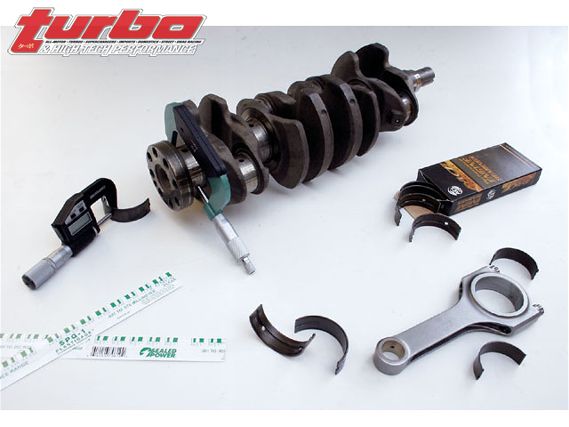
Engine bearings do many things. They support moving parts like crankshafts and connecting rods, but they also play a role in determining an engine's oil pressure and protect the crankshaft from being damaged by micron-sized particles. Improper bearing selection and/or sizing can result in problems ranging from poor oil consumption to all-out, catastrophic engine failure. Ensuring that the correct bearing size, and therefore proper clearances are selected, can be accomplished relatively easily and for surprisingly little money.
Plain, or sleeve, bearings are the most common type used today. Such bearings come in half-shell-shaped pairs that, when matched together at their parting faces, encompass a crankshaft's main journals and rod journals 360 degrees. Bearings can be made of a variety of different materials and always consist of a soft and a hard material cast, sintered or bonded to one another. Bearing material choice affects factors such as engine longevity, corrosion resistance and the ability to withstand fatigue and occasional detonation through increased load capacities. Babbitt, copper-lead alloy and aluminum are a few of the most widely used surface-coating materials of recent years. No matter which material is selected, all three are coated on top of a low-carbon, hardened steel backing-the material that makes up a good portion of the bearing shell, gives it its shape and receives the brunt of the load. Such coatings are applied in approximately 0.01-0.02-inch layers.
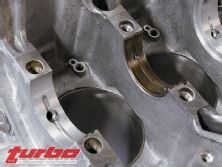
Babbitt is just about the oldest bearing surface coating and is probably the least used today. Its most useful trait is its high rate of embedability, a situation in which the bearings are more likely to pick up foreign particles, keeping them from scoring the crankshaft or floating in the oil film. The particles simply make their way around the bearing until they are completely covered by the material. Pull an old bearing out of an engine and you're sure to find speckles of particles thanks to the bearing's embedability characteristics. Of course, religious oil changes make a bearing's embedability less of an issue. Babbitt bearings also have a higher rate of conformity, which lends itself well to nitro and alcohol engines with extreme cylinder pressures. Copper-lead alloy bearings on the other hand are highly resistant to fatigue and extremely durable-not so much for the nitro engine but perfect for the typical race engine and most any street engine. Such bearings consist of a sponge-like layer of copper interspersed with lead particles. This combination allows for copper's strength and lead's embedability properties. Finally, aluminum bearings share many of the same characteristics with copper-lead alloy bearings but are even more resistant to corrosion. Aluminum bearings rank lower in deformability and embedability but that's becoming less of an issue with today's more sophisticated filtration systems. The aftermarket has also concocted a few different surface coatings including various alloys designed for even greater corrosion resistance and strength and there are certainly other less popular materials from years back such as tin-based and lead-based alloys as well as others that were cast directly as part of the connecting rods.
