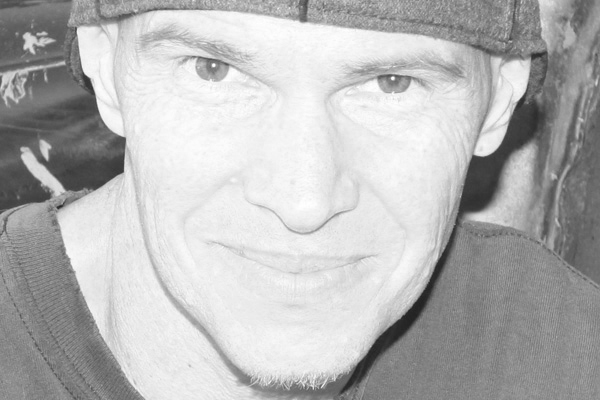
Kevin Blumer
Contributor
Bumpers are a great fabrication project, especially if you aspire to bigger and more intricate endeavors, such as building a rollcage or fabricating a custom suspension system. Build a bumper and you’ll have the chance to learn about tube bending, tube notching, symmetry, cutting and forming plate, and, of course, welding. If you’re unhappy with the resulting bumper, it’s easy to set it aside and build another one. It’s a lot tougher to redo a bad rollcage, and it’s downright dangerous to put a badly executed suspension on the street or the trail. Start your fabrication career the right way by building yourself (or a lucky friend) a bumper.
Step By Step

1. Every bumper needs a strong foundation. Locate your attachment points. Quite often, the stock mounting points will work just fine. As for our ’04 4Runner, we decided to fabricate a custom crossmember and weld that across the front framehorns. We’ll anchor the bumper to the outermost bolts on the front face of the crossmember.

2. We’ve also welded an attachment plate to the forward most A-arm crossmember. This will serve to stabilize the bumper that much more thoroughly.

3. You can start with a drawing, or start with a mental picture. We started with a mental picture and a short piece of tubing. The short stick of tubing let us try a number of routes across the grille, and allowed us to see what would clear and what would hit. We weren’t using the front edge of this factory bracket anymore, and it was in the way.

4. A Dremel tool with a cutoff wheel attachment trimmed the extraneous material and opened up our intended route.

5. It seems like more and more bumpers today are built primarily using plate instead of tubing. We’re going to use a bit of both. The first step was to tack weld a piece of 1⁄8-inch-thick plate onto the bolt-on mounting pad. The large plate measures 9x13 inches, and will be trimmed into its final shape later on.

6. The winch is mounted onto the frame’s front crossmember via bolt plates. The winch’s solenoid box was in the way of our intended tubing run. Worse yet, in this position the only way to plug in the remote control is with the hood open. Relocating the solenoid box will solve two problems by making room for bumper tubing and making the remote control connection more accessible.

7. Here’s where the solenoid will end up, held in place by a bracket that’s yet to be fabricated.

8. The winch’s engagement lever will also get in the tubing’s way, a problem that’s easily solved.

9. It’s possible to carefully clock the housing into a new position by removing the bolts along the perimeter of the planetary housing. Take care, as there are several parts that can fall out of order if you get clumsy with this step. Nervous? Have your local 4x4 shop handle this.

10. With the solenoid box moved, there’s room to run this tube.

11. The lower tube will run below the winch mount.

12. The holes were carefully laid out on each plate, and then bored with a hole saw mounted in a handheld drill. The plate was trimmed down using a Piranha ironworker at Desolate Motorsports, but careful work with a Sawzall will suffice if you don’t have an ironworker machine or a large metal-cutting bandsaw available. There are four plates, two per side.

13. Two short sections of 1.5-inch square tubing were welded together in a “T”. This will be enclosed in the box sections and won’t be seen, but it will add substantial stiffness and strength to the assembly.

14. Hopefully the mental picture is making more sense now. We’ll call each box section a “bulkhead”. Short stubs of tubing were used to help align the outer plates, along with machinists’ blocks along the back and bottom edges. The back and bottom edges were used as references while the holes were being laid out. Several strong clamps are essential for a project like this.

