You would have to be pretty new to the wide world of street rodding and hot rods to not know the name Fred Warren. The 75-year-old lives with his wife, Patty, in (coincidentally) Warren, Ohio, and he owns one of the better collections of award-winning rods in the country. He says he “only owns eight hot rods”, but those eight would include two AMBR-winning roadsters (the “Smoothster”—the winner from 1995, and “Shockwave”, the 1999 winner), one Ridler winner (the blue “Aero Coupe” from 1994), a pair of Marcel-built Murocs (one roadster and one with fenders), a Ridler contender (the “Aftershock” coupe), plus a couple of others.
Not only a patron of rod builders, Warren also works on and helps build his cars, fabricates parts, and does exquisite wiring jobs on his rides. But he’s the first to admit there is one thing he doesn’t do, and that’s bend metal. He leaves that to the experts, which is why in 2010 he was happy to find Bobby Walden’s booth at the Grand National Roadster Show in Pomona, California. Warren knew of Walden’s metalwork on George Poteet’s “Snyper” project back in 1997, and thought Walden was still living/working in Texas.
Though the two had never met before the 2010 GNRS, Warren introduced himself, liked what Walden had to say, and asked him if he would scratch-build a coupe for him. The two discussed what it would look like, and Walden suggested Warren contact illustrator Jimmy Smith to get his ideas down on paper. Warren called Smith, and the two talked for about an hour and a half. In a few days a drawing arrived and, after Warren looked at it and saw it had everything he and Smith talked about, he said “That’s it! We’re gonna build that car!”
The team at Walden’s Speed Shop (Walden, Wesley Kent, Blake Tomlinson, and Matt Bryant) in Pomona started with a stack of 4x8 sheets of 19-gauge steel and, a year-and-a-half later, rolled a pristine one-off coupe out of their shop that combines design aspects from both 1932 and 1933 three-window Fords. Expressing how he feels about his coupe, Warren says it’s “better than anything he’s got”, and that’s really sayin’ something! This month’s article will cover the car from its beginning up until the first time Walden’s was able to set it on the ground with all of its drivetrain in place. Next month’s article will carry on from that point, and you’ll get to see the finished project, inside and out.

The project started after Walden designed and built a one-off set of framerails, then dialed in where the front wheels will sit.
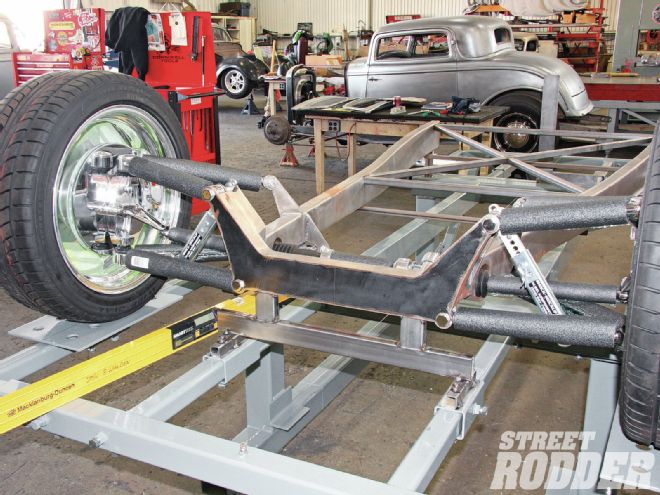
The front suspension uses a Kugel Komponents IFS system, which Fred Warren also has on two of his Muroc roadsters.
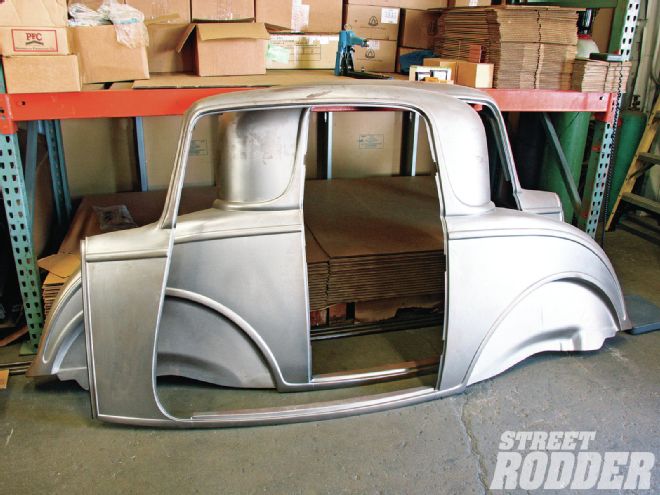
Though he had ’32 side panels from Brookville Roadsters, very little of the stampings would be used in the final product.