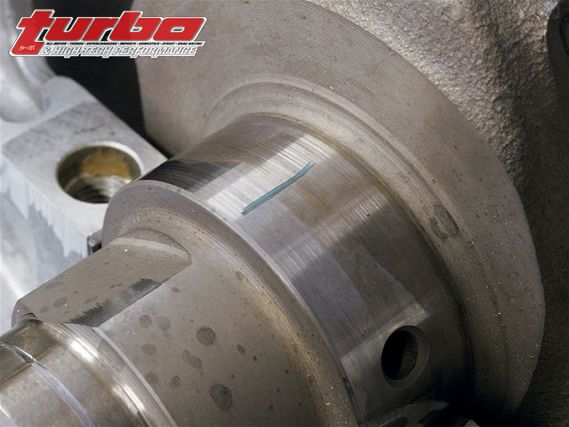
There are a few more terms to go over before discussing bearing sizing. Spread comes to mind first. This refers to the bearing's slightly larger arc in comparison to the block's bearing journal. In short, the spread is what keeps the bearing in place during assembly. You'll notice this from the snapping sensation when positioning a bearing in the groove. Crush also refers to an oversized condition, but in a different way. Bearings are manufactured so that when they are placed in the block and main caps their edges protrude above the block's or main cap's parting surfaces. The protrusion is minimal-just enough to barely grab your fingernail. The added material results in a crushing condition in which the two bearings are forced together upon tightening the main caps in place. This condition, along with a series of tangs, keep the bearings in place as the crankshaft spins, helping prevent what is known as spun bearings. However, excessive crush can hurt more than it helps. Too much crush causes the bearing to bulge inward, reducing oil supply and potentially causing metal-on-metal contact. Other bearing tricks include chamfered edges for fitting filleted crankshafts and dowel holes for when using aluminum connecting rods. Often times with aluminum rods it's necessary to permanently locate the bearings since such rods' thermal expansion rates do not allow for as much bearing crush. Finally, you need to consider a bearing's oil grooves. More or larger grooves take away bearing surface area, making them ultimately less capable of handling high loads. But often times there's little you can do here since eliminating oil passages isn't an option. Fortunately, some aftermarket bearings are offered with specially shaped grooves and holes that put forth the best compromise in surface area versus oiling.
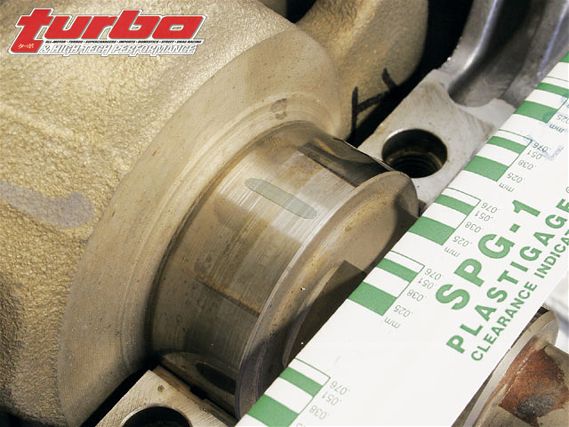
It's actually only partially true that the bearings support the load of the engine's crankshaft. In reality, the film of oil on top of the bearings supports the crankshaft, thus transferring load to the bearings. As such, bearing clearances as well as oil weights play major roles in just how much oil pressure an engine actually gets. Depending upon where the oil pump is located, a single improperly sized bearing can disrupt an engine's oil pressure, causing catastrophic failure. Loose clearances lead to low oil pressure conditions while tight clearances lead to higher pressure ones. But assuming tighter is better isn't always a good idea as it's easy to restrict oil away from the bearing, completely causing it to contact the crankshaft (higher pressure can lead to less volume). Metal-on-metal contact in terms of moving parts rarely works effectively. But erring on the tight side is becoming more popular as today's engine's feature far more sophisticated oiling systems and the machining processes used for engine building are far more accurate. To put the importance of bearing clearances into perspective, consider this: by simply doubling the space between the bearing and the crankshaft, as much as four times the volume of oil can be distributed.
