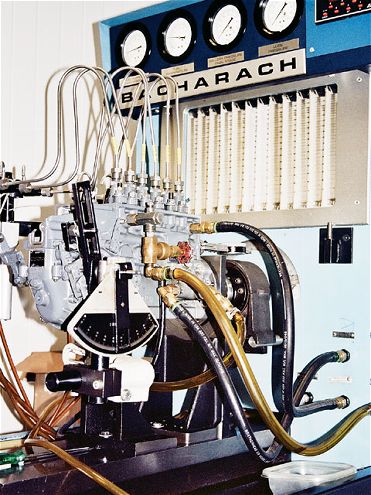
| diesel Basics diesel Motor
In The BeginningIn 1673, Christian Huygens invented the first engine. It was designed to pump water from the Seine River to King Louis XIV's Palace of Versailles. Built with an open combustion chamber, it consumed gun powder as a fuel. Though it was the first documented engine to be built, it had a striking resemblance to a 1509 Leonardo da Vinci drawing, which never came to fruition.
German Nicholaus Otto is generally credited with the creation of the first successful spark-ignition, four-stroke powerplant that bears any resemblance to today's modern engine. Frenchman Alphonse Beau de Rochas fathered the original concept 14 years earlier in 1862, but he was not completely successful in getting it to work. Otto's original goal was to improve on the efficiency of the French Lenoir two-stroke, non-compression engine, and his inspiration came from watching steam rise from a smokestack. As a result, his surname is often used synonymously for the four-stroke cycle.
Rudolf Diesel invented the compression ignition engine in 1897, though his first working model was produced in 1893. Shortly thereafter, refining technology produced gasoline, albeit not in today's current form. Gasoline was basically a derivative of kerosene, a waste byproduct of early oil refining. It was considered a nuisance and was disposed of by being dumped on the ground or into rivers.
Diesel vs. GasThe major difference between the gasoline and diesel engine is that the former relies on spark ignition and the latter on compression ignition. More specifically, the combustion process in the diesel engine is initiated by spontaneous ignition of the fuel when it is injected into a highly compressed charge of air, which has reached approximately 1,400 degrees Fahrenheit. Diesel engine combustion also tends to occur at constant pressure rather than at constant volume, as in a gasoline engine. This means that in the diesel engine the combustion pressure continues to rise steadily as the piston retreats and the cylinder volume increases, whereas in the gas engine, the combustion process is so rapid that there is very little movement of the piston while it occurs and, thus, very little increase in cylinder volume. The expansion of the flame at a constant pressure is responsible for the diesel's reputation for extreme torque along with a flat torque curve.
When the displacement is the same, the diesel engine produces only about two-thirds the horsepower of the gasoline engine. This poses a question: Why is the power output lower even though the combustion pressure is higher?
-
-
Since combustion is an oxidation reaction, there is a specific weight of air that will completely oxidize one gram of fuel without leaving excess oxygen. This weight of air is called the stoichiometric air/fuel ratio. The gasoline engine operates with an air/fuel mixture very near stoichiometric. This is due to the fact that a mixture much leaner than stoichiometric is difficult to ignite in a gasoline engine with a spark plug, and an extremely rich ratio is very inefficient. The mixture is supplied to the gasoline engine by a carburetor or fuel injectors in the manifold and is well mixed and nearly homogeneous.
In the diesel engine, the fuel is injected into the combustion chamber near the end of the compression stroke and ignites spontaneously. This is responsible for the combustion sound that a diesel engine generates that is music to the ears of everyone who reads this magazine. As mixing between the fuel and air occurs, burning continues. This process is very heterogeneous (since the fuel and air are mixed in a combustion chamber it is not as uniform as in a gas engine that has the mixture created prior to entering the cylinder head). Soot is formed during combustion because some of the fuel burns with insufficient oxygen, and the combustion of the fuel is not completed. As additional fuel is injected, more and more soot is produced. Therefore, the air/fuel ratio of the diesel engine must always be leaner than stoichiometric to prevent excessive amounts of smoke. For this reason, a modified, high-output diesel will blow black smoke because it is fueled for power alone with no concern for soot generation. The smoke-free diesel has less fuel present in the cylinder than in the cylinder of the gasoline engine, and diesel power is therefore reduced in comparison.