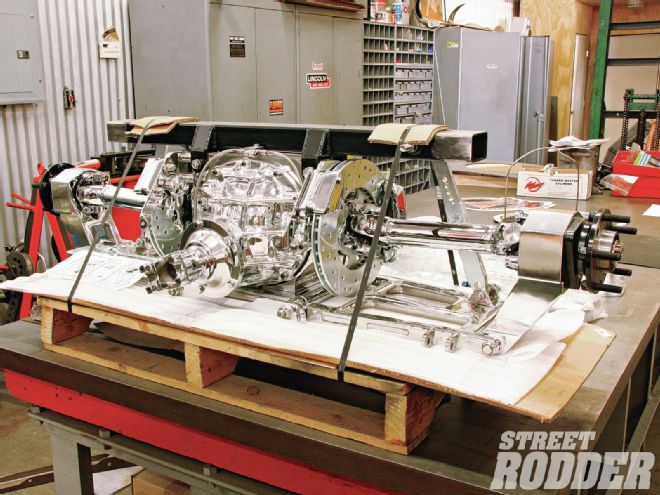
A fully polished Kugel Komponents independent rear assembly would also be used in the coupe.
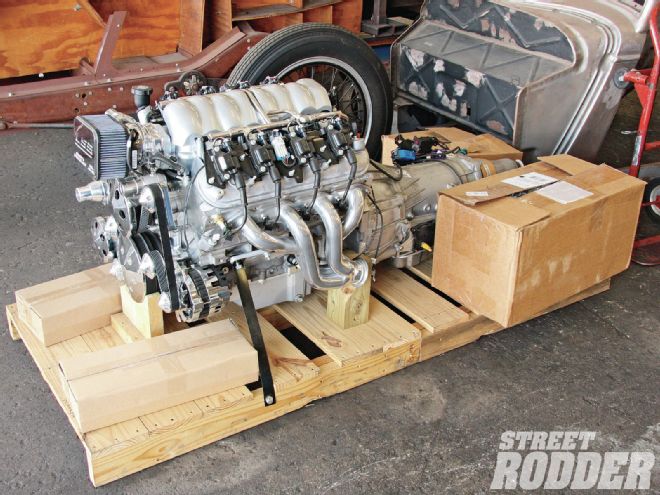
The last bit of over-the-counter items for the three-window was the LS3 crate motor (from Mark Campbell at Street & Performance) and a 4L70 trans.
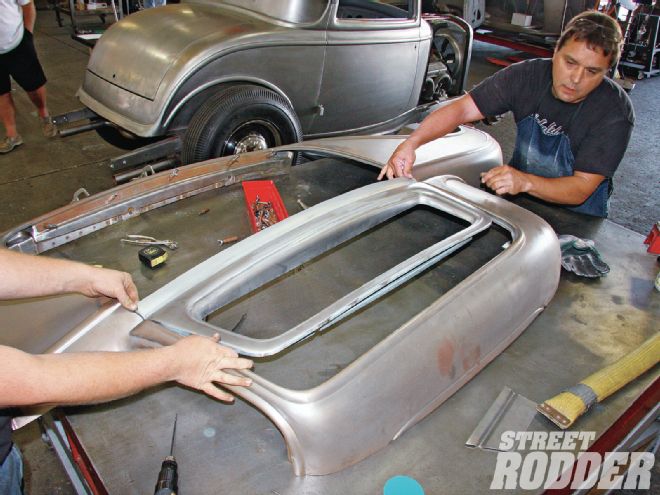
Using just the doorskin, Walden cuts off the window section, chops it (following a template shape he has), then attaches it to the factory side panel to see how much will be taken out of the roof.
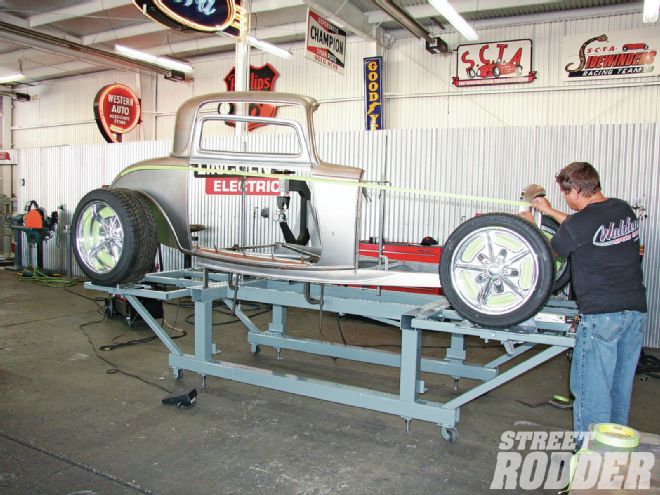
The side panel is placed on his jig, and tape is used to eyeball where the coupe’s body line will be, plus the height of the grille and radiator. (Note the rear wheel is placed just for general reference).
