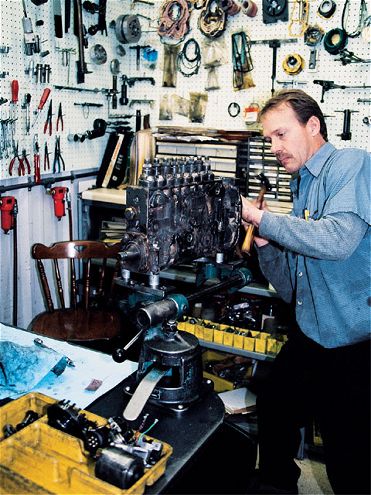
| A skilled technician at north West Fuel Injection completes the last few steps of rebuilding a Bosch P7100 injection pump.
The '94-'98 Cummins 5.9L engine has been the mainstay of diesel power in Dodge trucks, and has a reputation as an excellent performer with the ability to make some serious horsepower. One of this engine's features that makes it so desirable is the Bosch P7100 inline mechanical injection pump. This injection pump, often called a "P-pump," is the Holley Four-barrel carburetor of the diesel world. The P7100 pump has been around forever, is practically bulletproof, and is very tunable for high performance.
Cummins Injection Pump OverviewThe Dodge Cummins engine has used four different Bosch-sourced injection pumps over the last 20 years. The early engines ('89-'93) employed a Bosch vE mechanical rotary pump, while the later applications ('94-'98) used the Bosch P7100 mechanical inline pump. When the engine moved to electronic controls ('981/2-'02), the injection system switched to a vP44 rotary-style pump before being converted to commonrail injection in 2003 and receiving the Bosch CP3 injection pump.
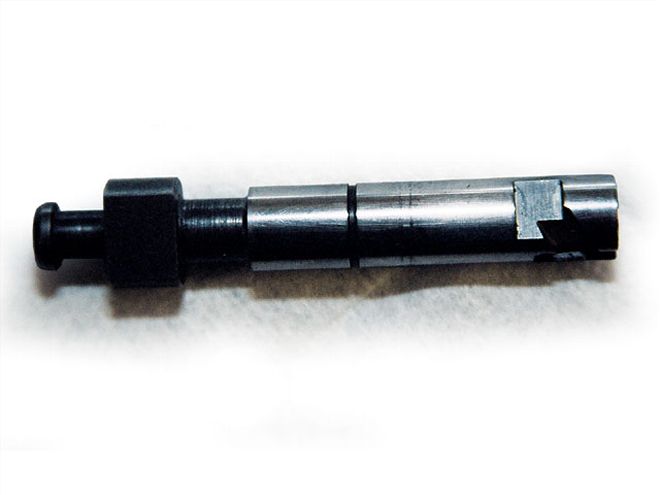
| The notch or scroll is what defines the P7100 pump as a port-helix injection pump.
How Mechanical Injection Pumps WorkA mechanical diesel injection pump is designed to pressurize, meter, and distribute the diesel fuel that's injected into the engine to create the optimum power output.
A mechanical injection system needs to be capable of pressurizing the fuel sufficiently to open the injectors (nozzles) and deliver the fuel to the cylinders in an atomized form. Mechanical injector opening pressures are usually between 3,000 and 5,000 psi.
The amount of fuel metered by the injection pump is the precise control of fuel quantity. Diesel engines operate with an excess of air in the cylinders so there is always more air present than is necessary to completely combust the fuel.
Distribution of the fuel is the last job of the mechanical injection pump. The fuel system needs to be phased (sequenced) to deliver the fuel to each cylinder at the correct time and in the correct firing order. Proper fuel system phasing is required to balance the engine output (all cylinders producing the same amount of power). Thus, if the injection event timing is set at 3 degrees before top dead center (BTDC), all cylinders must be fueled at the same respective crank angle.
A complete cycle of a diesel engine is 720 degrees of crankshaft rotation, and the fueling pulse has only a maximum of 40 crank angle degrees to be accomplished. For example, a four-stroke diesel engine running at 2,000 rpm produces approximately 17 power strokes in each of its cylinders every second, so the pumping, metering, and injection cycle are all measured in milliseconds, which is 1/1,000 second.