Older, naturally aspirated diesel engines can use only about 70-80 percent of the fuel employed by a gasoline engine with the same swept volume and still avoid black smoke.
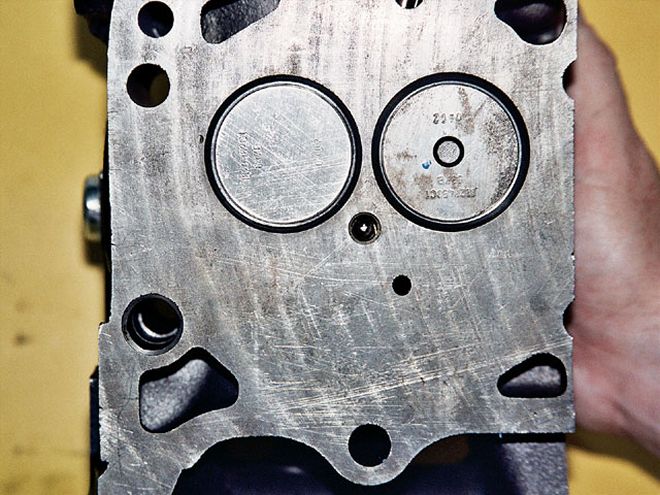
| The cylinder head of a DI engine has a flat deck with no combustion chamber. The valves are flush with the cylinder head. Our example is from a 7.3L Ford Power Stroke.
Indirect vs. Direct InjectionIn diesel engines, the utilization factor (the ability to have smoke-free combustion) varies with the combustion system. For example, the diesel engine featuring a precombusiton chamber system, or indirect injection (IDI), has a utilization value of about 80 percent. The earlier naturally aspirated direct-injection system has a value of about 70-80 percent. The turbocharged direct-injection (DI) system has values of approximately 50-70 percent.
The utilization percentage of light-duty diesel engines with direct injection has been improved upon greatly with recent designs. This is the result of advanced combustion chamber technology and electronic controls along with the need to limit tailpipe emissions.
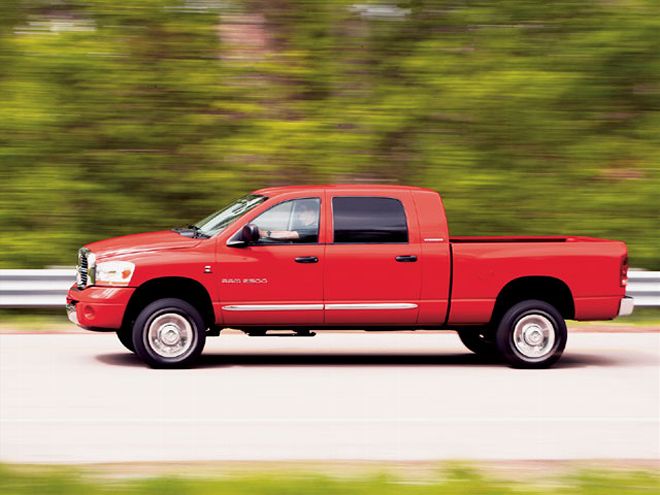
| A DI engine has the combustion chamber cavity in the crown of the piston. This design is called a Mexican Hat piston. Note the size of the pin bore for the wristpin. You will not find anything like that in a gas engine!
An IDI system sprays the fuel into a small precombustion chamber where the ignition occurs and then spreads out into the main combustion chamber. In contrast, a DI engine has no prechamber. Due to the differences in pressure rise, combustion chamber shape, and burn speed with an IDI versus a DI design, the combustion sound becomes unique. To a trained diesel enthusiast, each combustion chamber will produce a unique noise.
Interestingly, the latest version of the GM Duramax has a slightly lower compression ratio to limit the noise generation of this already extremely quiet engine.