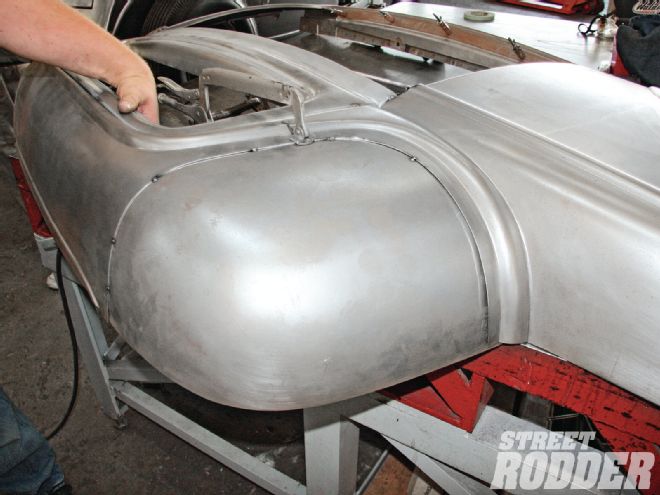
The corner of the roof is cut, and then the roof gets chopped to match the window opening. At that point the corner is reattached.
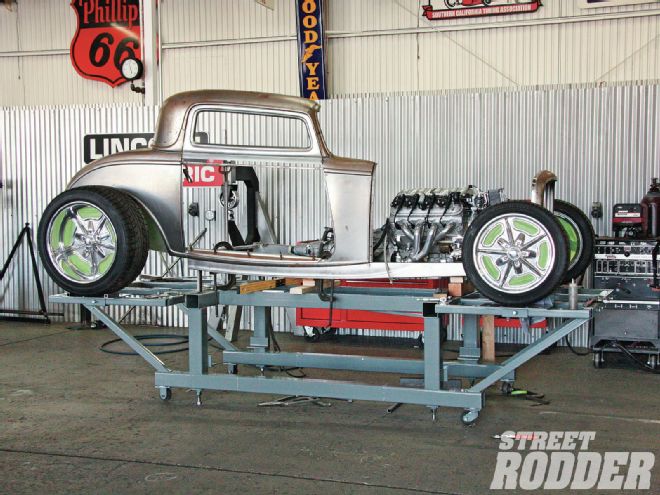
The modified profile is now starting to come out, though Walden already knows at this point much of the stock cowl, quarter-panel section, and rockers will be replaced with hand-fabricated pieces.
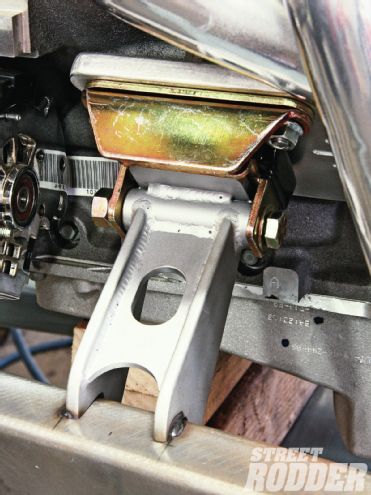
Lots of little parts were handmade for the project, too, including the LS3’s engine mounts.
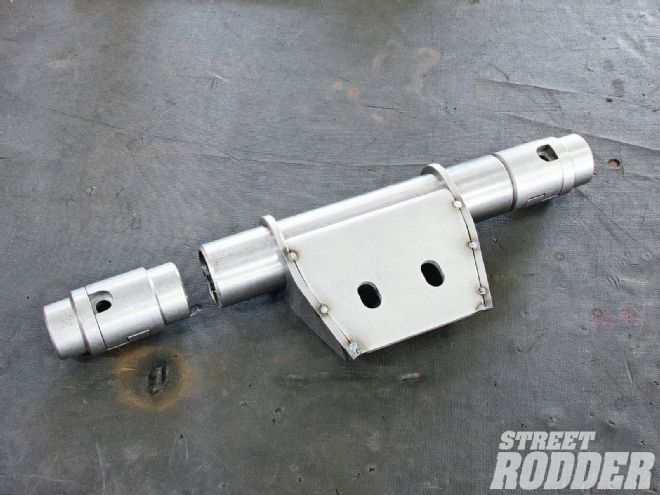
For easy transmission removal, a slip-collar section was sectioned into the transmission mount. (Refer to the Feb. ’11 issue of STREET RODDER to see how it was installed.)
