Towing a trailer can be one of the most stressful—but ultimately rewarding—endeavors a new truck owner will take on. With a bit of common sense and a firm grasp on the basics, pulling a trailer can become just as routine as driving to work. Over the next several pages, we’re going to look at the basic terms any towing veteran should know and give a brief overview of how a few essential towing systems function. As always, be sure to consult your vehicle’s owner’s manual for its specific towing capacity prior to hitching up any trailer, and be sure your equipment is in good working order. The satisfaction of completing your first haul will leave you wanting more, and your truck will thank you for putting it to work. After all, heavy-duty trucks do nothing better than tow a load.
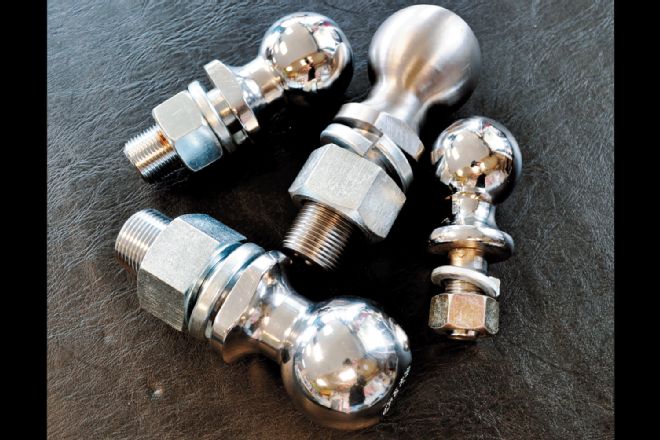
| There are three standard sizes of tow balls available: 1 7⁄8-inch, 2-inch, and 2 5⁄16-inch. Small utility and boat trailers are often found needing a 2-inch ball, while heavy-duty trailers, often those with electric brakes, require the larger 2 5⁄16-inch ball.
Towing Terminology
Ball Mount: The ball mount is placed inside the receiver tube opening of the trailer hitch, which is mounted to the vehicle.
Bumper Hitch: These hitch applications are only to be used for lightweight towing, including bike racks and cargo carriers.
Coupler: The component that is placed over the trailer ball to connect the vehicle to the trailer. The trailer’s coupler size determines which trailer ball is to be used, as the sizes must be identical.
Fifth-Wheel Hitch: A hitch that mounts in the bed of a pickup truck and, although much smaller, mimics the hitch design used on tractor-trailers.
Gooseneck Hitch: Commonly used to haul livestock, horse trailers, or heavy work trailers; utilizes a ball mounted in the bed of a pickup to engage the coupler on a trailer.
Gross Trailer Weight (GTW): Gross trailer weight is the weight of the trailer and all cargo; it’s measured by placing the fully loaded trailer on a vehicle scale.
Jack-Knife: When the truck and trailer may become damaged due to extremely acute turning angles; usually occurs when backing.
Pintle Hitch: Pintles and pintle mounts are most commonly used in military, agricultural, and construction industries when towing large equipment.
Safety Chain: Safety chains are required by law and should be crossed under the tongue of the trailer so that if the tongue should drop from the hitch it will not make contact with the road surface.
Sway Control: A device used to control unwanted lateral movements of a trailer. These may be used with or without a weight distribution system and are not to be used on trailers with surge brakes.
Tongue Weight (TW): The downward force that is exerted on the trailer ball by the coupler. Tongue weight will vary depending on where the load is positioned in relation to the trailer axle(s).
Trailer Ball: The object that connects the trailer hitch and the trailer together.
Weight Carrying Capacity (WC): The measure of the total weight a trailer hitch can safely pull without adding a weight distribution setup.
Weight Distribution Capacity (WD): The measure of the total weight a trailer hitch can safely pull with a weight distribution system installed.
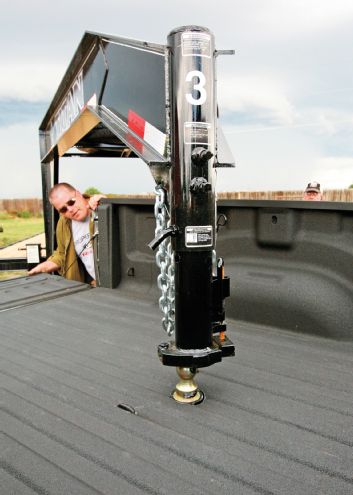
| Goosenecks utilize a standard-style hitch ball connected to a subframe that mounts directly to the truck’s chassis. This style of hitch is common on equipment and livestock trailers.