The compression ratio of a diesel engine is usually indicative of the combustion chamber design. Due to an increased surface-to-volume ratio and its inherent negative impact on thermal efficiency, an IDI design will employ a higher static compression ratio of usually 20:1 or more. In contrast, a DI diesel has less combustion chamber surface volume, so a compression ratio of approximately 15:1 to 17:1 is sufficient. In addition, an IDI application would depend more on forced induction to clean up the exhaust over a DI engine.
Why Diesels Don't Make HorsepowerSince any Otto cycle engine's output is dependent on the amount of air the pistons can pump, high rpm are required to produce horsepower. The higher the rpm, the greater the potential for horsepower. This is due, in part, to the definition of horsepower being work over time.
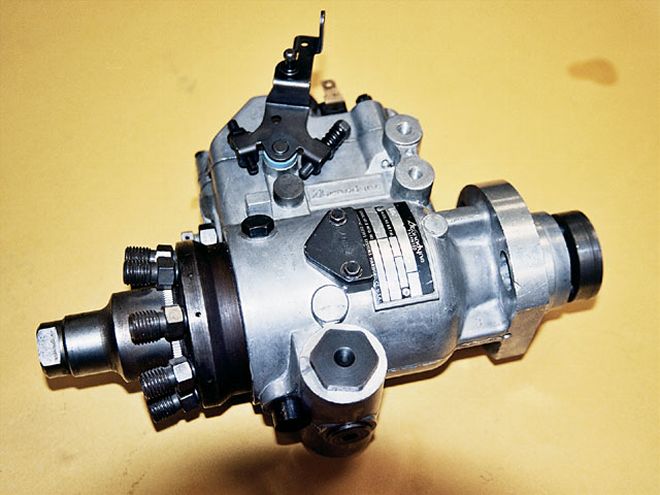
| GM light-duty diesel engines prior to the Duramax employed either a Stanadyne (shown) or Roosamaster rotary injection pump. The example is from a 6.5L GM engine.
The quicker the engine can do the work, the more horsepower it has. A naturally aspirated diesel is limited in power per cubic inch simply because the burn rate of diesel fuel is very slow when compared to gasoline. Thus, by nature of the chemical composition of the fuel, the diesel engine is slow to rev and has limited maximum rpm. For this reason, the diesel engine responds favorably to forced induction through turbocharging or supercharging.
Turbocharging a DieselSince the mid 1960s, the heavy-duty use of diesel engines was increasingly offered in turbocharged form. This was originally a means of improving power output in the medium- to high-speed range, but recently, especially with the light-vehicle market, turbocharging has been employed to produce an environmentally cleaner engine. The turbocharger increases the amount of air delivered to the combustion chamber so the injected fuel can be burned more efficiently. The benefits are a lower fuel consumption rate for the power developed, and as a consequence, better control of emissions. Furthermore, the engine will be quieter because the turbocharger has a silencing effect on the induction and exhaust noise.
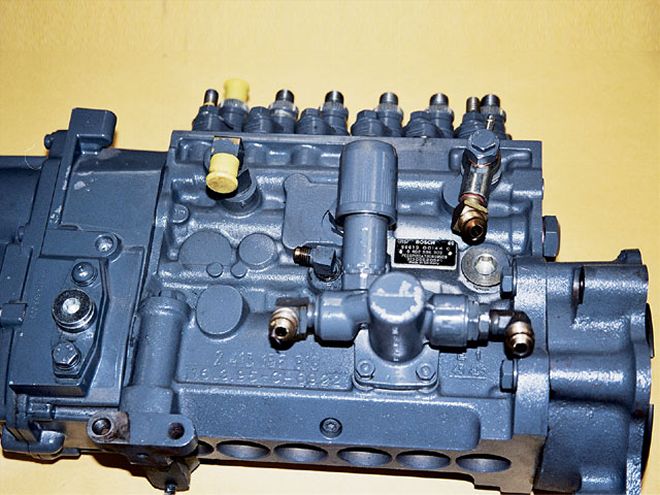
| The '94-'9811/42 Dodge Cummins used an inline Bosch injector pump. The injector pump creates the fuel pressure necessary to open the mechanical injectors. This known as pop-off pressure.