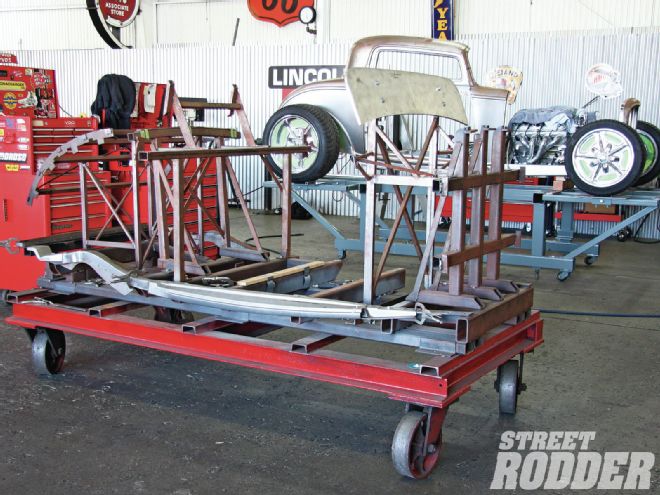
For the past five years Walden has used this ’32 coupe fixture he built to locate various points. Its sections bolt together, so he can add or subtract stations as he needs them.
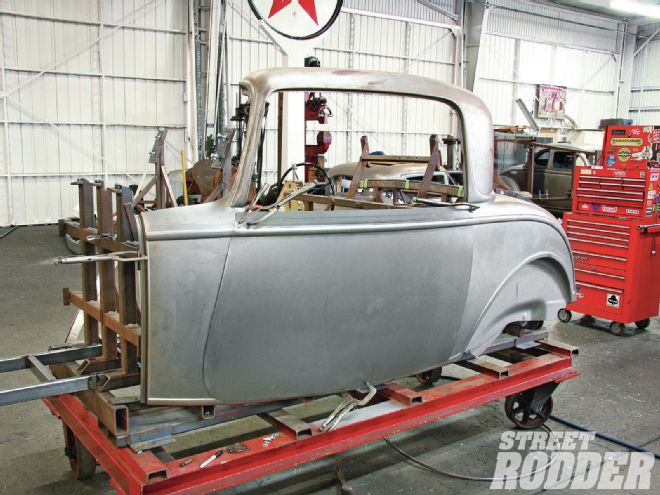
This is what the driver side section (with unchopped doorskin) looks like attached to the fixture.
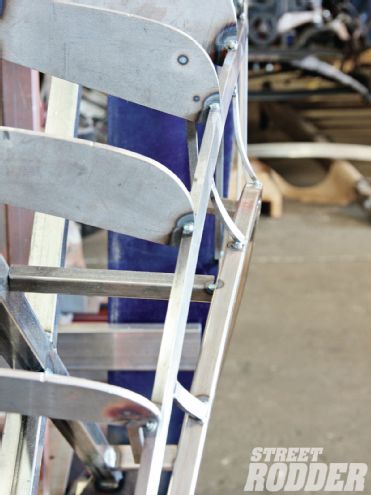
This is a bolt-on addition to the fixture, made just for Warren’s coupe, as it will have raised wheelwells and a roadster-type flair.
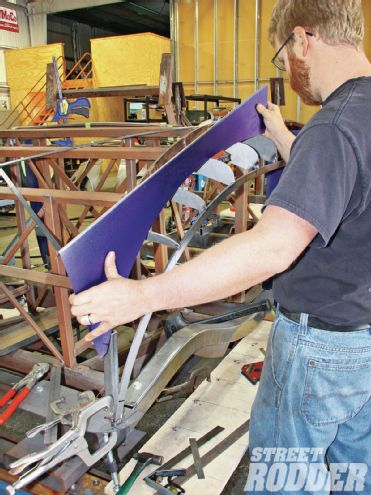
To copy the exact shape of the new addition to the other side of the fixture, Blake Tomlinson makes a template to transfer the information.
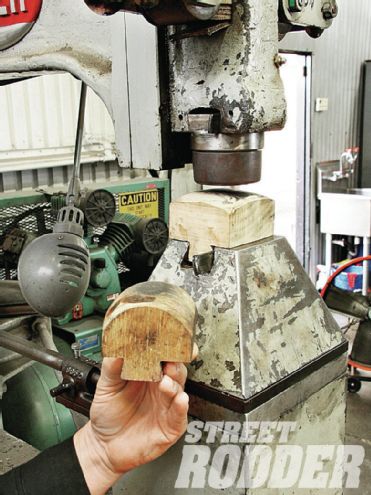
To do the forming of the quarter-panel on Walden’s Yoder powerhammer (but not shrink or stretch the metal), wood-forming blocks were made to work with a rubber upper die.
