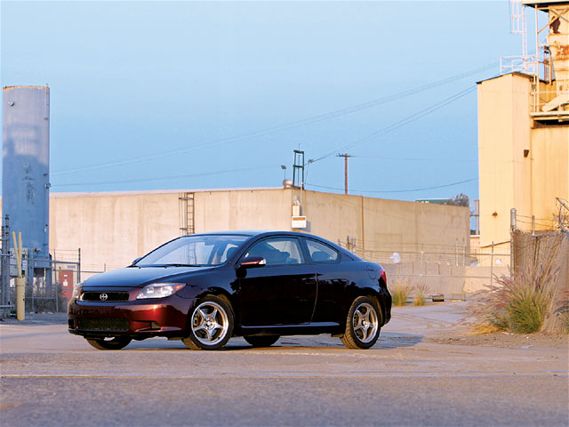
About a year ago, we reached the point with Project tC where we thought we had enough to turn the lifestyle-branded wannabe performance car into something worthy of the Sport Compact Car name. By our estimate, the tC should have been tuned well enough to take on a mildly tuned Acura RSX Type-S on identical tires. Bang for the buck and performance-wise, the two were closely matched. So it was off to the racetrack to do a project car shoot-out between the two.
The results were close. So close and (more importantly) uninspiring, we put off posting the results until we could arrange a proper rematch. The bottom line was that while the RSX possessed decent track potential out of the box, our tC struggled to convey the same driving feel, even if the numbers were about the same. We knew the car had more in it. The only question was if it would be a waste to spend more money on our purple coupe. We could have just started with an RSX and called it a day.
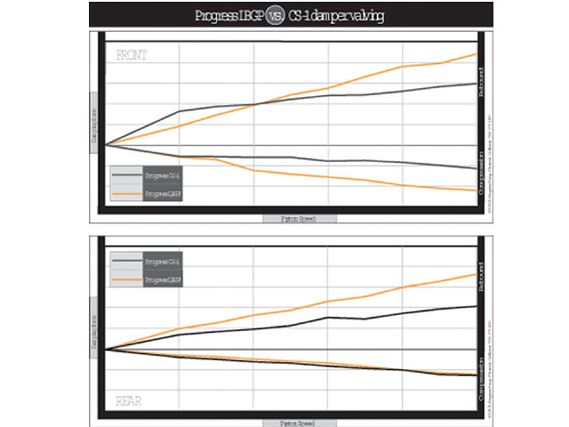
So the Scion sat un-tinkered with for a year as we scratched our heads and thought about what to do with it. In the meantime, it held up reliably as our cargo carrier and daily commuter, without any incident or mechanical difficulty. The selection of quality parts from manufacturers like Progress, Hotchkis Tuning and TRD made the car immensely better, but not great. With its supercharged engine, bigger brakes and coilover suspension, our tC was actually pleasant to drive and fast, the way it should have been straight from the factory.
We knew we still had some speed left on the table, so we got ambitious and dug back in. But this time we weren't going to spend more money and get more parts. We were just going to refine what we already had.
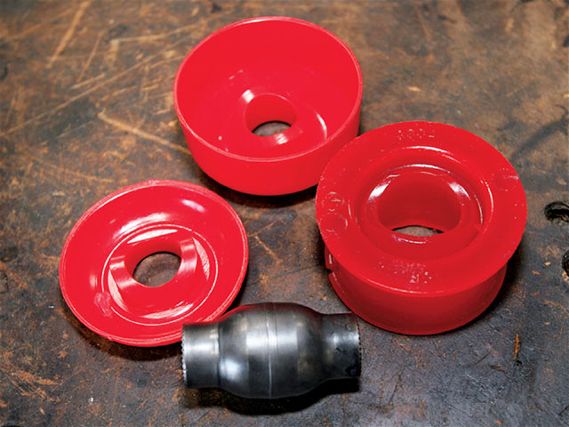
The original Progress suspension was an excellent choice for street performance, firm enough to reduce body roll and quicken transitions to nearly Evo speed, yet also smooth enough to drive your mom around. However, the limitations of the suspension's street focus became apparent during our shoot-out experience. Major complaints were the not-so communicative ride, appearance of mid-corner understeer and the overall sloppy nature of the econo-box platform. The car had also been set up with too little rear spring rate and suspension travel, causing the dampers to bottom out when going over speed bumps.
Our first task was to eliminate the bushing gush and flex out of the suspension. It's obvious that the tC was built to ride well and have minimal NVH (geek-speak for noise, vibration and harshness), with crisp handling low on the list of priorities. Gush is bad for handling. For a car to handle well, its suspension should work to keep the alignment true, with the tire's contact patch consistent and as large as possible. The frictional grip of a car's tires can transfer over a 1000 pounds of force to the suspension, with suspension arms acting as levers that can multiply this many times over.
