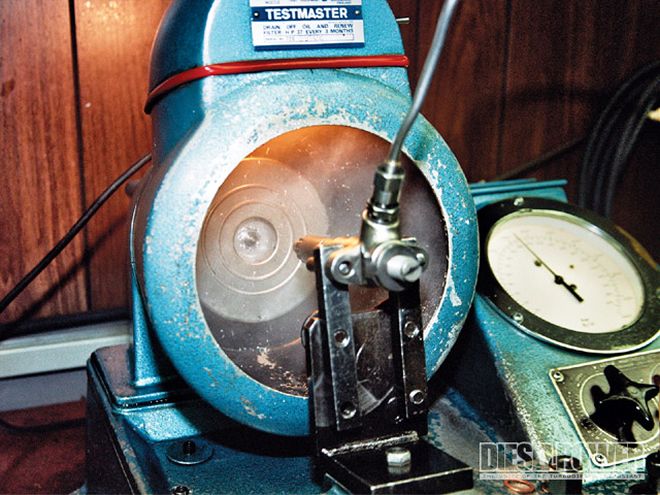
| The first step to determine a diesel injector nozzle's condition is to test the nozzle opening pressure (NOP) and spray pattern in a special fixture. A hand-operated hydraulic pump creates the NOP. The nozzle is sprayed into a chamber that features a fan to remove fumes. Calibration fluid with the same specific gravity of diesel fuel is used.
Your diesel engine injector nozzles are responsible for delivering the proper amount of fuel to each cylinder bore for the load and horsepower demand. Over the course of the life of the engine, the number of injection events can reach the billions, and possibly trillions. In addition, the injector nozzles are subjected to an extremely abusive environment-more than any other part of the engine. The nozzles live in the diesel engine's combustion chamber and are exposed to temperature peaks of more than 1,800 degrees, while the internal pressure may exceed 30,000 psi.
Though almost every fuel system manufacturer recommends servicing the nozzles, these procedures are often neglected by the engine owner and only addressed when a problem exists. Preventive maintenance should be part of every diesel engine owner's plan if long life and trouble-free performance is desired.
Injection ExpertsTo expose Diesel Power readers to the steps required to service mechanical injector nozzles, we visited with Mack Boring & Parts Company in Union, New Jersey. Having no association with Mack Trucks, Mack Boring not only sells brand-new diesel engines, it also rebuilds diesel engines and offers complete fuel system service for most diesel applications.
The Mack Boring & Parts Company's fuel system shop senior technician is Frank Pakay. He is part of Mack Boring's service department, managed by Mike Alfano, where diesel nozzles and injection pumps are serviced for customers around the country as a result of the shop's reputation and long history of working with only diesel engines.
While Diesel Power was at Mack Boring, a set of multi-orifice injectors was being prepared for service. They were from a 440hp Yanmar 6LY2A-STP turbocharged six-cylinder marine engine. The customer's complaint that prompted the injectors to be removed was a report of blue/black smoke at idle. Other common issues that often point to the need for injector service are a rough idle or misfire, excessive fuel consumption, hard starting, and a general lack of performance. Though the Yanmar engine uses its own design of nozzle, it is very similar to what would be found in a Cummins engine with a mechanical fuel system.
Injector Parts and PiecesWhen discussing diesel engines, many people refer to the part that delivers fuel to the cylinder as an injector. To a true diesel expert, the injector is the nozzle holder assembly, but over time, it has been used to describe the actual nozzle. This has become complicated by the different fuel system designs that are employed on diesel engines. There are now mechanical unit injectors (MUI), electronic unit injectors (EUI), common-rail injectors (CR), and hydraulically actuated electronic unit injectors (HEUI) that became popular with the introduction of the Ford Power Stroke engine.
To complicate matters, there are many different nozzle designs within the mechanical category that share operating characteristics in some instances. Hydraulic injectors are usually classified by the nozzle design. There are poppet, pintle, multi-orifice, and electro-hydraulic nozzle styles. Within each design category there are subsets of styles as well, such as those designed for indirect or direct injection applications. Regardless of the design, a mechanical injector that contains no electronic parts can and should be serviced. Electronically enhanced injectors in light-duty applications are traditionally not serviceable and need to be replaced as a unit.
Servicing Mechanical InjectorsThere are three terms that should be understood that pertain to nozzle testing and service. They are nozzle opening pressure (NOP), back leakage, and forward leakage. An injector nozzle can be considered a hydraulic switch. One of its design elements is the pressure at which it opens. This is usually set with either a spring tension adjustment, or on some models, with shims. The term "pop-open pressure" or "popping pressure" is often used instead of nozzle opening pressure. Regardless of which term you use, it describes the amount of pressure that must be created by the injection pump before the nozzle will pass fuel into the cylinder. Each model of engine and nozzle design has its own NOP value that typically varies from 1,000 to 5,880 psi.
Some nozzles employ an internal opening valve that returns unused fuel to the tank. The internal leakage is a result of the nozzle-valve to nozzle-body clearance. It is measured during bench testing for ten seconds and recorded as back leakage.
Forward leakage is a nozzle's ability to not drip or flow fuel until the NOP is reached. It confirms the nozzle's ability to seal. To test for forward leakage, a pressure of approximately 150 psi below the NOP is created on the test bench. No visible dripping is allowed.
If you are the owner of a mechanical diesel that is not running as it used to or are preparing to step up the power, the first thing you need to do is have the nozzles serviced to guarantee the proper amount of fuel is being delivered.