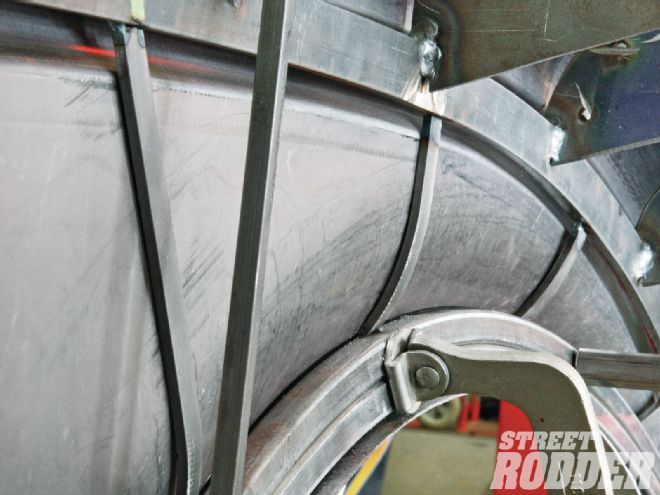
As the quarter-panel is fabbed, it is checked and rechecked against the fixture for fitment. With this view looking out from inside the trunk, you can see there are no gaps between the panel and the fixture.
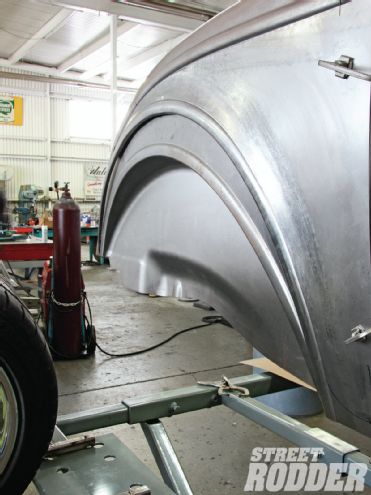
To demonstrate how much the wheelwells were raised, the new quarter-panel is laid on top of the old skin.

Custom dies were also made to press sections of the body’s beltline that couldn’t be formed on any of the presses.
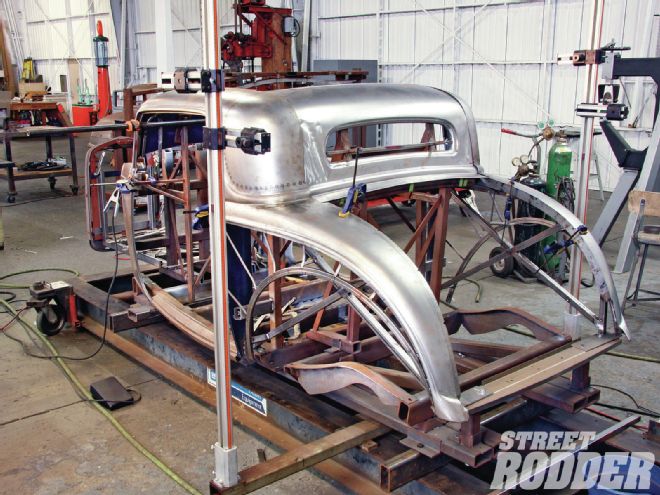
With the two side sections already chopped and attached to the fixture, Walden then chops the rear window (while it’s out of the car) and then adds it to the right and left body halves. (Note: the strip of quarter-panel from the roof to the rear apron is all that is left from the original Brookville side stamping.)
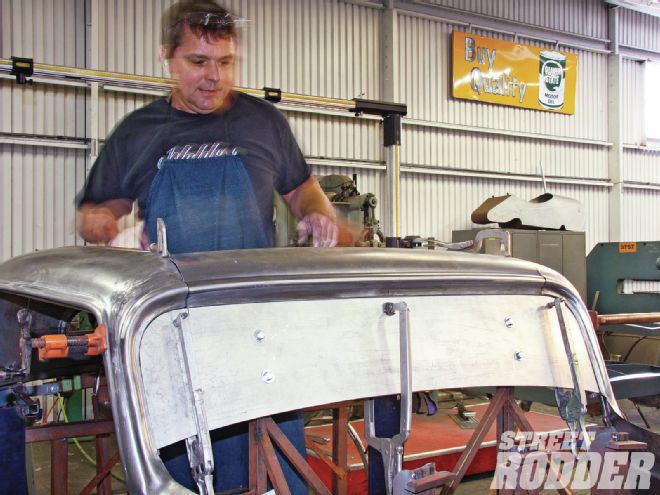
Walden has two windshield templates when he chops a Deuce coupe: a 3.5-inch and a 5-inch. Warren’s car got the 3.5-incher.