15. It wasn’t necessary to weld every edge of the inner structure. We used a front-loading Weldcraft WP-225 TIG torch in order to reach in between the plates. Arc-Zone.com is our source for genuine Weldcraft products. Our TIG machine (not shown) is a Lincoln Precision TIG 185 that’s been in action since 2004.

16. The bulkheads and the main tubes are mocked into place but are not welded to each other just yet. Look at the heat marks on the bulkheads and you can see the extent of the welds on the internal square tubing structure: just enough to gain the desired strength and reinforcement.

17. All the unfinished seams shown here will be welded in the end. This will add up to a very strong, rigid structure. The main tubes are 1 3/4-inch, 0.120-inch-wall thickness.

18. Time to bend the main tube! This step was a little scary because both bends need to be in the same plane. Precision bending is much easier if you’ve got a powered bender, and Swag Offroad’s bender conversion kit (used with a Harbor Freight air-hydraulic ram) puts a powered bender within almost any budget. If you get Swag’s weld-it-yourself bracket kit, then you’ll save even more cash. Tube bending is a skill just like welding. There’s not room enough for a bending tutorial within this story, so we’ll write a stand-alone tube bending story in a future issue.

19. The driver-side bend was where we wanted it to be. Now it was time to make a mirror image bend on the passenger side. Since we’d written down the final length of the hydraulic ram, it was easy to bend to the recorded measurement.

20. We double-checked the first bend with a protractor, and tightened the set knob to lock the measurement in place. This protractor is part of the Tube Bender Survival Kit from Van Sant Enterprises. After the second bend was performed, the protractor verified we’d gotten it right.

21. There’s more than one way to get the bends lined up in the same plane, but the one we’ve seen most professionals use is the “eyeball” method. You sight down the tube and line up the bend with the top edge of the die. Do this while the tube is loosely clamped in the bender, and then tighten things down when the tube and the die are properly lined up. Done correctly, this is more accurate than using a bubble level. Take your time. Coincidentally, the white fridge behind the tubing made it easier to get things lined up. Can’t see? Put some white paper in the background or rig up some more lighting.

22. Since we’d written down our bender measurements (taken at the hydraulic ram) it was quick and easy to perform the second bend. Next, we needed to notch the tube that would intersect the main tube. An angle indicator from Van Sant Enterprises showed us where to set our notcher.

23. The JD2 TN-100 notcher (also sourced through M-Tech Supply) uses a basic design, and the rugged, precise construction has performed well for several years to date.

24. One-and-a-half od tubing slips snugly inside of 1-3/4-inch, 0.120-inch-wall seamless tubing. We’d planned around this.

25. Nothing is tack welded yet, but the pieces fit together snugly enough that carefully placed supports held the assembly well enough to check the fit relative to the body lines. It’s common for frames and bodies to be slightly mismatched, and you want the bumper to flow with the body lines.

26. The angle iron at the bottom of the photo was temporarily tack welded to the bolt plate, supporting the bumper during the mock-up process. A 1⁄8-inch-thick piece of flat stock was slipped between the angle iron and the bumper. This lined the bumper up with the body.

27. There were two tubes left to add, running between the bottom of the bulkhead and the upper tubes. Translation: two bends and two notches.

28. You can use the main die itself to help you get an idea of how the imagined tube will fit after it’s bent.

29. One bend performed, now we need another.

30. Careful notes taken during the first bend made correct repetition possible.

31. More measurements were taken. We needed to know where to place our notch, and what angle was needed. A floor mat worked as a square layout surface.

32. Once the tube was in the notcher, we measured how far the tube stuck out past the holding jaws prior to cutting the notch. Again, this measurement ensured repeatability. We also checked to make sure the tube was vertically aligned with the notcher before firing up the drill.

33. Before tacking the short tubes in place, the mounting pads were tied to the bulkheads more thoroughly by adding gusset plates.

34. In an effort to keep things from distorting during final welding, the whole shebang is stitch welded onto a 2x6-inch section of heavy-wall box tubing. There’s more to do, but deadline and space constraints mean we’ve got to stop here for now.