Trailer Hitch Class Review
Class I Receivers
- Towing capacity up to 2,000 pounds GTW and 200 pounds TW
- 1¼-inch receiver hitch opening
- Uses a ½-inch pin to secure the ball mount in place
- Will work with hitch balls with ¾-inch-diameter shank
Class II Receivers
- Towing capacity up to 3,500 pounds GTW and 350 pounds TW
- 1¼-inch receiver hitch opening
- Uses a ½-inch pin to secure the ball mount in place
- Will work with hitch balls with ¾-inch-diameter shank
Class III Receivers
- Towing capacity up to 6,000 pounds GTW and 600 pounds TW
- 2-inch receiver hitch opening
- Uses a 5⁄8-inch pin to secure ball mount in place
- Will work with hitch balls with 1-inch-diameter shank
Class IV Receivers
- Towing capacity up to 12,000 pounds GTW and 1,000 pounds TW
- 2-inch receiver hitch opening
- Uses a 5⁄8-inch pin to secure ball mount in place
- Class IV hitch balls require a 1¼-inch-diameter shank
Class V Receivers
- Towing capacity up to 18,000 pounds GTW and 1,800 pounds TW
- 2½-inch receiver hitch opening
- Uses a 5⁄8-inch pin to secure ball mount in place
- Class V hitch balls require a 1¼-inch-diameter shank
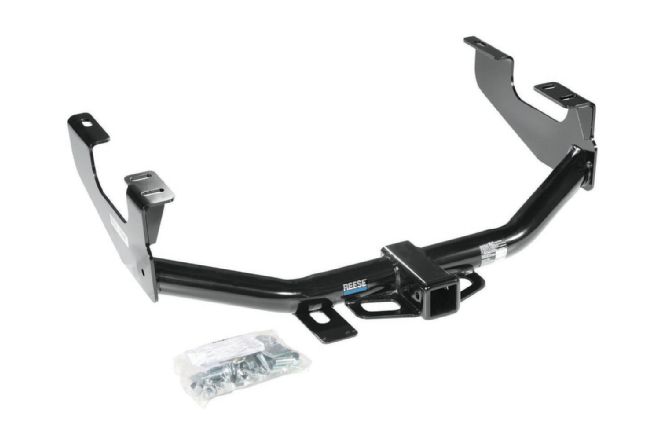
| The Class V trailer hitch is becoming more common as tow ratings continue to climb ever higher, now coming as standard equipment on many ¾- and 1-ton trucks.
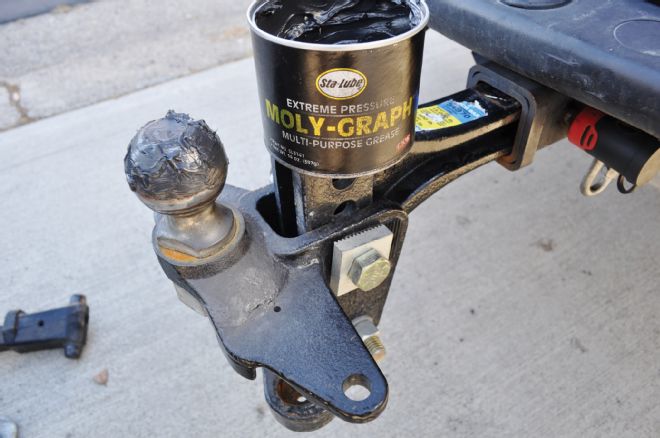
| A weight-distributing hitch setup is usually required to reach your vehicle’s maximum tow rating. Units such as this one from Reese combine sway control and weight distribution into one seamless hitch system.
Choosing the Correct Ball Mount
A level trailer will lead to a safe and comfortable towing experience, and using the proper ball mount is what makes this possible. Having a level trailer will put less strain on the connection between the trailer and hitch, as well as help the trailer stay in line behind the tow vehicle. To choose the proper ball mount, you must first measure the distance from the ground to the top of the receiver opening on the trailer hitch. Next, with the trailer parked level, measure from the ground to the bottom of the trailer’s coupler. Once you have these two numbers, compute the difference between the hitch and coupler height. If the hitch height is greater than the coupler, a drop mount will be required. If the coupler height is greater, a mount with a rise will be the correct choice.
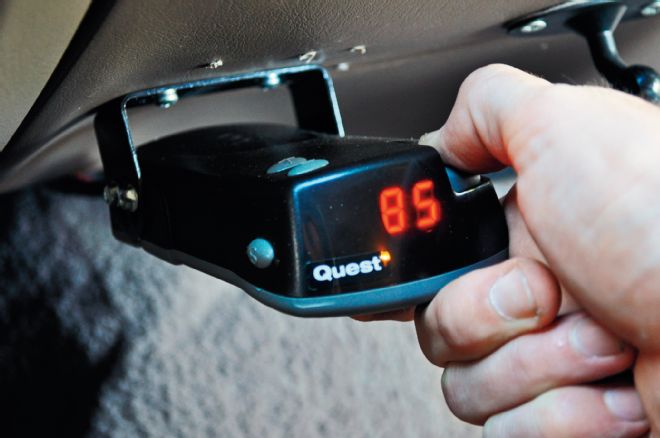
| Electric brake controllers can be set for different levels of braking intensity, which is determined by the user based on the size of load he or she is hauling. There is no one-size-fits-all setting, since each trailer will have a different braking need.
