Electronic Stability Control, or ESC, is designed to prevent a driver’s loss-of-control frequently caused by insufficient traction. The two basic loss-of-traction events are referred to as understeer (plowing) and oversteer (spin out). An example of understeer is driving straight down an icy road and turning left or right to avoid an obstruction. Because of the lack of traction at the front wheels, the vehicle will continue traveling in a relatively straight line, ignoring the direction of the driver’s steer. Oversteer is a loss of traction at the rear wheels, driving straight on a slippery, wet, road surface, and attempting an abrupt hard turn. The front tires grab, but the rears don’t, causing the rear end to slide sideways, potentially resulting in a 180-degree spin.
Either loss-of-traction event (or a combination of the two) can lead to a collision or rollover crash. Rollovers most often occur when a loss of control causes the vehicle to veer off the roadway, then “trip” on a curb, soft shoulder, and so on. Untripped rollovers are much less common, less than 5 percent according to the National Highway Traffic Safety Administration (NHTSA), and come about with top-heavy vehicles and/or an overly aggressive maneuver with good traction.
ESC is a great safety concept, which does save lives. As of model-year ’12, all U.S.-bound vehicles with a gross vehicle weight of 10,000 pounds or less are required to have an ESC system. The NHTSA predicts that offering ESC on all vehicles may annually save 5,300-9,600 lives and prevent 156,000-238,000 injuries.
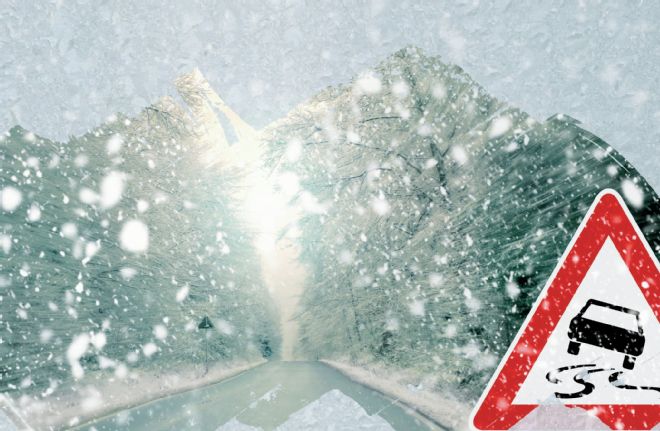
| Driving In Blizzard Conditions
So let’s take a look at how ESC works and how it was developed.
We’ll start off with the anti-lock braking system (ABS). It may seem unrelated but quite the opposite is true. ABS actually began in 1929 with a fully mechanical version used on aircraft landing gear. Experimental versions were slowly applied to motorcycles and automobiles through the ’50s and ’60s, but Chrysler and the Bendix Corporation developed the first modern (electronic) ABS system with production of the ’71 Imperial. The rest of the industry eventually followed suit.
The key to electronic ABS was the installation of wheel speed sensors, which report to the electronic control unit (ECU). The ECU receives individual speed inputs from all four wheels, as opposed to just one reading from the transmission indicating vehicle speed. With this data, the ECU predicts the instant a tire is about to lock up (skid) when the brakes are applied. The ECU immediately responds with commands to hydraulic valves and a fluid pump to control brake pressure at each wheel independently. By reducing the brake pressure (in a pulsing, high-speed process), each wheel will continue to spin at a determined low rate of speed and maintain traction. In most circumstances, ABS can reduce stopping distance, but its principal benefit is maintaining steering control during loss of traction while hitting the brakes.
A bit more trivia: ever heard of MaxTrac? This was the earliest stage of an electronic traction control system (TCS) implemented by Buick on the full-size, rear-wheel-drive ’71 Riviera. MaxTrac used an ECU with inputs from a left-front wheel speed sensor and a transmission speed sensor to compare the front-to-rear wheel speed difference. When the ECU detected higher wheel speed (wheel spin) from the rear axle due to lack of traction, it would modulate engine power accordingly by interrupting the ignition circuit. This would therefore reduce drive-wheel spin and regain some traction, regardless of the driver’s position on the accelerator pedal.
Today’s most recent traction control systems do basically the same thing as far as engine power reduction, only with the use of electronic throttle control (ETC), but modern TCS is also integrated with ABS. Just like anti-lock brakes use wheel speed input, commands to hydraulic valves, and a pump to control braking pressure and prevent wheel-skid, TCS applies brake pressure at each wheel with your foot off the brake (along with throttle control), to reduce wheel spin at the drive wheels while accelerating on low-traction surfaces (wet roads, sand, snow, etc.).
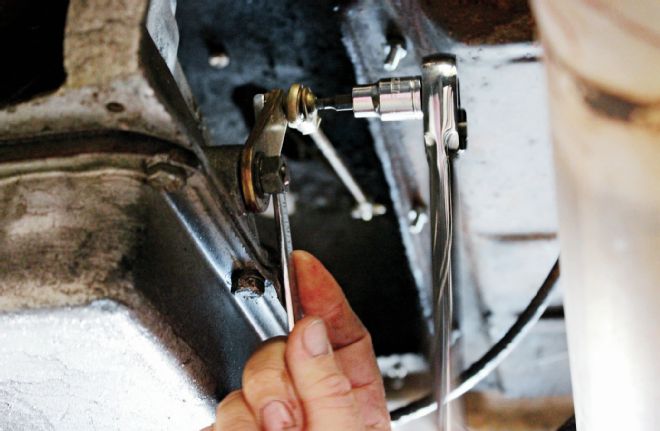
| Driving On Snow
Knowing ABS and TCS operation helps us understand electronic stability control. ESC fundamentally combines the technology of ABS and TCS with additional data used in the algorithm, along with modifications to hardware components. The two new data inputs are steering angle and yaw rate. Steering angle is data received by the ECU from a sensor mounted in the steering column. The steering angle sensor determines how many degrees, left or right, the driver is turning the steering wheel. The yaw rate, or rotational speed sensor, involves the direction and degree of potential vehicle spin. Look back at oversteer, where the vehicle loses rear-wheel traction and spins out. That amount of spinning momentum is the yaw rate.