Forced induction increases the volumetric efficiency (VE) of the cylinders not through piston velocity but with an external fan. VE describes the amount of the cylinder that is filled with charge. Contrary to what many believe, on any normally aspirated engine (regardless of the fuel consumed), the cylinder bore is never completely filled with charge, which describes fuel mixed with air. A production gasoline engine will experience approximately 80 percent VE at peak torque while a normally aspirated diesel, due to the low piston velocity, may experience only 55-60 percent VE.
Forced induction when applied to a diesel engine makes up for many of the disadvantages of the slow-burning fuel. Since a diesel does not experience detonation in the same manner as a gasoline engine, both a high compression ratio and large amounts of boost pressure can be employed simultaneously with excellent results.
Advantages Of Diesel EnginesWhen comparing fuel consumption per horsepower/hour at the maximum output between the best diesel and the best gasoline engine, the oil burner uses only about 70 percent of the fuel the gasoline engine does. Partial load conditions are what most engines-either gas or diesel-operate under, and during this scenario, a diesel will burn only 60 percent of the fuel that a gasoline engine would.
The reason that a diesel engine has such good fuel economy lies in the high compression ratio required for auto-ignition. The higher the compression ratio, the better the thermal efficiency. A gasoline engine can't utilize a diesel-like compression ratio because of the fuel's inability to resist auto-ignition, or what is commonly known as detonation or ping.
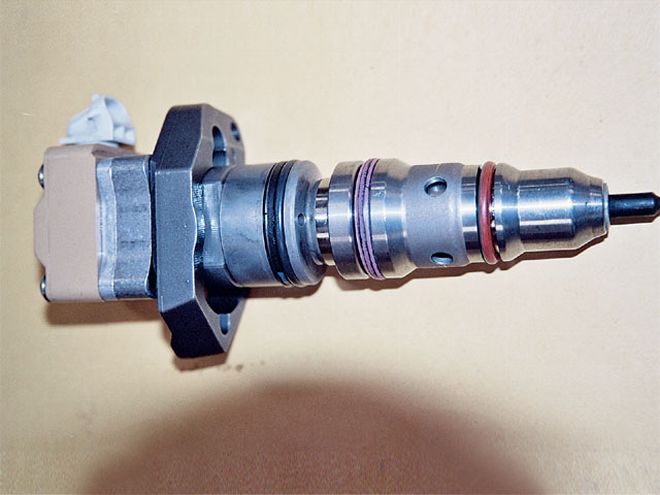
| The Ford Power Stroke was the first light-duty diesel that incorporated electronic controls over the fuel delivery. The same basic injector is used in the International DT-530 engine. Many enthusiasts install DT-530 injectors in modified Power Strokes because they have the ability to pass more fuel.
As long as fuel economy is measured using fuel volume, diesel fuel has another advantage. Diesel fuel has a specific gravity about 10 percent heavier than gasoline. In other words, one gallon of diesel fuel is 10 percent heavier than a gallon of gasoline. The amount of energy in a specified weight of diesel fuel is almost the same as that of gasoline, so the amount of energy in a gallon of diesel fuel is 10 percent greater than gasoline.
Another important reason for higher efficiency in diesel engines is that, while diesel uses an air/fuel mixture with around 40 percent excess air, the gasoline engine runs with a stoichiometric mixture (less air for the fuel consumed). The leaner diesel mixture results in higher efficiency because the combustion temperatures are lower with less fuel when sufficient oxygen is supplied. Lower combustion temperature reduces heat losses in the engine, and more of the energy from the fuel is used to expand against the piston. This reduced heat means the radiator can be downsized (in relation to a gas engine producing the same amount of power) and the cooling fan can be made smaller. In many direct-injection diesel applications, the radiator size can be reduced by more than 35 percent.