Braking Control Basics
Getting a trailer slowed down in a controlled manor is arguably the most important aspect of towing safety. To accomplish this, trailers must be outfitted with functional brakes of the proper size and quantity, and the tow vehicle must be equipped with a trailer brake controller. An electric trailer brake controller is a device that supplies power from the tow vehicle to the trailer’s brakes. There are many different brands and models available that differ in how they look and the number of axles they can control, but all controllers can be divided up into one of two groups: proportional or time delayed.
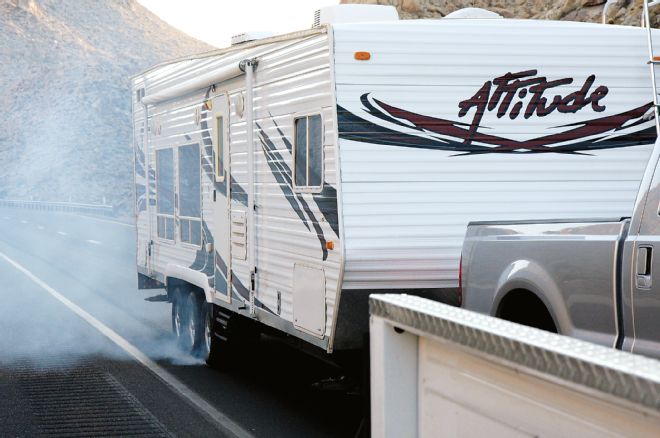
| When too much braking power is dialed in on the controller, it can cause the trailer’s brakes to lock up unnecessarily. This can lead to uneven tire wear, loss of control, or even a blowout.
With proportional brake controllers, once the vehicle’s service brakes are depressed, a motion-sensing accelerometer determines how quickly the vehicle is slowing and applies power to the trailer brakes equally as fast (or slow) as the tow vehicle. This type of controller provides the smoothest and quickest braking, while also providing the least amount of wear on both the vehicle’s and trailer’s brakes.
The time-delay brake controller is easily installed and is typically more user friendly than the sometimes-complicated proportional controllers. They are low profile and can be mounted at any angle. Time-delay controllers work in a way that when the tow vehicle’s brake pedal is pressed down, a pre-determined amounted of power is sent to the trailer brakes. Based on the trailer’s weight, the user sets the desired amount of braking power, and a delay is used from the time the brake pedal is pressed and when full power is delivered to the trailer. In most cases, either the truck or the trailer will be doing the majority of the braking, resulting in uneven brake wear.
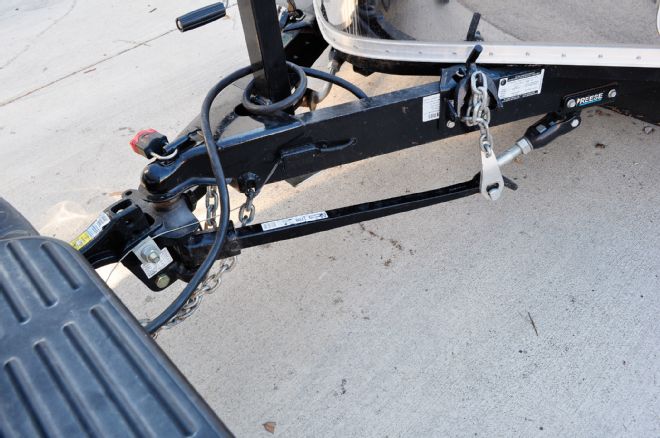
| A weight-distributing hitch setup is usually required to reach your vehicle’s maximum tow rating. Units such as this one from Reese combine sway control and weight distribution into one seamless hitch system.
Weight Distribution and Sway Control
When towing a trailer with a standard, rear-mounted hitch system, your trailer’s tongue weight is transferred to the rear axle of the tow vehicle. As a result of this, the rear end of the vehicle is forced down, and the front end is raised. Less weight on the front of the vehicle can lead to diminished steering performance and stopping power. The solution for this is the use of a weight-distributing hitch system. Adding a weight-distribution hitch to your towing setup transfers the load applied to the rear of the tow vehicle by the trailer’s tongue weight to all the axles on both the trailer and tow vehicle. The even distribution of weight results in a smoother, more level ride, and gives you the ability to tow at the maximum capacity of your hitch.
Adding a sway control device is recommended when using most standard weight-distribution hitch systems. Trailer sway can be caused by a number of environmental and human conditions, including crosswinds, poor trailer loading, or inadequate tension in the weight-distribution system. An independent, friction-style sway control helps to reduce trailer sway after it has begun. The device bolts onto the trailer frame at one end and attaches to the hitch with a secondary small ball at the other. They function by utilizing an interior bar, which telescopes in and out as the trailer moves side to side. As soon as the trailer begins to move out of line, friction pads inside the unit make contact and create resistance, which acts to reduce any further side-to-side movement. Other types of sway control devices include dependent and active sway control, both of which are a function built into weight-distributing hitch systems.