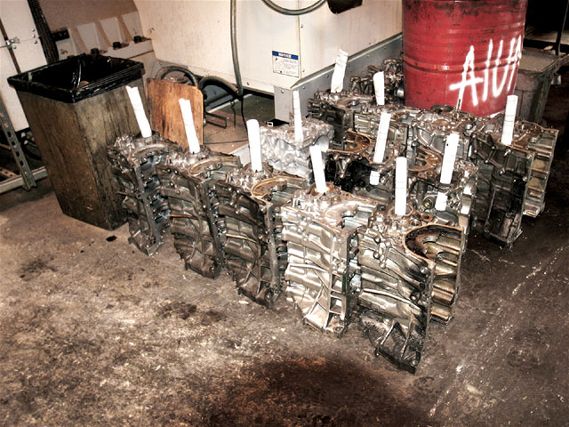
Beefin' Up The K-Series
"Steve Austin, astronaut. A man barely alive. Gentlemen, we can rebuild him. We have the technology. We have the capability to build the world's first bionic man. Steve Austin will be that man. Better than he was before. Better, stronger, faster." This opening narration to the '70s television classic The Six Million Dollar Man becomes much less farfetched with every dawning decade. While we have yet to embark down the path of robotically enhanced humans, the revival of Honda engines has become a specific science. When a semi-catastrophic failure renders K-series cylinder walls unusable, there are only two choices: toss it or sleeve it.
Of course, sleeving is not just for the revival of bloodied and scarred powerplants. The process of replacing a Honda block's relatively weak aluminum inner structure with specially designed ductile iron inserts is classically used to allow for greater power. Stronger cylinder walls can hold more compression, more boost, or more nitrous-induced bang. Snapped connecting rods or DVS (dropped valve syndrome), thereby grinding up any surface of the engine that sees combustion beyond the point of machining, happens. Sleeving is often the only option for making something useless useful, and like Lee Majors, this time around it'll be better, stronger, faster.
The Same, Only Different
When it comes to the K-series, engine replacement versus sleeving costs are competitive concepts. Replacing the engine is easier but never as strong. Naturally, one might ask what the major differences are between sleeving a K-series engine and the tried-and-true methods of sleeving the more commonplace D- or B-series. Remarkably, the processes are similar. Special considerations, like machining dimensions, and other application specifics aside, Honda engines are Honda engines. Newer models have the same anatomy but with a bit more spit and fire. Sure, the blocks have advanced but true evolutionary changes lie within the cylinder heads. Still, block sleeving is not something to be taken lightly. Newer engines have higher performance potentials that require tighter tolerances. In short, just because sleeving a K is not much different than a B doesn't mean a more specialized procedure needn't be followed.
It's Who You Know
For such an invasive operation, experts like those at Golden Eagle in San Dimas, Calif., must be at the helm. Golden Eagle has been in the sleeve installation business for nearly 10 years. The process is handled by a single technician-one internally trained and capable of the company's specialized methods. Note: Golden Eagle sleeves are not for sale. They are only available through the machine shop's professional installation services. There are a number of factors to consider when installing sleeves so don't trust the job to just anyone.
CNC Demolition
The first step in sleeving an engine is to remove its old cylinders. Honda blocks are made as one-piece, die-cast aluminum units. Aluminum isn't up to the task of withstanding conditions inside the cylinders, so a steel (or composite) liner that is usually fused to the aluminum cylinder structure during the casting process, is used. Since the cylinders are indeed a part of the casting, taking them out calls for removing a bit of material. The cylinders must be cut down and their top sections removed; they're then machined farther down, opening up their bores to accept new sleeves.
Golden Eagle employs CNC (computer numerically controlled) dissection when it comes to sleeve removal. That's right. While many engine builders use barbaric technologies like vertical boring machines and prehistoric deck grinders, Golden Eagle CNCs everything. For those unaware, the CNC process ensures accuracy, which is key to long lasting, reliable engine builds. As a general rule of tooling, the work being done can only be half as good as the tools being used. Therefore, to get the best product, only the best tools should be used. With full Haas machining centers one can be comfortable knowing that Golden Eagle performs sleeving to the best attainable tolerances and with the latest technology.
About Those Sleeves
Once the cylinders are removed, the block is brought up to proper specs to accept Golden Eagle's specially produced ductile iron sleeves. The sleeves are made of a proprietary material that is formulated differently than other sleeves to promote better piston ring bedding-critical for optimal sealing of both compression and oil. The sleeves are individually machined in-house from solid iron billets. Typically, iron can be heat-treated to provide greater wear resistance, but in this application heat-treating is not necessary since wear isn't a concern. In fact, such treating would counteract the material's properties, obstructing proper ring seating.
This is a good time to note Honda's siamesed or open-deck block configuration. Each cylinder is joined inline with open water jackets surrounding them. The design promotes efficient cooling but lacks the lateral stabilization of a closed-deck block, which can lead to instability at Honda-capable engine speeds. So, as part of the sleeving process, the new cylinders will be braced for greater stability. The spline employed by Golden Eagle is specifically placed in the upper-middle portion of the cylinder where cylinder deformation begins to propagate upward. The splines fit against the water jacket's internal walls thereby bracing the cylinders against the block. This method promises to keep cylinder deflection in check while minimally effecting coolant flow. Other sleeves can restrict coolant flow to the cylinder head, making driving dangerous for spurts longer than a quarter-mile at a time.