How The P-Pump WorksThe P7100 injection pump is flange-mounted to the engine and is driven directly from the engine's crankshaft through a gear train. The internal pump components are housed in a case constructed of cast aluminum, cast iron, or forged steel. The engine crankshaft drives the pump via a timed reduction gearset. The geardriven pump drive plate is connected to the injection pump camshaft (not the engine cam, but internal to the pump) with eccentrics designed to actuate the pump elements. Rotating the pump drive plate rotates the pump camshaft. The camshaft is supported by main bearings and rotates within the injection pump cambox. The cambox is the lower portion that houses the camshaft, tappets, and integral oil sump. In many ways, the P7100 pump has many of the components of an inline internal combustion engine.
The camshaft inside the P7100 is designed to have one cam profile dedicated to each engine cylinder. Riding each cam profile is a tappet assembly driving a pump element consisting of a plunger and a barrel. The barrel is stationary and drilled with two ports in its upper portion, which are exposed to the fuel-charging gallery.
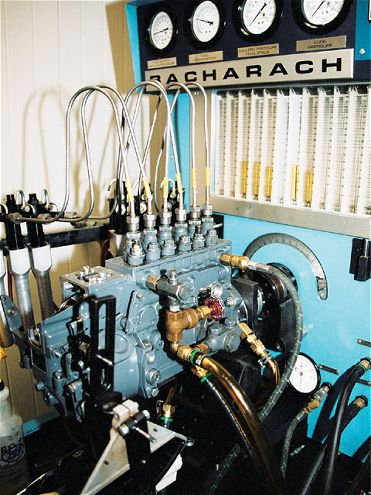
| At the University of Northwestern Ohio, we used a test-bench mounted P7100 pump to show the timing procedure.
The fuel gallery is charged with low-pressure fuel (15 to 75 psi). This permits fuel to flow into and through the barrel ports when the plunger does not obstruct them. The plunger reciprocates within the barrel; it is loaded by spring pressure to ride its actuating cam profile. Therefore, the actual plunger stroke is constant.
The Bosch P7100 injection pumps use a port-helix fuel metering system. This term describes its scroll-shaped (helix) fuel-metering method. The plunger is milled with a vertical slot, or cross and center-drilled with helical recesses. The function of the vertical slot or cross and center drillings is to maintain a constant conduit between the pumping chamber above the plunger and the helical recesses. Thus, whatever pressures exist in the pumping chamber must also exist in the helical recesses.
The fuel delivery stroke begins when the plunger is forced upward by the cam profile and the plunger's leading edge traps off the spill port. As the pressure rises in the pump chamber, it acts first on a delivery valve and next on the fuel confined in the high-pressure injector line transmitting diesel to the injector nozzle, and finally delivers a fuel pulse to the cylinder. This happens at the precise moment that upward travel of the plunger exposes the helical recess to the spill port. High-pressure fuel is spilled back to the charging gallery, causing a rapid collapse of pressure in the pump chamber, line, and nozzle. The injection pulse ceases when there is no longer sufficient pressure to hold open the delivery and nozzle valves. Port opening always occurs while the plunger is moving upward, that is, not at plunger TDC or beyond. This is required because the pressure in a port-helix pump element is designed to rise through the delivery stroke, thereby producing smaller atomized droplets from the injector toward the end of the effective stroke.
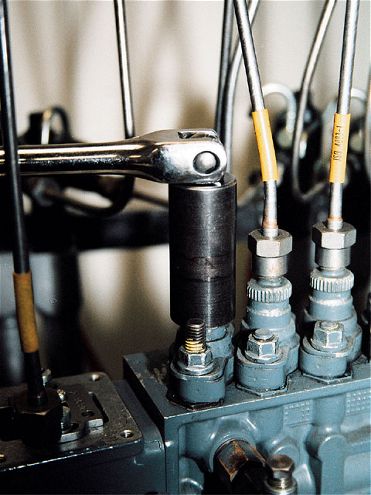
| After removing the fuel line from the pump for cylinder #1, a special socket (Snap-On part # SP503) is required to unthread the delivery valvebody.
Timing Is EverythingFuel delivery timing is critical during all engine operating conditions and speeds. In a diesel engine, fuel is injected into the cylinder slightly before the piston completes its compression stroke. The objective of the injection pump is to match the operating conditions with the proper amount of fuel to create the desired air/fuel ratio.
The goal is to smoothly and evenly transmit force developed in the cylinders to the flywheel or torque converter. The job of the injection pump is to manage the cylinder pressure (by injecting fuel) and cause it to peak when the crankshaft throw angle offers little mechanical advantage, and to diminish as the crankshaft throw is driven to a 90-degree angle with the connecting rod when mechanical advantage is highest. Most diesel engines are engineered to attempt to produce peak cylinder pressure 10 to 20 crankshaft rotation degrees after TDC.