Shortcomings of Diesel EnginesWhen compared to a gasoline engine of the same displacement, a diesel's biggest disadvantage is weight. Usually, diesel engines have a weight per horsepower of one and a half to three times more than gasoline engines. The reason for the increased weight is that a diesel engine relies on a high compression ratio.
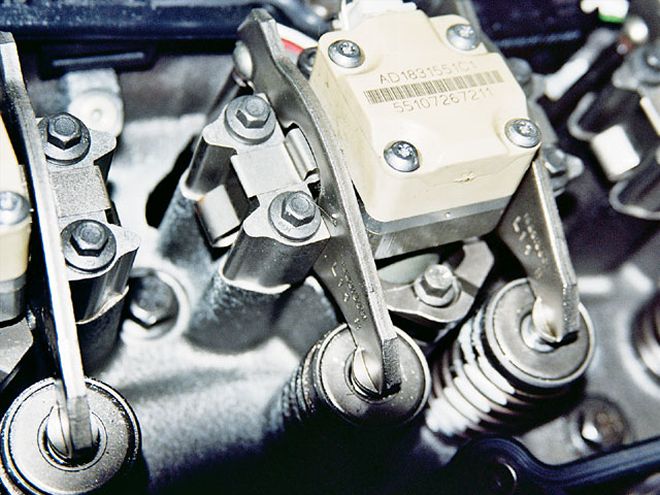
| On the Power Stroke, the injector resides in the cylinder head between the two valves.
In a diesel, the air is heated by the squeezing action of the piston and the fuel is ignited by being sprayed into the heated air. As a result, its combustion pressure is much higher than a gasoline engine; a robust structure is required to withstand the high pressure. The combustion pressure of a naturally aspirated (no turbocharger) diesel engine is about one and a half times higher than that of a naturally aspirated gasoline engine.
Another reason the output of a diesel engine per cubic inch is less than that of the gasoline engine is because a spark-ignition engine can operate at a higher rate of speed. This is due to the combustion burn rate of gasoline being faster. Diesel fuel has a reduced combustion efficiency at high speeds because of the longer ignition delay, longer injection duration (in crankshaft angle degrees), and from the slow mixing rate. In diesel engines, the government-mandated smoke limits are very hard to meet at high speeds since the engine doesn't have enough cylinder event time to burn all of the fuel. Since the diesel engine has a high compression ratio, the energy required to revolve the engine itself, or what is known as friction loss, is greater than that of the gasoline engine. Therefore, when speed is increased to boost horsepower output, the friction loss raises enough to offset the output component of the engine. For a production-style gasoline race engine, a practical maximum speed is around 10,000 rpm. A similar diesel engine would only be able to achieve approximately 5,000 rpm.
The Four-Strokes of DieselAll modern light- to medium-duty diesel engines sold for use in a motor vehicle in the U.S. are of the Otto cycle (four-stroke) design. In the four-stroke diesel cycle, the following sequence of events is continuously repeated when the engine is running:
1. The Intake Stroke:During this time, the piston is moving downward and only air is drawn into the cylinder. This occurs on a normally aspirated engine as a result of the difference between atmospheric pressure and the depression created by the piston and the piston ring seal. On forced-induction applications, the induction process is aided by the external air movement caused by the turbocharger or supercharger.
2. The Compression Stroke:The piston is moving upward in the bore and compresses the air into the very small volume of the combustion chamber and raises its temperature high enough to ensure auto-ignition of the fuel charge. This demands a compression ratio higher than that employed in a gasoline engine. The air is heated by the friction of the molecules being packed into a very small area.
3. The Power Stroke:The proper name for this event is "expansion" because of the flame expanding against the piston. Created by the diesel fuel charge injected into the combustion chamber and being mixed with the very hot air, the ignited gases expand and are responsible for the transfer of chemical energy to mechanical energy.
4. The Exhaust Stroke:During this step, the byproducts of combustion are purged from the cylinder and combustion chamber. First, by the pressure differential between the bore and the exhaust port of the head (this is identified as blow down), and then by the movement of the piston upward. The inert gases exit the cylinder bore through the exhaust port in the cylinder head.