Measuring And More Measuring
Installing sleeves requires a lot of measuring. Since holes cut into the block will have some degree of variance, Golden Eagle prides itself in ensuring that each sleeve is specifically machined to fit in place. Similar to how Honda engine bearings must be matched and spec'd by color, it's not surprising to find out that piston rings must also be gapped correctly and sleeves must be machined to variable tolerances to fit properly in the block. The fit to be achieved is a perfect press fit. No fasteners will hold the sleeves in place so machining must be done to as exacting a standard as possible. It is another factor that makes a Golden Eagle installation more reliable, if not for longevity, for pure peace of mind.
Pressing Your LuckOnce sizing and final trimming is completed, the cylinders are sealed together in their final siamesed configuration and pressed into their new home as a single piece. Just when it seems like you're out of the woods, the risk of cardiac arrest is ever present. Pressing in the cylinders is one of the most critical parts of the process. They must be perfectly vertical when mated with the engine to avoid binding or cracking the block. It's important to know that the cylinders have been pressed in completely. An unfortunate consequence of lack of attention to detail may cause sinking issues further down the installation process.
Step Off!
To understand sinking, one must also be aware of step decks. A block must be decked to create a nearly perfect flat top in order to promote proper head gasket sealing. In a step deck, an even greater seal is achieved by machining the cylinders slightly higher than the rest of the deck. Naturally, one would expect the cylinders to have a very tight seal after this sort of operation. However, this is only true if the cylinders don't sink. If they're not pressed into the block far enough then the step deck will cause the head to push the cylinders farther down once torqued. This not only weakens the cylinder wall seal but also creates a general failure in the head gasket's ability to keep oil and water divorced. Ensuring that the cylinders are fully pressed into the block before performing the step deck is critical to maintaining proper engine sealing. Golden Eagle's press process guarantees such a fit, and the block is decked again utilizing CNC machinery to achieve a 0.003- to 0.005-inch step. It is yet another reason to have those sleeves handled by a pro.
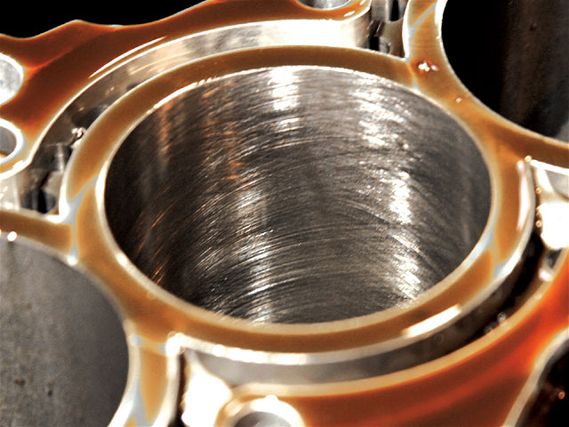
Don't Forget Those Pistons
Our sleeving tour is almost complete. The last step involves the pistons. When you send off that block for sleeving be sure to include those pistons. Providing them will allow your machinist to create a specific bore, hone the walls to a perfect match with ideal tolerances, and maybe even gap those rings for you. All of this may even help prevent piston slap, which is especially prevalent when using forged pistons. Piston slap occurs when the pistons clack back and forth within the cylinders. Forged pistons have high thermal expansion properties that usually cause slap at startup but goes away as the engine warms up. When it doesn't, there's too much clearance between the pistons and cylinder walls. Naturally, with proper fitment the annoyance and potential issues with piston slap can be avoided.
If You're Gonna Sleeve It...
It should be expected that in big-power upgrades internal engine strengthening would be required. Pistons are usually the first to go, suffering from burnt or cracked ring lands. Typically, forged pistons beget forged rods, and why not throw some head studs in to keep that head gasket confidently smashed? In all too many cases, however, sleeving the block is seen as an excessive or unnecessary precaution against catastrophic failure. It is given by experience that a stock Honda engine can withstand stints up to 10-12 psi, or 12:1 compression with proper fueling. When engine speeds rise, and cylinder pressures increase, longevity reduces drastically. So, many who add aggressive performance modifications to their daily, or even weekly drivers find themselves sidelined with repetitive and expensive repairs due to neglecting to "do it right the first time." For those going to the extent of installing forged pistons and rods, make some room in the budget for sleeves. Even if extreme power isn't the goal, sleeving the block will add tens of thousands of miles to any over-achieving Honda engine.
On an ending note, it should be mentioned that while Golden Eagle sleeves will hold up to 60 psi, the most critical part of an engine build is fuel control. It has been proven time and time again that performance upgrades are only half as effective at best without corresponding computer tuning. Everyone's budget should have a spot for this important aspect as well. Power is nothing without control. What good is a cyborg without adequate programming anyway?