, although the wastegate discharge is merged earlier in the cast O2 housing so stock cats may be bolted directly to the housing.
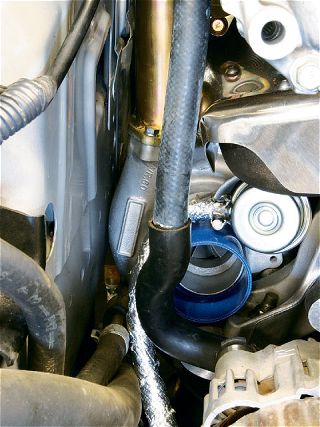
Charge Piping And Intercoolers It's no easy task plumbing intake air to two turbos, sending compressed air from those turbos to a front-mount intercooler and then to a single throttle body. Doing it within the confines of the 350Z's engine bay-while making it reliable-becomes a serious feat of engineering. Plumbing in the JWT kit starts with a single top-mount POP Charger air filter, located behind the driver's-side headlight. Right after the ambient intake air is strained through a POP Charger filter and registered by the airflow meter, the air is split off through a cast 90-degree T-section and plumbed through 2.25-inch mandrel-bent aluminum pipes toward each turbo.
Once pressurized, the air is sent to JWT's large front-mount intercoolers to shed the heat created by the turbochargers' adiabatic compression, which further increases the intake charge density. All pressurized plumbing after the turbos is bead-rolled to prevent the hose connectors from popping off. The compressed charge exits forward and down from the turbo on the driver's side, next to the oil sump, through 1.7-inch steel pipes (to cope with the heat from the manifold), which are gold-cadmium coated (like OEM hard lines) to prevent corrosion. The remaining aluminum piping plumbs to the intercooler end tank of the two side-by-side front-mount intercoolers.
On the other side, the plumbing is more complicated. It routes up over the passenger-side turbo and sideways over the frame rail and down over the wheel well to the end tank on that side. At least sheet metal cutting is not involved.
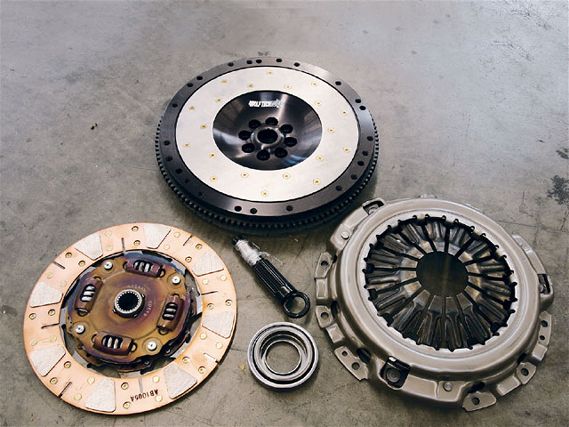
The intercooler assembly consists of two big bar-and-plate, air-to-air heat exchangers sharing a common center plenum to direct air to the throttle body. Bar-and-plate intercoolers are excellent heat exchangers and have more thermal mass than lighter tube-and-fin charge coolers. They're more effective at low speeds, or on the street, where airflow across the core is limited because a beefier core design takes longer to heat up. The flip side is that it also takes longer to cool down.
To prevent turbo-damaging, throttle lift-induced compressor surge, a single Bosch-type compressor bypass valve is situated after the airflow meter to assure proper driveabilty when modulating the throttle on boost. On cars with a mass airflow meter, if gases are simply dumped overboard (in ricer blow-off valve style), air already metered will not be ingested by the engine. Since the engine thinks this previously measured air is going to be burned, its ECU injects fuel for it. However, that air got dumped, so the engine momentarily runs too rich. This can cause stalling and sputtering.
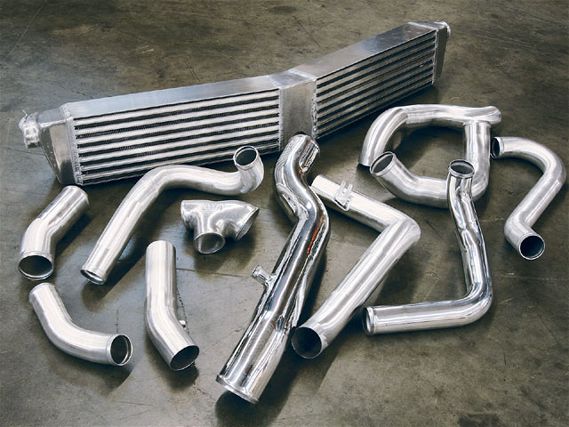
Engine Management
JWT turbo kits use a pre-programmed piggyback spark timing computer, larger 530cc/min injectors, a larger in-tank 255lph fuel pump and a 4:1 boost-dependent fuel pressure regulator. JWT designed them to use a rising-rate fuel pressure regulator to work with the stock return-less fuel system (instead of reprogramming the ECU) so off-boost engine management stays close to stock. This allows our car to run as clean as a stock Z for emissions reasons. On boost, the larger injectors and higher fuel pressure will ensure a sufficient supply of gas. Spark timing is retarded through the piggyback computer, but only under boost. This turbo kit has produced well over 500 wheel-hp, with 530cc/min injectors and less than 14psi of boost. We relish the idea of making so much power at such an under-stressed boost level.