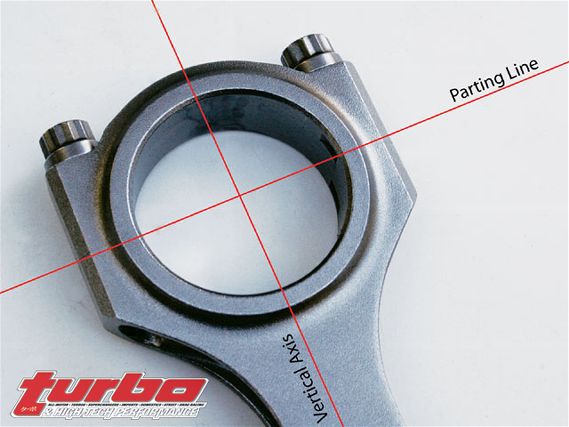
Sizing an engine's main and connecting rod bearings is relatively easy, but there's also a hard way. Of course, the hard way's more precise, but more than a few successful race engines have been assembled using the easy way. We're talking about Plastigage. But first the hard way. To size bearings appropriately, most machinists will use a dial bore gauge. The process involves using the dial bore gauge to measure the bare crankshaft bore's internal diameter. The crankshaft journal's outer diameter must also be measured and subtracted from the previous figure also taking into account the necessary clearances for bearing thicknesses. Bearings must be measured using an outside micrometer fitted with special ball-shaped anvils to fit the curvature of the bearing. An alternative method would be to install an arbitrary set of bearings into the block (or rods), torque the main caps (or rods) in place and measure the inner diameter with the dial bore gauge. For improper clearances, undersized or oversized bearings can be added and re-measured. Most manufacturers offer bearings that vary in sizes as little as 0.0002 inch from one another while most aftermarket bearings are generally offered in standard, 0.010-inch and 0.020-inch oversizes. Such large sizes require the crankshaft to be reground but allows for just about the closest tolerances you could imagine. It's important to note that's it's not at all necessary for each crankshaft journal to use the same size bearings. It's not even necessary for a single journal to use two bearings of the same size. What is important is that the final clearances are as close to one another as possible. If two different size bearings are going to be used on the same journal, just make sure they are within 0.0005 inch of one another and that the thicker bearing is placed on top for rods and on the bottom for the mains. Additionally, all measurements must be taken along the vertical axis (90 degrees from the parting line), where the brunt of the load is placed. This is especially important considering the bearings' eccentric shape once installed. The thicker area along the axis is referred to as the bearing crown; the thinner is the parting face. Despite the method chosen, before measuring bearing clearances, it's important to ensure that the block's main bore and the crankshaft journals are perfectly round and that the connecting rods are straight. To do this, you'll need a dial bore gauge.
Plastigage is not just an easier method of bearing sizing, it's also a lot cheaper. A good dial bore gauge and outside micrometer setup will set you back at least a few hundred dollars. Plastigage costs roughly two bucks and will last you through an entire eight-cylinder rebuild. Begin by cutting off a strip of the waxy string and place it on a clean crankshaft journal. Repeat the process for each journal. Make sure the bearings are already positioned in the block and on the main caps, free of contaminants and especially assembly lube. Next, install the main bearing caps and torque them to the proper specifications. Be careful not to turn the crankshaft, as it will distort any measurements. Remove the main caps. Take care when setting the caps down and when pulling them off that the Plastigage is not unnecessarily disturbed. Notice the crush process the material has undergone and compare the results with the Plastigage packaging, which features a metric scale on one side and standard measurements on the other. Note that the wider the strip, the smaller the clearance. Whether you'll be swapping bearings and re-measuring or bolting everything together for final assembly, it's important to clean off all of the excess Plastigage as it can easily disrupt oil flow across the bearings.
The perfect bearing would be a single piece encompassing the entire crankshaft journal, with the entire clearance between them occupied by a film of lubricant. The surfaces would not deflect under load conditions, and there would be no interruptions in the bearing surface such as oil holes, grooves, and irregularities. Corrosion would not be an issue and a sacrifice between embedability characteristics and strength would not have to be made. Unfortunately such a case doesn't exist. For the time being, the best engine builders can do is to ensure that the clearances are as optimal as possible and just as importantly, consistent.