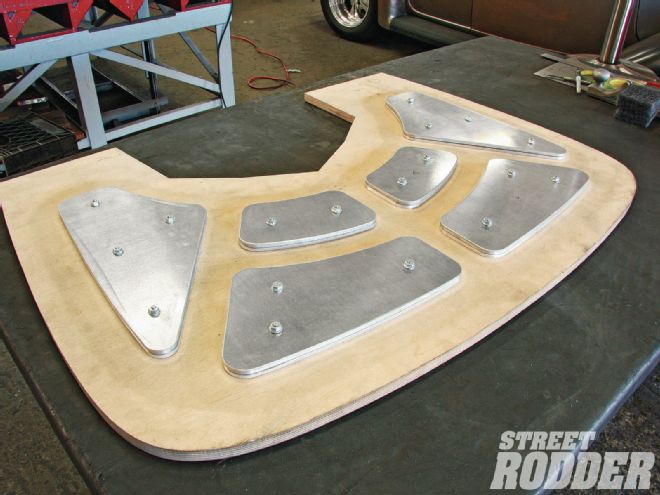
Warren’s car has two firewalls—an inner and an outer. To duplicate the designs for both, a die was made that allows the sheetmetal to be clamped down and the exposed areas run through the Pullmax, mashing that area down and creating a reveal.
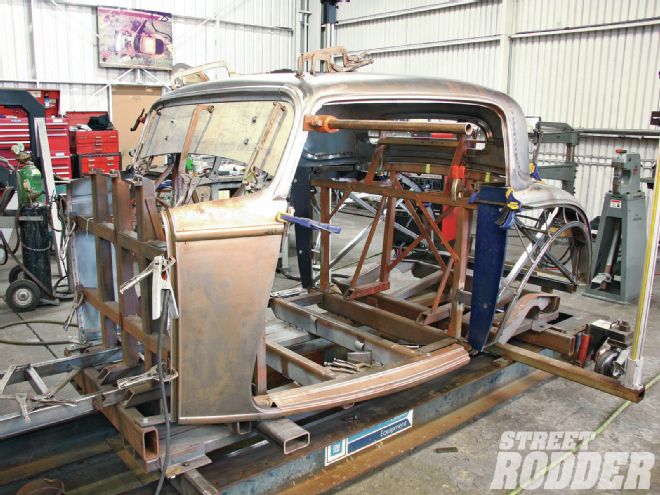
Walden didn’t want the “kink” in the cowl all ’32 Fords have, so he made a new side cowl section that runs straight from the hood side and back to the door. He also widened the opening for the firewall by an inch, narrowed the posts from the beltline up, and redesigned the rounded corner at the base of the door.
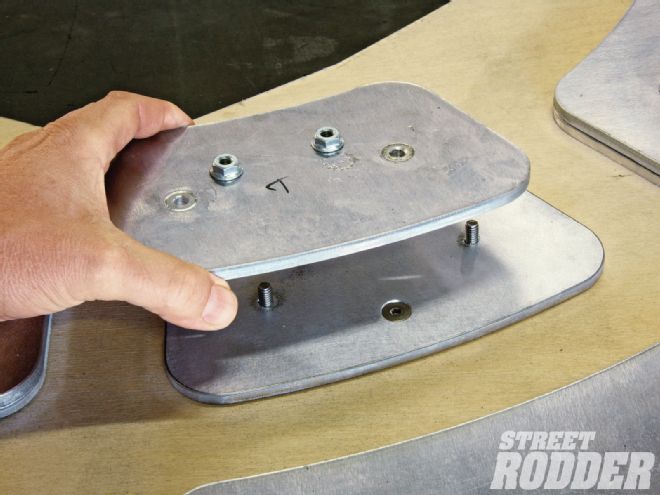
Holes are drilled in the sheet so it will fit between the two dies, which will be bolted together.
