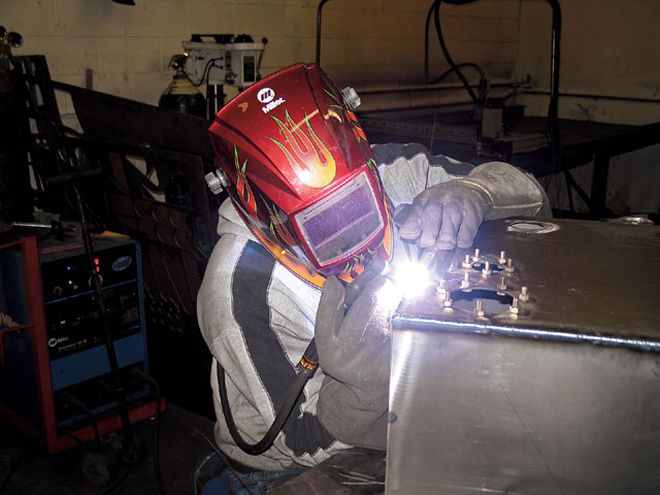
| tig Welding tig Welding
Experienced welders know that without the right information, it's easy to sacrifice quality, lose time, and become frustrated with gas-tungsten-arc welding (GTAW), also known as tungsten-inert-gas (TIG) welding. For novices, that statement is even truer. While there's merit in learning to weld by trial and error, if you want to move toward precision GTAW or TIG welding, an introduction and starting off with the basics is a must. Of course, as with anything, practice is the key to fully developing these techniques. Follow along and learn how you, too, can get the most out of your TIG machine and exactly what TIG welding is all about. For more information, contact the companies listed in the source box.
What type of tungsten should you use?The four main tungsten choices for GTAW are 2 percent thoriated tungsten, pure tungsten, 2 percent ceriated tungsten, and 1.5 percent lanthanum tungsten. Two percent thoriated tungsten is a good choice when using a DC power source because it maintains a pointed shape, resists melting, and has a high current-carrying capacity. When welding thin aluminum (0.09 in. or less) thoriated tungsten is also a good alternative to pure tungsten because it creates a more focused arc. It is recommended that thoriated tungsten be used in a properly ventilated area and measures be taken during preparation to capture dust from grindings. Pure tungsten performs well when welding aluminum using a conventional AC power source. Two percent ceriated tungsten is a good alternative to thoriated tungsten and provides good arc starts at low currents, along with greater arc stability. This type of tungsten is recommended for aluminum AC welding with an inverter-based power source. Last, a 1.5 percent lanthanum tungsten is most commonly used for applications in which long weld times and multiple arc restarts are necessary.
How Can You Prevent Tungsten Contamination And Discoloration?Allowing the tungsten to touch the weld pool is one of the most common causes of contamination. This problem can be resolved by moving your torch farther away from the workpiece, which in turn lengthens the arc. Touching the filler metal to the tungsten also can be a source of contamination, but there is no clear solution to this problem other than practice; trial and error will determine your best technique. If you feel your technique is not the culprit of tungsten contamination or discoloration, check to see that you have adequate gas flow, and allow adequate postflow time, as well. Permit several seconds of postflow, about 1 second for every 10 amps of weld current. Finally, you may want to consider using a power supply that offers high-frequency starts if you think using the scratch-start method is causing the contamination.
What Causes Porosity In A GTAW Bead,And How Can You Prevent It?A loose hose or torch component is a primary cause of porosity. It is remedied by tightening the fittings. If you cannot find loose hose connections by doing a visual check, you might want to place the hose in soapy water until you find the leak and tighten the fittings accordingly. Using the wrong shielding gas or one that has impurities also can lead to porosity. This is remedied by using pure argon after using nitrogen to purge the line of air and any condensation that may have accumulated. Drafts from fans or open doors also can lead to porosity, so be sure that your working environment is well-isolated from drafts or use a gas lens to provide better gas coverage. To prevent porosity caused by inadequate shielding gas flow, follow the recommended flow rate, which is approximately 10 to 20 cubic feet per minute (CFM), depending on the application. Doing so helps ensure quality welds.
What Are The Causes And Solutions For Excessive Electrode Consumption?Using too much current on a given application is a major cause of excessive electrode consumption and is most easily solved by increasing the tungsten size, changing the type of tungsten you are using, or decreasing the amperage. Using the wrong polarity also can result in excessive tungsten consumption. During AC welding, for example, using more electrode-positive current may provide more cleaning action, but it also subjects the tungsten to more current, and thus, consumption. Instead, it is best to set the power source more toward electrode negative on the balance control to minimize the amount of current and time spent on the electrode. Using an incorrect or contaminated shielding gas can lead to high electrode consumption. Be sure to use pure argon, and check for leaks in the hoses, either from cracks or loose fittings.