In our last installment, we pushed the performance level on our 2006 2WD F-150 with the installation of a JD Fabrication long-travel suspension kit and Bilstein dampers. So, next, it was time to get some fenders back over the wide track from the JD kit and make room for the tires to take advantage of the 16 inches of usable wheel travel we now have.
We turned to Glassworks Unlimited for fiberglass front fenders and bedsides for this project, and purchased a four-piece set of panels for our F-150. The fenders we ordered offer a 4-inch flare and 3-inch rise at the fender arch over the stock fenders. They've also been enlarged to create a wider opening at the back edge near the door for better tire clearance. They will match great with the JD kit that pushes each tire out 4 inches over stock. We're headed towards running 37-inch tires soon, so the flare and rise will make room for stuffing the larger rubber under the front end.
Out back, we chose to use Glassworks fiberglass bedsides for the '04-to-‘08 F-150 with a 4.5-inch flare and 3-inch rise over stock. They come with a contoured area for the fuel-filler door and can be used with the stock tailgate. While it's possible to work with the stock metal bedsides and pull them out almost 1-1/2 inches, it requires inner fender slicing and some reconstruction behind the outer bed panel. We were looking for a little more bedside width, so the replacement bedsides fit the build plan better.
When the fiberglass arrived, we set to work stripping off the factory pieces and installing the Glassworks replacements. The fenders were mostly a bolt-on affair, with some minor trimming and fitment work. The bedsides were more involved, but still manageable as a DIY home project.
Check out our latest progress this month on our Fast-150.
Step By Step

The factory steel fender is on the left and the fiberglass fender on the right. You can quickly see how similar they are, but the fiberglass piece has a larger wheel opening and more pronounced bulge.

We had previously removed the plastic inner fender liners when doing the long-travel install, so those were already out of the way. We removed the three bolts along the upper edge of the factory fender, two in the doorjamb area, and two at the lower edge near the door.

Three headlight bolts need to be removed and the bulbs pulled to set the headlight aside.

With the removal of a final bolt behind the headlight assembly, the stock fender can be pulled. It’s a good idea to line the edges of the door, hood, and front valance where they meet the fender with tape to protect the paint as you work.

With the fiberglass fender sitting in place, we checked for hood clearance and started marking and drilling the holes along the top edge to align with the existing holes on the metal inner fenders. We used a small standard twist drill to start holes and enlarged the holes with a step drill.

We were careful with the body panel gap at the door. We opened and closed the door to check that the door and fender would not rub. The required gap may be more than you expect.

Areas like this corner in the headlight bucket may need trimming and shaping. Both of our fenders needed to be opened up to clear the headlight assemblies.

We cut the fiberglass with a thin cut-off disc in a 4-inch angle grinder and a multi-tool with vibrating blade. Smaller areas of cleanup were done with a flap discs on a grinder and sandpaper. The fenders may not be exactly symmetrical and some test fit and trim iterations are often required.

Holes were drilled in each fiberglass fender and the original fender bolts used to secure the lower edge using the factory nut locations. The final fender positioning requires some pushing around before the bolts are tightened. Having a friend help align the body seams can make this goal far more attainable.

The fiberglass bedsides replace the entire outer bed skin while retaining the inside bed walls. These are 6.5-foot bed pieces. The tailgate, taillights, and bumper need to be removed to remove the factory sheetmetal.

Dealing with the bedsides meant cutting sheetmetal or cutting spot welds to separate the outer skins from the inner panels. We used a simple spot-weld cutter from Harbor Freight in a cordless drill to cut through all the welds. Center punching and pre-drilling a small pilot hole for the center pin takes a little more time, but this keeps the cutter from jumping around as easily.

Accessing the spot welds at the front of the bed requires removing it from the truck or at least sliding it backward about a foot on the frame With all the spot welds cut, we were able to lift off each outer metal panel.

Here’s what you end up with once the outer skin is removed. On the driver side, we had to also disconnect the fuel filler hose from the factory bedside. We set each new bedside in place to check for initial fit and marked a few areas that required minor trimming of the fiberglass piece or the metal inner bedside.

The guys at JD Fabrication have hung a lot of bedsides on these trucks and offered us a tip to strengthen the new bedside and improve the mounting rigidity. As such, we welded a piece of 1-inch box tubing to the factory inner panels to further support the fiberglass bedside.

With the bedsides in place over the added box tubing, we had the bed back in place on the frame and made final position adjustments. We secured each bedside to the box tubing and to the stock inner bedside using large-head 3/16-inch aluminum blind rivets. The factory plastic bed rail covers were reused and glued onto the fiberglass. We drilled the fiberglass bedsides where the taillight pins are inserted and reused the factory plastic bushings from our metal bedsides.

Here’s another tip we picked up from JD Fabrication. We mounted the bedsides so the trailing lip at the tailgate sits to the outside face of the stock inner bedside, rather than to the inside face. This leaves a gap at the tailgate joint allowing the tailgate to fit well. Otherwise, you have to sand the fiberglass very thin to fit at the tailgate joint or remove the tailgate. Some minor grinding of the inner bedside sheetmetal helped get a close fit.

As the final step, we modified the stock bedside support rods and reused them on the new bedsides to keep the lower end of the panels from flapping around.

We chose to build the bumper from 2- by 0.120-inch wall DOM tubing. After making a few bends in the main loop, we set it in place to fabricate the mounts. You may have noticed we’re sporting a new front bumper on our truck. We shed the stock bumper and made plans to fabricate a bolt-on replacement. We started by cutting off the front frame horns flush with the factory bumper mount plates.

Front bumper brackets were boxed from 3/16-inch plate. One-inch support tubes were added near the ends of the bumper and an aluminum skidplate added to fill in the area below the bumper and between the front frame rails.

Ford saw fit to mount the power steering cooler line down low on the front of the lower A-arm crossmember. Not a great spot for protection off-road. We welded a piece of box tube spanning the frame rails and moved the cooler line up higher, needing only to make one hard line bend to reposition it. The cooler line is now protected behind the new skidplate.
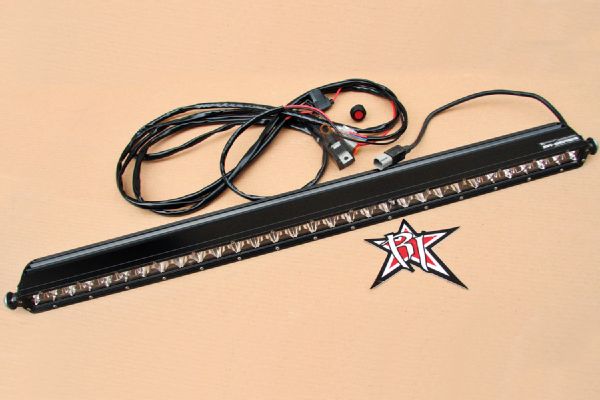
We topped our bumper with a Rigid Industries SR-Series light bar. The single row LED bar is a 30-inch spot and flood combination light. It’s discreet at a mere 1.5 inches tall but throws substantial light in front of our truck. A full hookup harness and dash switch are included.

Six of the LED reflectors on each end of the bar throw a flood pattern to the side of the main beam, while the 28 LEDs in the center of the bar compose the spotlight portion of the beam. The 30-inch bar draws only 104 watts (7.2 amps) to throw out 9,600 lumens.

Here’s the finished front bumper with our Rigid LED bar mounted using a set of their weld-on light tabs. For now, it’s got several coats of rattle-can spray. Once we get around to the back of the truck and build a new bumper there, we’ll have both bumpers powder-coated for a more durable finish.