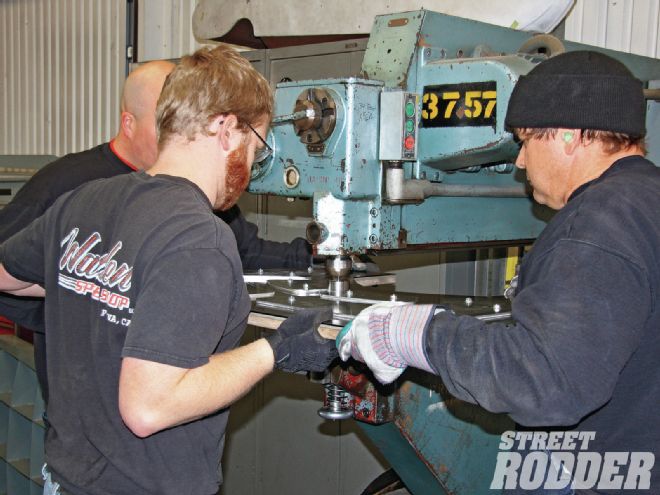
The big fixture is run through the Pullmax, and it takes a few hands to make sure the die evenly stamps the metal.
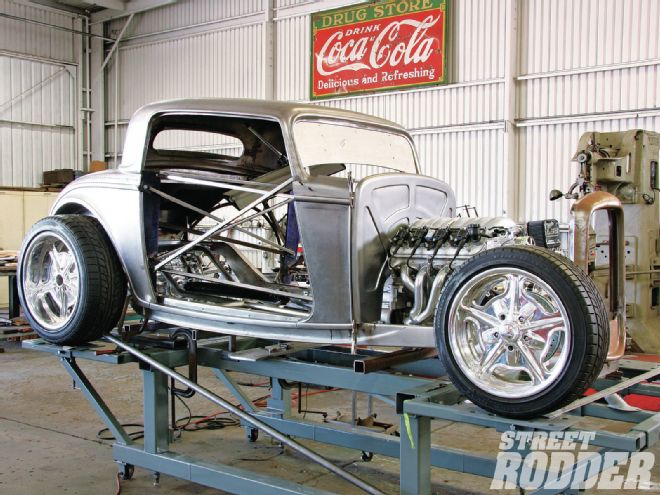
To help locate how much kick will be needed in the rear section of the frame, the wheels are set in place and measurements made.
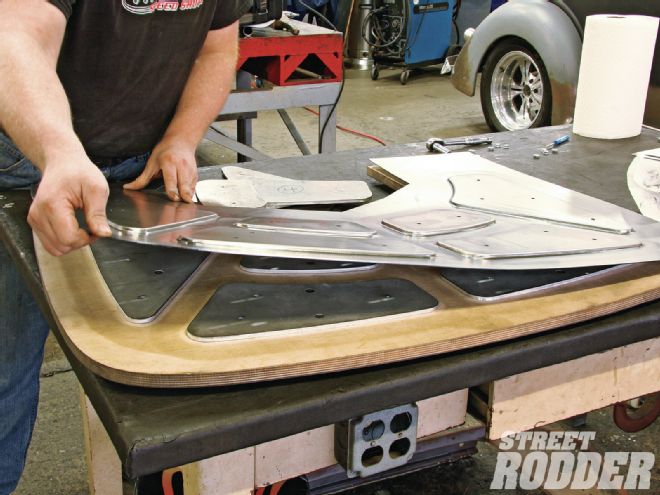
After the work is done, the top dies are removed and the firewall can be removed from the fixture.
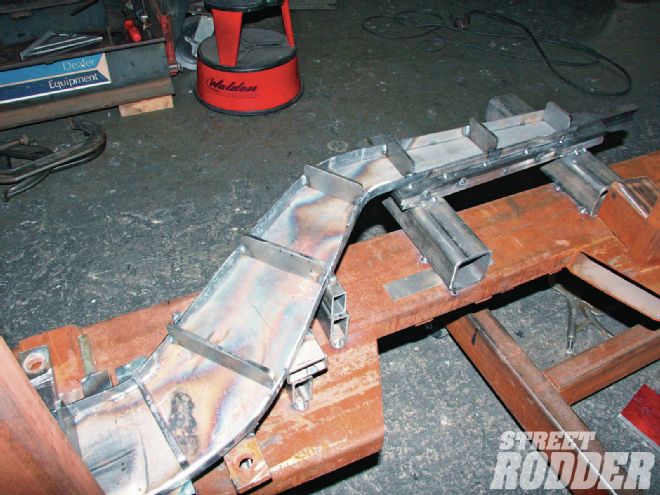
The framerails Walden custom fabs are two-piece and made on his flanging machine. This photo shows the one half in his jig, with gussets added to keep a uniform width when the second half is put in place and welded.