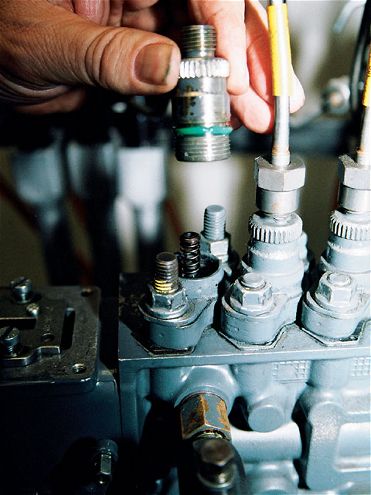
| With the delivery valvebody removed, the delivery valve core is in view.
Fuel delivery timing is extremely critical in a diesel engine and impacts power, fuel economy, and emissions. If the injection timing is overadvanced, a loss of power will be experienced, along with possible internal engine failure such as piston damage. Excessive gray/black smoke can be a sign of an overly advanced pump setting. If the injection timing is retarded (too late), a loss of power will result along with excessive smoke, high exhaust gas temperature (EGT), and if extremely late, severe white smoke.
It turns out that many of the symptoms of incorrect pump timing are shared by timing the injection on either side of the optimum specification. For this reason, it may be very difficult to determine if the timing is advanced or retarded only by examining the exhaust color or the engine's power output.
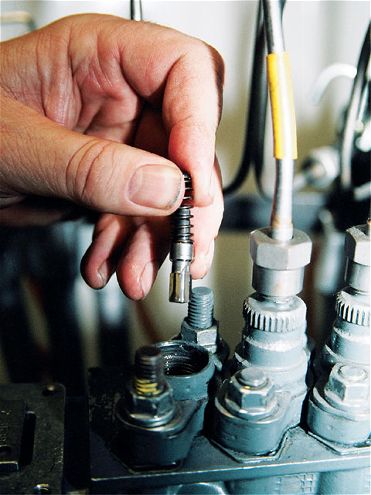
| Gently remove the delivery valve core and put it in a clean and safe place. If the injection pump is dirty on the outside, the engine should be washed prior to doing any work.
P7100 Pump TimingThe port-helix P7100 injector pump used on '94-'98 Dodge Cummins engines is timed by the phasing port closure of the #1 cylinder. The injection pump must be accurately timed to the engine. This means phasing pump port closure to a specific number of degrees BTDC on the cylinder to be timed to a specification that can be no more than one degree of crankshaft angle off. The injection pump timing needs to be very accurate and precise for the engine to run its best.
To review the timing procedure, Diesel Power traveled to the University of northwestern Ohio (UnOH) and worked with diesel instructor Bill Sergent and his class. In addition, we visited with Brad Anderson of north West Fuel Injection Service, a premiere injection pump rebuild shop in Columbus Grove, Ohio. We were exposed to not only stock rebuilds of injection pumps, but also the theory behind modifying the fuel delivery for a hopped-up diesel. Anderson told Diesel Power that injection pump performance is something that many enthusiasts overlook when modifying an engine. They assume the timing and operation are correct. If the injection pump is not functioning properly, then all the speed parts in the world will only have a minimal impact on the engine.
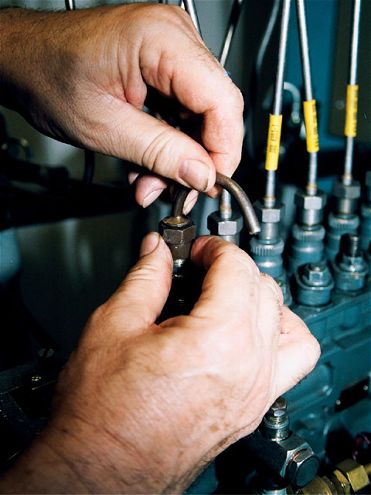
| Install the delivery valvebody (without the core) and the fuel line that you fabricated as a test drip tube. Get a container ready to catch the fuel.
There are three methods to time a Bosch P 7100 pump-spill, pin, and dial indicator. The most accurate and effective method of timing is the spill theory. It identifies in crankshaft degrees when helix-port closure occurs. It is also the easiest method for the enthusiast to use since it requires little in the way of special tools, but you may need to invite a few of your buddies over to help.