Now we can put it all together and view ESC operation. A vehicle traveling in low-traction conditions is about to oversteer on a hard turn at excessive speed. The ESC control unit looks at wheel speed, steering angle, and yaw rate, and it determines an oversteer event is about to take place. Now that it’s quickly analyzing all the data, the ECU sends out instantaneous commands. By applying precise amounts of brake pressure at the appropriate wheels and regulating engine power when needed, the ESC prevents the oversteer. The system realistically views the difference between the driver’s intended course and what’s really going to happen and dictates the necessary actions to maintain control.
Credit goes to Robert Bosch GmbH and Mercedes-Benz for the introduction of today’s ESC systems with the ’95 S-Class sedan. Electronic Stability Control (ESC) is a fully recognized generic term, but the system goes by various names deemed by each manufacturer, although principles, components, and operation are very similar.
*Electronic Stability Program
(ESP; various automakers)
*StabiliTrak
(General Motors)
*Vehicle Stability Assist
(VSA; Honda, Acura, and Hyundai)
*Vehicle Stability Control
(VSC; Toyota and Lexus)
*Vehicle Dynamic Control
(VDC; various automakers)
*Dynamic Stability Control
(DSC; BMW, Jaguar Land Rover, and Mazda)
*AdvanceTrac with Roll Stability Control
(Ford)
ABS and TCS are now incorporated with the ESC system. Often the control unit, hydraulic pump, solenoids, and valves are combined in a single assembly referred to as a modulator unit, located in series with the brake lines between the master cylinder and all four brake calipers (or wheel cylinders in rear drum brake applications). The control unit uses network communications with other relative systems such as powertrain control.
ABS/TCS/ESC has been enhanced over time with additions including Active Rollover Protection (ARP), Emergency Brake Assist (EBA), and Dynamic Rear Proportioning (DRP). ARP adds a rollover or lateral acceleration sensor to aid the ESC system in preventing vehicle rollover. EBA determines an emergency braking situation by viewing the speed off the accelerator and on to the brake pedal. When an emergency is detected and the driver’s force on the pedal is insufficient, additional brake pressure is applied until ABS takes over. DRP is a method of proportioning rear-wheel and front-wheel brake pressure for optimum stopping power.
Automatic braking is cutting-edge technology. By detecting a pending collision with the use of radar, video, infrared, ultrasonic, or other sources, the ABS/TCS/ESC system can apply the brakes independently with no input from the driver. This can prevent or reduce the severity of collisions. The same technology is used in adaptive cruise control to maintain a safe distance from vehicles ahead.
During real-world use of ESC, typically an indicator light will flash while the system is operating. Depending on the severity of the event, the driver may feel nothing, thanks to seamless operation, or a degree of noise/vibration from the modulator unit. The majority of ESC-equipped vehicles provide a switch that fully or partially disables ESC and TCS temporarily. This may be used in unusual situations where TCS cannot get the vehicle out of snow or mud. And yes, ESC should be turned off prior to doing a burnout with sportier models.
Just like the powertrain control module, which controls engine functions, the ESC system performs self-diagnostics. If the ESC, TCS, ABS, ESC Off, or any combination of these warning lights remain on, this indicates a failure, the system is disabled, and a diagnostic trouble code (DTC) is stored in memory to aid in repair.
Obviously, ESC cannot maintain vehicle control in all situations, like extreme weather conditions or overly aggressive driving. A driver may even counteract the advantages of ESC with more extreme cornering as compared to driving a non-ESC vehicle. Aside from racecar driving (risk expected), taking any vehicle to its outer limits of control is an accident waiting to happen.
A lot of off-road enthusiasts do consider this stuff cheating, but recent programs based on the ABS/TCS/ESC system can be a distinct advantage. Traction control and anti-lock brakes alone take a 4x4 in low range to new levels crossing severe rocky or soft terrain. But sub-systems similar to Toyota’s Crawl Control provide even more enhanced capabilities. Using the basics of ABS/TCS and a little throttle control, Crawl Control allows a driver to dial-in a designated low speed of travel in low-range four-wheel drive. Once engaged, the vehicle creeps along, providing optimum traction and eliminating driver error at the pedals. This focuses the driver’s attention on steering and keeping the truck in an upright position.
Remember all these utilities are building blocks on the foundation of anti-lock brakes, and there will be new ideas added to the mix in future models. Just like PCs, smartphones, and tablets, software technology is a remarkable aspect of the entire system.
Write to Us!
If you have a technical question regarding your pickup, SUV, or van, feel free to contact us! Send a letter care of Truck Trend Shop Class, 831 S. Douglas Street, El Segundo, CA 90245, or email us at
[email protected]. Due to the volume of questions received every month, we cannot guarantee that everyone’s question will be personally answered or will appear in the magazine.