All this force is brought to bear on the soft biscuits of rubber known as tC suspension bushings. Rubber is an excellent choice for an average driver, whose idea of taking a fast turn only stresses a car to 40 percent of its maximum lateral capability. For those who like to push the envelope, smooth-riding rubber means a lack of steering precision and a loss of grip, due to shifting alignment.
The rear suspension subframe hangs on four huge, squishy rubber bushings with large-windowed cutouts to add additional shock-absorbing compliance. The lower trailing arm's main bushing also shares a similar cut-out rubber biscuit design. When moved with a prybar (to simulate tire loading), it was possible to get the rear suspension to move nearly half an inch in either direction. Because 1/16th-inch of movement is something most drivers can feel, one inch is extreme and makes an iffy proposition of precise driving at the limit.
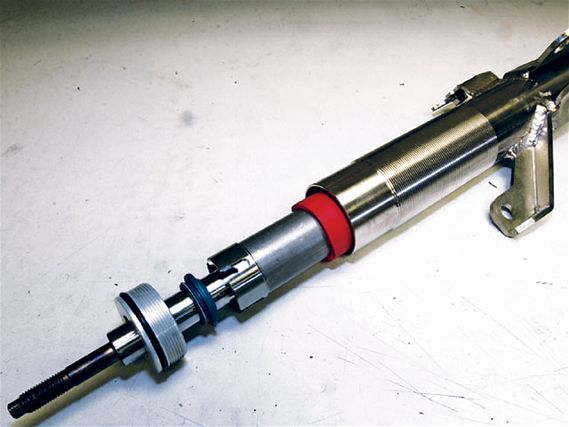
The front suspension's lower control arm had a huge rubber bushing at the forward pivot. This bushing would allow for over a quarter of an inch of deflection when loaded via a prybar. Although this might be acceptable for grandpa's Buick, it was a source of much steering slop. Although we liked our tC's refined cruising ride, all this monkey motion made for a lack of turn-in crispness and some rear-end twitchiness when pushed to its limits on the track. The key was to keep the rear suspension from moving around.
We found our solution through Energy Suspension (ES), who provided us with one of its recently released bushing kits for the Scion tC. Originally prototyped for track use, ES bushings replace all rear subframe-to-chassis bushings with super-stiff, 95A-durometer, solid polyurethane pieces. Large 88A-durometer rear trailing arm bushings are also available.
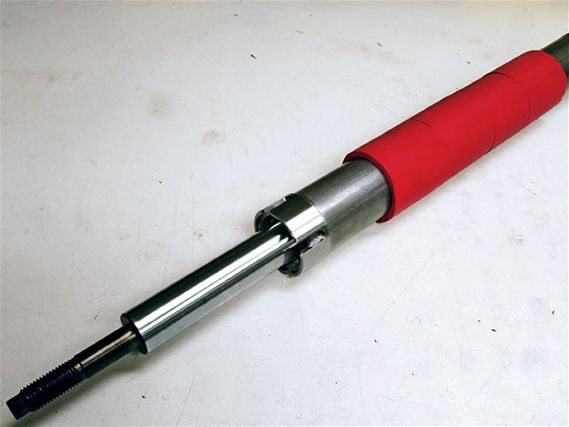
According to ES engineers, subframe bushings actually contribute less to NVH than control arm bushings, so our race bushings should minimize subframe movement without rattling our teeth out. ES will initially release the subframe bushings to the public in the softer 88A-durometer form. Since the tC's rear suspension requires some bushing compliance to prevent bind, ES only replaces select bushings, mainly those that have the largest affect on wheel tracking.
Up front, the two inboard lower control arm bushings were replaced with 88A-durometer pieces. The front item is a conventional rotation bushing while the rear vertical ball bushing is a work of art. ES created a multi-piece urethane ball-and-socket affair to eradicate most of the gush, while having less bind than the factory rubber part. Revisiting the suspension with our semi-scientific prybar test revealed that we had eliminated about 80 percent of the suspension's deflection.
In previous installments, our horsepower additions to the tC had created severe engine torquing issues. The compliance of the hollow rubber engine mounts added so much lash to the drivetrain that the engine felt like it was attached to the throttle with a yo-yo string. This lurching contributed to a pounding case of wheel hop. We reduced the engine motion with the use of an engine torque damper from Ingalls Engineering. But it wasn't enough. The piece transferred all engine vibration to the strut tower and sheetmetal, essentially making the car a rattle can between idle and 3000rpm.
Desperate to address the engine's wind-up and subsequent wheel hop, we replaced two of the engine's four mounts with ES's polyurethane parts. While we knew stiffer engine mounts typically add more vibration (especially to the steering column at idle), our hope was to sacrifice some comfort at idle in order to eliminate the perpetual rattle from the engine damper. ES makes a complete four-piece kit, but to preserve some smoothness, we opted to change the forward and transmission mounts only. Unfortunately, this operation upset the harmony of our car's inner being and our once-smooth Scion turned into a vibrating beast.