As with any procedure on a diesel engine, the factory shop manual should be referenced. The following is an overview of the steps to time a mechanical injection pump on a P7100-equipped Cummins diesel.
Do-It-Yourself P7100 TimingFirst, check the injection pump specification plate on the engine for the port closure value. Then, with a breaker bar on the crankshaft bolt, manually turn the crankshaft in the engine's direction of rotation to position the #1 piston on the compression stroke. Locate the engine calibration scale that is usually found on the front pulley, harmonic damper, or the flywheel. Position the crankshaft approximately 20 degrees before the port closure specification. For example, if the specification is 10 degrees, you would set the crankshaft at 30 degrees.
Remove the high-pressure pipe from the delivery valve on the injection pump #1 cylinder. Unscrew the delivery valvebody and remove the delivery valve core and spring. With a scrap piece of injection line from a salvage yard or engine shop, install it as a test spill tube on the injection pump. A discarded high-pressure pipe cut neatly and shaped into a gooseneck is all that is required.
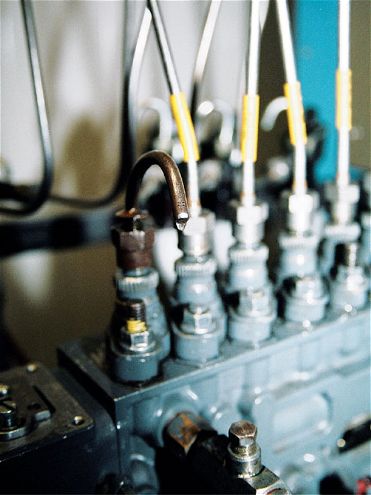
| With the crankshaft positioned properly, use the prime pump and have a helper turn the engine over with a bar. The stream of fuel will become a drip when the pump reaches port closure. The drip rate should be 2 to 6 drops per 10 seconds.
Use the hand primer pump to charge the gallery. The pressure created by the pump will be insufficient to open the delivery valves, which means the fuel will exit through the spill tube you have attached to the #1 port. The fuel should exit in a steady stream, so have a friend hold a coffee can or other container under the tube.
Then, slowly and smoothly turn the engine over with the breaker bar in the direction of rotation while observing the stream of fuel from the test tube. When the injection pump plunger leading edge rises to trap off the spill port, the steady stream of fuel exiting the test tube will first break up into droplets and then cease as the plunger passes the spill port.
The critical thing here is to locate the pump precisely (through the movement of the crankshaft) at port closure. At that time, the flow at the test tube should exist but be minimal; 2 to 6 drops per 10 seconds.
Now check the engine timing marks. Where the crankshaft position produced the drip from the test tube is the port closure. The crankshaft should be within one degree of the listed specification if the injection pump is timed properly.
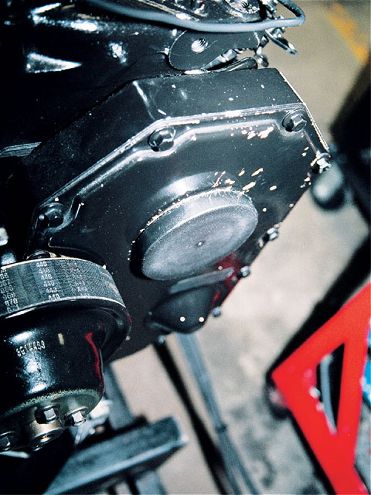
| Look at the crankshaft timing scale to see if port closure occurs at the proper amount of degrees. If not, the cover shown in the photo needs to be removed to gain access to the pump drive flange and bolts.
If the pump timing is found to be wrong, remove the accessory drive cover plate. To do so, loosen and remove the fasteners that connect the pump drive gear to the pump drive plate. With a breaker bar on the crankshaft bolt, turn the crank to the port closure specification. By uncoupling the pump drive plate from the pump drive gear, the pump will remain stationary at port closure on the #1 cylinder while you turn the crankshaft. When the engine is in the correct position, torque the fasteners that couple the pump drive gear to the pump drive plate. Turn the engine backward approximately 20 degrees before the port closure timing specification and then recheck the setting.
The timing test procedure is not complicated, but may be difficult to perform with the engine in the truck, especially if the vehicle is raised up or has big tires. Do not become frustrated. You will most likely have to go through the steps two or three times before you feel comfortable the values you obtained are accurate.