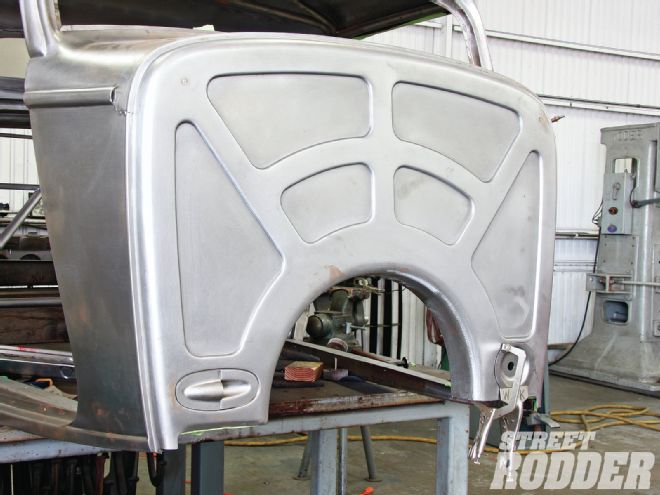
With the inner and outer firewalls made, the coupe’s wiring and A/C hoses are run between them to keep them out of sight.
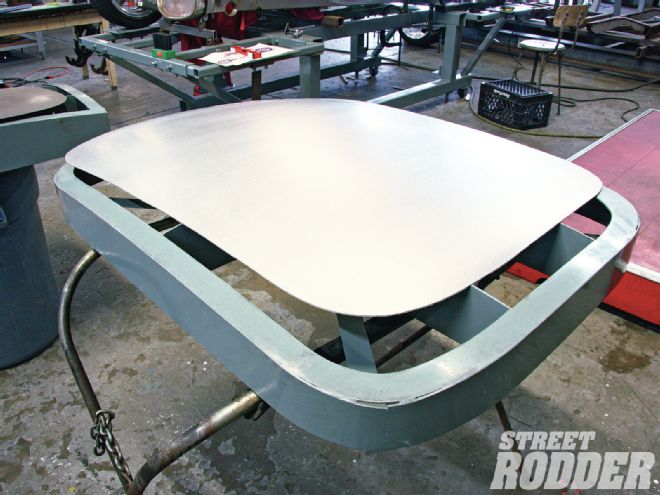
Walden made the buck for the ’32 coupe roof inserts that he made back in 1995. (He also sells others years, too). They’re made from 19-gauge steel and pounded into shape on his Yoder machine.
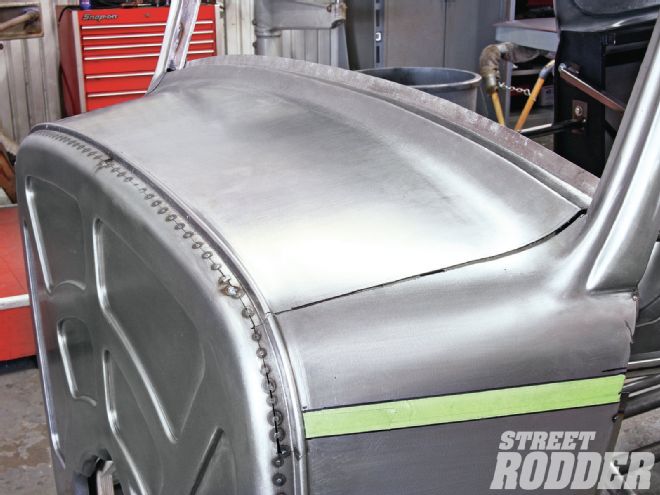
The cowl top is also hand fabbed on the Yoder with a linear stretching die and a rubber forming die.
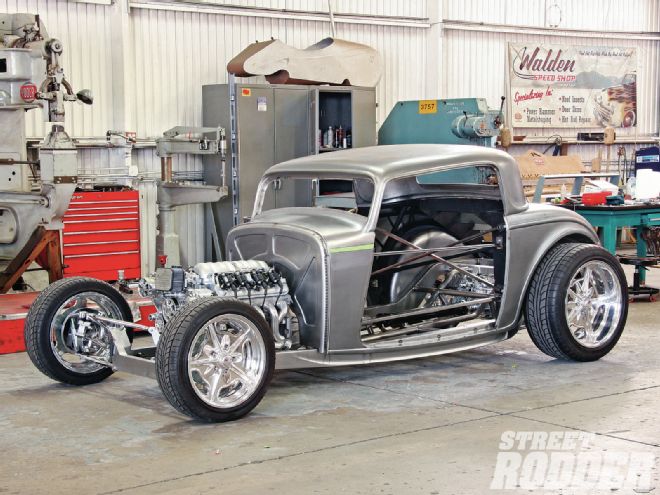
This was the first time the car was on the ground with its suspension and drivetrain in place, as well as the cowl, firewall, roof, and quarter-panels in their final form. In the next article, we’ll look at the tubular inner structure of the coupe, how the decklid, doorskins, trans tunnel, and floor were made, plus the entire finished car in metal.