This turned out to be far shakier than any other car we've ever experienced with polyurethane mounts. Even road-race tCs with four solid urethane mounts and no harmonic mass dampers had much less vibration. Our theory is that the cantilevered-forward weight of the TRD supercharger-and perhaps the exhaust attachment-had something to do with this. While the mounts and the bushings effectively eliminate all wheel hop, it was unbearable on the street. So we reinstalled our stock mounts. Vibration gone, although we're now back to the same sloppy wheel hop and engine lash problem.
Now that we were sure our tires would point to where they were being told, we switched attention to our Progress re-valveable Competition Series (CS-1) coilovers. In response to our inquiry about a more trackworthy set-up, Progress informed us that it already had an off-the-shelf solution. Progress supplies the suspensions for the tCs driven in the Toyota Pro/Celebrity race at the Long Beach Grand Prix. This is a support race run at the seaside event, where some celebrities and pro racecar drivers bash it up for a few laps and wow the crowd in the name of charity. With inexperienced drivers at the helm, Progress couldn't dial up an edgy calibration. In fact, the spring and shock rates used for the 'celebrity' suspension look reasonable enough for a weekend warrior street car.
Due to the rampant copying of performance parts by offshore mills, Progress requested that we keep the exact numbers of its suspension calibrations secret, just in case some East Asian clone factory got the itch to actually make something good. So, unfortunately, we will not share the numbers, just the differences between the two calibrations.
The Pro/Celebrity suspension uses a front spring rate that's 30 percent higher than the street suspension and a rear spring rate 45 percent stiffer, putting the bias of front-to-rear stiffness a little less prone to understeer without making the car like a typical lighting quick rotation (and easy for the inexperienced to spin) front-wheel drive race car.
To handle the extra rebound energy from the stiffer springs, Progress revalved our dampers to Pro/Celebrity specs. The front dampers now have 35 percent more high-speed rebound damping, but 45 percent less low-speed rebound damping. Nearly 50 percent more compression damping was added across the velocity range. In the rear, 40 percent more high-speed rebound was added, as well as 30 percent more low-speed rebound damping. Rear compression damping is nearly the same.
After installing the new springs and recalibrated dampers, Joey at Progress aligned and corner-balanced our suspension. The rear camber was reduced from over three degrees negative to 1.7 degrees. Our front tires were in the vicinity of zero degrees of camber. Since the front suspension is not adjustable, Progress added a camber bolt to one of the two spindle bolts so we could dial in some negative camber. We normally frown on camber bolts because they are notorious for slippage. The smaller bolt used usually stretches and allows the spindle to move. The tC has huge strut-to-spindle bolts, so the smaller-than-stock-diameter camber bolts are still bigger than most bolts. We set the front suspension at two degrees of negative camber, while the front and rear toe settings were set to zero. This is a substantial improvement and will contribute greatly to increasing front grip and reducing understeer.
The rear ride height was found to be disproportionally lower than the front, so it was raised to reduce the chances of it bottoming out under roll. At this time, the corner weights were also set for a 50 percent cross weight. Corner weighting is weighing the car at each wheel and adjusting the spring perches until the diagonal cross weight percentage is equal or 50 percent. This assures that the car will have equal understeer/oversteer balance in both right and left turns.
To round out our set-up changes, we replaced our balding Kumho MX tires with some maximum-grip summer tires from Bridgestone. The 225/45/17 Potenza RE-01R tires are among the stickiest non-R-comps available in America. It might be overkill for a car in this price bracket, but it's a far cheaper and simpler option than a limited-slip diff to control excess front wheelspin engendered by the massive torque from our supercharged engine.
To further tighten the rear, we also installed a prototype steel strut tower brace from Ingalls Engineering. This is much needed, as the tC doesn't have a rear shelf to keep the rear towers from flopping around. The brace installs in the floor of the rear hatch and ties the two towers together as well as to two additional points in the rear sheetmetal. When installed correctly, the spare tire, foam tool carrier and trunk lining can all be stuffed back into place.
Even though Project tC generated decent handling numbers with its original set-up, the major improvement now is in feel. The most noticeable change is the increase in front grip. The steering response is now much sharper and the rear feels much more stable. Overall chassis balance is still quite forgiving, though, and the ride is not all that bad. It could easily be considered acceptable for most enthusiasts in daily driving.
If our plans don't get shelved for another year, we'll soon be looking at a retuned ECU and some massive NVH work before we face off against a heavily tuned, naturally aspirated RSX Type-S.
Previous InstallmentsNovember 2005Part 1: Improving stick
June 2006Part 2: Bolt-on brakes for geeks
July 2006Part 3: Smog-legal boost
August 2006Part 4: More boost and lots of shiny parts