For our application, we will have some custom tuning performed on our factory ECU by Clark Steppler at JWT, to optimize performance with our hardware package. According to JWT, the 530cc/min injectors should be good for up to 700 wheel-hp.
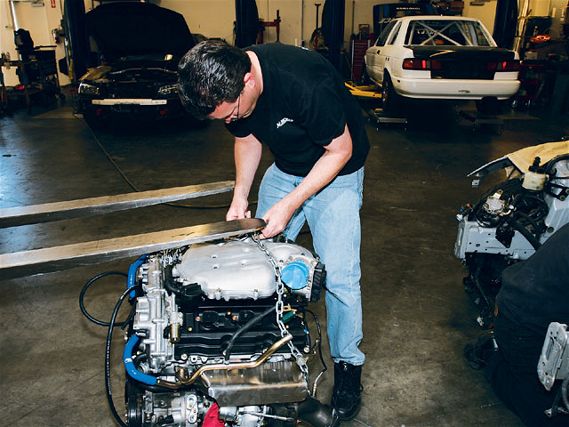
Driveline
A new clutch had to be procured to handle the near-doubling of power. We didn't want a multi-disc design that would make everyday driving difficult, since the car spends most of its time on the street. But we also anticipate some track beating, so finding a clutch with the right balance of usability and durability was critical.
After much searching and debate, we chose one of JWT's less aggressive, smoother and more streetable heavy duty clutches. The JWT Stage Three unit can easily hold our anticipated 540lb-ft of torque and offers the driveability we were looking for. We'll see what happens when we use the 700 wheel-hp the turbos and engine are capable of. At 500 wheel-hp and on super-sticky street tires, though, Project Z will already be traction-challenged .
The Stage Three clutch has a pressure plate with 2750 pounds of clamping force. Compared to the stock 1936 pounds, that's an increase of 70 percent. By fiddling with the fulcrum point of the pressure plate's diaphragm spring, this increase in clamping load comes with only a minimal increase in pedal pressure. The clutch disc uses heat-resistant metallic pucks for maximum holding power at high temperatures.
Since metallic pucks tend to have harsh, lightswitch-like engagement qualities and tend to chatter as the clutch is engaged, a four-sprung hub is used to make it more user-friendly. Marcel springs are leaf spring-like devices that look like Ruffles potato chips. As the clutch is engaged and the pucks come into contact with the flywheel and the pressure plate's pressure ring, the marcel spring limits the clutch's clamping force. As the clutch pedal is released further, the marcel flattens out and the full clamping load of the pressure plate can now bear on the puck, making for a smoother engagement.
JWT's metal disc also has a beefed-up hub with shock-absorbing springs that both smooth engagement and cushion the drivetrain, making this aggressive clutch more streetable. Despite their race-bred nature, our prior experience with these clutches predicts a surprisingly smooth engagement.
The original JWT 13-pound aluminum flywheel was one of many things stolen from our Z. JWT was gracious enough to supply us with another as we bolted the drivetrain together. This flywheel is significantly lighter than the weighty stock dual-mass unit, which tips the scales at 29 pounds.
This lightweight flywheel makes a noticeable difference in throttle response and acceleration, particularly in the lower gears. It's also easier on the transmission synchros and makes heel-and-toe downshifting much easier. It has a replaceable steel friction surface for long wear and serviceability. Getting rid of the noise-damping dual-mass system will add an increased amount of NVH-how bothersome this is depends on personal taste. Most likely, if you're willing to deal with the compromises involved with having a 500 wheel-hp Z, a little extra noise will be low on the list of downsides. It doesn't harm anything in the drivetrain and can be damped with viscous gear oil, like Red Line's Heavy Shockproof.
Soon, Project Z will receive the final hardware necessary to survive the 500 wheel-hp track beating it has an upcoming date with. We'll get it on the dyno for final tuning by JWT and also experiment with some simple bolt-on power-adders to optimize our new turbo hardware. Five hundred wheel-hp here we come.